141 | How to Choose Rods
Summary
Connecting rods are one of the most stressed components inside a performance engine and a failure here can quickly destroy an entire engine block. In this webinar we’ll discuss the various options for aftermarket conrods and fasteners. In particular we’ll compare I beam to H beam conrod designs as well as steel vs alloy material considerations.
00:00 | - It's Andre from the High Performance Academy. |
00:01 | Welcome along to today's webinar where we're going to be discussing some of the aspects that you need to keep in mind when it comes to choosing the correct connecting rod for your next engine build. |
00:13 | Now there's a lot of confusion out there in the industry in general when it comes to connecting rod design. |
00:20 | You only need to google which is stronger between an H-Beam and an I-Beam conrod and you're going to straight away see, there's a huge amount of confusion out there. |
00:30 | And particularly when you don't really know what these differences are, what these are going to mean to your engine operation, it can be really difficult to make up your mind as to what parts are going to be correct for your application. |
00:44 | Now when you get it wrong you're going to end up with a situation like we've got here. |
00:49 | Which is where we've got a Tomei H-Beam connecting rod that has been fitted to a 4G63 drag engine and it snapped in half. |
00:58 | Now obviously this gets to be pretty expensive because when we have a connecting rod break in half like this, generally there's not a lot salvageable out of that engine. |
01:08 | It's almost always going to result in a hole punched through the side of the engine block. |
01:12 | Usually that means that the engine block is going to be rendered completely useless. |
01:17 | So we wanna make sure that we avoid that situation at all costs if we can. |
01:23 | But of course in order to avoid that we need to understand a little bit more about what exactly it is that a conrod does. |
01:31 | Obviously it's pretty self explanatory, it's going to connect the piston through to the crankshaft journal. |
01:38 | But what I'm really getting at here is what the connecting rod has to put up with. |
01:44 | And in its operation essentially there's two aspects that it needs to deal with. |
01:49 | First of all it needs to deal with tension forces which is what we're going to find when the piston comes up towards top dead centre on the exhaust stroke. |
01:58 | And essentially in this situation, the connecting rod via the crankshaft is trying to reverse the motion of the piston and convert its energy from moving up the bore to pulling it back down the bore. |
02:09 | Of course due to the inertia in the piston due to its mass and its velocity, that piston would quite happily continue moving up through the cylinder head and out into space. |
02:19 | So its the connecting rod's job to halt that progress and reverse it around. |
02:23 | So that's one aspect, the other aspect of course is it has to put up with an immense amount of compressive load during the power stroke where we've got our fuel air charge burning. |
02:35 | It's creating a huge amount of pressure inside the combustion chamber, forcing down on the top of the piston. |
02:40 | And this puts a huge amount of force down through the beam of the connecting rod, that the connecting rod needs to be able to deal with and hopefully that's going to prevent it from bending and buckling and breaking. |
02:53 | Now in order to deal with these two separate forces there's really two aspects of the design of the connecting rod. |
03:01 | In order to handle the compressive force, in other words to provide good compressive strength, this really comes down more to the design element of the connecting rod, the design of the beam, as well of course here in both aspects we're talking about the strength of the material used in the connecting rod design as well. |
03:24 | Now strength in compression on the other hand, this comes more to do with the cross sectional area of the connecting rod beam as well as again the material. |
03:37 | So the compressive strength we find is going to be more important with high cylinder loads so this really comes from engines that are running high boost pressures at low RPM. |
03:49 | Also nitrous oxide is another situation where we're adding a lot of pressure into the combustion chamber that's going to cause a large combustion event with all of that pressure being passed down through the connecting rod. |
04:03 | So this is where a conrod that offers high compressive strength becomes critical. |
04:08 | On the other hand with these engines, we generally see that they'll be relatively low revving engines. |
04:16 | So on the other hand if we've got an engine that is revving very high, in this situation the conrod's ability to, or strength in tension is much more important. |
04:30 | So that's a situation which we're going to be more interested in, in engines that rev to very high RPM. |
04:38 | OK so we need in a conrod design, enough stiffness to withstand compressive forces during the power stroke, and obviously we also need enough strength so that the connecting rod isn't going to be torn apart due to those tension forces when the piston is going past top dead centre on the exhaust stroke. |
05:01 | Now during the compression event, sorry during the power stroke I should say what we often will find is that if the strength of the connecting rod, the stiffness of the connecting rod is a little bit marginal, what we're going to end up with is some amount of flex in the beam of the connecting rod. |
05:23 | And what this does is ultimately causes a fatigue failure. |
05:27 | So this is a situation where the conrod won't necessarily fail immediately, but over time and over a series of cycles the fatigue failure can occur so this is a situation we can come into, where we've got an engine that's been together, it's been operating perfectly well, producing x amount of power for perhaps a number of races or even a number of seasons of racing. |
05:55 | And then for no apparent reason that connecting rod fails even though the power level has remained the same. |
06:02 | And this is a really important aspect to consider that I think a lot of people don't understand or overlook, is that there is a difference between the maximum strength of a component, in this case we're talking obviously about the connecting rod, and the fatigue life of the component. |
06:20 | So this is what I mean here. |
06:22 | With a component where we are operating below its maximum strength, we're not going to have that component fail straight away. |
06:31 | But over a life period of that product, we may find that it does end up failing from fatigue. |
06:38 | If on the other hand we put our engine together and the first time we hit the dyno and run the engine out to maximum power and the component fails, this is more an indication that we've chosen a component, we've chosen a connecting rod, that simply doesn't have enough strength for the task that we're asking of it. |
06:56 | I'll just point out here as well, as usual with our webinars, we will be having questions and answers at the end so if you do have anything that you would like me to go into more detail on or cover off, please ask those in the chat or the comments, and Ben or Taz will transfer those through to me. |
07:14 | OK so we've got in front of us here, we'll have a look in a little bit more detail, a number of conrods. |
07:19 | We've got some production factory cut conrods as well as a couple of different samples of aftermarket conrods. |
