386 | Cómo modelar conductos de admisión y escape en CAD
Resumen
Los colectores personalizados son una modificación común cuando se busca mayor potencia o eficiencia. Los canales suelen presentar formas, curvas y transiciones complejas. En este seminario web, analizaremos algunas maneras sencillas de modelar los canales, teniendo en cuenta los diferentes métodos de fabricación.
00:00 | Hey team, Conor here from HPA, welcome to another one of our webinars. |
00:03 | Today we're going to have a look at how to model intake or exhaust runners in CAD. |
00:10 | So, we'll have a little look at the tools that you need to use in CAD and then the kind of rough process that you should take or at least the common process that I take to modelling exhaust or intake manifolds. |
00:22 | And we'll look at a few different approaches that you can take depending on the manufacturing process that you're going to use. |
00:29 | So, we'll come back to that in just a moment, I just wanted to start off by discussing where it's useful or why we do this. |
00:37 | So, basically obviously if we're designing an intake or exhaust manifold for naturally aspirated or forced induction applications, and then the same techniques that I'm going to show you here can also be used for modelling other parts, anything kind of conveying fluids I guess, so plumbing and inlet pipes, intercooler piping, exhaust, anything really. |
01:04 | Even brake lines you could use, probably some of these techniques. |
01:09 | So, why are we showing you this? Basically, if you're designing a part that you're going to make, be it an intake or an exhaust manifold, it's good to be able to plan this, plan it in CAD and you can also do a lot of optimisation of your design first or just fleshing out whatever's going to work best in CAD before you then go and spend the money creating it on the car rather than perhaps taking the more traditional fabrication approach of just kind of making it in situ. |
01:41 | It's a lot easier to make it in the virtual world first and then kind of hit the ground running with a good design. |
01:49 | And we can also, if we design it in CAD, we can use tools such as CFD or computational fluid dynamics to be able to compare different designs as well. |
02:02 | So, look at two different designs, see how they flow, things like that. |
02:07 | We can do all of that on our computer if we have a CAD model of it first. |
02:12 | So, we'll jump onto my computer screen and I just have Autodesk Fusion open here and you can see I've already got some flanges set up in my workspace. |
02:27 | This flange for the cylinder head and then this is the turbo flange here. |
02:31 | So, this is actually for a turbo manifold, I think in this case it's actually for a Mitsubishi Evo, 4G63, and I'm pretty sure it is a stock position one, or I might be wrong, might be like a high mount or something, not really sure. |
02:50 | But if I just turn on this part here, we can see I actually have a 3D scan of the original turbo manifold, or not the original one, it's an aftermarket unit. |
03:02 | And don't be scared off here thinking that we have to have 3D scans to do this work because you absolutely don't. |
03:09 | I'm just kind of showing this for reference of something that we're going to create, something similar to today. |
03:15 | I'm just going to kind of base it off this design rather than creating something completely new kind of on the spot. |
03:22 | But essentially, this is actually a worked example from our 3D scanning course where we reverse engineer this manifold from a 3D scan. |
03:34 | If you are interested in how that side of things works, I'll get Jayden to drop a link to that course in the show notes or in the chat. |
03:44 | But without that scan, an easy way to do it is just to measure up the whole spacing and everything on the exhaust manifold, on the cylinder head and similarly we can do the same kind of thing for the turbo flange here and then just position those in space where we kind of need them. |
04:04 | And these are just simple sketches and 2D extrudes and these could be then laser cut parts or something like that. |
04:14 | So, like I said before, how we're going to model the exhaust manifold or intake manifold, it doesn't matter. |
04:22 | It's basically the same process either way. |
04:24 | The same ideas. |
04:26 | How we're going to model that really depends on the manufacturing process we're going to use. |
04:31 | And whenever we're doing a design process like this, we probably want to have that, we want to know what the manufacturing process and the materials we're going to use are from the very start before we start designing. |
04:43 | So, we can keep in mind DFE and we'll design for manufacturing considerations and we don't end up designing something that we can't then manufacture by the intended way that we want to do it essentially. |
04:55 | So, if we're going to design something to be CNC'd on a three axis mill because that's all we have access to, then we need to keep in mind the limitations of that machine when we're designing. |
05:11 | So, we don't make something impossible to manufacture or extremely difficult or inefficient to manufacture. |
05:17 | So, if we talk about the manufacturing options for an exhaust manifold like this, the aftermarket wise or custom setup would be traditional fabrication techniques. |
05:31 | So, we're going to be using sections of straight or pre bent, mandrel bent tubing and basically welding that together to get the runners. |
05:41 | And these would typically be like a plasma cut or laser cut or water jet cut flanges. |
05:49 | The more factory alternative or some aftermarket parts are, for example, Artex manifold or a manifold that I've been working on recently for a Volvo setup, we can actually do cast manifolds as well. |
06:07 | And that's maybe they're going to be investment cast or sand cast or die cast. |
06:13 | That's definitely an option. |
06:14 | If you're looking to make a product that's going to be die cast and you're going to sell some of them. |
06:23 | There's a lot more, there's more design flexibility I'd say in like a cast part compared to a fabricated part where we're in a fabricated part, we're obviously somewhat limited to circular section for our runners, where in a cast part they could be kind of changed from this oval or slot shape here into whatever the shape here is for the turbo manifold, kind of gradually as it sweeps through that, whereas in a traditional tubular manifold, that's going to obviously be circular, that section. |
