119 | Dyno Operation - Torque Test
Summary
The Mainline dyno offers the ability to perform advanced tests to help optimise many tuning parameters. In this webinar we will focus on the Torque Optimisation Test and discuss how to configure it to help optimise ignition timing, cam angle, injection timing and air fuel ratio.
00:00 | It's Andre from the High Performance Academy. |
00:01 | Welcome to this webinar where we're going to be looking at the torque optimization function on the Mainline Chassis Dyno. |
00:09 | Now for those of you who have viewed our other webinars, we have already covered this in our Mainline Chassis Dyno setup webinars to date, however this will be a slightly more detailed and specific look at solely that function. |
00:24 | If you're interested in the Mainline Chassis Dyno operation and you haven't already viewed those other webinars, please check those out in the archive by searching for Mainline. |
00:34 | I think we've got about three in there now, and they will give you a more complete and more rounded view of how the Mainline's advance functions work. |
00:43 | Alright, so we'll start with what exactly is torque optimization. |
00:47 | This is terminology that Mainline use, and this is actually one of the things that drew us to the Mainline brand initially, because it makes our job with training and explaining complex concepts quite easy. |
01:01 | So put simply, the torque optimization test in the Mainline Chassis Dyno will allow us to plot any particular parameter we like, versus the torque being produced at the rear wheels. |
01:15 | So what this allows us to do is analyze any particular parameters that are going to have a significant effect on the amount of torque that the engine produces. |
01:26 | And when I'm talking about these parameters, I'm considering things such as cam timing, ignition timing is a great one, this is one that I quite frequently demonstrate, also air fuel ratio and injection timing. |
01:41 | So essentially, anything that can have an influence over the amount of torque that the engine produces, we can plot these using the torque optimization test, and this will graphically show us what particular aspect or what particular point with that channel is going to give us the optimal torque, and even further than that, the Dyno will also, once we've completed the torque optimization test, will also show us at what point for that particular parameter we achieved maximum torque. |
02:15 | So this makes it very easy, for example, to decide exactly what ignition angle produced optimal torque, and then we can simply set the cell that we've been performing that torque optimization test in to whatever that value is in this, for ignition timing we call this MBT timing, maximum brake torque timing, it's also referred to as minimum timing for best torque. |
02:40 | So it makes it very, very easy. |
02:42 | Now, of course I'll just mention as well, this isn't necessarily a technique that we're going to go through and apply to every single cell in our ignition table or perhaps our cam timing table. |
02:56 | It would physically just take an eternity to get the engine tuned. |
03:00 | So typically, when we are tuning something like ignition timing, we'd conventionally use the torque graph on the Dyno, and we're simply going to be looking at the torque graph, making adjustments to our ignition timing, and then figuring out, watching that torque graph to decide when we've reached MBT timing, and this is a technique that I demonstrate in our practical Dyno tuning course as well, for any of you who have gone through that course. |
03:30 | So this is a quick way of doing that, because we are simply able to watch that torque graph, tune and optimize the cell, then move into the next cell and repeat the process. |
03:41 | However, quite often we can be chasing very, very small changes in torque, and also sometimes that can be useful to perform our torque optimization test as a little bit of a sanity check just to make sure that we are in fact moving in the right direction and we have reached optimal timing. |
04:00 | So this torque optimization test definitely isn't something we're going to be using in every single cell of every single table when we're actually tuning. |
04:09 | I'm just going to get our Toyota 86 up and running, and for today's demonstration, we obviously are using our Toyota 86 with the Motec M150 ECU, but of course, this is going to be, the tests we're going to go through will be 100% relevant to any ECU that is supported by the Mainline Chassis Dyno with CAN communications, and realistically, that list is so long it's hard to imagine what ECUs out there aren't supported. |
04:38 | Let's start by jumping across to our Dyno and we'll just go through the basic setup to get the CAN communication up and running. |
04:48 | So if we go to Setup and we go down to External Devices, and then we want to click on Setup Data Devices. |
04:56 | So this also will require if you're going to bring in data via CAN, this does require an upgrade for your Dyno. |
05:04 | So the base model Dynos don't have this by default, you'd need to contact Mainline to see what's involved to activate this. |
05:13 | And essentially what I've got here is a simple two-meter long CAN-Bus that goes from the Dyno, there's a USB to CAN dongle, and then I've got a termination where I can simply plug that into the car while it's on the Dyno. |
05:29 | Now, this allows us to perform the torque optimization test but it also means that we've got access to almost all of the data that is being seen on the laptop screen as well. |
05:41 | So this makes it really really powerful for analyzing any of the aspects of our tuning at a later point, inside the Dyno software. |
05:49 | Alright, so at the moment you can see that in our Dyno we have our ECU communications setup here, and we've got our Motec M1 general template selected. |