07:26 | And what we want to do is first of all start by talking about production or factory fitted conrods. |
07:33 | Now generally these conrods are going to be produced either through the technique of casting or much more common these days in a performance application, is that they may be forged. |
07:47 | Now this comes down to we need a little bit of an understanding here about these two different processes. |
07:53 | Because they do have quite big impacts on the strength and capability of the connecting rod that we are choosing. |
08:00 | So first of all if we consider the casting process, really what we do here is we take our material or steel that we're going to be making our conrod from, and it is melted down into a liquid component and then it's poured into a mould that's essentially the same shape as the connecting rod, as the finished connecting rod that we want. |
08:21 | Now the problem with this is it does create a conrod that is quite brittle And there's also no grain structure in the conrod itself which doesn't promote a huge amount of strength in the connecting rod. |
08:35 | From the OE manufacturer's sight, standpoint though, it is a very cheap and cost effective way of manufacturing a large number of connecting rods. |
08:45 | So that's probably one of the biggest considerations that they have in mind. |
08:50 | The other technique that as I've said, we see much more prominently in performance orientated engines, and definitely in the aftermarket conrods is where the conrod has been forged. |
09:02 | Now this is a slightly different process. |
09:05 | If we just jump across to my laptop screen for a moment. |
09:08 | We can see sort of an idea of what the forging looks like here. |
09:12 | We've got basically a forging dye, and the base material is heated up and then pressed into the approximate shape of a connecting rod using high amounts of pressure. |
09:27 | Now the advantage with forging a connecting rod in comparison to casting, is that it creates a denser material. |
09:36 | It also promotes a grain structure inside that material which is really important to promoting strength. |
09:43 | So when I'm talking about the grain structure, if we take our connecting rod here, and let's just look at this with our vertical overhead camera. |
09:54 | OK so in a cast application, we've got absolutely no grain structure in this connecting rod at all. |
10:01 | When we forge the conrod on the other hand though, the grain structure tends to follow the shape of the connecting rod, and particularly if the grain structure follows around the big end cap of the connecting rod, this is going to promote a lot more strength than just a random grain structure. |
10:18 | So forging, very very common and popular on performance applications. |
10:24 | When we're talking about production conrods, another technique that is used is a powdered or sintered metal connecting rod. |
10:33 | This again really i believe is more a drive towards reducing the cost of manufacture. |
10:40 | What we've got here is essentailly a powdered metal along with a bonding agent, is packed into a connecting rod shape mould, under quite a lot of pressure, and then it is heated up and basically bonds and melts together under a sintering process. |
10:58 | The key here is that the powdered metal conrod construction results in a connecting rod that requires very little finishing work so again this is really a drive from the manufacturers, to bring down costs. |
11:11 | Nothing particularly wrong with these conrods, any of these conrods obviously fine in a standard production application, but for our interest when we're starting to increase the power that the engine's making, or increase the rev limit that the engine's running to, this is where we need to consider the strength of the connecting rod. |
11:33 | So when we're increasing the power, we're doing this by increasing the air flow into the engine, we're introducing additional fuel to match that air flow, this is creating a bigger combustion event inside the cylinder, inside the combustion chamber, and the result of this is it's producing more pressure inside the cylinder acting down on the top of the piston and then being transferred down through that connecting rod. |
11:57 | So this is where the compressive strength of the connecting rod comes in and this is where we may need to consider improving that. |
12:05 | Now a good indication of this is again, we'll just jump to our overhead camera here. |
12:11 | And we've got a couple of conrods out of our Subaru FA20 engine here. |
12:18 | So these are just a factory conriod. |
12:20 | And when we pulled this engine apart, it had a slight knock although it was still operating fine. |
12:27 | And at the time we couldn't actually find a really good reason for it, and once we got the engine stripped down, what we found though is that one of the conrods had thoroughly bent. |
12:37 | And hopefully if we can see that directly, two conrods directly one above the other, we can actually see that there is quite a sizeable bend in the conrod that I've got on the top. |
12:47 | And in particular we see this through the beam here. |
12:51 | So in this instance we simply exceeded the compressive strength of the connecting rod, and essentially the beam buckled. |
12:59 | So this is where we need to be careful. |
13:02 | For that particular engine, just to put some context around it, it is a factory naturally aspirated engine that produces approximately 200 flywheel horsepower. |
13:12 | And the application we're running it on, we've fitted a turbo charger, we're running it on E85, and we're producing around about double the factory power. |
13:21 | Running around about nine psi of boost pressure, so that creates a lot more pressure inside the cylinder which in turn we're creating a lot more torque at the crankshaft and a lot more power. |
13:32 | So that's what our connecting rod needs to deal with. |
13:37 | Now another thing that I just wanted to mention here is that if we look at the beam of our connecting rod, this is often a good way of telling how the conrod has been manufactured. |
13:50 | And what we want to look at here is the parting line down the beam here. |
13:56 | So if we've got a cast part, and this goes for crankshafts, it goes for pistons and it goes for connecting rods, what we're going to end up with is a very sharp single line down the parting face of our mould. |
14:08 | In this case we've got a wider face, a wider parting line which is more in line with what we see when we're dealing with forged components. |
14:17 | So if you're looking at a factory component, you're trying to decide if it's a forged component or it's a cast component, that's one little tip to have a look at. |
14:26 | With the powdered metal conrods that I've mentioned, because of the way these are manufactured, generally we see almost no marks on the outside surface of the connecting rod, so that's the sign that you're looking at a powdered metal component. |
14:43 | OK so obviously when we move into the aftermarket world we are looking at stronger components in order to, actually sorry before I move on, one other thing I wanted to just mention here, because I can demonstrate this quite nicely on our Subaru FA20 engine. |
15:00 | Again if we look at our overhead camera here, hopefully you'll be able to see the detail of the way this conrod, the big end cap, is parted from the body. |
15:10 | And it actually looks like the surface is broken here and that's because that's exactly what's happened. |
15:16 | This is what's referred to as a cracked cap. |
15:19 | And essentially the conrod is manufactured in one piece and then the cap is actually split or broken off. |
