378 | Introducción a la simulación de estrés mediante elementos finitos (FEA)
Resumen
El análisis de elementos finitos (FEA) es una herramienta potente para simular la respuesta de un diseño a cargas reales. En este seminario web, presentaremos el FEA y cómo configurar y ejecutar un estudio en Autodesk Fusion.
00:00 | Hey team, Conor here from HPA, welcome to another one of our webinars. |
00:03 | This week we're going to be taking an introductory look into FEA and stress simulation. |
00:09 | So, we're going to start off by talking about what FEA actually is, then we're going to move into looking at how to set up a basic static stress simulation and we're going to be using Autodesk Fusion in this case, just because it's a free bit of software that you could do this in, but the ideas are the same no matter what FEA software you'd be working in or CAD software if it has this functionality. |
00:35 | And hopefully all this will give you a bit of an insight into how you might be able to use it for your projects as well. |
00:41 | We'll talk about a few considerations around using it. |
00:45 | So, yeah, let's crack in. |
00:47 | And first I want to start with a little bit of a disclaimer. |
00:50 | Obviously, this type of simulation and work involves a fair bit of engineering knowledge and it's obvious that many people watching aren't going to have engineering backgrounds or degrees in engineering and so on. |
01:06 | That doesn't mean that this is just some type of software that's reserved for people with degrees or anything like that. |
01:14 | You can absolutely get good results from it. |
01:17 | But it is something that you need to be aware of that it's a case of garbage in, garbage out. |
01:22 | So, if you're setting up the simulation wrong or feeding it kind of weird data, then what you're going to get out the other end isn't going to be very useful, probably be quite misleading. |
01:35 | Yeah, and moving on from that I would say that you need to be aware that you can't just blindly trust the results that you get from FEA. |
01:44 | Basically, you need to do a lot of validation and real-world testing to be able to trust the actual numbers you get out of FEA. |
01:54 | In some cases, in more simple cases, then absolutely you might be able to trust it. |
02:00 | But generally when it comes to developing models and FEA simulation, professional workspaces do a lot of back and forward between the FEA model and real-life testing to develop it and make sure they can understand the differences or get the FEA results as close to the real-life situation as possible. |
02:21 | That said, if you are feeding it the right information, you can still get very indicative results and that can be really good for just making comparisons between different designs. |
02:34 | So, you might have two designs you're working on and if you set up the studies as representative of the real-world situation as you can and keep things consistent between those two designs, then you should be able to very clearly see from that which design is better than the other and play around with it and see how those differences kind of change. |
02:57 | But that's going to make a little bit more sense as we get into it. |
03:00 | So, to summarise that, this does take a bit of knowledge to use but if you're keeping things consistent and doing the best job you can, you can get very good results that are usable at least for comparing designs and then with a bit more development, use it to make some real kind of, get some real data out of it that would represent the real-life situation as well. |
03:24 | So, let's just start off by talking about what is FEA or this form of stress simulation. |
03:32 | So, basically it's a form of computational simulation. |
03:36 | To break that down a little bit more, we're basically using our computer software to see how a model will react to real-life stresses or loads for example. |
03:49 | By saying reacts there, for a stress simulation anyway, we're seeing how the loads will result in stress distribution in the part so how the stress is kind of built up in the part and we can look at strain and deformation and so on. |
04:08 | And if we have the material characteristics set up for the part like the yield strength for example, the Young's modulus which dictates a lot of the stiffness and so on, density, things like that, we can, if we have those material characteristics set up, then we can understand the strength and the stiffness of the part so if it's likely to fail from those loads and how much it's likely to deform or deflect to understand the stiffness. |
04:42 | The model, and this really comes down to the finite element analysis which is what FEA stands for, so the model is converted into a mesh. |
04:51 | So, it's basically broken up into a lot of smaller elements. |
04:56 | We'll have a look at a mesh file soon to just show you but if you can imagine the surface of a model being split up into all these tiny little elements, facets, whatever we want to call them, typically triangular shaped and each of those faces is connected by a node or edges as well. |