06:00 | So obviously I've already got this communicating, but if we come over here to the right, we can simply select the ECU or device that we want to communicate with from this dropdown list, and I'll just move through this so you can see how extensive this list is. |
06:16 | There's not a lot of the mainstream and even less mainstream ECUs that are out there available on the market that aren't supported in this list so at the moment we are on M1 general, there's also some more specific M1 templates as well listed in there. |
06:34 | And what we can do there is if we just click Set Default once we've chosen our particular template, that's going to set up the communications for that particular template and specifically there it's going to be setting the address, the CAN address for all that information coming through. |
06:53 | If we want to go a little bit further and customize that, one thing I do have to do here, because of the way the M1 ECU is configured in our Toyota 86, it is communicating at a slightly unusual speed, which if we click on Channels, we can see our Bus Speed here is set to 500 kilobytes per second, whereas by default this would be one megabit per second. |
07:15 | And that's simply because we're also communicating in the 86 with the factory CAN-Bus so the speeds must match. |
07:23 | So that's an important part here. |
07:24 | However, that's all up and running now, and also another aspect of that, if we click on the CAN-Bus Analyzer, this is a really rudimentary and basic CAN-Bus analyzer, we'll be able to see all of the information that's available on the CAN-Bus. |
07:39 | So I've actually used this and if you've seen our CAN webinars, I've actually used this to demonstrate how we can use the Mainline Dyno as a CAN analyzer and how to decode and find data in the CAN-Bus. |
07:55 | So that's all of the information currently available on the CAN-Bus being connected to the Mainline Dyno. |
08:02 | Okay, so at this point, I'll also mention we've got our User 1 input, which is a Motec LTC network, so that's our lambda CAN network and that's where we're getting our lambda or air fuel ratio data from. |
08:16 | And that is actually still coming in from the Motec M150 as well, that's coming from the LTC connector to the M150, so that's all coming in from the car, and it's all just being communicated over a two wire bus. |
08:33 | So at this point, we've got all of that information coming through, and if Colin can just show this right screen on the Dyno, if that's not visible, I'm not quite sure. |
08:43 | This just gives you a really quick glimpse of some of the information I've got set up here. |
08:47 | We can choose anything we want, so let's right click here on this particular box, and if we move down the list we can see there's a little enunciator before each of the channels that are available, and what we're looking for here, the channels that are being sent via the ECU, via CAN, will all have the little E enunciator before them. |
09:11 | So for example, if I click here, that will now bring up engine speed, obviously we've got a replication here, we've got it right this side, but let's have another look. |
09:19 | We can have inlet manifold pressure, let's have throttle position, or basically anything we want. |
09:25 | I'll also mention in the Mainline Chassis Dyno, the data on this particular screen on the right is only useful to a point. |
09:33 | It's useful to watch when we are running the engine in steady state, but when we're actually doing a ramp run, what we find is that this information only updates, I think at around about two times a second. |
09:46 | So it operates way too slowly to actually be useful to us during a ramp run. |
09:52 | But of course, I'll just demonstrate this quickly. |
09:56 | If we go to our ramp run screen, we will see that across the top of our ramp run screen, this is currently set up for a Link G4 Plus, as we can see by the little label at the top, but all of these little boxes here, which we can configure to display any of the data, either coming directly from the ECU or alternatively, coming from the Dyno itself, we can display all of that data and this updates very, very quickly. |
10:23 | So this is the sort of data that we're actually going to be watching during a ramp run. |
10:28 | Okay, so now we're going to actually have a look at our torque optimization test. |
10:33 | And we can get to that by going to Test, and then click on Torque Optimization, which is about halfway down that long list. |
10:41 | Now this brings up our torque optimization screen, and I'll just give you a little bit of a tour of this particular screen. |
10:48 | So first of all we have our torque, so this is coming from the load cell on the Dyno, so this is what the Dyno is actually measuring. |
10:56 | So we've got torque in newton meters on our vertical axis, and then we have whatever the parameter we're interested in is being displayed here on the x axis. |
11:06 | And we also have some live data here on the right hand side. |
11:10 | We've got in this case, I'm currently set up for fuel timing, so this is the injection timing, in this case on our 86, it's the injection timing of the primary or direct injectors. |
11:22 | We have the torque, obviously currently I'm just sitting here idling, so the engine's not running on the Dyno, so we're measuring zero torque. |
11:29 | We've got our engine RPM and of course we've got our throttle position. |
11:33 | Performing the torque optimization test does take a little bit of practice and it is a little bit of an art to it, because of course we are, particularly in some instances, looking for really, really small changes in the measured torque. |
11:49 | And it can take, perhaps 40 or 50 seconds to perform a full torque optimization test, so over that time we want to make sure that we're holding our throttle very, very stable because if we move the throttle, understandably that's going to give a fairly big influence to the amount of torque that's being measured and we're going to end up seeing that displayed in the graph that we produce, and of course the data is then somewhat useless to us. |
