142 | How Big Does a Fuel System Need To Be
Summary
One of the most common and frustrating issues we see on the dyno is a fuel system that isn’t large enough to support the required power level from an engine. In this webinar we’ll discuss sizing both the fuel injectors and the fuel pumps to handle your expectations so that you get it right the first time.
00:00 | - Hi guys it's Andre from High Performance Academy, welcome to today's webinar where we're going to be discussing the fuel system requirements for an electronically fuel injected car. |
00:11 | The reason we're going through this webinar is because this is one of the more common problems that I've struck over my career of 15 odd years now professionally tuning cars. |
00:23 | There's a list of the common problems we actually cover in another webinar so you may want to search that out in the archive. |
00:31 | There's a webinar named five common problems, so you may wanna look at those other problems, but this is one of those problems that we highlighted in that particular webinar and I wanted to dig down a little bit deeper and discuss in particular what we can do to combat that. |
00:48 | So the issue is we get a car on the dyno, we begin our tuning, maybe we've gone a long way through the tuning process and towards the end of the tuning process once we start performing some wide open throttle high power ramp runs, we suddenly find that there's a deficiency in the fuel system, we simply can't get enough fuel into the engine, the engine's starting to run lean, and obviously that's not a situation that we can put up with so generally this is going to waste time, 'cause we're going to have to pull the car off the dyno. |
01:17 | Often we've also wasted a lot of the work that's already gone into the tune up to this point, because it's going to need to be readdressed once we have corrected the fuel system deficiency, whatever that may be. |
01:29 | So of course if we can get around this in the first place, and start with a car that has a fuel system that is correctly designed then we're ahead of the game right from the get go. |
01:39 | We're going to know that that particular aspect of our car design is not going to let us down. |
01:47 | Of course there still may be other problems, we are dealing with cars after all, nothing ever goes smoothly. |
01:52 | But if we can make sure that everything in our fuel system is up to the task then we should have less problems in the long run. |
02:02 | Now we're going to find out during today's webinar that realistically it is actually quite easy to get our fuel system sized correctly. |
02:10 | If we understand what's actually going on, we understand what we need in terms of fuel flow into our engine and how the engine operates. |
02:21 | Just some of the basics there. |
02:23 | So we're going to go through this and at the end, once we've talked about sizing the injectors and we've talked about sizing the fuel pump, we're also going to cover just briefly a little bit about fuel pressure regulators. |
02:36 | These are an aspect obviously of the fuel system that are quite important and there's a few misunderstandings around fuel pressure regulators so we'll cover that off as well. |
02:47 | And lastly we're going to touch on what exactly the signs are when we're on the dyno that you have a problem with the sizing of your fuel system. |
02:58 | So generally when we're going through the fuel system sizing one of the best places to start is by focusing on our injectors so we're going to do exactly that. |
03:08 | And the general way or the conventional way I should probably say of sizing the fuel injectors is to take into account an aspect of the engine operation that's known as the break specific fuel consumption or BSFC for short. |
03:26 | And this essentially tells us how much fuel the engine needs to burn in order to produce a certain amount of power. |
03:35 | And it's, I guess you could really relate this to an aspect of the efficiency of the engine. |
03:41 | Now in particular this actually causes its own set of dramas because measuring the break specific fuel consumption of an engine, for us outside of a laboratory dyno facility, is probably pretty challenging to do it with enough accuracy to actually get worthwhile answers. |
04:00 | And for that reason what we generally have to do is use generic produced break specific fuel consumption numbers for the purposes of our calculation. |
04:12 | Now that's fine to a point but of course if your particular engine varies dramatically from sort of the averages that we may use for this calculation it can really throw off your calculation. |
04:26 | In terms of those numbers it does get a little bit tricky. |
04:28 | For a naturally aspirated engine we may be looking at a BSFC value around about 0.5 For a turbo charged or super charged engine we may be burning a little bit more fuel to make the same amount of power. |
04:42 | Generally we're going to be running a super charged or turbo charged engine a little bit richer, and hence the BSFC typically would jump to a value somewhere around about 0.6 That's a couple of really basic average numbers that I've just pointed out but there are as I've mentioned huge variety in these numbers. |
05:02 | If we look at a really efficient engine, maybe something like a Honda K20, which is a naturally aspirated two litre engine, you could be looking at a brake specific fuel consumption down in the region of around about 0.3 If we look at a really poor example here, something like an air cooled engine that's turbo charged, we're going to be running that particular engine much much richer because we're going to be using a lot of the fuel as a cooling aspect of the engine's operation. |