15:26 | So this results in a really rough appearance to the parting line, because the material simply has been cracked or split apart. |
15:36 | Now that gives a couple of upsides and it also gives one downside. |
15:40 | What it does on the positive side is it provides very good location of the connecting rod cap onto the conrod body, so this is very well, very positively located. |
15:52 | There's also no need because of that to provide dowels or any other way of orientating and locating that cap. |
16:00 | So from an OE perspective, just one more aspect that is going to reduce their requirements in terms of manufacturing steps, bringing the cost down and the speed of production up. |
16:11 | One aspect that can be a bit of a pain though for us in the aftermarket is it becomes all but impossible to resize a connecting rod with a cracked cap. |
16:22 | Traditionally if we were to resize the big end journal. |
16:26 | So this would happen perhaps when we're fitting stronger aftermarket rod bolts. |
16:30 | It would happen if perhaps we had a conrod that had seen a little bit of heat and distorted the big end journal so it was no longer completely round. |
16:39 | What the general technique is, is that our machinist will remove a small amount of material from the parting faces, hence reducing the diameter of the journal, and then that journal will be honed to the correct finished size again. |
16:54 | Now of course with our cracked cap that is not possible. |
16:58 | So these can't be resized. |
16:59 | In some instances where we've got very popular engines that run a cracked cap, there may be oversize bearings available so this allows the big end journal of the connecting rod to actually be bored out and honed to a larger finished size and then a oversized bearing shell set is fitted to it. |
17:18 | but generally a bit of a problem, but of course for our purposes, more often than not we are going to be going straight to an aftermarket set of connecting rods. |
17:29 | So first of all I want to cover off the two main techniques or the main design styles that we have with the aftermarket connecting rods. |
17:39 | And these are referred to as H-Beam and I-Beam. |
17:42 | I've already touched on these briefly but now we'll find out what that means. |
17:46 | So first of all if we can jump to my overhead camera again. |
17:50 | We've got here an I-Beam conrod. |
17:53 | This is an Argo connecting rod for a Mitsubishi 4G93 that's produced in Australia. |
18:00 | OK so the term I-Beam or H-Beam refers to the shape of the beam through the main beam of the connecting rod here. |
18:08 | So essentially if we cut through the centre of this beam and then we turned the beam so we could view it end on, an I-Beam as its name would suggest, takes up the shape of an I. |
18:21 | So that's our I-Beam conrod, we'll grab our H-Beam conrod now. |
18:24 | And our H-Beam conrod. |
18:27 | Again if we cut through the centre of the beam and we turn and view the beam side on, this time instead of an I, we're going to end up with an H. |
18:36 | So that's the two terminologies there, that's the two aspects that we refer to, H-Beam and I-Beam. |
18:43 | And as I've said there is a huge amount of confusion between these two. |
18:49 | And I'm not even sure if there is a general consensus opinion on which is superior. |
18:56 | However there is a little bit of information that I can give you. |
19:00 | And that is the I-Beam construction technique generally is going to result in a conrod that has a lighter weight, a lighter mass. |
19:11 | And what that's going to mean is that the I-Beam conrods are generally superior for very high RPM applications. |
19:20 | And actually what i'll do now, I haven't quite got this up on my screen. |
19:27 | If we can just jump across to my laptop screen again for a second. |
19:32 | Just to give a bit of an idea as to where these designs fit into the big scheme of things, these are some conrods from a 2008 Honda F1 engine. |
19:44 | And as you can see here despite the conrods looking slightly different to what I've got here in front of me, these are in fact an I-Beam design. |
19:54 | So remembering with a high RPM ceiling, like we're seeing in F1 I think at 2008, I think from memory these engines were limited to 19000 RPM. |
20:06 | The outright cylinder pressure compared to what we may be seeing with some very very high boost turbo applications is actually a little bit lower. |
20:15 | But of course the tension aspect, the tensive strength aspect of the connecting rod is much more important under these sort of applications. |
20:24 | And I think this is really where it comes down to there is no superior conrod between the I-Beam and the H-Beam. |
20:32 | There isn't one conrod that should rule them all. |
20:37 | The important aspect is to understand that the correct application, the correct conrod for you is going to depend on your application. |
20:46 | The other aspect that's easy to get lost here is that the design of the connecting rod beam is simply one aspect of the conrod's design in its entirety. |
20:58 | And the beam design for example is much less important than the material being used for the connecting rods. |
21:07 | So if you're got an H-Beam conrod that's got a poor quality material that's been used for its manufacture, and then we compare this to an I-Beam conrod that's using a superior material, then the I-Beam conrod's going to win every time. |
21:24 | However if we do compare two conrods that are made using the same material, same material strength, what we're going to find is, all things being equal, the H-Beam design generally results in a slightly stiffer conrod beam. |
21:41 | They do however require a little bit more material and hence an H-Beam conrod is generally going to end up being slightly heavier than a comparable I-Beam conrod. |
21:53 | So this does make them somewhat better suited to very high cylinder pressure applications as I was saying earlier, situations where we are running high boost pressure, situations where we may be running high levels of nitrous, the H-Beam design can be a little bit stronger. |
22:11 | Now I want to just add a caveat here because as I've said you can't take this as gospel and apply it across all conrod designs. |
22:20 | There are many other aspects that need to be considered here. |
22:24 | For example the material that's being used. |
22:28 | For example also the actual thickness of the beam of the connecting rod. |
22:34 | So for example again if we can just jump to my overhead camera here. |
22:38 | We've got our H-Beam conrod. |
22:40 | This is for a Subaru FA20 engine. |
22:43 | And what we can see here is the width of the beam, all things being equal if that beam width was increased, we're going to end up with an increase in the stiffness and strength of the connecting rod. |
22:56 | Obviously that's also going to come at the expense of additional mass to the connecting rod. |
23:01 | So all of these components, all of these aspects of the design, are as always a bit of a balancing act that need to be considered. |
23:09 | So the important point here is if you are in the market for some connecting rods for your engine, what you need to do is have very clear, very clear outline of exactly what you're trying to achieve. |
23:24 | What I mean by this is what your power levels are. |
23:27 | Also what you engine rev limit is. |
23:30 | I think this is an area that a lot of people overlook. |
23:32 | They focus more on the power levels that they're shooting for as opposed to actually considering the additional load that's applied to the connecting rod in terms of the tension during, in a situation where the engine rev limit is significantly increased. |