06:59 | And the other alternative is 3D printing as well. |
07:03 | So, we get even more design flexibility with 3D printing or additive manufacturing. |
07:10 | We can do some really kind of crazy stuff with it. |
07:15 | There's limitations obviously, but not as much as a traditional fabricated part. |
07:21 | We can put some crazy detail into it that doesn't have to be manufactured by hand, so it's a really good way to go about that. |
07:28 | If we do some kind of conformal ribbing on the surface or something like that, to minimise the wall thickness to save weight, but also get some of that thickness back, crazy stuff like that. |
07:41 | But obviously with the cast parts and the 3D printed parts, size limitations around kind of the material that we use obviously has a big impact on the cost of the part. |
07:54 | If we're getting a die made for a very big six cylinder cast manifold, like inline six, then it's going to be quite expensive as opposed to a very tight, compact something for maybe like each side of a V6 or something like that. |
08:11 | The same thing for 3D printed. |
08:12 | The bigger our part gets, kind of exponentially the cost is going to go up because we're going to have to use a larger 3D printer and the material cost obviously goes up as well. |
08:24 | And that's especially for exhaust manifold materials where an intake made out of aluminium is actually surprisingly cheap for 3D printed parts now, but stainless steel, titanium, Inconel, things like that are quite expensive. |
08:41 | So, just something to consider. |
08:43 | All of these options when it comes to designing it in CAD, whether it's traditional fabrication or designing it for a 3D printed part, follow the same kind of similar approach when we're going to model this in just a moment, but there are some differences between them. |
08:59 | So, we will kind of have a look at two different approaches, I guess. |
09:05 | All right. |
09:05 | If you have any questions come up during this time, just feel free to ask them in the chat and I'll do my best to answer them at the end. |
09:12 | So, let's have a look at option one being the kind of traditional fabrication approach. |
09:21 | And before we do that, I'm just going to, here, just pull this onto the screen. |
09:27 | So, what we want to do is basically review the supplier's offerings for the materials that we're going to be able to work with. |
09:35 | And this is going to be different depending on who your supplier is, but basically I've just chosen Vibrant Performance here, they're a fairly kind of standard one, I think it's available, Australia, America and so on. |
09:50 | So, just going to kind of review the raw materials that they have when it comes time to fabricate the part and make sure that when I'm designing it in CAD, I'm essentially using those raw materials as I go. |
10:04 | So, I'll just jump into 304 stainless, just a simple kind of cheap, but good, well-suited stainless steel to making something like this. |
10:18 | And we can see that they have, you know, 180 mandrel bends here and the tubing out of diameter. |
10:27 | We're going to design around 1.75 inches here, and then they have some options for the centerline radius here, the diameter in this case, and stepping up to about 6 -inch centerline diameter. |
10:43 | So, we can kind of keep in mind these options as we're designing. |
10:49 | There was another one here. |
10:54 | They've got pie cuts and so on, but there was something as well, but it basically steps down to the centerline radius being one times the diameter. |
11:04 | So, we'll just keep that in mind kind of as we start designing. |
11:09 | And they also have, sorry, if I just jump back into that, not in this one, but they also have some options but the wall thickness options, I think they'll be down the bottom here. |
11:23 | Maybe not, but how could I find that really quick? Right, I'll just skip forward on that. |
11:34 | But I can't remember off the top of my head. |
11:37 | I think it's 45 hundredths of an inch, or I'm not good at Imperial, or 6,500. |
11:43 | So, it's about, we'll go about 1.6 millimeter wall thickness for that tubing. |
11:48 | That's pretty standard anyway. |
11:50 | I think that's the Imperial equivalent is 0.065 inches. |
11:55 | But anyway, we'll get into it. |
11:58 | So, what I'm going to start by doing is basically creating a sketch and then mapping out, I guess, the trajectory for the tubing. |
12:09 | And we're going to kind of copy this design of the 3D scanned manifold here, but we could just be creating one completely from scratch. |
12:19 | I'm just going to hide that. |
12:21 | So, here I'll create a sketch, and we'll just start by creating a sketch on this plane. |
12:26 | This is actually going to become a 3D sketch, so it's not going to matter too much. |
12:31 | If I hit P on my keyboard, I can project this front face of this cylinder head flange, and that's going to bring me up all the details of that flange, basically, and the profile of it. |
12:46 | So, next what I'm going to do is I want to just find these hole centers, or the exhaust port centers. |
12:54 | So, what I'm going to do is just get a construction line type, click line, and then I'll turn the 3D sketch preference off for now, actually. |
13:04 | We'll come back to that in just a moment. |
13:05 | And I'm just going to connect these two points here. |
13:08 | And then as we come back to this soon, we'll be able to hover over that line. |
13:12 | And as that little triangle pops up, that's the midpoint. |
13:15 | So, I know that's the center of the exhaust port. |
13:18 | And we'll just do the same thing for each of these. |
13:21 | So, I'm just clicking between those points. |
13:25 | Oh, missed that one. |
13:28 | Just snapping to those. |
13:32 | And the last one there. |
13:35 | Cool. |
13:36 | And then I'm going to jump up to the turbo manifold here. |
13:40 | Slightly different approach here because this isn't on the actual sketch plane that we originally selected for a 2D sketch. |
13:48 | So, what we're going to do is come down under here, and we're going to include 3D geometry. |
13:54 | And then I'm just going to click that face there. |
13:57 | Let's just undo that, actually. |
13:59 | Take that off construction line type. |
14:04 | Clicking too many things at once. |
14:10 | So, include 3D geometry. |
14:13 | Select that. |