05:29 | BSFC in that case could be in the region of as high as 0.7 So as you can see there's a huge variety of range in there which makes our task a little bit trickier but if we are going to use the BSFC values then we are going to need to take some value on board and average there for our calculation. |
05:50 | Now if we can just jump across to my laptop screen for a moment we'll just go through a sample of this sort of calculation. |
05:57 | And we've got up here the actual calculation that we're going to go through. |
06:02 | And this will produce an output in terms of injector size in pounds per hour. |
06:08 | I will point out straight away that this is quite broad calculation. |
06:13 | There's a lot more parameters that can go into this if we really wanna fine tune it. |
06:18 | So this is going to give you a very broad ball park value. |
06:21 | So I'll talk more about that shortly. |
06:23 | So for a start on the top line of our calculation we have our desired horsepower. |
06:28 | We are working in imperial units here so we're talking about flywheel horsepower. |
06:33 | So this is our target horsepower value for our engine. |
06:37 | And then multiplied by the brake specific fuel consumption there of our engine. |
06:43 | So again for a naturally aspirated engine we might be in the range of 0.5 to 0.55 For a super charged, turbo charged engine, probably in the range of 0.55 to 0.6 On the bottom line of our calculation here what we're going to do is take into account the number of injectors fitted to the engine. |
07:01 | So we're going to be dividing our fuel flow essentially here by the total number of injectors fitted to the engine. |
07:08 | We're also going to take into account here the maximum injector duty cycle that we're happy running our injectors out to. |
07:16 | Now we're going to talk a little bit more about maximum injector duty cycle further into the webinar. |
07:23 | So for now let's just assume that we want to limit our maximum injector duty cycle to 0.85 or 85% probably a pretty good safe run of the mill number there for our maximum injector duty cycle. |
07:37 | And as I've said this is going to output an injector size, required injector size in pounds per hour. |
07:43 | So I've just put some sample numbers into this equation and here we're looking at a four cylinder engine that's turbo charged and we wanna make 800 horsepower out of that engine. |
07:55 | So first of all on the top line we've got 800, our desired target flywheel power multiplied by a brake specific fuel consumption of 0.6 And then on the bottom line of the equation we've got four injectors multiplied by our 85% injector duty cycle and this shows us that we need an injector size in the region of about 141 pound per hour. |
08:18 | Now for those of you who don't work in pounds per hour, we've got two general ways of rating our injector flow, pounds per hour or cc per minute. |
08:28 | A little bit of a confusion in there because we can't easily directly swap between those two units. |
08:35 | We're talking about a mass in one sense, pounds per hour, mass of fuel per hour, and in the other sense we're talking about a volume. |
08:43 | So we can't actually convert directly from a mass flow into a volume flow without accounting for the density of the fuel, that's how we convert between volume and mass, we have to account for the density of the fuel, or in other words how much a given volume of that fuel weighs. |
09:01 | Now the complexity here is the density of the fuel is going to depend on the fuel we're talking about. |
09:07 | Whether it's gasoline or E85, just the two examples there, and it also just to throw another spanner in the works, the density of the fuel will also vary with its temperature. |
09:18 | Now we don't wanna get too tied up in this, but generally if we use a value of 10.2 as a conversion factor this is going to give us a reasonably close approximation, given those caveats that I've just talked about. |
09:33 | So here on the bottom line of our equation here you can see, just draw a horrible line, we've got our 141 pound per hour injector, multiplied by our conversion factor of 10.2 shows us that we need an injector size around about 1440 cc per minute. |
09:51 | Now with all of that taken into account, what we also want to do, as we already have talked about, our brake specific fuel consumption is unlikely to be absolutely accurate to the number that we've used in our assumptions there. |
10:09 | So generally what we're going to do is take that number and we're going to find an injector that is slightly bigger. |
10:16 | So we're going to use this as our absolute minimum injector size. |
10:20 | And that's generally a pretty good way of getting an idea of what sort of injector flow you want. |
10:28 | However there is one big consideration here that we do need to take into account. |
10:34 | And that is that this calculation on its own completely ignores the engine RPM, or engine speed. |
10:42 | And this is an important consideration in our injector size calculation. |
10:47 | The reason for this is if we are running an engine to let's say 10000 or 12000 RPM, I'll admit probably not that common, but particularly if we're dealing in the motorcycle world, definitely that's not unheard of. |
11:00 | We could even be going to 14000 or 15000 RPM. |
11:03 | What happens in this instance is as the engine speed increases we have less time available to actually inject fuel. |
11:13 | In other words each engine cycle, each individual engine cycle physically happens faster. |
11:18 | So if we need to get a given mass of fuel into the cylinder during the engine cycle we've got less time available for that to occur. |
11:28 | For that reason I've tended to move away a little bit from this calculation. |