23:52 | Now the other thing I wanted to just talk about here is another material choice that can be reasonably popular which is aluminium for the connecting rod. |
24:04 | I've got a aluminium drag racing connecting rod here from a Mitsubishi 4G63 let's just have a look at that in our overhead camera. |
24:14 | And you can see straight away that the aluminium conrod is physically a very very bulky conrod. |
24:20 | It's a lot bigger and it's because the actual outright strength of the aluminium material is much lower than the typical 4340 steel alloy that is used in steel conrod construction. |
24:34 | All things being equal though, even given the larger amount of material that is used in the aluminium conrod, we find that they do end up significantly lighter than a comparable steel conrod. |
24:48 | So obviously this would be an appealing aspect if we are considering anything we can do to reduce the rotating and reciprocating mass inside the engine, it's got to be a good thing. |
24:59 | Aluminium seems like a really obvious choice. |
25:03 | There are some considerations here with aluminium though that we need to keep in mind that make it not particularly suitable for most applications. |
25:12 | First of all while it does have a lighter weight, aluminium does fatigue. |
25:17 | So it has a fatigue life. |
25:19 | And this is really, comes back to what I was talking about earlier with the steel rods, we do still have a fatigue life with our steel connecting rods, but it's generally very very long and depending how far below the ultimate strength of the component we're operating we can get essentially an infinity fatigue life out of those components. |
25:41 | Aluminium on the other hand does fatigue, it's known to fatigue and what this means is that we will need to replace aluminium conrods after a period of time in the engine otherwise we risk having them fail. |
25:54 | So this doesn't make them particularly useful for anything other than drag racing applications really, where the engines are known to run for short periods of time. |
26:04 | And depending on the specific power levels we may see these conrods being replaced after somewhere in the region of maybe 50 to 100 passes down the drag strip, and at that point they're basically just garbage and they're thrown away. |
26:21 | The other aspect with aluminium conrods that needs to be understood is that first of all they will expand with heat so they have a higher level of thermal expansion, higher coefficient of thermal expansion, than a 4340 steel connecting rod. |
26:39 | The other aspect as well is that they do tend to stretch in operation at high RPM. |
26:44 | So all of this affects the static clearances that we need to provide for in the engine. |
26:51 | In particular we do need with an aluminium conrod, to provide more piston to cylinder head, and piston to valve clearance. |
27:01 | It's not uncommon to take the clearances that we'd use with a stiff steel connecting rod, and add perhaps 60000ths of an inch to that measurement or 1.5 millimetres. |
27:11 | So it's quite a large aspect that we need to consider there and if we use the sort of clearances that work for a steel rod, we're going to end up with a whole lot of problems once the engine's actually operating. |
27:23 | One of the key advantages beyond the weight of the aluminium connecting rod though, is that they actually are a lot more friendly on the engine when we're operating on the absolute edge. |
27:34 | So what I mean here is that if we are operating the engine and it perhaps runs into detonation, obviously not a situation we want happening in our engine but if it does happen with a steel rod, there's no ability for that steel rod to absorb the shock loading of detonation so detonation results in very very large pressure spikes occurring inside the combustion chamber. |
27:58 | These are essentially a little bit like someone slamming down into the crown of the piston with a sledgehammer and that shock loading force is then transferred down through the connecting rod and into the crankshaft. |
28:10 | Now it can damage the connecting rod anyway, it can bend the beam of the connecting rod by exceeding its strength. |
28:18 | But the other aspect we quite often see is due to that shock loading being transferred through the connecting rod, we also see this result in damage to the big end bearings. |
28:29 | So with the aluminium rod it can absorb some of that shock loading. |
28:32 | And it gives us a little bit of a buffer, a little bit of a safety margin, for us to operate the engine in a slightly more extreme level of tune than what we could get away with potentially with a steel rod Of course if we run the engine into detonation for any extended periods of time we're also going to end up damaging the piston. |
28:53 | So whether or not this is really a long term benefit is arguable. |
28:58 | I'd like to make sure that my engine isn't suffering from detonation, but this is one of the aspects that high powered drag engines do get a little bit more head room, I guess in the tune through virtue of using aluminium connecting rods. |
29:14 | OK so when it comes to the connecting rod that we are using regardless whether it's steel or aluminium what we do need to do is first of all make sure that it is going to actually fit inside our engine. |
29:27 | Now in most off the shelf instances where we've perhaps got a GM LS2 six litre V8 and we're staying at the stock capacity, this is probably unlikely to be an issue. |
29:40 | There's going to be a number of conrod options from a huge range of manufacturers that are simply going to drop into that engine, and we can be confident that they're not going to give us any issues. |
29:52 | Likewise this goes for all of the Japanese domestic market engines as well. |
29:58 | What does get to be a little bit more complex though is when we're making large changes to the engine's basic design aspects. |
30:06 | So in other words one of the key ones here would be if we're fitting a stroke crankshaft then this can cause problems with clearance between the connecting rod and the underside of the block perhaps also the connecting rod and the camshaft and wheel. |
30:22 | So we need to be very careful when we're dummy assembling the engine that that isn't an issue. |
30:28 | In particular what we're going to be running into problems with potentially is clearance between this area of the connecting rod and the underside of the block. |
30:36 | This is a big problem particularly when we look at the size difference between the beam on the aluminium connecting rod and the steel rod we can see that aluminium connecting rods are a lot bulkier through there so much more likely to present us with an issue. |
30:53 | Now this is an area that of course if we've got a major clearance issue, we're going to find out about this very quickly because when we assemble the engine we're simply not going to be able to turn it over. |
31:04 | The more concerning issue though is where we have marginal clearance when we've dummy assembled the engine so it doesn't necessarily present itself as an issue when we're assembling the engine in the shop. |
31:17 | However when everything moves around slightly at high RPM, this is where we can end up with those components clashing. |
31:23 | So if you are varying your engine design away from stock, it is always a good idea to physically check and make sure that you do have clearance between the connecting rod and other components inside the engine. |
31:38 | This can in itself get a little bit tricky. |
31:40 | There's a couple of ways I go about this. |