05:17 | So, basically by breaking the model up into these smaller elements, the computer can solve equations at each node kind of making it more achievable and solving smaller parts of the model and then kind of iterating and building up from there to solve the entire model from that. |
05:36 | So, basically it's taking a large differential equation for the entire model and breaking it up into smaller linear equations which are easier to solve. |
05:47 | And to do FEA we typically set up the conditions and the load case and so on, but we're going to have a look at this in practice so it's all going to make a little bit more sense soon. |
05:59 | But it's quite a typical process that we're going to go through for most FEA software. |
06:05 | If you have any questions relative to today's topic that come up during this discussion just feel free to ask them in the chat and at the end I'll do my best to answer them. |
06:15 | Ok, so let's jump into it and I'll just jump into Fusion. |
06:20 | So, what we have here is a wheel design for a little project we're working on at HPA. |
06:27 | This is just a really basic wheel design that I've done just basically for this example. |
06:35 | So, three piece wheel, 15 inch wheel and I've designed a centre and this is the exact same lip and barrel that I have behind me here. |
06:47 | And it's all been fastened together with the hardware that we have as well to do that. |
06:53 | You can see in this case we just have the hub and brake set up here so I can make sure everything kind of clears which looks like we're going to have a bit of problem with the hardware in this case but those can be shortened a bit. |
07:07 | But yeah, just designed for a three piece wheel. |
07:10 | So, we'll do a little bit of a static stress analysis on this wheel that would be useful to be able to compare this to different wheel designs if we move forward. |
07:23 | So, I'll just get out of that little section view I've got going there. |
07:26 | So, this is our design workspace in Fusion but if we come over here to change workspace we can jump into our simulation workspace. |
07:34 | So, I'll do that here. |
07:36 | And in this case I've actually done this before and I wanted to set this up just so we don't have to wait at the end of this webinar to see the results because it takes a little while sometimes to solve these studies. |
07:47 | So, I've just got that static stress study sitting there but we're going to create a new one which basically mimics what we've got there just to show you the process of setting up that study. |
07:58 | Then at the end we'll just jump back into that one which is exactly the same to look at the results so we don't have to wait. |
08:04 | So, typically when we jump into our simulation workspace it'll automatically go into this new study tab here. |
08:13 | We'll be prompted to select a new study. |
08:16 | So, you can see we have static stress up in the corner here and it gives us a little blurb about what that's all about. |
08:21 | But there's all sorts of different simulation studies we can do in fusion in this case. |
08:30 | Looking at thermal stresses and so on and modal frequencies like vibrations. |
08:36 | There's also some stuff on dynamic simulation which is a little bit more representative for a wheel obviously. |
08:46 | And there's some stuff around like plastic injection moulding for example as well. |
08:51 | Shape optimization, that's a whole new thing around like topology optimization or generative design. |
08:57 | There's also another workspace for that. |
08:59 | We're getting away from the point. |
09:00 | We're going to just do a basic static stress analysis for today as our introductory look. |
09:06 | So, let's go create study there and that's just brought us into this study 2 tab. |
09:14 | The first thing we're going to do is jump into the simplify tab. |
09:18 | So, for a 3 piece wheel that's held together with a whole bunch of hardware like in this case that kind of makes things a little bit tricky. |
09:31 | So, also have a component here, this big red dot which is the forging block that the part would be machined out of just to understand the envelope I could work inside of. |
09:45 | Besides the point. |
09:46 | So, basically we have all these other components in here and we don't want them to be included in our study. |
09:53 | So, we just want to start off by simplifying our model a little bit to make the analysis a little bit easier to do. |
10:01 | Avoid any kind of variation between different designs that we don't need to account for. |
10:08 | So, in this case all I've done in the timeline down here already is just remove all of the hardware and also the hub and brake package behind. |
10:16 | So, we just have our face, our lip and our barrel in this case and we'll just go finish simplify. |