12:17 | So it does take a little bit of time to perfect this. |
12:20 | What we'll do is we'll click on our setup screen. |
12:24 | And this is where we can set up our torque test, our torque optimization test. |
12:28 | And there's a few parameters here that we need to consider. |
12:31 | The first thing to do is bring in or make sure we've got the channels that we're actually interested in testing being brought in. |
12:39 | So we can do that by clicking on the Select Channels tab and on the right hand side of this screen we've got all of the channels that are currently available to us for the torque optimization test. |
12:50 | So you can see I've got ignition timing, throttle position, ignition timing again, as a backup. |
12:56 | I've got inlet cam one position, ambient temp, not particularly sure how useful that would be, and then I've got fuel timings by primary and secondary. |
13:05 | And again, if we decide we want to look at any particular parameter, let's just see what we've got here, I'll see if there's something I can just drag through for an example. |
13:16 | Where are we? Probably gone a little bit a far through this list now. |
13:24 | Okay, so we've already got fuel timing secondary, but just to demonstrate this, because there's no point me searching for another one just for the sake of it. |
13:33 | What we need to do is click on the one we're interested in, and then just drag it across to a position on this list, and there it pops up. |
13:42 | So once we've got all of the channels that we're interested in, we can go back and we can start by defining our test. |
13:48 | So I'm gonna perform a few different tests here. |
13:52 | One of these you've probably seen if you've been following our courses or our webinars, which is the torque optimization test for ignition timing. |
14:00 | It's probably one of the more common ways of using this particular test. |
14:04 | So what I'm going to do is choose the item or channel source for our x axis, so in this case, obviously that's going to be ignition timing. |
14:14 | Now what we're going to do is select here a minimum scale of 10 to 50 degrees, so really we can set this over whatever we're going to vary our parameter across. |
14:27 | So for ignition timing, 10 to 50 degrees is probably a pretty good range. |
14:32 | On the other side of this we've got our torque scales, and I just generally, as a rule of thumb I like to leave this manually scaled and just make sure that the scale I'm using is going to suit whatever the measured torque is. |
14:44 | A reason for this is if we have our torque scale set too closely over the range of the parameter we're viewing, it can start to look a little bit haphazard, so often having a slightly broader scale gives you a bit more idea of exactly what's going on. |
15:01 | So let's just get our engine up and running now, and we'll perform this torque optimization test for ignition timing. |
15:10 | And what we'll do is, this is one of the little tricks with the torque optimization test, is we need to be operating at the RPM set point that we want to test before we actually start the torque optimization test. |
15:27 | So on the left hand side of our Dyno screen here we have our speed control and normally we can change that with our F11 and F12, and during the torque optimization test, we can't do that. |
15:41 | So what I'm going to do is we'll just close down our torque optimization test and what I want to do is just bring, I'll just actually turn off my traction control. |
15:49 | What we want to do is bring our engine speed up for this particular test to 2,500 RPM, or let's make it 2,000 RPM. |
16:02 | And we'll get into fourth gear, and let's just jump across to our laptop screen for a moment. |
16:10 | Oh, actually I think Colin should actually have a complete screen drawn up for this where we can see both the torque optimization test as well as my laptop screen at the same time. |
16:20 | So what I'm doing at the moment is I'm just going to get central at 50% throttle and 2,000 RPM, actually I'll bring it up to 60% throttle there. |
16:33 | So just want to stay central in this particular zone. |
16:37 | And currently we're measuring at about 100 newton meters of torque. |
16:41 | Okay, so now what I'm going to do on the Dyno is we'll just open up our torque optimization test and for this test, just so it's really nice and clear and there's absolutely no chance of interpolation, what I'm going to do is I'm going to start by setting all of the cells that I'm interested in including the cell that I'm centered on, I want to set them all to 10 degrees. |
17:00 | That's the start of my test, I obviously want to start with the most retarded timing possible and then we're going to slowly advance that. |
17:08 | So we're going to now click on Begin. |
17:13 | I'll just make sure I'm centered in that cell before I start that. |
17:16 | We'll click on Begin and now what I'm going to do is advance the timing at basically a degree a second. |
17:24 | So we've clicked on Begin now, and what I'm trying to do here is just make sure that my throttle position stays really, really accurate or as accurate as I can, and we're just going to advance the timing up. |
17:38 | And you can see that as I'm doing this, the Dyno's starting to draw a little red line which shows how the torque is varying as our ignition timing advances. |
17:49 | So it's coming up through 18 degrees now. |
17:52 | And again, as you can see, just while I'm talking here, it is quite tricky to maintain a really constant throttle position, which is so critical with this particular test to ensure that the results are really meaningful and are going to give us a good idea of where we're going to end up with peak torque. |