31:43 | One if we can get reasonably good vision in there, a bore scope which allows us to sort of get a bore scope inside the engine block and look at the area where we're likely to get a clearance problem, and then view what that bore scope's showing us on a screen that's a really great way to see what's going on. |
32:04 | Another good way of doing this as well is to apply some plasticine or some Play-Doh to the underside of the block and when I do this I also apply a light coat of engine oil to the outside of that Play-Doh or plasticine, and we can dummy assemble the engine, turn it through one full revolution and then disassemble it again, and we're going to get witness marks in that Play-Doh if we've got clearance issues. |
32:29 | Likewise you can also apply that Play-Doh or plasticine to the connecting rod itself. |
32:36 | And that's going to give us a pretty good indication of what's going on there if we've got clearance issues. |
32:44 | OK so once we know that the connecting rod fits, we've got the option of what's going to suit our application here. |
32:53 | Now we've talked about the H-Beam versus the I-Beam, and really in the aftermarket right now, unless we're shooting for either very very high RPM levels, or very very high specific power levels, the reality of the situation in my opinion, is it probably doesn't matter. |
33:12 | Now that might be a little bit controversial. |
33:14 | The reason I say this is because we've now got so many aftermarket connecting rod manufacturers out there vying for our dollar and we've got simply as many H-Beam as we've got I-Beam connecting rod designs. |
33:26 | And provided that you are not trying to reinvent the wheel with the sort of power levels you're expecting out of your engine or the RPM range that you're expecting to run it to. |
33:37 | Provided you are dealing with a quality conrod supplier out there in the aftermarket, you're probably going to find that both H-Beam and I-Beam are going to be totally suitable for your application. |
33:49 | Now a good example of this is our Brian Crower connecting rods for our Subaru FA20. |
33:55 | These are their 600 horsepower rated H-Beam connecting rods. |
34:01 | They also produce an I-Beam version of this exact connecting rod. |
34:06 | And we quizzed the guys at Brian Crower about the differences between those connecting rods and they're both rated at exactly the same power level. |
34:15 | And their answer was that they felt driven to produce both an H-Beam and an I-Beam variant because there's so much confusion in the industry that if they only produced one, they'd be losing out on a segment of the market that was determined to have whatever it was that they weren't producing. |
34:32 | So in their opinion for that particular application, the power rating, the RPM rating of the connecting rod is identical, regardless whether you are dealing with H-Beam or I-Beam. |
34:43 | So interesting aspect there. |
34:45 | It's always a good idea to discuss your requirements with the conrod manufacturer, and get their feedback on what particular components they supply are going to be best rated or best for your particular application. |
35:02 | OK so we've talked about the conrods, another aspect though that is really important to understand when it comes to the connecting rod is the fastener that holds the cap onto the body of the connecting rod. |
35:15 | Now this is one area where we can influence the strength or the capability of that connecting rod. |
35:22 | So this really comes down to the tension strength of the connecting rod, when it's trying to be pulled apart as that piston goes through top dead centre on the exhaust stroke. |
35:36 | Now at that point we've got the connecting rod attached to the crankshaft journal. |
35:41 | and we've got, at the top of the connecting rod, we've got the mass of the connecting rod as well as the piston trying to pull that connecting rod off the crankshaft journal. |
35:50 | So it's under these conditions that the strength of the rod bolts becomes very very important. |
35:57 | And what we find is that the, most conrods, most performance conrods are available with a variety of different rod bolt materials depending on our particular application. |
36:09 | What we'll find is one of the most common bolt materials that is used in aftermarket connecting rods is made by ARP and is given the relatively uninspiring name of ARP 2000. |
36:21 | So it's essentially one of their base materials. |
36:24 | Still a very good material, much stronger than the likes of a factory rod bolt. |
36:29 | So we also see that these are available as rod bolt upgrades for stock connecting rods where they are known to have a strength issue just with the connecting rod bolts as opposed to the actual beam design of the conrod. |
36:43 | However if we're, I'll come back a little bit, if we are looking for relatively modest power levels. |
36:51 | So let's say for example we're tuning a, building a four cylinder, two litre engine, and we're maybe shooting for 500 to 600 horsepower, these days that's a relatively modest power aim for that sort of engine. |
37:05 | Perhaps we're hoping to extend the rev limit out to about 8000 RPM. |
37:09 | Under those conditions I'd be more than happy to use an ARP 2000 rod bolt material. |
37:15 | If we're starting to get a little bit more serious with our aims though, maybe we're now trying to produce 800 horsepower, maybe we're now increasing our rev limit out to 9000, 9500 RPM. |
37:26 | In that situation I'm going to be much more inclined to uprate the rod bolt material. |
37:31 | And in the ARP lingo there's a few different options there. |
37:35 | L19 is a good step up from the ARP 2000 base material. |
37:40 | For the most extreme applications they also produce another bolt material called ARP Custom Age 625. |
37:47 | So this is just a much stronger material. |
37:50 | It provides much better clamping and it's going to provide a connecting rod that will be much better suited particularly to high RPM applications. |
38:00 | So again this is something to consider. |
38:02 | Of course uprating those rod bolt, the faster material does of course add to the cost of your connecting rods so that's something that you need to consider there. |
38:14 | If you are going to be uprating the rod bolts in a factory rod you will often find that the additional clamping force from the stronger rod bolt is going to provide some level of distortion to the main bearing, the conrod bearing tunnel. |
38:31 | So essentially it's really important for our big end journal of the connecting rod to be absolutely perfectly round in order to achieve the correct clearances, oil clearances on our bearing shells to the crankshaft. |
38:45 | And if we fit a stronger fastener with better clamping that can distort, and that can affect out oil clearances and hence the long term reliability of the connecting rod. |
38:55 | So a key point when we are upgrading fasteners is that the rod does need to at least be checked for size and it may need to be resized in the big end journal in order to make sure that everything is absolutely perfect and our oil clearances are going to be correct along with the crush on those big end bearing shells. |
39:16 | Now another aspect I'll just talk about here before we move into questions, so if you do have any questions please ask those now, we'll get those transferred through. |
39:24 | Is the way the conrod is supporting the wrist pin. |
39:29 | So in the small end of the connecting rod, let's just go to our overhead shot here. |
39:34 | In the small end of our connecting rod we're generally going to have a bush pressed into the connecting rod body. |