10:22 | So, you might be thinking surely we need the hardware to hold the parts together because that's how the wheels held together and we're trying to replicate the real life situation and that is something that we could include just in this case it makes it significantly more complicated and we will be able to get indicative results from doing it without that, just keeping things more simple. |
10:52 | Typically a wheel like this if we're using it in a performance application anyway, it should be welded around here for extra safety after it's been assembled. |
11:03 | So, we're going to basically copy that, like represent that in our simulation. |
11:09 | So, if we just jump ahead, we typically work from left to right along these toolbars but we're just going to jump ahead a little bit and we're going to set up contacts here between our three parts. |
11:23 | So, I'm just going to do an automatic contact in this case and it's saying the contact detection tolerance, so anything that's within 0.1, any part that's within 0.1 millimeters of each other, I know they're all touching in this case, is going to be joined together with a contact. |
11:40 | So, I'm going to go generate and this will take a little moment just to kind of set up these automatic contacts but basically what we get in the end if we right click and go manage contacts is we have these three contacts here and they're just on the flanges between the parts. |
12:01 | So, basically it's saying bonded which is the equivalent of it being perfectly welded together so it's like three parts that are touching each other there, all bonded together. |
12:13 | So, I've basically just turned our three piece design into a one piece wheel in this case just to keep things simple. |
12:20 | Again, that might not be the perfect representation of the real life situation for this wheel but it would be a good way to simplify the design to be able to compare different designs together, simplify the simulation rather. |
12:35 | We could set up bolt connectors at all these bolting points as well and I've done a little bit of testing back and forward between that method and this method and the results are pretty insignificant I would say in most cases considering the kind of variability of loading a wheel in the first place when you're just driving around on the road or the track. |
12:58 | Cool. |
12:59 | So, that is our contact set up between the parts. |
13:03 | We're just going to jump back into this materials tab here so we can see we have our lip, barrel and our face and these are all set up as aluminium 6061 T6 which has all been set up in the design workspace. |
13:18 | I did that just to be able to get a bit of an idea of the weight of the parts which we'll jump back and have a look at if I remember at the end but that's all set up and that is the material that these parts would be made out of. |
13:34 | Specifically the face would be machined out of that material so that's just applied all those material specs and characteristics to our design so that's an important step here. |
13:46 | If it's going to be made out of this material we want to model it in that material not steel or something like that which is going to be completely different. |
13:55 | Cool. |
13:55 | So, that's a lot of our set up done in terms of the basic kind of background set up and then we get into what's called our load case. |
14:05 | So, the load case includes the constraints as well so the constraints as the name implies is basically how the part is fixed and then the load case is obviously the load that's applied to the part. |
14:19 | I'm just going to jump over to another document here. |
14:23 | So, this is actually the New Zealand and I think Australia standard as well for wheel testing for aftermarket wheels. |
14:32 | This doesn't exist in every country, this is just a local one that we use and it's different everywhere but this is fairly representative of a lot of them that I've seen so there's kind of three main different tests here. |
14:47 | This one which we're going to focus on today is a lateral load test on the wheel to kind of simulate the forces through a corner. |
14:58 | And they also have this radial one here which is basically the forces of the load down through the wheel. |
15:07 | And then the final one they have here is an impact test basically dropping mass onto the wheel as well. |
15:15 | So, what we're going to do is rather than try to simulate a real life situation of the wheel being mounted to a hub and then the forces through the tyre being transmitted into the wheel through the bead seat and so on which is a little bit more complex, we're just going to basically copy this little bit more simplified version of that, which is this test here. |
15:44 | So, basically you can see the cross section of the wheel here and they clamp the bead seat down to the table here and they have mounted to the mounting surface, they have this moment arm and then they apply a force to that. |
15:59 | And this is all the force, the load here is calculated based on the amount of torque that's generated by the cornering force of the vehicle through the tyre and so on. |