11:33 | This calculation is going to work for a mainstream run of the mill engine where we might be revving to perhaps 6000 to 8000 RPM. |
11:41 | As I've said already this is quite a broad calculation. |
11:46 | But if we're going to be using an engine that's running to extremely high RPM, or a rotary engine for that matter, then things change quite dramatically. |
11:57 | So another technique or another way of calculating our injector size that I'm going to cover here is actually thanks to the team at Injector Dynamics. |
12:07 | And this is care of their injector flow calculator. |
12:12 | So if we can just again look at my laptop screen, I've gone across to Injector Dynamics' website here. |
12:17 | And you can find this under the fuel flow calculator tab. |
12:22 | There's a little bit of a preamble on how this works. |
12:25 | But if we move down here basically on the left hand side of the Injector Dynamics fuel flow calculator, we have a range of parameters that we need to set based on our particular engine. |
12:40 | So for example we've got our engine displacement, our number of cylinders, number of valves per cylinder, our target boost pressure, the lambda that we're going to be running at wide open throttle, lambda at idle. |
12:52 | Another really key point, we're going to be talking more about this shortly, is our ethanol percentage that has a really dramatic effect on our required injector and fuel flow size. |
13:02 | Then our fuel pressure and also they've taken into account cam aggressiveness. |
13:07 | Now I've just gone through and put some numbers into those parameters there for a relatively run of the mull turbo charged two litre engine running on gasoline. |
13:19 | Now what we can see here is that the resulting graph on the right hand side shows us for each of the Injector Dynamics injectors, what sort of injector duty cycle we're going to be seeing at x RPM. |
13:32 | This is a really good way of demonstrating that the RPM that the engine's running to does have an impact on our injector sizing. |
13:40 | So for example if we looked at 8000 RPM with an ID725, 725 cc injector, at that particular point if we hover over it, it shows us that at 8000 RPM we're at 88% injector duty cycle. |
13:54 | So that's probably getting a little bit borderline, that's probably about as far as I'd like to run the injector. |
14:00 | If on the other hand we were going to run out to 9000 RPM we can see that that injector is completely tapped out. |
14:06 | We're at 99% injector duty cycle. |
14:09 | So we'd really need to step up our injector size in order to give us a little bit of head room. |
14:14 | If we move down the ID850 at that same RPM, we've dropped down to 82.4% injector duty cycle. |
14:21 | Now the other aspect with this particular fuel flow calculator is it shows us at the bottom, the required total fuel flow. |
14:29 | So for example there at 9000 RPM, we require 160.93 litres per hour of fuel. |
14:37 | So this particular calculation comes from a lot of data that injector dynamics have gathered from tuners all around the world. |
14:47 | They have gathered data and basically come up with the result that on average if we're running on gasoline, we need around about 0.35 litres of fuel per horsepower per hour. |
15:03 | Now that also just to be clear is a value that is rated at the wheel. |
15:09 | So this is dyno data from rolling road or chassis dyno data. |
15:14 | So of course the other aspect here that's important to note is the fuel flow calculator will show us what the differential pressure across the fuel pump is. |
15:25 | So this takes into account our base fuel pressure that we've added. |
15:29 | It takes into account whether or not we're running a constant pressure fuel system or a boost referenced fuel pressure system. |
15:36 | If you don't understand that, don't worry, I'm going to be talking about those two terms a little bit later in the webinar. |
15:41 | And then it also takes into account our boost pressure, and shows us that in this instance we would need whatever our total fuel flow in litres per hour is, at a rated pressure of 63.5 psi for our fuel pump. |
15:59 | Now of course the data here is specific to Injector Dynamics and their particular injector sizing. |
16:08 | We could of course also cross reference this to injectors from other manufacturers but the guys in Injector Dynamics have put a lot of work into this. |
16:17 | And if you can, I'd support them if you're going to use their fuel flow calculator. |
16:23 | So at this point we've talked about some of the information regarding our fuel injector sizing, and I've gone through two different ways of getting some idea of what injector size you're going to need for your particular application. |
16:39 | We've looked at a very simple calculation will give you a ballpark to work in, and we've looked at the Injector Dynamics fuel flow calculator. |
16:47 | One aspect we need to just discuss before we do move on here is the maximum injector duty cycle. |
16:53 | Now there's a huge amount of confusion out there in the industry, in the tuning world, about what is safe, what we can get away with. |
17:02 | And there's probably some misconception as well around why we need to limit the maximum injector duty cycle. |
17:09 | There is what I would call a tuner myth that if we run the injector at excessive injector duty cycle it can overheat and this can cause problems with the injector reliability. |
17:21 | That's actually not the case, I've discussed this in depth with Paul Yaw from Injector Dynamics, and there is actually a test that injectors need to go through which is where they are run at 100% duty cycle, run continuous for a period of time. |
17:36 | So they don't get damaged from doing so. |