14:14 | Cool. |
14:15 | And then I'm going to kind of do a similar approach here. |
14:18 | Just find a way to kind of locate the rough center of this. |
14:23 | So, if I draw - sorry, I don't know why this is running so slow at the moment. |
14:29 | Sometimes when we're streaming things, it slows it right down. |
14:34 | So, construction line from the midpoint here to there and across there. |
14:43 | So, I know roughly the midpoint of that is going to be pretty good for the midpoint of that port, I guess. |
14:54 | Cool. |
14:54 | So, now what I'm going to do is I'm going to map out the trajectory for the, I guess, the center line of the tube for this port here. |
15:07 | So, I know in this case, this back port, I think that's cylinder 4 from this engine, is going to come along here, and then it's going to go into this other kind of opposite port on the turbo manifold. |
15:22 | So, I'll just hide that sketch again. |
15:26 | Cool. |
15:27 | So, I need to have my 3D sketch preference open now because I'm going to start kind of sketching in 3D space as I do this. |
15:36 | And we'll start off by just creating another construction line from the center point here. |
15:43 | And now that I'm in this 3D sketch kind of mode, as I click that center point, it's giving me options to select the active plane that I want to work on. |
15:54 | And we can rotate these and stuff as well, but it's just basically popping up this new coordinate system. |
16:00 | I can work on either of these two for now, but I basically just click that one. |
16:05 | I want to come around and just make a line that comes straight out kind of perpendicular from that port. |
16:16 | And that's automatically put the horizontal constraint on it in that case, snap to horizontal there. |
16:23 | So, that's good. |
16:24 | That's actually what I want. |
16:25 | But what we're going to do is kind of copy the original design and have, I guess, a bit of an arc coming out of here. |
16:35 | So, we're straight into a bent section. |
16:37 | It's still going to start tangent from that exhaust port, so the flow out of it isn't coming straight into a sharp angle, but it is going to go into an arc. |
16:49 | So, we'll start with the arc tool, and I'm going to select that point there for the base of my arc. |
16:56 | I'm going to sketch on this plane and just pick a point out here. |
17:03 | And I don't know what happened there. |
17:05 | Oh, snapped to the other plane. |
17:07 | I actually also want to make that not construction line type because we're actually going to use these now. |
17:14 | So, again, do that, select that plane. |
17:19 | I don't know why it's doing that. |
17:25 | Bear with me a second. |
17:31 | Arc, three-point arc, click the base point. |
17:36 | I'm going to select this plane, bring it out here. |
17:41 | Okay, for some reason that worked fine. |
17:44 | Don't know what it was doing the first time. |
17:45 | And then what I'm going to do is I'm just going to use a tangent constraint between this arc and that. |
17:52 | So, I know the arc's kind of coming straight out of the port at a nice angle. |
17:59 | Cool, and then I'm just going to dimension the radius of that. |
18:04 | So, in this case, we're going to use the largest centerline radius that Vibrant offered, which was six inches. |
18:10 | So, even though I work in metric, I can just still, in the dimension box here, click six, little semicolon for inches, and that's going to give me that arc coming out of the head there. |
18:24 | And I'll just come back. |
18:26 | And just for reference, turn the scan back on, and I'm going to drag this point kind of back roughly to where I want it here. |
18:35 | And the reason I clicked to view the assembly straight from the side here, and this is a reason to have your workspace all kind of lined up with your coordinate system, is if I drag it now, I know it's not going to move out of alignment with that plane. |
19:03 | Come on. |
19:05 | Not wanting to drag that for some reason. |
19:07 | There we go. |
19:08 | So, I'm just going to kind of set that on that weld line there. |
19:12 | Cool, and I'll turn that back off. |
19:14 | So, I did want to make a note here that when you're working with a 3D sketch like this in Fusion, and you're working with curves or arcs, it is quite hard to get them to be fully defined because essentially the arc can kind of move off axis a little bit, and it's quite hard to basically lock them down to the coordinate system. |
19:38 | So, don't stress too much if you are doing a 3D sketch and it's hard to make your lines go white if you're working with the gray background or black if you're working with the white background to show that it's fully defined in your sketch, which you generally always want to do. |
19:54 | It's quite hard to do if you're working with arcs like this. |
19:57 | But basically what I try to do is I use a bit of a wireframe to map out where the points land in 3D space. |
20:07 | So, for example, for this part, I'm just going to connect a construction line from the end point just back to the base here, and then I'm going to use a perpendicular constraint between that line and this kind of line parallel of the port. |
20:27 | And that's made it go really small or something. |
20:32 | I'll add a dimension in there first just to prevent that. |
20:35 | So, let's just set this at 53. |
20:38 | Looks pretty good. |
20:40 | And then do the same thing again. |
20:44 | There we go. |
20:45 | And I did see a tiny bit of movement there. |
20:48 | And if I view this from the top now, I can see that that arc is actually perfectly in line with that kind of horizontal construction line we drew earlier, whereas before it was just ever so slightly off. |
20:59 | And that can make a big difference when all these things stack up at the end. |
21:03 | And we're kind of wondering why the alignment isn't very good. |
21:07 | So, just something to keep in mind there. |
21:09 | Cool. |
21:09 | So, basically, I know if I get from Vibrant a 1.75 OD bit of tubing with a 6-inch centerline radius, I'll be able to kind of make this first section. |
21:22 | Then what I'm going to do is do another one here and then another curve up to the port here. |
21:30 | Cool. |
21:30 | So, we'll start off with that next one, a 3-point arc from the end point here. |
21:38 | And now what I'm going to do is I'm just going to rotate this down slightly to what looks about kind of tangent with this. |