16:11 | So, we won't get too deep into that, how to calculate tyre forces and so on because it just gets a little bit complicated but I will show you kind of a rough idea of the type of forces that we're talking about. |
16:24 | So, again we're just going to try to set up the equivalent of this test in FEA. |
16:31 | So, we'll just jump back into here. |
16:35 | We'll start with the constraints. |
16:37 | So, what we want to do is set up a structural constraint and the constraint for that part was fixing that bead seat onto the table. |
16:44 | So, all we need to do here is select a face by the bead seat. |
16:49 | We'll just select this one here, it'll work pretty well. |
16:52 | That's where the bead of the tyre would kind of rest against the wheel and we're just going to fix that. |
17:00 | We could kind of select a few of the other faces around here as well and it would probably give us very similar results but we're just going to keep it simple, select that relatively small face. |
17:10 | So, that's just going to fix that in space. |
17:13 | Jumping ahead just a minute again, so we have now fixed that face and all our parts are bonded together. |
17:22 | If we jump to our degrees of freedom view here we can see that everything is fully fixed and we want that to be the case for a setup like this. |
17:31 | We don't want to apply a load to a part that isn't fixed to something else because it won't transmit any of that load through to the other parts, it'll just kind of pull it out of position basically. |
17:42 | So, in this case we know it's fully fixed, it's green and that's going to be good moving forward. |
17:47 | So, we have our wheel fixed down to the table essentially and then now what we're going to do is apply a load on a lever arm to the mounting surface. |
18:00 | So, if I jump in here to the loads tab, I'm going to go structural load in this case. |
18:06 | The target is going to be the mounting surface for the wheel to the hub and in this case there's a few different ways we can do this, but we are going to apply a remote force. |
18:20 | We could do this with a moment to get a very similar setup, but in this case we're just going to try to copy that standard study test that I showed you before as closely as possible. |
18:33 | So, remote force there and I'm just going to set this up, the direction type basically is how we control the load that's being applied. |
18:43 | I find it a little bit easier in this case to set it up with these vectors. |
18:48 | So, it's going to be in the Z direction and we're going to use 5000 newtons here. |
18:55 | Basically, I've done some calculations for a car of the type of size or weight that would be running a wheel like this, pulling about three Gs in a corner which is very high, not something that most typical road cars would be pulling, three Gs is more something that like a car, GT car with serious aero might be able to pull in a corner. |
19:18 | So, that three Gs is going to be our safety factor. |
19:22 | But basically that translates to a torque about the centre of the wheel or the mounting surface of about 5000 newton metres in that ballpark anyway. |
19:34 | So, we're going to apply 5000 newtons in this case and use a lever arm of one metre to give us our 5000 newton metres. |
19:43 | So, we've got 5000 newtons and we can see the arrow of that, just the direction that's being applied and we're just going to set up the lever arm now so our source location is going to be that so we can see it's just kind of moved things out a little bit and we have 34, so this one here needs to be zero so we're applying it to the centre but this value here actually needs to be one metre or 1000 millimetres so we're going to put 1000 in there so that's basically, we've got our 934 and then we know this was about 64, 65 millimetres from the face there. |
20:29 | So, we've got that force now applied, 5000 newtons applied one metre from the surface to the centre so basically a remote load essentially on a lever arm like that test we looked at. |
20:42 | I'll just jump back to that to refresh your memory. |
20:44 | So, we've kind of simulated this if the force was just being applied directly to the lever arm here. |
20:51 | Cool. |
20:52 | So, that's our structural load set up and at that point we're basically ready to go. |
20:59 | So, in this case for fusion if we click solve it will automatically generate the mesh or we could generate the mesh ourself and the mesh is kind of like one of the important parts of this finite element analysis process. |
21:12 | Naturally, it's very important that the mesh refinement, we consider the mesh refinement, so what I mean there is if we do the mesh view so I'm going to generate the mesh now so we can have a little look at what that actually looks like. |
21:32 | So, mesh refinement, the higher the mesh refinement or the more fine the mesh is the smaller the elements are, the more elements we have, the more points we have for those equations taking place and generally speaking the more accurate the model will be but also we have more equations and more calculations so that also takes longer for our computer to process. |