17:40 | What we will find though is that at the higher injector duty cycles we see a non linear area of injector operation so the flow from the injector deviates from linear. |
17:52 | So this gives us a little bit of difficulty in actually controlling the ECU I should say and controlling accurately the injector flow. |
18:00 | So at very high injector duty cycles we can start seeing inaccuracies in our fuel delivery. |
18:06 | The other aspect is we do need to retain some head room in our fuel system. |
18:12 | So we don't want to be running our injectors maxed out. |
18:15 | This would mean that if under atmospheric conditions, maybe we get a very very cold day, which requires additional fuel due to the higher air density in order to maintain a specific air fuel ratio, we've got no head room for that to occur. |
18:31 | Likewise if we're running a turbo charged car and for whatever reason we end up with a slight boost spike or our boost increases very marginally, if we're already maxed out on our fuel system, we're not going to have the potential to cope with that. |
18:45 | So generally I like to keep my maximum injector duty cycle in the range of around about 85% to 90%. |
18:53 | This gives us a little bit of head room and it means that we're not operating right in the top of that non linear area of injector flow. |
19:00 | So this also gives us a little bit of head room in the future if we are going to maybe make further modifications to the engine and increase the power level. |
19:09 | It's always a good idea to just have that head room there. |
19:13 | Before we move onto fuel pump sizing, these two will sort of work hand in hand, there is of course the ability to increase the flow through the injector by increasing our fuel pressure. |
19:28 | Now a lot of people would think that that's an instant get out of jail free car. |
19:32 | If we've modified our car and we've maxed out the injector flow well all we need to do is increase the fuel pressure, it's going to give us some extra injector head room, we're going to get extra flow through the injector for a given pulse width. |
19:46 | But there are no free lunches in this world. |
19:49 | And when we increase the fuel pressure in the system, yes the flow through the injector does increase. |
19:57 | However it also means that the fuel pump has to work extra hard to provide that fuel flow, and this can get us into a situation where we may have achieved increased fuel flow through the injector but we may actually find that we're now maxing out our fuel pump flow. |
20:15 | The other aspect when we increase the fuel pressure, is that it does affect the operation of the injector in terms of its injector dead time, or injector latency. |
20:25 | And if we go very very high with our fuel pressure, we can get into a situation where at low battery voltages, which we may see perhaps during cranking, we may actually see a situation where there isn't enough voltage to physically open the injector, so the injector just will not open, and of course at that situation it's impossible to get our engine to start. |
20:51 | OK so if we've gone through our fuel system calculator, our fuel flow calculator and we've decided what size injectors we need for our particular engine, the next aspect we can come to is our fuel pump sizing. |
21:06 | Now the fuel pump sizing needs to be able to support all of the engine's fuel requirements. |
21:15 | It needs to be able to provide whatever amount of fuel our engine needs. |
21:19 | Obviously this in turn means it needs to be able to provide all of the fuel that our injectors could potentially use. |
21:25 | So if our injectors for example were operating at 100% injector duty cycle, we need to pump enough fuel so that we're supporting those injectors. |
21:35 | And in reality what we actually need to do is provide a slight over supply of fuel, in order to maintain some fuel pressure. |
21:46 | So what I mean by this is let's say for example we have 4000cc injectors fitted to a four cylinder car. |
21:53 | Ignoring all other aspects at the moment and assuming they just simply flow 1000cc per minute when they're wide open to 100% injector duty cycle, this means that our total fuel flow at that point is 4000cc or four litres per minute. |
22:09 | So on face value we'd think that if the fuel pump can supply four litres of fuel per minute, it should be happy days. |
22:16 | That can cope with the injector flow and everyone's going to be happy. |
22:21 | The reality is though that if we are right on the limit where the fuel flow from the pump only barely matches the fuel requirements of the injectors, we're going to get into a situation where we have little to no fuel pressure. |
22:35 | And then everything goes downhill because the injectors can't flow the amount of fuel that they're supposed to et cetera. |
22:42 | So in order to maintain pressure in our system we need to actually provide an oversupply of fuel. |
22:49 | So as a rough rule of thumb I generally try and size the fuel pumps so that they can support around about 25% more fuel flow that the injectors. |
22:59 | So in other words if we were looking at four litres of fuel per minute for all of our injectors wide open, we'd really want our fuel pump to be able to supply five litres of fuel per minute just to provide that over supply, just to provide that extra fuel. |
23:18 | And generally when we're talking about fuel pump flow, we're not actually talking in litres per minute, this is another sort of confusion where when we're talking about injectors we're talking cc per minute, when we're talking about fuel pump flow, we're much more likely to be talking in litres per hour, or if you wanna talk in imperial numbers, gallons per hour. |