21:48 | And then I'm going to select this plane, then drop a point out here, go like that. |
21:58 | Cool. |
21:59 | And just take that off construction line type because, yeah, I want it to be a real line, I guess. |
22:09 | Cool. |
22:09 | So, now ideally what I want is to get a nice kind of flowing transition between these two lines. |
22:17 | So, when we cut those tubes and weld them together, the fit-up's nice and close. |
22:22 | So,metimes you can do this by clicking tangent like that, but we can just see it's kind of dropped out of alignment with the plane I wanted that to be on. |
22:33 | So, what we're going to do instead is kind of use that same wireframe method that I used before. |
22:39 | And this does get a little bit fiddly, so just bear with me. |
22:43 | But I'm going to create a construction line here first on this plane, just coming back to here. |
22:50 | And I'm going to set this tangent with that line from before. |
22:56 | And same thing, I just want to make sure that is vertical above, kind of in that same plane that that's on. |
23:04 | And then I'm going to make a little bit more of a wireframe here. |
23:11 | And be aware that this kind of approach does take a little bit of trial and error to figure out sometimes. |
23:18 | It's not the most intuitive, but as you get kind of better with these constraints and understanding how it all works in 3D space, you get a little bit more of a feel for what's going to work. |
23:30 | Cool. |
23:30 | So, the end of that's on there. |
23:33 | So, I've just kind of made this other little wireframe to guide the second curve. |
23:39 | And what I want to do is make this line collinear with the tangent line before. |
23:49 | And then I want to make this now tangent to that. |
23:57 | So, that's kind of snapped that in. |
23:59 | So, I know this line's collinear or parallel of this one. |
24:03 | And then I know this first arc is tangent to that. |
24:07 | And then the second arc is tangent to this. |
24:10 | So, now essentially this arc must be tangent to this. |
24:13 | And this set up anyway. |
24:16 | And I'm just going to make that tangent there. |
24:19 | Cool. |
24:19 | And now I'm going to set the centerline radius of the second arc. |
24:25 | And I'm not going to use the same 152.4 or 6-inch centerline radius. |
24:31 | I'm actually going to use a tighter arc here, just based on what the 3D scan looks like. |
24:37 | I'm going to pull that into alignment soon. |
24:40 | But I'm going to use a 1D centerline radius. |
24:47 | So, it will be 1.75 inches. |
24:50 | We know that's the diameter of the tube we're using. |
24:53 | So, if I go 1.75 inches, that will pull that up there. |
24:59 | And that's already looking really good with that second part of the arc there. |
25:05 | If we view that from the top view, yeah, pretty good, I think. |
25:10 | Pull that second tube following the kind of centerline of it. |
25:15 | Cool. |
25:20 | What we can do as well is put another kind of dimension on that to control a little bit more. |
25:29 | But we'll just try to blast forward and draw the third arc into here. |
25:35 | So, before I actually draw that arc, what I'm going to do is just make a line from the center of this, a construction line, come down here on this plane. |
25:53 | Just coming down like that because I'm going to use that as a kind of tangent or try to use it anyway. |
25:59 | It might not work, but we'll see. |
26:01 | So, put another one in here too. |
26:07 | So, we've got this kind of horizontal line here along that face that I know is perpendicular or, sorry, just straight across that part. |
26:17 | But I can now make this line that I've drawn straight off that flange perpendicular to that one and that one. |
26:26 | So, that kind of fully constrains that or locks that down in space. |
26:31 | You see it go white there. |
26:33 | So, I know that's coming straight out perpendicular to the port. |
26:38 | And now I'm going to make another arc from here up to here. |
26:46 | Okay, and I've got that construction line type on, so I can just change that back to a real line. |
26:54 | Cool. |
26:55 | And now is the kind of tricky part, and this might not work really great, but I don't like that. |
27:09 | How are we going to fix this? So, let's just delete that and try to draw it again. |
27:23 | I'm just going to tilt this over a bit. |
27:36 | Sorry, bear with me. |
27:37 | Find that midpoint. |
27:44 | That looks a bit better. |
27:47 | Something like that. |
27:50 | Again, make that not a construction line. |
27:54 | That's pretty close to what we want, I'd say. |
27:57 | Let's try to tidy it up a little bit. |
28:01 | Make it tangent there. |
28:04 | Yeah, that looks pretty good. |
28:05 | And then I'm just going to use that same 1D centerline radius for that. |
28:12 | So, I'll just set those two equal. |
28:14 | And I know that this one here isn't tangent to that, and I don't think it will let me, just because of how it's all kind of constrained before. |
28:25 | But with a little bit more time and playing around with a wireframe system, I think we could probably true that up a little bit and kind of maybe put a short straight section in here to make sure this tube would come into that port. |
28:40 | But I won't spend too much time here. |
28:43 | We now have three kind of curves that lead up to that port, and the fit up between at least each of those three should be pretty good. |
28:52 | So, with that, I'm just going to finish this sketch for now, and I'm going to jump under the Create tab here and select the Pipe tool. |
29:00 | So, essentially what the Pipe tool does, and this is really handy for creating any plumbing that uses like a circular cross section or roll cages are also great. |
29:11 | If we have a 3D sketch, we can use this Pipe tool, and it's kind of like if you're familiar with CAD already, it's a sweep tool that automatically has the section or the profile set to either circular, square, or triangular in this case. |
29:27 | So, it just kind of gives you a default profile section, and then it's going to sweep that along the path or trajectory or whatever you want to call it. |
29:35 | So, great for creating something like this, which is tubular. |
29:40 | I'm going to make sure the chain selection is off because I'm going to create three separate tubes for this runner. |
29:48 | So, if I select the first one here, and I've already set this up before, so the section size is 1.75 inches. |