22:00 | So, if I zoom in we'll get a little bit of a better idea here. |
22:03 | We have all these kind of triangular faces or elements that the model has been broken down into. |
22:10 | We can jump in here and we can manage adaptive mesh refinement for example so we see a little bit of that here where areas of more detail have more mesh refinement and big kind of more simple areas have a more coarse mesh to kind of strike a balance between the accuracy and the processing time. |
22:34 | A good practice if you're doing a lot of this is to do what's called a mesh convergence study, so basically it would be running the simulation a lot of times for different mesh refinements so essentially as you make it more and more refined the mesh the results will change and we want to plot those changes in the results with the mesh refinement and find a point where they converge with that convergence study, so basically we get to a point where more mesh refinement doesn't specifically give us a more accurate result and that's how we kind of one, find that our setup is accurate, because if we have something weird happening it will basically be a red flag that we've got something wrong but also find that balance where we can continue to run studies like this on different designs and we can be happy that they're going to be accurate enough, but it's not going to take us too long to process it. |
23:36 | So, that is just a bit of an introductory look around what meshing is and the things that we need to consider but for this we're just going to run with the default settings in this case it's already meshed the thing that I would just last thing I want to note here is if we're comparing different designs then we need to use the same mesh refinement naturally be it the default settings something else we've kind of figured out works maybe from our convergence study and so on, but there's no point comparing different designs and ones solved with a very coarse mesh and the other ones solved with a very fine mesh, because we're not going to be able to compare them then essentially. |
24:18 | So, from there we get this little pre-check box and green tick basically shows us we're all ready to go and everything's set up as it should be and then we can basically come through here and click solve and it'll solve the study and so on and go from there. |
24:35 | I'm not going to do that just to save a little bit of time and I'm going to just jump into that study that we'd already solved before which is set up exactly like this one was so we'll just look at the results from there. |
24:48 | Again, if you have any questions that have come up during this or the next few minutes feel free to ask them in the chat and I'll do my best to answer them in just a moment. |
24:59 | So, let's just activate that other study and then we can just jump over here and go to view the results. |
25:07 | So, this is typically what we get as the results and in Fusion we have this little kind of toggle tab over here where we can change between the different factors I guess so we've got a safety factor in this case. |
25:24 | Just see if I can get the report up. |
25:28 | Nope. |
25:31 | No. |
25:34 | Is it here? No it's not. |
25:36 | Okay. |
25:37 | But basically we can see from this that the minimum safety factor in this case is 1.2. |
25:44 | So, remember that we solved this or set this all up around that 5000 newton metres load on the wheel and that was at 3 g's of cornering force, so that was my way of basically pulling in a bit of built in safety factor there. |
26:01 | So, this is still saying that this wouldn't fail from one time of being loaded at 3 g's. |
26:10 | We might not ever get to that 3 g's but in this case it's only 1.2 so if we did get to 3 g's we'd be able to handle it once probably yes. |
26:20 | If there was any manufacturing defects little cracks in the wheel or something like that then probably no and those would if it was repeated loading which obviously a wheel would be exposed to then those cracks would grow and we'd end up with something like a fatigue failure so this is just showing us in this case one static stress analysis that's saying it's not going to fail, but yeah that's not really representative of a real life situation for a wheel. |
26:51 | Let's move on and have a look at the stress distribution in the wheel. |