18:13 | Alright, so we're just coming up through about 24 degrees now, we'll just keep coming up, I probably won't go all the way through to 50 degrees in this particular example, there's really no need. |
18:24 | So we can see there on the Dyno screen that our throttle is sitting pretty stable there at 23%. |
18:31 | Just coming up through 30 degrees now, and you can see that we've basically plateaued now. |
18:38 | And what we'll probably find shortly is that our torque is actually going to start decreasing. |
18:47 | So at this point, once our torque starts decreasing, essentially what that means is that now our combustion pressure is actually fighting against the piston, making it harder for the piston to come up towards TDC and that's why we actually start seeing the engine torque start to reduce. |
19:05 | Okay, so we're up to about 44 degrees now, I'm just going to back off and let's have a look at the results that we just achieved. |
19:12 | Okay, so there's a little bit of an art to also analyzing the results of a torque optimization test. |
19:19 | What we can see is the general shape that we'd expect to see. |
19:22 | So we started really low here in the torque, at about 75 newton meters with 10 degrees, and what we can see is as we start with very, very retarded timing and we add a couple of degrees, we see quite a dramatic increase. |
19:36 | So over that first five degrees, we've gone from about 75 to a bit over 95 newton meters. |
19:43 | And that continues, we probably get a similar gain as we add a second five degrees and we go up to 20 degrees. |
19:49 | What we can see then though, is as we get past 20 degrees, the sort of gains that we get are much, much flatter. |
19:56 | And once we get past around about 26 degrees, right through to, in this case about 36 degrees, we really haven't seen any change in our engine torque. |
20:06 | So that's an important aspect of seeing exactly what's going on with our torque versus our parameter, in this case ignition timing. |
20:14 | Now the Dyno does show us at what point we reached peak torque. |
20:19 | So in this case, it's telling us that the white crosshairs that it's drawn in here at 35.8 degrees of ignition advance, we've ended up with 127 newton meters of torque. |
20:31 | Now that's all well and good. |
20:32 | That is, for this particular example, the absolute peak torque value that we saw. |
20:38 | What we do need to keep in mind though is how well we performed that test. |
20:42 | If we were starting to fluctuate the throttle position slightly, or the engine really wasn't running central in the same cell for our entire test, this is gonna have a big impact on the accuracy of this MBT test or this torque optimization test. |
21:01 | What we really want to do is look a little bit more broadly at this and be a little bit more sensible. |
21:05 | So for this particular example, we can see that the Dyno's shown us, yep, 36 degrees, 35.8 degrees is where we've reached the MBT but let's look at it and we see that realistically our torque has been completely flat from around about 27 or 28 degrees of ignition advance, all the way through to 36. |
21:25 | So for safety's sake, really what I'm going to do in this case is I'd actually choose the fist point where we start to see this plateau, around about 27 or 28 degrees. |
21:36 | And then as well, we also need to consider our particular engine. |
21:41 | So at this point in the Toyota 86's operating area, we're well into vacuum in our ignition table, there's very little load, you saw I was only using around about 22% throttle. |
21:52 | There's very little load on the engine. |
21:53 | So at this particular point, the engine will not knock, regardless of how much ignition timing I use. |
22:00 | However in some engines, we may find that the engine is quite prone to knocking, and this is an area where we would start using our common sense. |
22:09 | So for example, if we find that we're making peak torque at around about 28 degrees, but we know that the engine is going to start slightly suffering from detonation if we were using perhaps 30 degrees, it gives us a relatively small window to operate in. |
22:26 | So in this case if we use some common sense here and we look at the torque graph, if we dropped our timing from 28 degrees to perhaps 26 or 27, we can see we're only dropping a few newton meters so there's really an almost unnoticeable drop in our engine torque, and for me that's worth it to buy myself a wider window from that knock threshold and reduce the chances of our engine suffering from detonation. |
22:53 | So when we've got the torque optimization test complete though, this gives you all of that information. |
22:58 | You can straight away see where peak torque is, and more importantly, or just as importantly, we can also see what that sort of spread is in terms of how much torque we're going to lose as we start pulling the timing back from MBT, if we've got an engine that is sensitive to knock. |
23:17 | Alright, so that's a quick demonstration of using the torque optimization test for our ignition timing. |
23:26 | And again, this is a relatively common test or common use for the torque optimization test. |
23:32 | We're gonna go through a couple more examples now, and this time what we're going to do is we're going to set up our torque optimization test for cam timing instead. |
23:41 | So what we're going to do is we're going to choose Inlet Cam 1 Position from the ECU here. |
23:48 | In this case, we're going to start with our timing from, I think we can go between minus 10 and about 50 degrees. |
23:57 | So that's probably a good enough test here for us to demonstrate. |
24:02 | I'll try and use exactly the same point in our operation as well. |
24:07 | And this time what we're going to do is go across, let's look at our Dyno screen, we're going to go, sorry, our laptop screen. |
24:14 | We're going to go across to our inlet cam position table and what I'm going to do is choose 2,000 RPM again. |
24:23 | We'll get our engine running in fourth gear. |