29:59 | And then the section thickness, we'll see how this goes, 0.065 inches. |
30:07 | And then just new body is good. |
30:11 | And we can see that that tube is there. |
30:13 | Obviously, this would need a little bit of work to match the kind of port here, whether we kind of deform or work the middle here to make it match and then weld it, or we use a little 3D printed section or something else in here. |
30:27 | We'll come back to that soon. |
30:30 | But there I go. |
30:31 | Got that first section. |
30:33 | I'll go OK that. |
30:36 | Sorry, I don't know why it's running so slow today. |
30:41 | And then I just want to make that sketch visible again. |
30:46 | And I'm going to create tube, essentially the same thing for the next section here. |
30:51 | I don't want to join. |
30:53 | I'm just going to go new body. |
30:59 | And then I'll do one more again for the last section. |
31:04 | When it goes there. |
31:09 | And it's trying to cut. |
31:11 | New body again. |
31:12 | OK. |
31:18 | Cool. |
31:18 | So, I can see it's a little bit different to the kind of 3D scan one there, but it's essentially the same idea. |
31:28 | I could play around with those arcs a little bit and dial it in and get it really close to what the original one is. |
31:34 | Or if I was just designing something new, I'd just work with it to get what I want. |
31:40 | But we can see there that if I just turn off the sketch, I have these three sections of tube that I could buy from Vibrant and kind of fabricate. |
31:50 | So, one approach, if I was just creating a fabricated tubular manifold like this, is do that for each of them. |
31:58 | Play around with different arcs and different sections of tube and just figure out what's going to work best. |
32:05 | And then at the end, I might be able to even measure the length of like these sections here. |
32:19 | So, it has given me lengths for each of the sections, so I have to add those together. |
32:24 | And I can figure out basically if I've got equal length runners, if that's something that I'm aiming for in that case. |
32:32 | But that's basically the idea. |
32:34 | So, you'd have them all snake around and basically have something like this. |
32:38 | So, that's one way of planning out a traditionally fabricated exhaust manifold like that, designing it in CAD. |
32:50 | Obviously, a lot more time goes into it than this, but we'll move forward and have a little look at a different approach that you can take, which would be more suitable for a cast or 3D-printed manifold. |
33:03 | So, what I'll do for now is just delete these three. |
33:08 | And I'm going to jump back into that same 3D sketch that we had because, again, it's using a similar approach, but I'm just going to create the 3D body a little bit differently. |
33:23 | But I'm still going to use the same kind of 3D sketch here. |
33:26 | So, rather than using these kind of more consistently curved arcs that need to match the raw materials that we can buy, what I'm going to do is just use a spline tool, the spline tool here, and I'm going to create a bit more of a free-flowing form for the runner. |
33:47 | So, I'll do that for these two middle ports here, and I'm just going to start by selecting the middle of that and then up. |
33:58 | Before I do that, jump onto the line type tool. |
34:02 | I'm going to come over and I'm just going to find that midpoint and then just create a horizontal line out there, and then I'm going to do the same thing and just make a vertical line down from that. |
34:18 | Oh, sorry, a line perpendicular to that port like we did before because I'm going to use that to kind of true up the runner that I create so it comes into that port nice and straight. |
34:30 | Cool, so I've got that there, and I can pull that through the backside so it's kind of out of the way as well. |
34:37 | All right, now let's jump back into our spline tool. |
34:40 | We'll find the middle of that port, and I'm going to start by just defining the two endpoints for the spline, which I keep doing that, not swapping off the construction mode. |
34:54 | So, straight spline at the moment, that doesn't work very good. |
34:59 | What I'm going to do is right-click on the spline and I'm going to insert spline fit point here. |
35:07 | So, I'm just going to put two fit points on that spline, and then what I'm going to do is I'm going to view from the side here, so I'm looking straight at it from one direction. |
35:19 | I'm going to have the 3D scan shown, and I'm going to basically drag that spline into kind of match the profile of this runner here. |
35:36 | Oh, shouldn't have done that. |
35:39 | Cool, so just drag this over here, drag this down here, and then I'll hide that for a moment. |
35:52 | If we click on the end of the spline here, you can see this little green line come up, and that's like the handle for the spline, and if I kind of move that around, you can see how it moves. |
36:02 | That's basically the line that the spline is tangential to. |
36:08 | So, if I make that line, actually, I'll make it horizontal, then I'll make sure that the runner is going to come straight out of that port. |
36:21 | So, make that horizontal there, and then, sorry, it's just going really slow today. |
36:30 | It's definitely not helping things. |
36:32 | I'm going to do the same thing at the other side here, but I'm just going to make this handle co-linear with that little line that we created before. |
36:41 | Cool. |
36:43 | Jump back into that side view, and then what I'm going to do is put another fit point in here, drag that down. |
36:59 | So, I'm just trying to kind of match, I guess, the shape of that runner. |
37:06 | Just tidy things up a little bit here. |
37:09 | I can drag the handle here to make it a bit shorter, which basically just controls the tangency weight of the spline coming out of that point, so how long it stays, kind of holds that tangent or that direction for before it kind of veers off that path to match the rest of it. |
37:30 | I'm just going to do that on both of them, just bring them in a little bit. |
37:37 | So, my view from that side looks pretty good, and then should do the same thing from the front here. |
37:45 | Just drag it into the center of the tube there, because I'm just kind of matching this design. |
37:52 | That looks like it's pretty good. |
37:54 | Cool. |
37:56 | So, I'll finish that sketch for now. |
37:58 | We'll come back to it in just a moment. |