23:38 | Of course pretty simple, if we're got five litres of fuel flow per minute we just need to multiply that by 60 because there's 60 minute in an hour, that gives us a required fuel pump flow of 300 litres per hour. |
23:52 | So that's how we can take our total injector flow for our engine and work out from that approximately what we're going to need in terms of our fuel pump flow. |
24:03 | However like with anything in tuning, it's never quite entirely that simple, and there's a little bit more to it. |
24:13 | OK so first of all we need to understand that in terms of our fuel pump sizing and our fuel injector sizing, this is also going to depend on the type of fuel we're running on. |
24:24 | So for our calculations everything we've looked at so far we have been assuming that we're running on gasoline. |
24:30 | If we're running on E85 for example, we're going to find that we need to supply quite a lot more fuel to make the same amount of power, to match the same amount of air flow into the engine. |
24:41 | We're obviously also, as we've found, we're going to need to take into account our desired engine power and our desired engine speed. |
24:49 | In terms of fuel pump sizing, another really rough rule of thumb that I tend to use, is that we need approximately one litre per minute of fuel flow for every 200 horsepower we want to make. |
25:06 | And when I'm using that term I'm talking about fly wheel power. |
25:10 | So again it's not 100% accurate in all situations but it's a really good sanity check if you're looking at a fuel system and you're trying to figure out if the fuel system is just not keeping up on the dyno and that's why you're seeing problems. |
25:25 | OK so in terms of the aspects of our fuel system that can affect the flow from our fuel pump, we're going to have a look at a couple of aspects now. |
25:36 | In our example we've just looked at, we found that we needed 300 litres of fuel flow per hour. |
25:43 | So on face value we'd assume that we just simply need to go an choose a pump that can flow 300 litres per hour of fuel. |
25:52 | But we do need to consider the pressure that that pump is going to be running at. |
25:58 | What we find is with an electric fuel pump, as we increase the fuel pressure, this touches on what I was talking about a little bit earlier, as we increase the fuel pressure it's harder for that pump to pump the fuel and hence we see the actual flow from the fuel pump tend to drop off. |
26:15 | So if we can just jump across to my laptop screen at the moment. |
26:19 | This is a graph that is provided with the Walbro 450 litre per hour E85 rated pump. |
26:27 | We've got one of these running in our Toyota 86 development car. |
26:32 | So I just wanna talk about a few of the aspects on this graph here. |
26:35 | On the left hand axis we've got our fuel flow there in gallons per hour. |
26:41 | On the horizontal axis here we've got our fuel pressure. |
26:47 | So this is the differential fuel pressure that the pump is operating at. |
26:52 | OK so what we can see here is that if we look at, let's take a point here, at approximately 40 psi, we can see that our fuel flow in gallons per hour here, let's take our green point which is at 13.5 volts, we're at somewhere around about maybe 110, 115 gallons per hour. |
27:16 | If on the other hand we now increase the fuel pressure up to, oop that's a horrible line, let's try that again. |
27:22 | We increase the fuel pressure up to 80 psi, we can see that that same green graph line now is only around about 90 gallons per hour. |
27:33 | Now you might think that that's excessive, we're never going to be operating at 80 psi. |
27:40 | But we're not just talking here about our base fuel pressure. |
27:44 | For example if we had set our base fuel pressure on our regulator to 40 psi and then we're talking about a turbo charged car, and obviously pretty unlikely on pump gas, but for the sake of this example, let's say that we now increase our boost pressure up to 40 psi. |
28:00 | A boost pressure referenced fuel pressure regulator is going to then increase the fuel pressure in line with our boost. |
28:07 | So what we do is we add our boost pressure, 40 psi, on top of our base fuel pressure, which was 40 psi, so we get to 80 psi. |
28:16 | So right at the point where our engine is now making maximum power under very high boost, we've seen that our fuel flow from our pump has dropped from around about 110, 115 gallons per hour, down to about 90 or 95 gallons per hour. |
28:31 | So that's a pretty significant problem. |
28:33 | What we can see is as we start to increase the fuel pressure I should say even further, our fuel flow simply drops off a cliff, so we certainly wouldn't really wanna be running this sort of electric pump at much over about 80 psi. |
28:48 | Now at the same time because the pump is working harder and harder to pump that fuel, we can also see that our current is climbing the whole time. |
28:59 | So the higher our fuel pressure, the more the current draw from the fuel pump will increase. |
29:05 | So of course with this in mind we need to have a little bit more detail than simply what our fuel flow needs to be. |
29:15 | We want to know what our fuel flow needs to be at the pressure the fuel system's going to be running at. |
29:22 | So in this case if we're talking about a boost pressure referenced fuel system, fuel pressure regulator, we want to take our base pressure, we want to then add our maximum boost pressure that we're going to see, and we want to use that at the point in our table to decide on our flow. |
29:37 | So if we just jump across to our next screen here, we're got a graph here, this is exactly the same, oop that disappeared, that's not very helpful. |
29:50 | See if I can just get that back. |
29:54 | Right there we go. |