24:30 | And you'll see that my cam timing tables here are defined relative to throttle position. |
24:36 | And again, this is a slight peculiarity with just the way I have our Motec running. |
24:43 | Normally this would be based off manifold pressure. |
24:47 | Okay, so we've got our engine running now, I'll just actually bring us down to, let's do 30%. |
24:56 | Okay, so I'm running in now 30% zone, but what we can see straight away on our Dyno is we're way off the chart. |
25:05 | So we're making too much torque, we're currently sitting at about 210 newton meters. |
25:10 | So what I'm going to do is just change my scaling and what we'll do is we'll change our scaling from 150 to 250 newton meters. |
25:20 | That should give us a fairly good spread so we can see what's going on. |
25:23 | And what I'm going to do is in our cam timing table, just gonna start by setting our cam timing to minus 10 degrees. |
25:34 | Now, straight away what we could see on the M150 ECU, if you had noticed, down in the bottom of this we've got our closed loop fuel control. |
25:45 | So this engine, the ECU is currently running fully in closed loop and as soon as I removed the cam timing and set it to minus 10, straight away the ECU had to remove a lot of fuel in order to maintain our lambda target. |
26:03 | So this is also a really good sign that minus 10 degrees of intake cam timing is not the optimal value for this particular site, however, let's go through the process and see what we want to be. |
26:15 | Alright, so what we're going to do is click Stop, we'll clear our test and we'll click on Begin. |
26:23 | And what I'm going to do again is just increase the cam timing or advance the cam timing at about a degree a second and you can see that as I'm doing this the Dyno is producing a plot, just like we previously saw, down to minus four degrees now. |
26:42 | So looks very similar to what we were seeing occur with our ignition timing test, little bit more haphazard there because we're making changes to our cam timing. |
26:52 | Again, this is a bit of an art to reading one of these torque optimization tests. |
26:57 | And what we want to do is really just mentally smooth the values that we are seeing being produced here. |
27:05 | So coming up through four degrees now, five degrees, and actually our closed loop control has just disabled because while I was sitting at minus 10 degrees, I'm actually at that particular point, I've got a limit of plus or minus 10% trim and if the ECU sits at that limit for an extended period of time, what it does is it detects a fault, so it actually shuts down the closed loop control. |
27:33 | So at the moment we actually don't have closed loop operating, and what that's going to end up with inevitably, is my lambda or air fuel ratio moving while I'm performing this test as well. |
27:44 | So coming up through 15 degrees now, 16 degrees. |
27:48 | And what I'll try and do is just get to a point where we've just gone past our peak value and hopefully what that's going to end up with is our torque will start to also drop away again. |
28:00 | So really, the graph that we produce is very, very similar to what we saw with our ignition timing. |
28:08 | Okay, so you can see that right now with 25 degrees we're seeing our torque start to drop away. |
28:15 | If we're using this in conjunction with watching our lambda or air fuel ratio, we'd actually start now to also see our air fuel ratio start to move richer, because we've now reduced the volumetric efficiency of the engine, we're getting less air entering the cylinder. |
28:34 | Alright, so I'll just cut that test off there. |
28:37 | That's enough of a demonstration there, and what we'll do is just have a quick look at the results we've got. |
28:43 | So again, what we need to do is mentally smooth the shape of the graph that we've got. |
28:48 | We also want to take note, if we know that at any particular point we weren't quite stable on the throttle, obviously that may require us to either completely disregard that particular test, or we may want to disregard a particular point. |
29:01 | And that'll normally show up. |
29:03 | So what we're expecting to see here is a relatively consistent and smooth shape to the graph. |
29:10 | And for the most part I have got this. |
29:11 | Obviously we're mentally averaging all of these little tiny blips. |
29:16 | What we can see in this particular point where I was around about eight to nine degrees, we see this little dip here, and then a bit of a blip. |
29:24 | And that would probably most likely be a result of me not being 100% stable in that cell. |
29:31 | So obviously if that happens as it has here, well short of where we've reached peak cam timing, we may be able to disregard it. |
29:41 | But if we're starting to get large haphazard or erratic shapes to our torque optimization test in the area where we are actually at peak torque, then that needs to be factored in and we may want to rerun that test. |
29:56 | Now, I'll just mention though, there are a few more considerations when it comes to cam timing. |
30:03 | Beause when we're optimizing the cam timing, there's a few factors going on here. |
30:07 | What we're really doing is moving the cam opening and closing position of the valve opening and closing position to help optimize the volumetric efficiency of the engine. |
30:16 | What we're trying to do is pack as much air inside the engine as we can. |
30:21 | Now, when we change the engine's volumetric efficiency, as you'd know, that affects our fueling requirements and it also can affect the optimal ignition timing. |
30:32 | So we do need to factor that in and particularly if we're doing a sweep test like I've just done, and we're not monitoring or controlling our air fuel ratio with closed loop, then this can affect our torque optimization test and our results. |
30:50 | And I'll just explain that a little bit so you understand. |