38:00 | And the way I like to do these ones rather than using like the loft tool from the solid toolbar is I'll go to the surface toolbar here, and I'll just use a little bit of surface modeling to do it, and then at the end, I can basically thicken that up into a solid body. |
38:18 | But the surface modeling tools just give us a little bit more flexibility when we're creating more intricate forms like this. |
38:24 | So, a loft, for those who aren't familiar with this type of stuff in CAD, can basically transition one cross section into another. |
38:32 | So, if we look at what we've got here, we have this port, which is the slot or oval shape, and we're going to transition it into this quadrilateral shape here, four-sided shape that's a little bit different. |
38:46 | So, it's really good for kind of blending one cross section shape into another, like a square into a circle or triangle or so on, something like that. |
38:54 | So, what we're going to do is we're going to do a loft between these two points and then use this as a guide for the center line to kind of set the path that it's going to take. |
39:06 | So, loft tool for the profiles, what I'm going to start by doing is setting the chain selection on. |
39:13 | I'm going to select that for profile 1, and then I'm going to come over here and select this for profile 2. |
39:20 | And we can see that it's already tried to put this surface between them here. |
39:27 | So, the next step is to come down to the rails here or the guide type. |
39:33 | I'm going to set it as a center line guide rather than the rails. |
39:36 | And for the center line, I'm going to select that spline that we had before. |
39:43 | And we can see that that's kind of created this new runner, which is the cross -sectional shape of it merges from the slot into this other shape kind of as it goes, and it follows that center line trajectory there. |
39:59 | And I'm just going to have that as new body for now, which has to be anyway because it'll be our first surface body. |
40:04 | And I'm going to click OK. |
40:07 | So, that's all good. |
40:09 | If I turn our first runner back on, we can see we've got some kind of interference here. |
40:15 | So, what I could do is jump back into that sketch, view it from the side, and I can just pull these over a little bit just to kind of make some more clearance there. |
40:30 | Jump back in. |
40:31 | You can see it's still touching a little bit, but that's the kind of approach that you'd take to kind of going back and forth and modeling something like this. |
40:38 | You can just drag that spline around a little bit to get it how you want it. |
40:42 | We could pull it up about here to make that a little bit shorter and so on. |
40:46 | But that's the approach. |
40:48 | So, what I'm going to do now, just jump back into this other one. |
40:52 | I'll do this one a little bit quicker. |
40:55 | So, I'm going to do this runner here from this port to same one, just following the same kind of approach that I did before. |
41:12 | Next, I right-click on that line, insert spline fit points, and I'm just going to put three along here. |
41:23 | Generally, with splines, it depends what you're trying to follow, but I'd avoid having too many of these fit points because it just makes things quite messy and the spline loses its kind of smooth flowing shape. |
41:40 | So, grab that handle. |
41:43 | Things are so slow. |
41:47 | So, next I want to make this handle come straight out of this port. |
41:51 | So, if I just drag it a little way first like that, it's looking pretty good. |
42:00 | And I'll set that to horizontal out of that port. |
42:03 | And then this other one up here, I'm going to go collinear with that. |
42:11 | And that's really short. |
42:13 | So, just drag it up a bit. |
42:17 | Cool. |
42:18 | And then come to the side, do this, and then I'm going to start dragging this into the shape to match this runner. |
42:29 | So, I've kind of got to grab the wrong thing there. |
42:36 | I've kind of got to do that from the side direction. |
42:41 | And then this direction here as well. |
42:46 | So, I'm looking at it from two different angles. |
42:50 | And we'll just check the top. |
42:53 | Which looks pretty good. |
42:57 | So, just making sure it's following that path in three directions. |
43:00 | I know it's getting kind of harder to see here. |
43:07 | Even I'm losing it. |
43:09 | Oh, yeah, that's because that's way over there. |
43:14 | So,mething's gone wrong here. |
43:16 | It's snapped up onto that flange for some reason. |
43:22 | Cool. |
43:22 | All right. |
43:23 | We're looking a little bit better. |
43:32 | Just kind of matching where those weld points are on the original one. |
43:39 | It gives us a nice kind of path to follow. |
43:42 | All right. |
43:44 | Cool. |
43:44 | Turn that off. |
43:46 | We can see what we've done there. |
43:50 | Just going to shorten up that handle there a bit. |
43:57 | And then maybe extend this one a little bit. |
44:00 | But this is kind of back and forth approach that you take and just play with it until you get something about right. |
44:06 | Cool. |
44:07 | Finish that. |
44:08 | Same thing. |
44:11 | Profile. |
44:12 | This port. |
44:13 | Profile one. |
44:15 | Profile two is this port. |
44:19 | Guideline. |
44:20 | Guide rail. |
44:21 | Guide type is the center line and then choose the center line and then chain selection. |
44:27 | If I select that now because I've got two, it's trying to kind of go nose to tail. |
44:31 | So, just take that chain selection off and just select that profile there. |
44:37 | We can see that's created that there. |
44:41 | And new body is good for that. |
44:44 | And I'm just going to hide that first runner again. |
44:47 | I'm going to hide those sketches. |
44:49 | So, we can see we've got our two flange solid bodies here. |
44:53 | And then we have our two surface bodies for those runners. |
44:57 | And I'm just going to show you how we'd kind of combine those into one and then thicken them up into a solid body that can actually be manufactured because essentially at the moment they're infinitely thin. |
45:11 | They're just a surface. |
45:13 | What I'm going to do is just remove the flanges. |
45:17 | And if we look into the end of it here, we can see we don't have basically each runner is blocking the other runner's flow. |
45:25 | So, we just get this funny little volume in the end here and it's not going to really work. |
45:29 | So, what we can do is just jump into here and use the split body tool. |