29:55 | We've got exactly the same information here, just presented in a numeric format. |
30:00 | And what we'd want to do in our example there with 40 psi base pressure and 40 psi boost, we would be looking at the flow numbers here at 80 psi differential pressure, that's what the fuel pump's actually going to be operating at and we want to know that our fuel flow under those conditions is adequate. |
30:20 | In this case if we simply used our previous example, we wanted 300 litres per hour, this gives us 330, we've got a little bit of extra head room so that's going to work for that particular example. |
30:32 | Now the other aspect with our fuel pump flow is it is variable depending on the amount of voltage being delivered to the fuel pump. |
30:43 | Now I think I'll probably try and just drag up my other graph here because it shows it a little bit better. |
30:50 | Let's just jump into this one here. |
30:53 | Right so this particular graph actually shows two points, I kind of glossed over it before. |
30:58 | But if we look at our flow at the moment, let's ignore current for this point. |
31:03 | We've got our green line which shows the fuel flow at 13.5 volts and then we've got our blue line which shows the flow from the fuel pump at 12 volts. |
31:14 | And what we can see is there's a pretty big difference between those two. |
31:18 | So for example here if we look at 40 psi, we've got somewhere around about 110, 115 gallons per hour at 13.5 volts and we're a bit under 100 gallons per hour if the voltage drops to 12 volts. |
31:33 | So what's all this mean? OK with our automotive electrical systems we are expecting the voltage in most instances to be around about 13.8 to perhaps 14.2 volts. |
31:45 | This is generally the charging voltage of the alternator, the charging system of the car. |
31:50 | So this is what the fuel pump should be seeing, this is what it should be delivered. |
31:55 | However due to a variety of potential reasons, perhaps poor wiring to the fuel pump, maybe poor earthing, we definitely see this a lot with factory fuel pump wiring when we go and fit an aftermarket fuel pump. |
32:09 | We may actually find that under operating conditions, the fuel pump isn't receiving the correct charging voltage, so it isn't receiving a full 14 volts. |
32:20 | And it's not uncommon to see that voltage drop away to maybe only 10.5, 11 volts, at high RPM and wide open throttle, where we really need that fuel flow the most. |
32:31 | And in this instance we can start to see our fuel system struggle to keep up even though we've got a fuel pump that on paper should be more than up to the task. |
32:40 | So one of the aspects of our fuel system design is we want to be very certain that the fuel pump is wired correctly, that our charging system is working correctly and that our fuel pump is receiving full operating voltage when we need it the most. |
32:58 | OK so I just wanna also touch here on the mechanical pump design. |
33:03 | This is probably not something that we are going to see too often in a street car or a circuit car. |
33:10 | But as we've seen here, let's just jump back to our graph for the moment. |
33:15 | We saw with our electric pump, there's point around about, for this pump here, at 80 psi differential pressure where the flow kind of drops off a cliff and as we continue to increase the fuel pressure we just see the flow drops away to almost nothing. |
33:30 | Now for most of our street cars this probably isn't going to create a huge amount of issue, but certainly in the turbo charged or super charged engines that we see in drag applications, this can be a huge problem. |
33:43 | And it's not uncommon to see, particularly some of the high performance import drag cars running in the low sixes, and high five second quarter miles, it's not uncommon to see those sorts of engines running boost pressures in the region of 90 plus psi. |
33:59 | So all of a sudden when we add 90 psi of boost pressure on top of what'll often be an 80 psi base fuel pressure, we're seeing maximum differential pressure in the region of about 170 psi and it's very very difficult to find an electric pump that can cope. |
34:18 | So in these applications we tend to see the use of mechanical fuel pumps which are driven directly from the crankshaft of the engine. |
34:27 | They have the advantages that they do provide massive amounts of flow, they are suitable for that drag application. |
34:35 | But they can be difficult to prime during cranking at very low engine speeds like we're seeing when the engine is being cranked over, they generally don't provide enough fuel pressure to get the engine started so it can be a necessity on these sorts of systems to provide an electric primer pump to get the engine initially up and running. |
34:58 | OK so we've talked about our fuel pump requirements. |
35:02 | We're going to now talk about a way we can test the fuel pump and see if this is actually up to task, it's actually working. |
35:12 | Because it's one thing looking at the manufacturer's data there, we looked at the Walbro data, all of the pumps that are available to us will have their own data. |
35:22 | But here we're looking at data that's been collected on a test bench under perfect conditions. |
35:27 | When we've actually gone and installed the pump in the car, maybe we've used plumbing that is a little bit small, maybe we've got a fuel filter fitted in the system that is a little bit restrictive. |
35:39 | All of the installation aspects can actually add up to reduce the flow from the pump under real world conditions. |
35:48 | And one of the tests that I quite often will perform on a fuel pump or a fuel system is to test the flow that I am seeing at the return line. |