30:52 | Let's say for example, we'd started that test at negative 10 degrees cam timing, and we see from our graph on the Dyno that negative 10 degrees gave us something like about 178 or 180 newton meters of torque. |
31:07 | The cam timing there is well away from where we optimally want to be, and this has resulted in a reduction in our volumetric efficiency. |
31:15 | We've got less oxygen, less air entering the cylinder, hence we need less fuel. |
31:20 | Now what I'm getting at there is if we'd optimized our efficiency table, our volumetric efficiency table for a cam timing of minus 10 degrees, and we were bang on our lambda target, let's say, I think for that particular zone we were around about 0.96 or 0.97 lambda, what we're going to find is then as we begin our test, and we swing the cam timing, and we get up to 21 degrees, which is where we made peak torque, what we're going to find is at 21 degrees, we've now got a large increase in volumetric efficiency, but if we're not using closed loop fuel control or making changes to our VE table to account for this, what's likely to happen is that our lambda will end up excessively lean. |
32:05 | And this can influence the actual torque the engine makes. |
32:09 | If we have an excessively lean air fuel ratio so let's say we get to a point where the lambda's perhaps 1.08, maybe 1.12, the engine's going to be making much less torque at that cam timing and 1.12 lambda than it would at that particular cam timing at 1.0 or 0.97 lambda. |
32:31 | So we need to take this into account and understand this. |
32:34 | So if we are not watching our lambda or controlling it, then we can actually end up influencing and affecting the results that we see. |
32:45 | Likewise, we may find that once we've optimized our cam timing, the optimal ignition angle will be different as well and again, the ignition timing is affected by the cylinder fill, the amount of load on the engine, and we do need to be careful of that. |
33:01 | Generally when I'm optimizing cam timing though, we find that if we start with a relatively conservative ignition timing, optimize the cam timing, the fueling and then go back and optimize the ignition timing, this is sufficient. |
33:15 | And one last thing I want to mention here is that obviously with the Toyota 86 engine, the FA20, we have continuously variable cam timing on both the intake and the exhaust cams, so there's an interaction there. |
33:29 | The optimal cam timing for the intake cam will to a degree, depend on where the exhaust cam is, so it becomes an iterative process. |
33:37 | However, this webinar isn't about optimizing your cam timing, it's about how to use that torque optimization test. |
33:44 | I just wanted to go into a little bit of detail there because I feel that that is important to understand. |
33:51 | Otherwise you can end up getting yourself into trouble with the torque optimization test and end up with results that are potentially subpar. |
34:03 | Okay, so we've got one more test that I want to perform here. |
34:07 | And we want to look at the effect of injection timing. |
34:13 | Now we have run webinars in the past on injection timing, and generally if we're doing this with a port injected engine, it's quite difficult. |
34:23 | We won't typically see a massive change in the engine torque as we adjust our injection timing. |
34:32 | So I'm hoping that this test will give you a better idea. |
34:36 | So what we're going to do here is adjust the direct injection timing on our 86. |
34:43 | So what we'll do here is we'll go back to our Dyno and we're going to just clear that test and we'll stop it. |
34:49 | We're going to click on Setup, and we're going to go through and choose Fuel Timing ECU. |
34:58 | And in this case, you need to understand the way the ECU sends this data. |
35:03 | So the way the 86 package is set up, the primary injectors are considered to be the direct injectors and the secondary injectors are our port injectors. |
35:14 | So what I'll do is we'll just set this out to 400 degrees just so we've got a little bit of variation there. |
35:23 | And what we're going to do now is go into our fuel timing screen, and actually what we're going to do for a start is I'll just make sure that we are running on our primary injectors only at the point that the test is going to be completed. |
35:45 | So what we're looking for here is our injector secondary contribution. |
35:48 | This is basically our primary and secondary injection split table, so it defines what percentage of the required fuel volume is going to be contributed by the primary injectors and what's going to be contributed by the secondary port injectors. |
36:03 | So again, we're going to be performing this test around about 2,000 RPM, and what I'll do for the sake of this test, is we'll just set all of those values around that area to zero. |
36:14 | So in this case, a value of zero means that all of the fuel is going to be contributed by our primary direct injectors. |
36:22 | Let's get our engine up and running again, and what we're going to do is go back to fourth gear and we'll get up to 2,000 RPM, and I'll just get everything stable. |
36:36 | What I'm actually just going to do here as well is we will just get our closed loop fuel control running again, and that'll just reset our little error that we had there. |
36:51 | Okay, and we can go back to our tuning workbook and fuel timing. |
36:56 | So we can see now that our closed loop fuel control is just adding 2.5% fuel there. |
37:02 | So just so that our results aren't going to be affected by our varying lambda, we'll just make sure that that's nice and stable. |
37:11 | Alright, so what I'm going to do, I'll just bring our throttle position up to 24, 25% and we'll just get our setup configured again. |
37:21 | So what we want to do here is have our minimum value for our torque set to 100 newton meters and a maximum of 200 newton meters. |
37:34 | And we're currently sitting at 320 degrees. |