39:41 | So we don't actually have a bearing as such, not like the bearing shells that we have in the big end of the connecting rod. |
39:48 | This is simply a bronze bush that is pressed in there. |
39:52 | In this instance we do have an oil hole in the top of the connecting rod. |
39:57 | So this relies on an oil mist to achieve lubrication of the wrist pin. |
40:02 | There is also a circumferential groove, couldn't get my mouth around that word, through the centre of that bush that distributes the oil flow around. |
40:15 | So these bushes can be pressed out and can be replaced by a machine shop if you've got a connecting rod that needs to be serviced and rebuilt if it's showing wear in those bushes. |
40:27 | So they can actually be serviced. |
40:30 | Alright we'll move into some questions and answers now. |
40:37 | OK our first question comes from Mohammed who's asked when to use conrods with oil squirters drilled on, and will those holes affect the oil pressure? I'm assuming there Mohammed you're talking about the under piston oil squirters that are going to supply a mist of oil to the underside of the connecting rod, sorry the underside of the piston, and that's going to also help lubricate the wrist pin via that oil mist. |
41:08 | There is also some factory connecting rods which do have an oiling hole through the upper body of the connecting rod, where it's going to use a forced oil supply from the big end journal to supply oil to that wrist pin. |
41:26 | So both of these techniques, yes they will have some influence on the oil pressure. |
41:32 | The small oiling hole that we see through some of the connecting rod big end journals, would be relatively minor. |
41:39 | Certainly with the under piston oil squirters that are common in a lot of performance engines, these will have a larger impact on our oil pressure. |
41:47 | I've always been inclined to retain under piston oil squirters in any application where they were factory fitted. |
41:56 | I think they probably make a lot of sense and they're a reasonably good idea. |
42:00 | I do know however a lot of engine builders remove these because they are concerned about oil pressure with these under piston oil squirters removing some of that oil, draining away some of that oil, essentially from our main oil gallery. |
42:16 | When it comes to aftermarket connecting rods, we very seldom see an oiling hole drilled through the side of the connecting rod. |
42:25 | We do see some applications where there is a forced wrist pin oiling hole drilled through the body of the connecting rod. |
42:31 | Really comes down to the specific application. |
42:37 | Doosey has asked Nissan SR20 have 17 mil and 19 millimetre big end bearing size options. |
42:44 | Is the extra two millimetre surface area that worthwhile? It's been a long time to be perfectly honest since I've dealt with SR20s. |
42:52 | I think from memory what you're talking about there is the GTIR engine, had that 19 millimetre big end bearing shell. |
43:02 | So anything you can do to increase the surface area of the bearing is going to improve the reliability of that bearing shell. |
43:12 | It's going to support additional load better than a narrower bearing shell. |
43:17 | So there is some advantages there, and certainly I have used those wider bearing shells in the SR20s that I have built. |
43:27 | One consideration there though is that the wider bearing shell, while I doubt that we're probably in a situation where we'll be able to measure the difference, can result in a slight increase in the frictional loss from the oil shear on the big end journal of the crankshaft. |
43:45 | So there is a potential downside there. |
43:47 | You'd weight that up against reliability and life expectancy. |
43:54 | Pantera Turbos asked with a multitude of rod designs and weights even from the same manufacturer, how do you decide of which to use? Obviously excess weight is a bad thing as well if you're aiming for optimum performance. |
44:06 | Also how would you decide if upgraded rod bolts far exceed the capability of the rod itself. |
44:12 | OK few questions in there and all good questions. |
44:15 | So this really comes down to the situation where often you're going to need to have a discussion with the manufacturer supplier of the connecting rods that you're looking to use. |
44:26 | So a good example of that, exactly what you're talking about here is what I've mentioned with our Brian Crower FA20 conrods. |
44:33 | So as I've already mentioned these are available in both H-Beam and I-Beam rated at exactly the same power and RPM range. |
44:42 | Now these ones here are fitted with the ARP 2000 rod bolts, so these are the base level connecting rod from Brian Crower. |
44:50 | Absolutely fine for our purposes. |
44:52 | We never really expect to take our FA20 beyond about 500 horsepower. |
44:57 | And that builds us in a nice safety margin which is actually something I should've probably talked about earlier. |
45:04 | I'll come back to that in a second. |
45:06 | Now these exact same conrods are also rated, I forget the specifics, I think they might also rate these at about 800 horsepower and something like 9000 RPM, if you replace the ARP 2000 rod bolts with the Custom Age 625 or L19 rod bolts. |
45:24 | Again I can't remember the exact specifics it was around about six or eight months ago that I was researching these rods. |
45:31 | So you've got a little bit of flexibility there. |
45:33 | Obviously if affects the cost of the connecting rods. |
45:36 | So this is where it's really worthwhile to have a discussion with the rod manufacturer, and discuss what your intended purpose is with those rods. |
45:46 | And that way they're going to be able to guide you particularly with regard to the rod bolt material. |
45:53 | Because as you've quite correctly said, there's not really a lot of point going and spending what can be quite a considerable amount of money on a flash set of rod bolts if the base conrod itself is just not up to task and you're going to be operating right at that limit. |
46:08 | OK so now I'll just come back to what I was saying there about a bit of a safety margin. |
46:15 | So this really comes back down to what I was talking about earlier in the webinar where we have both the ultimate strength of the material. |
46:23 | So if we exceed that even one time, the conrod's going to fail. |
46:26 | But of course beyond that we also have the fatigue limit. |
46:29 | So if we're operating below the ultimate strength of the conrod design and conrod material, but we're quite close to it, then it's going to end up fatiguing over time and it can fail. |
46:41 | So essentially the further we can operate below that ceiling, the ultimate strength ceiling of the connecting rod material, the longer our fatigue life's going to be. |
46:52 | And as I've mentioned earlier, if we've got a conrod that's perhaps rated to 800 horsepower and we're operating that at 500 horsepower, all things being equal, assuming we've got all of our clearances correct that conrod is probably going to live just about forever. |
47:09 | If on the other hand we've got an 800 horsepower rated conrod and we're operating it to 750 horsepower, obviously we're getting quite close to the rated limit of that connecting rod, we're getting quite close to that ultimate strength ceiling and hence, while it's not going to fall apart, we are underneath that ultimate strength ceiling, it is going to fatigue and it's going to have a shorter life. |