26:56 | So, this is quite a good way of optimising our design so we can basically see the blue areas are very low stress and then these kind of yellow to red areas are higher and this will be comparing this stress to the ultimate yield stress of the wheel and then from there that's how it determines the safety factor and if the wheel's going to fail or not, but we can basically come in and find these stress concentrations in the back so we've got mostly in these little pockets here and that might be some areas that we go well okay we want to reduce those stresses so maybe we need to change the design around there potentially add more material into those sections add a larger radius or something like that to reduce the stress concentration or maybe we can also look at areas in the blue here and go that's a pretty low stress area maybe I could extend these pockets right out to the edge here and take some weight out of the wheel without taking a penalty in the strength department - we'll move on again look at displacement, so same thing it's just showing us this kind of colour gradient of where the areas of the wheel that have displaced or deformed more than the other ones and we've got this kind of deformation thing here, so that would be showing no deformation this would be the actual deformation which you'd hardly be able to see and then this kind of scales it up so we can just more clearly see how the wheel was actually deforming in this case in this area in red here is deforming by half a millimetre we can use this to understand the stiffness of the wheel compare that to other designs and so on the stiffness here it's leading to something that we call camber compliance in the wheel, so we basically want to reduce that as much as possible, because it's like compliance in our suspension bushings and so on and it's taking away from the camber of the wheel it's losing camber in a corner, so we have to run more negative camber in our static alignment and so on generally we want it as stiff as possible to reduce any compromises in the static alignment and it kind of gives more precise steering feel and so on as well so the stiffness of the wheel is just as important as the strength in a lot of cases as well oh sorry the strength to weight I should say the strength is obviously probably the most important thing we don't want the wheel to fail, but in some cases they will make the wheel a little bit heavier for a motorsport wheel to get back some of that stiffness compared to maybe something that's just used for street use really depends on the application so we'll just leave it at that. |
29:47 | We have a few more things here that we could look at but that's the main three ones I'd say stress, displacement safety factor is just a way of looking at the stress as well; so yeah that is the results kind of covered for that and yeah like I said we could compare that to other designs or in some cases we would validate that with real world testing as well like using this test here and yeah that's basically the introductory look at FEA or static stress simulation just using a bit of an automotive example there so what we'll do is just jump into the questions and yeah I'll see if I can do my best to answer any of them. |
30:33 | So, Samson Wang "Hey there will you guys be willing to walk us through how to simulate cycle loads down the road?". |
30:42 | Yeah, I would be really keen to look into that more dynamic or like fatigue failure testing and simulation as well at the moment in Fusion, which we typically work in the static stress is a lot easier to do and it's free for us to do as well, so it's accessible to everyone but I would love to get my hands on some software and have a look at doing that what you're talking about there as well so yeah something we're definitely working towards doing more of the simulation stuff and computational simulation and modelling in the future so I hope to do more of that. |
31:23 | Cool, right hopefully, I don't butcher this Zhao Shizi one "Great to see the metal 3D printed part wondering if the exhaust will be polished exhaust will be polished for better performance?". |
31:39 | Hmm, polished for better performance. |
31:42 | Better performance how I would ask, typically exhaust flow through it I don't think the boundary layer of the part needs to be polished on the inside I'd say that would probably pretty small gains in performance especially past the kind of primaries into the merge collector. |
32:03 | It's pretty smooth in there it's probably not as rough as you think but sometimes a rough surface finish like this can kind of promote flow as well or you might also be talking just about thermal performance in this case this could be polished or this one is actually glass what was it bead blasted to get this finish, but yeah it could be polished it could be coated with Cerakote or so on we're not 100% sure what we're going to do in that case sorry I didn't really answer your question, but maybe gave you something there. |
32:45 | Cool, leave it at that that's all the questions we have, so again just hopefully that's given you a little bit of an insight into FEA if you weren't familiar with it or maybe you know what it is but you've never seen it used before that's just a very basic look at setting up a basic study, but it can still give us results and be able to compare that between different designs as well it's probably the main use I'd like to point out here unless we're kind of looking at the higher level of it. |
33:16 | So yeah, we'll leave it at that and we'll see you guys next week for another one of these webinars thanks for coming. |
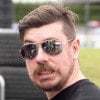