37:40 | So what I'm going to do is we'll start by taking that up to 360 degrees, and we can go either way with one of these tests. |
37:50 | We can either start at zero and advance it, or we can start with a larger value and reduce it. |
38:00 | So in this case, that's what I'm going to do here. |
38:03 | We're gonna start at 360 degrees, I'll just clear our test and we'll click on Begin. |
38:09 | And actually before I do that, I do want to also mention that we do need to be a little bit careful with some direct injected engines as to the point that we are injecting. |
38:20 | So right now, 360 degrees is 360 degrees before top dead center on the compression stroke, and this means that we're injecting when the piston is right near the top of the stroke. |
38:31 | Now that's okay for the FA20 engine, because, particularly at high RPM, that's actually the factory injection angle. |
38:39 | But in some engines, if we're injecting at that point where the piston is at TDC, this can actually damage the piston, so we do need to be very careful of that. |
38:49 | Right, we'll clear this, we'll get our throttle position set. |
38:53 | And right now, what I'm going to do is just reduce our injection timing. |
39:00 | We're going to do this reasonably quickly because we do have quite a large range that we're going to want to span here. |
39:09 | And hopefully what we're going to see, hopefully this test doesn't end up making me look silly. |
39:15 | Hopefully what we're going to end up seeing is the effect of having our injection timing optimized. |
39:22 | Now again, here what I've gotta make sure I do, is make sure my throttle position stays very stable around about that 24% 'cause otherwise that's going to have quite a large influence on our torque reading. |
39:36 | So we can see straight away, we've actually seen our torque jump up. |
39:40 | So we've gone up to a peak of about 150, 153 newton meters. |
39:46 | We started at 360 degrees and we're down to 280 now. |
39:51 | The other thing we want to watch when we are doing this as well, this is probably more relevant for port injected engines, is we also want to watch what our lambda is doing, whether our air fuel ratio is being influenced by the injection timing. |
40:09 | Now, we see we've got a jump there in our torque, but that's also been influenced 'cause my throttle position has just jumped up to 25%. |
40:19 | So we do, again, need to be very careful with what we're doing on our throttle. |
40:26 | Alright, so we're coming down through 250 degrees. |
40:28 | Now when I'm seeing a trend like this, where we're constantly reducing our injection timing, so we're going down through 240 degrees and I'm seeing the torque continue to drop. |
40:43 | Well in that case, that's a good indication to me there's not really much point continuing with our test because we're going the wrong way, so our torque is reducing. |
40:54 | What we have seen though is just through that little test if we ignore this little jump here, where I slipped up to 25, 26% briefly on the throttle, what we can see, again we need to sort of do a little bit of mental averaging here of the shape of this, what we can see is that we were probably, disregarding again this little blip here, we'll probably actually find that our optimal injection timing at that point was somewhere around about 300, maybe 290 degrees versus the 360 that we started with. |
41:29 | Now of course if you have got a blip like we've got there, right around that area that we think we're at the optimal injection timing, in that case we can simply rerun the torque optimization test and that's going to really clear that out, make it very, very obvious. |
41:48 | Okay, so we're going to move onto some questions and answers very shortly, so if you do have anything that you would like me to cover off here, please ask that now in the chat and Colin will transfer that through to me. |
42:03 | Now I was initially going to perform another test using air fuel ratio or lambda as an input for our x axis, but essentially I think by now you've seen the process being applied and how the torque optimization test can be used, so I don't see there's too much useful to be had by simply going through that process for another time. |
42:26 | But what I do want to now sort of give you is a little bit of a run down on how we can actually use the torque optimization test, because as I've said, we're not going to necessarily go through and use the torque optimization test to tune every single cell in our ignition table and our cam timing table, et cetera. |
42:50 | And otherwise, we're going to simply be there forever. |
42:52 | So what is the power of this? What is the usefulness of this? So in typical terms, what I would be doing when I'm tuning cam timing, where I'm tuning injection timing, or ignition timing, is I'll be using the normal torque graph on the Mainline Dyno. |
43:11 | But that, as I've said, can be quite tricky to really see exactly what's happening, particularly you don't get to see the full extent of what's happening with that torque graph as you sweep across the ignition timing values, for example. |
43:26 | And that's where the beauty of that torque optimization test comes in. |
43:31 | So what I might do is pick out some key cells in my ignition table and use the torque optimization test to really make sure that those particular cells are optimized, they're absolutely perfect. |
43:45 | And then I can continue my usual technique just using the real-time torque graph on the Dyno to fill in the remaining cells. |
43:54 | And what this does is, particularly when we're talking about a graph, sorry a table such as ignition timing, well for that matter, all of them, ignition timing, cam timing, injection timing, we don't as a rule, typically see completely random, erratic numbers through these tables. |
44:12 | We see smooth and consistent trends. |