47:31 | Whether that's going to be a season of racing, maybe three seasons of racing, I can't tell you but if you want to ensure a little bit more reliability long term it's always a good idea to use a component that it rated to a higher level of power and RPM than you're actually wanting to run. |
47:52 | And generally I try and build in around about a 20% buffer there. |
47:57 | Of course these numbers that manufacturers quote are also a little bit difficult to specifically trust and what I mean by this is they're generally quite conservative. |
48:10 | Obviously if the conrod manufacturer is specifying that their conrod is good to 800 horsepower and 9000 RPM, and you're running at 800 horsepower and 9000 RPM they want to be very sure that that connecting rod is going to hold together. |
48:31 | Next question comes from Motor Rave who's asked what's the best lubricant for rod bolts? OK this is really a situation where we need to use the specified lubricant. |
48:43 | Now I know that on the face value might not sound particularly useful but it has a really big bearing on the clamp load that we achieve through the rod bolt. |
48:53 | These are one of the most highly stressed fasteners in our engine so we want to be very sure that when we've done these up that they are at the manufacturer's rated stretch, so that we're going to achieve the manufacturer's rated clamp. |
49:07 | OK so the lubricant that we use affects the friction between the threads on the fastener and the threads inside the connecting rod. |
49:17 | So this in turn affects the amount of torque that we need to use. |
49:21 | So what you'll find is that if we're assembling a factory engine, more often than not the specified lubricant will be something like a 10W-30 motor oil. |
49:31 | That's simply because every mechanic has that easily available. |
49:36 | And there's nothing specifically wrong with that. |
49:38 | When we're dealing with high end connecting rods such as these where we've got aftermarket rod bolts and the likes of ARP we're going to find that the rod bolt manufacturer will have their own specified lubricant. |
49:52 | I think I may have some here. |
49:55 | No I don't so in the case of ARP, they specify their own ARP moly based lubricant. |
50:03 | There is also, we've got a set of Carrillo conrods somewhere, they've got their own moly based lubricant that they specify which is a Loctite product. |
50:12 | The key point here is that all of the information around fastener torque that they supply is based on using their specified lubricant. |
50:22 | And if you swap that out for motor oil, what this is going to mean is you're not going to achieve the correct clamp. |
50:27 | Likewise though if you use a moly based lubricant with an OE fastener, an OE rod bolt, where you've been told to use motor oil, you're actually going to probably end up over tightening that fastener which is just as bad as under tightening it. |
50:41 | Sorry for the long winded answer there, but it wasn't one that's easy to be quick with. |
50:47 | And I will also just mention on that note as well, that if you really want to be particular when it comes to tightening your fasteners for your conrod bolts, again because this is one of the most highly stressed fasteners in our whole engine, and if we don't get this right, we can have catastrophic engine failures. |
51:08 | The correct way of tightening these fasteners, and this really takes the lubricant part out of the equation, is to actually measure the stretch of the fastener. |
51:17 | So you can buy special fixtures, that basically go on each end of the connecting rod and use a dial gauge and this will measure how much the rod bolt has been stretched. |
51:28 | And really this is what we're trying to achieve when we're torquing a fastener down, we're trying to stretch it by the recommended amount from that fastener manufacturer. |
51:38 | If we directly measure the stretch of the fastener, this gives us a much better indication of whether we have the correct rated amount of stretch and rated amount of clamp. |
51:50 | Michael Riggs has asked I'd like to know about the types of steel and how they relate to horsepower ratings so that we won't have to rely on a manufacturer's specification. |
52:00 | OK probably a question that goes a little bit beyond my metallurgical understanding unfortunately but I can give you some insight here. |
52:08 | So what we're going to find is that the majority of the aftermarket connecting rods that we see, likes of Brian Crower, the likes of Carrillo, the likes of Eagle as well, will use a 4340 based steel alloy. |
52:26 | Now the problem with that is not all 4340 steels are created equal. |
52:31 | So just because your connecting rod is manufactured from 4340, doesn't mean that it's as good as the next conrod that you get. |
52:39 | So a good example of this is the difference between let's say Eagle, which is obviously an entry level product. |
52:46 | Still, in my own experience, actually really quite a good value for money product. |
52:51 | I've been quite surprised, given how cheap they are, how well they have worked in some applications that I have used them in. |
52:58 | On the other end of the spectrum we have Carrillo probably in a lot of ways seen as one of the premier conrod manufacturers. |
53:05 | Now the differences here is in the processing of that steel. |
53:10 | Carrillo actually have their own alloy made to their own specifications. |
53:16 | And they're very very rigorous with the testing that that material goes through. |
53:20 | Can't remember the exact steps, number of steps but it is crack tested, it's also x-ray inspected. |
53:27 | So what they're doing is ensuring that the base alloy that the conrods are forged from is 100% perfect and structurally sound. |
53:39 | So on the other hand I believe that Eagle are not quite as strenuous on their testing. |
53:45 | So even though the two conrods may on face value be made out of what appears to be similar material there are still some significant differences there. |
53:55 | Marcos has asked how do you measure the rod and crank clearance and bearings? Probably a little bit beyond the scope of this webinar right now, we've actually run separate webinars on exactly that topic's also covered in detail in our Practical Engine Building course. |
54:14 | Essentially there are two techniques that are used, I'll just go into it briefly. |
54:18 | One is to use a ball gauge and a micrometer. |
54:22 | The other which is probably a much more budget approach and nowhere near as accurate is to use plastigauge during a dummy assembly of the engine. |
54:33 | Ali has asked when using Manley forged rods on a modular Ford engine under boost requirements, what else would you suggest upgrading in the rod assembly? What should you always look to combine in the forge rotating assembly? OK pretty broad questions there. |
54:48 | The modular Ford engine is not one that I am specifically familiar with unfortunately so I can't give you any personal insight there. |
54:57 | I mean Manley is one of the well respected manufacturers of conrods out there in the aftermarket. |
55:04 | So really probably the information I've gone through in today's webinar is still completely relavant there. |
55:11 | If you're not trying to really reset the record books there with that particular engine, Manley's off the shelf conrods are probably going to be more than capable. |
55:21 | So in other words if you're looking at maybe a 20% to 50% increase in power, and maybe a modest increase in rev limit, an off the shelf conrod from the likes of Manley is probably going to be absolutely fine. |
55:35 | It's when you're starting to really stretch the limit in terms of both power and rev limit that you need to be a little bit more on your game and make sure that everything is going to be absolutely perfectly suited to you. |