45:35 | Actually, back myself up a little bit. |
45:38 | First, what we need to do is just create a copy of these two. |
45:44 | So, if I go move copy, create copy. |
45:49 | And then for the other one as well. |
45:51 | We actually only need to do one, but I'll just do both of them for the sake of it because as I use one to cut the other one, it's going to delete the area that I need to use to cut the next one. |
46:03 | It'll make a little bit more sense as we go, but here split body. |
46:07 | So, if I split this body with the splitting tool being the other runner, I can extend that a little bit. |
46:14 | And that's going to cut the other one. |
46:17 | And then we can see we have this little part of the body here. |
46:22 | And then I can remove that. |
46:24 | And then we have another little section here just because of the kind of angles that they're collecting on. |
46:36 | I'm just going to remove that because I think that'll cause a little bit of issues. |
46:40 | Yeah. |
46:41 | Cool. |
46:41 | And then what I'm going to do is jump back into here, split body. |
46:46 | Now, I'm going to split this body and I'm going to use this tool here. |
46:59 | Cool. |
47:00 | Okay. |
47:07 | Bear with me for a second. |
47:10 | Okay, cool. |
47:12 | Now, what have we got? Don't want that one. |
47:25 | This one we want to remove. |
47:30 | Cool. |
47:32 | And this one we want to remove as well. |
47:35 | All right. |
47:36 | So, now we just want these two here. |
47:41 | I'll remove these other ones so we don't get confused. |
47:45 | And we can look down inside and see how they kind of collect. |
47:48 | It's like a merge collector. |
47:50 | They join into a single tube here. |
47:53 | So, the next step is going to be stitching these two together. |
47:57 | So, use the stitch tool and then stitch the two surface bodies. |
48:01 | And we can see the green line here is where they are going to be stitched together into one. |
48:07 | And then the next step from here is we go thicken. |
48:12 | And we just select that body. |
48:15 | And we can already see here I've got it set to 1.6 just to kind of match the wall thickness of the tube we're using before. |
48:23 | But we could change that to, oh, that's gone to 23, which is too thick for it anyway. |
48:30 | But we could change it to two millimeters and so on. |
48:34 | And we can also just change the direction that it does that. |
48:39 | But this is actually good. |
48:40 | So, it's just keeping the internal measurement the same, and it's adding that thickness to the outside of it, which is what we want so we still get that nice flow into our ports. |
48:52 | It's matching that original port shape. |
48:54 | New body is good. |
48:56 | And then if I find my two flanges again here, we've got these solid bodies, and we can go back to our solid toolbar, use the combine tool, and just go one, two, which for some reason it's not liking. |
49:14 | Bear with me. |
49:16 | Target body. |
49:16 | Okay. |
49:17 | One, two, three. |
49:20 | Okay. |
49:23 | All right. |
49:24 | For some reason, I didn't like that, probably because of this little gap here. |
49:27 | But the idea is that we merge them into a single body again. |
49:33 | And then as you can see, we've got this nice kind of flow. |
49:37 | Merge collector into this port here. |
49:39 | And then if we look inside these other ports, it's the same thing here. |
49:44 | And we've got this kind of solid body. |
49:46 | We could do the same thing for the other two runners here. |
49:51 | Play around a little bit with the shapes as well and get that dialed in and start kind of getting a design that we're happy with. |
49:59 | Then like I said, we've got a physical model from there. |
50:02 | We could do CFD with it and so on. |
50:04 | We could 3D print it out of plastic as well just for a test fit. |
50:08 | Lots of different ways that we can do it. |
50:12 | If we're designing an intake manifold for a naturally aspirated application as well, we could probably 3D print it using MJF or SLS with like a glass-filled nylon or carbon -filled nylon, which should be able to survive typical temperatures, especially for a streetcar. |
50:31 | So, there's a lot of different options of ways we could take it from there. |
50:35 | So, again, if you had any questions come up during that, just feel free to ask them in the chat and I'll do my best to answer them soon. |
50:43 | I just want to explore kind of like a third option, I guess, where you combine the approaches that we've taken here. |
50:55 | So, we could do, for example, like a 3D printed or machined or cast even little transition from the port here into a circular shape and then we could then use like a traditional fabrication approach to make a tubular manifold from there. |
51:18 | So, it's just a slightly different way to match that port shape there. |
51:23 | So, I'll just have a look at that now. |
51:25 | I turn that sketch on. |
51:28 | Just going to create a new plane off this face. |
51:34 | Let's bring it out, say, 30 millimetres, but we can play with that a little bit. |
51:39 | I'll turn that construction mode on there and I just want to sketch on that plane. |
51:46 | Then what I'm going to do is project this line and then turn off the 3D sketch tool here and then I'm just going to create a new circle centred on that. |
52:02 | That's going to be our 1.75 inch tubing and we'll add the wall thickness to it soon. |
52:13 | So, then same thing, we can just come back into our surface toolbar after that sketch finishes up. |
52:23 | Surface toolbar, use the loft tool to loft from, using the chain selection, loft from the port to the circle and we can kind of change how it leaves that to direction, direction here so we get this nice kind of transition and then I'll just go OK. |
52:50 | Same thing here. |
52:52 | I can thicken this up by 2 millimetres and then what we can do, actually in that case I want to go 1.6. |
53:06 | Yeah, 1.6 and I actually want to jump back into this here and because the tube, that's the outer diameter of the tube, 1.75 and then minus 1.6 times 2 is 3.2 millimetres. |
53:21 | So, see how that goes and then that means when the thickness is added to the outside, that should be 1.75 on the outside now. |
53:35 | Cool. |
53:36 | So, we could then just 3D print these little transitions like that and then weld them onto the flange and then weld the tubes to that so it's kind of like a little quick way to make a nice little transition there. |