44:15 | So what we're going to be able to do is straight away see if the trends that we've got already, using the real-time torque graph on the Dyno line up with what we've seen by perhaps choosing two or maybe four cells in the table and going through the torque optimization test and making sure that those are absolutely optimal. |
44:35 | Now if we're seeing everything line up, then we can obviously carry on as business as usual. |
44:40 | If we do see any really large discrepancies, this may be indicative that we need to go back and spend a little bit more time on the other cells around or outside of those areas that we've used the torque optimization test. |
44:53 | So I certainly wouldn't be advocating that you do every single cell, or even a huge range of cells. |
45:00 | Really, it's not necessary, and perhaps picking four or six cells in an ignition table and going about those and tuning them is sufficient to ensure that you're on the right track. |
45:13 | And also, I'm going to use this to give myself a bit of a sanity check if I've got one particular cell or an area of the table where I'm really struggling to make out or get enough clarity with what's happening with the torque being measured by the Dyno to really give me a good clue as to whether I'm going the right direction. |
45:31 | You also need to temper this with if we are starting to get fussy about perhaps one or two newton meters of torque, then the chances are that no one's going to be able to notice that. |
45:44 | We may be talking of differences of less than 1% and the driver's not going to be able to feel that so there's no point beating yourself up trying to get infinitesimally small gains that just aren't going to be felt, or realistic. |
45:58 | You're much better to just move on and continue with your tuning. |
46:03 | Likewise when it comes to our ignition timing table, sorry our injection timing table, again, we're going to see relatively consistent trends across that table. |
46:15 | So we can just jump back to the laptop screen for a brief moment here, and I'm still on that fuel timing table. |
46:22 | You can see at the moment, this particular timing table setup is a very basic two-dimensional table just to demonstrate this. |
46:29 | But if we look at the graph on the right hand side, I'll just get rid of this. |
46:34 | We look at the graph on the right hand side, other than this one particular cell that we went through and performed the torque optimization test, we can see that there is a relatively smooth and consistent trend and we see that our timing wants to advance as we get up to higher RPM. |
46:50 | So we don't necessarily need to perform that test at every single cell. |
46:55 | Perhaps we could choose 2,000, 4,000 and maybe 6,000 RPM, tune those cells and then extrapolate those trends out. |
47:03 | It's a little bit about understanding the implications of that particular test and how we can utilize them to our best advantage. |
47:13 | But particularly when we're dealing with a parameter that gives relatively small changes to torque, it is a very powerful way of seeing exactly what is going on. |
47:25 | Alright, I'll go back and have a look and see if we've got any questions. |
47:29 | And it looks like at this point we haven't, no, we do. |
47:34 | We've got one here, when tuning something with both intake and exhaust timing, in what order should you adjust the tables? Intake, exhaust, ignition, fuel, et cetera, et cetera. |
47:43 | Yeah, great question, and what I would suggest is that you have a look in the archive because there's now a couple of webinars that we've done on tuning dual variable valve timing engines. |
47:56 | But I'll just give you a brief synopsis of that. |
48:01 | This obviously isn't a webinar about cam timing so I don't want to get too detailed. |
48:04 | What we find is that the intake cam will almost always give us a larger gain or effect on our engine torque, so this is the one we're going to focus on. |
48:14 | A general technique is to start with conservative or safe ignition timing, optimize the intake cam timing. |
48:21 | We need to, as I've kind of mentioned in this webinar, we need to watch our air fuel ratio while we're doing this and make sure that we're not moving lean and that's affecting our torque. |
48:31 | Once we've optimized the cam timing, we can then go through and adjust the fueling and ignition. |
48:36 | Then I will finally follow that up with exhaust cam timing. |
48:40 | But when we move the exhaust cam timing that can then impact on where the optimal fuel, ignition and intake cam timing can be, so it does become an iterative process of going backwards and forwards. |
48:52 | As I've said, check out the archive, there's some really good data in there, some really good information, and whole webinars solely based on that. |
48:59 | Alright, looks like we don't have any more questions, so hopefully that's been a bit of an insight into the torque optimization test on the Mainline Dyno. |
49:09 | And if you do have any questions that crop up after this webinar, please feel free to ask those in the forum and I'll be happy to answer them there. |
49:16 | And for those of you who haven't already left us a glowing review on our Facebook page, we'd all love it if you could jump in and do so. |
49:25 | Just head to the review section on our Facebook page. |
49:30 | Hopefully we can get Ben to put a link there in the chat box about that. |
49:34 | And that's really useful resource for anyone who's considering getting involved in High Performance Academy. |
49:40 | It's always great to see what other members are finding great about High Performance Academy. |
49:45 | So this is just something that's going to help them to have the confidence to get involved with High Performance Academy. |
49:52 | More members we have, the better it is for everyone and the more content we can bring you. |
49:56 | Alright guys, thanks for joining us and we'll see you all next week. |
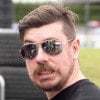