55:46 | The consideration you may wanna go through there as i've just talked about though is uprating the rod bolts depending on what those particular conrods are supplied with. |
55:57 | And in terms of what else you should be looking to combine in the forged rotating assembly, really in this case the only other aspect that you're most often going to be considering, is the piston that is being supplied there. |
56:12 | So piston and also the wrist pin. |
56:14 | And those are just as important, often more so that the connecting rod. |
56:18 | Can't really go into too much more detail about pistons because that's a complete webinar subject all on its own. |
56:28 | Daniel Davies has asked any views on old school hollow rods for naturally aspirated engines? Sorry not something that I've personally dealt with myself. |
56:40 | I mean again when it comes to something like that I'm assuming there you're talking about really a technique for reducing the mass of the connecting rod. |
56:49 | We've talked about how that is valuable in a high RPM application. |
56:54 | But yeah it's not something I'm specifically familiar with myself. |
57:02 | Shon has asked what about rod stretch at 16000 RPM motors are changing direction of the piston very fast. |
57:08 | Yeah absolutely so rod stretch is something that we need to take into consideration. |
57:15 | Probably not too many of us if you're outside of the motorcycle engine world are going to be dealing with engines that are running to 16000 RPM. |
57:25 | And of course at 16000 RPM the general design of the engine also will generally entail a shorter stroke to make everything liveable and control that piston speed. |
57:37 | But rod stretch is definitely a consideration. |
57:39 | This comes into when we're selecting our clearances between the piston crown and the underside of the cylinder head, that's one of the considerations there. |
57:49 | Obviously as the rod stretches , that RPM, that clearance is going to be reduced, that's why I was also mentioning with our aluminium conrods, these stretch more than a steel rod, we need to account for that, and provide additional clearance there. |
58:02 | Also this comes into the clearance between our piston crown and our valves too. |
58:12 | Anthony has asked do you have to balance a conrod as you would a piston in terms of weight? Actually that's a great question Anthony because that was another topic I was going to touch on there. |
58:22 | So yes you do have to balance a connecting rod. |
58:25 | When we're dealing with aftermarket connecting rods these will generally come balanced from the supplier depending on what supplier you're dealing with will really depend on what level they are balanced to. |
58:40 | When it comes to a connecting rod though, these are a little bit more involved to balance than a piston. |
58:45 | When we're talking about pistons, all we want to do is balance the entire set of pistons so that they're as close to each other's weight as possible, generally I like to be pretty precise here and try and get all of the piston sets down to about a 10th of a gram plus or minus. |
59:02 | With a connecting rod though, it's not just a case of making sure that all the rods weigh the same. |
59:07 | What we've got is a component of the connecting rod is considered of reciprocating weight where it's moving up and down and there is a component of the connecting rod, the big end attached to the crankshaft that is a rotating weight. |
59:20 | So we need to actually split these out into two components and balance them individually. |
59:24 | So the process of balancing a connecting rod relies on us first of all balancing the big end. |
59:30 | And this is done by placing the conrod in a fixture. |
59:34 | I'll just grab that now actually seeing as it's right behind me. |
59:41 | So this is a connecting rod balancing fixture, and what we can do is support the connecting rod, the big end of the connecting rod, on this fixture and this allows us to weigh just one end of the connecting rod independent of the other. |
59:57 | So what we'd do is go through and match all of the big ends weights of the connecting rods. |
01:00:01 | Once they're all the same then we can go through and weigh the entire connecting rods and make sure that they're all the same. |
01:00:07 | If there's a difference there, we've obviously balanced the big ends so we would take the weight off the small ends. |
01:00:12 | So there's a little bit to understand there when it comes to connecting rods. |
01:00:16 | They're not quite as simple to balance. |
01:00:22 | Barry's asked what are your views on running rods that run pinned bearings? This is quite common on aluminium conrods and in fact, I just wonder if I can get this cap off. |
01:00:32 | This aluminium conrod here does run pinned big end bearings. |
01:00:37 | I've never ever run pinned bearings on a steel connecting rod. |
01:00:41 | As long as you're getting sufficient crush on the bearing shells in the big end of the connecting rod then there should be no reason to have that bearing shell move, and hence there's no need to pin it. |
01:00:54 | I'll just see if I can get this out so we can have a quick look at that pinned bearing shell. |
01:01:00 | I'll just rotate that around, and let's just go to our overhead camera. |
01:01:05 | So yeah we should be able to see that. |
01:01:08 | There's a little brass pin here. |
01:01:10 | One of the problems with these rods is they do require a little bit of work in terms of machining the bearing shells. |
01:01:20 | Obviously the bearing shells need a matching hole machined in them for those pins. |
01:01:29 | Last question comes from Daniel who said how long could i expect aluminium rods to last in a race application like rally? Really it's just about impossible to tell which is the frustrating thing. |
01:01:41 | And I've actually had discussions with aluminium conrod manufacturers before and understandably they're not particularly interested in making any real commitment. |
01:01:54 | Generally I would not be inclined to use them in an application outside of drag simply because they do have that known fatigue life problem. |
01:02:04 | And when you consider that a high powered drag engine might be replacing these conrods once every 50 or so passes, that's not a lot of mileage when you consider what a rally car's going to go through. |
01:02:19 | However there are plenty of instances where I have seen particularly in the Mitsubishi tuning world, engine builders using aluminium conrods in street driven Mitsubishi Evo Lancers producing 800 to 900 horsepower, and still leading a pretty long and healthy life. |
01:02:38 | The problem is as we said at the start of this webinar, if you do have a conrod break, generally you're going to lose the entire engine. |
01:02:45 | So it's a pretty big gamble to make. |
01:02:48 | And for a street application of for a rally application, something that's going to see a lot of mileage, in my own personal opinion, the benefits of the lighter weight aluminium material are probably are outweighed by the potential downsides. |
01:03:04 | Alright guys that's brought us to the end of the webinar so hopefully that's given you a little bit more insight into conrod design and aspects that you need to keep in mind. |
01:03:14 | As usual for our HPA members, if you do have any questions after this webinar has aired, please ask those in the forum, and I'll answer them in there. |
01:03:24 | Thanks for joining us guys, look forward to seeing you next week. |
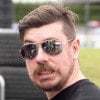