53:50 | You can use these for merge collectors or in the case where you have a cylinder head where essentially the exhaust manifold is like four different flanges. |
54:03 | So, like you had just this was divided into four different sections. |
54:09 | You could actually just include this in the flange design as well and then get that whole flange 3D printed and then come along and you could clamp them to a table or a jig or the cylinder head and then do the fabrication from there. |
54:25 | So, just a little bit of a different approach to take. |
54:27 | It's a useful way to get to that point using CAD. |
54:32 | So, yeah, hopefully that's given some insight. |
54:35 | I'll just jump into the chat now and see if there's some questions and do my best to answer them. |
54:42 | So, AMT97Racing, "Recently I cracked my boost record on a diesel build pushing 50 PSI of boost but we saw very little returns compared to 45 PSI I assume we ran out of cylinder head flow.". |
54:56 | Yeah, that's really not my area. |
54:58 | Definitely a question better to ask Andre. |
55:02 | Yeah, it seems like flow is probably the problem when you're increasing the boost pressure, but not making any more gains either manifold, turbo or cylinder head aren't keeping up, right? AMT97Racing, "How about 3D printing? I know Inconel can be done but it's super expensive. |
55:22 | I've looked into 316L SML stainless printing, but you're extremely limited on the temperature.". |
55:33 | Yeah, I'd be interested to know the temperature of the 316L, because I think like for most applications, I think it's pretty good, but maybe you're talking about diesel stuff where the exhaust temperatures are much higher. |
55:51 | So, I'm not really sure there. |
55:54 | But I'll just say if you're interested in 3D printing and you're looking for more 3D printing metals rather and you're looking for options that are a little bit more affordable at the moment, check out Craft Cloud because some of the Chinese 3D printing manufacturers are really, really accessible and affordable and they're doing some actually really good results. |
56:20 | We got our Merge Collector stainless, yeah, 316L like 4 to 1 Merge Collector printed through Craft Cloud for our 3D printing course and the price that we got for that was pretty comparable to like a fabricated one that would be for sale, that would be the equivalent. |
56:40 | So, yet to try it in an application, I imagine a naturally aspirated four -cylinder, the temperature rating would be fine but maybe a forced induction diesel, maybe it would be pushing it, not too sure. |
56:53 | It would be cool to hear a little bit more about that though if you want to send us some photos or something, if you do anything. |
57:00 | Nick M, "What's the best way to make tighter bends than 180?". |
57:08 | Tighter bends than 180, like you mean more than 180 degrees or you mean like tighter as in a smaller radius? A little bit tricky one to answer, tighter bends than 180. |
57:24 | Let's just say that you're talking about Vibrance offerings for their off-the-shelf kind of sections, then a way to get it tighter would be to look at like 3D printed, 3D printing them rather than getting a mandrel bent tube. |
57:49 | Yeah, we'll just leave it at that anyway. |
57:53 | Sorry, just bear with me while we're getting one more question coming through. |
58:04 | Cool. |
58:08 | So, ampt97racing again says, "You would 3D print a flange and then weld to it? Very interesting.". |
58:13 | Yeah, so the little experience I've had with welding to 3D printed parts is you can definitely do it, but it's definitely not as nice as like, you know, your typical fabrication materials. |
58:27 | It's more similar to welding to something that's cast because it has a kind of similar grain structure to a cast part. |
58:35 | Maybe not quite as nice as that again, but it can definitely be done. |
58:40 | And what material we're talking about, so stainless, for example, aluminium, any of them, titanium, they can all obviously be welded to it. |
58:50 | It's just the same as working with your typical materials. |
58:54 | One more question from the HPA website. |
58:57 | "Finding a smaller CLR would also effectively reduce the area needed for the bend correct. |
59:05 | Centreline radius.". |
59:06 | Yeah, yeah, of course. |
59:07 | Like if you can find a tighter or a smaller centreline radius, it's going to be a tighter bend. |
59:13 | Yeah, completely. |
59:14 | So, hopefully that answers Nick's question up above. |
59:18 | But we'll leave it there anyway. |
59:19 | That's all the questions. |
59:20 | Hopefully that's given some insight into some 3D modelling techniques that you might not have been too familiar with before. |
59:28 | I really like using that loft tool with the centreline or the guide rails to kind of guide the shape of it. |
59:35 | There's a lot more you can do of it as well, but that's the typical approach that I'd take to modelling at least the runners on intake or exhaust manifold or any other kind of plumbing or something like that where it has that shape that's going to guide fluid flow. |
59:53 | Typically set up with your flanges, have them where you want, and then use these 3D sketches to map out the trajectory of the runners and then use the pipe tool is really good if you're just working with kind of traditional tubular materials. |
01:00:10 | The loft tool or the sweep tool even can work for kind of more intricate shapes or a bit more of a free-flowing design that would suit like a cast part a little bit more or a 3D printed part as well. |
01:00:25 | And obviously different flanges here would work and you could have this all coming into a single V-band flange and you could also include here like a wastegate flange or something like that. |
01:00:39 | And the trick is when you're working with those more intricate shapes like use surface modelling tools and then use each body to cut the other one so you get a nice kind of merge collector as they all come together. |
01:00:53 | Stitch those bodies together and then thicken them into a solid body, merging that back into the flanges and then you have a full solid part that you can manufacture from there however you're going to go about it. |
01:01:05 | So, yeah, hopefully that's given some insight and we'll be back next week with another one of these webinars. |
01:01:11 | So, thanks for watching. |
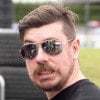