35:59 | And this allows us to test the actual fuel pump performance as it's installed in the car. |
36:07 | So we're seeing everything as installed including the actual voltage that the pump's going to be supplied. |
36:13 | Now this test is only going to work if we're talking about a fuel system that has a return line, or in other words we've got a fuel pressure regulator mounted in the engine bay, and we've got a return line that runs back to the fuel tank. |
36:27 | We can't perform this test unfortunately with a returnless fuel system where the fuel pump and regulator are both mounted in the tank and we've only got a single feed line that runs up to the engine bay. |
36:39 | So the test I perform is to remove the fuel return line from the tank or surge tank, whatever that may be, and run it into a graduated container. |
36:47 | Then we also want to, if we're talking about a super charged or turbo charged car we then want to apply the maximum amount of boost pressure that we intend to run onto our fuel pressure regulator. |
37:00 | This can be a little bit tricky, there are test tools, diagnostic tools available that we can use to provide a pressure signal onto thing such as our fuel pressure regulator. |
37:11 | So if for example we're expecting to run 30 psi of boost, we're going to provide 30 psi of positive boost onto that fuel pressure regulator. |
37:19 | Then what we want to do is start the engine and we want to run it for a period of one minute and we want to watch the fuel flow coming out of the return line. |
37:28 | After the engine's run for exactly one minute we can shut the engine off and we want to look at what volume of fuel we collected in our graduated container. |
37:37 | And this really comes back to what I was saying before, my really approximate rule of thumb is that we need one litre of fuel per minute, for every 200 horsepower we want to make. |
37:48 | So that's a really good sanity check if we've got a fuel system installation that really we're questioning whether it's up to task, it's a relatively quick test that we can perform, and that's going to give us a pretty good result. |
38:02 | So in other words if we did that test, and we ran the engine and over one minute we ended up with two litres of fuel in our container, that means that we've got enough fuel flow for approximately 400 horsepower at the flywheel. |
38:22 | OK we're just going to talk now about the requirements if we're going to be running on an ethanol fuel. |
38:31 | Here we'll just talk simply about E85, because it probably is still the most common ethanol blend. |
38:38 | So all of the calculations we've looked at so far are based on using pump gasoline. |
38:45 | If we change to E85 then we need to actually supply a lot more fuel and the reason for this is because of the fuel's characteristics. |
38:53 | First of all it has a vastly different stoichiometric air fuel ratio. |
38:58 | For E85 out stoichiometric air fuel ratio's about 9.81:1 whereas for gasoline we're around about 14.7:1 The density of the fuels is also different. |
39:10 | And all of this really without going through the calculations means when all's said and done, we need to supply around about 40% more fuel by volume when we switch form gasoline to E85. |
39:23 | So of course we can just factor this in if we're using a fuel calculator or a fuel pump calculator that's working on the basis of gasoline, we simply multiply the results we achieve by 1.4, a factor of 1.4 This is going to show us what we would need as we switch to ethanol or E85 in that instance. |
39:43 | I won't get too deep into this, we also do need to consider of course the compatibility of our fuel system with the ethanol fuel. |
39:55 | OK the last thing I want to touch on here is the fuel pressure regulator. |
39:59 | So this again as I mentioned right at the start is an area that a lot of people get confused with. |
40:05 | There are two main types of fuel system. |
40:09 | There is a returnless system where the regulator is mounted in the fuel tank. |
40:15 | A regulator is there to maintain a consistent fuel pressure in our fuel system which is required for our injectors to actually be able to supply fuel. |
40:25 | So the returnless system has the regulator mounted in the tank and these run at a fixed fuel pressure. |
40:32 | Generally this is in the region of about four bar or 58 psi. |
40:37 | The other system we will see is a return style fuel system, where there is a fuel pressure regulator mounted in the engine bay and there is a return line running from the fuel pressure regulator back to the fuel tank. |
40:52 | So I've got here just for an example, an aftermarket regulator. |
40:57 | This is a Turbosmart FPR-1200, it's rated at 1200 horsepower. |
41:02 | It's fitted with dash six AN fittings, and this does have a vacuum nipple on it which means that we can connect this to our manifold, our inlet manifold and this means that the fuel system will be what's referred to as boost pressure referenced, or in other words manifold pressure referenced. |
41:24 | Now the idea behind this is that the fuel pressure regulator will increase the fuel pressure as we build boost, or decrease the fuel pressure as we go into vacuum. |
41:36 | And the idea here is that we maintain a constant difference between the fuel pressure at the top of the injector and the manifold pressure at the bottom of the injector. |
41:47 | And this is referred to as maintaining a consistent differential fuel pressure across the injector. |
41:52 | Now if we can achieve this then the fuel flow through the injector for a given pulse width will remain constant. |
41:59 | With the fixed fuel pressure, constant fuel pressure that we see with a returnless fuel system, the situation is quite different, this results in a continuously changing pressure across the injector, differential pressure across the injector. |
42:15 | And particularly if we're talking about a turbo charged application here. |
42:18 | So if we've added a turbo charger to a fuel system that runs a constant fuel pressure, what we find is that as we increase the fuel pressure, we're actually decreasing the differential fuel pressure across the injector. |
42:32 | And in other words we're reducing the volume of fuel that the injector can supply for a given pulse width. |
42:38 | So this is why a common modification, when we add a turbo charger or super charger to a late model factory car that runs a returnless fuel system and a fixed or constant fuel pressure, is to change the fuel system so it uses a manifold pressure or boost pressure referenced fuel pressure regulator. |
42:57 | Now one of the terms I just want to clear up the confusion here is the term rising rate fuel pressure regulator. |
43:04 | This is a term I see used constantly and it's almost always misunderstood. |
43:09 | Most people use the term rising rate referring to a fuel pressure regulator that increases fuel pressure in line with boost pressure. |
43:19 | Now that's exactly what a fuel pressure regulator should be doing. |
43:25 | Generally what we will expect to see is that the fuel pressure regulator will adjust the fuel pressure in a 1:1 relationship between boost pressure and fuel pressure. |
43:36 | So in other words in our example before, we had 40 psi base fuel pressure, we've added 40 psi of boost pressure, we should see a 1:1 relationship so we should end up with 80 psi of total fuel pressure. |
43:48 | So this isn't a rising rate fuel pressure regulator, this is just a linear fuel pressure regulator doing exactly what it was designed for. |
43:56 | The term rising rate fuel pressure regulator is really it's a throwback to the days where we didn't have access to advanced ECUs like we do now and tuning was a little bit harder to achieve when we were modifying factory cars. |
44:12 | And a way of cheating the fuel system requirements when we added a turbo to a naturally aspirated car was to use a fuel pressure regulator that increased the fuel pressure more than we've added boost. |
44:25 | So in other words if we've gone from 40 psi, we've added 40 psi of boost pressure, instead of adding 40 psi of fuel pressure, the rising rate fuel pressure regulator, would instead add perhaps 60 few psi to our fuel pressure so that is what a rising rate fuel pressure regulator is. |
44:44 | In my own experience very very uncommon these days and not something that I have used in probably the last 12 years of my career. |
44:56 | We are going to move into questions and answers shortly, so if you do have any questions please ask those in the comments or the chat, and I'll deal with those when we get to the end of the lesson. |
45:09 | The last thing I wanted to touch on here, is how to know if you've got problems when you're on the dyno. |
45:16 | So for example what is a giveaway sign that there's something wrong here. |
45:22 | Now first of all this is generally going to show up as a lean air fuel ratio at high RPM and high load. |
45:28 | And at this point what we're going to do generally is we're going to find our air fuel ratio's lean, we're going to back off, abort our run on the dyno, and perhaps add some additional fuel into our fuel table or increase our volumetric efficiency to try and add some fuel back in in the area where it's lean. |
45:47 | We're generally going to get into a situation if the fuel system isn't up to the task where we can go through this process and we're going to add fuel but get no more fuel actually supplied to the engine because something's maxed out, and our air fuel ratio will remain lean. |
46:03 | Now of course at this point it could be due to either the injector size or the fuel pump size or perhaps even in the perfect storm it could be both that are causing our problem. |
46:14 | Now ideally in order to highlight this issue we would watch the fuel pressure. |
46:20 | But often that isn't fitted. |
46:22 | I would say probably less than 30% of the cars that I tune have a fuel pressure sensor fitted. |
46:28 | So it's a little bit harder to watch that often. |
46:32 | And often it isn't something that we will tend to focus our attention on too much after we've actually set our base fuel pressure, even if we have a fuel pressure sensor fitted. |
46:42 | So it is something that's easy to overlook. |
46:45 | So let's start by talking about what happens, we've gone over the point that we need to continue adding fuel at higher RPM and we're going to end up with our air fuel ratio still lean. |
46:58 | Now if we understand what we should be expecting from the shape of our fuel table, this is going to give you a good pointer. |
47:06 | Generally the shape of our volumetric efficiency of our engine or our fuel table should broadly match the shape of the torque curve of the engine. |
47:14 | And generally that torque curve is going to start relatively low. |
47:17 | It'll peak somewhere through the rev range, and then at higher RPM we're going to find that our torque will begin to nose over and drop away. |
47:24 | Now if we take that into account we should be seeing the same general trend from our fuel table. |
47:31 | And in the situation where we've got a deficiency in our fuel system we're going to see the exact opposite, what we're going to find is that the shape of our fuel table continues to increase, so our numbers will continue to climb at high RPM even though we've gone past peak torque and our actual torque curve is dropping. |
47:49 | So this is a really really good indicator that something's not wrong. |
47:53 | If for any particular reason your shape of your fuel table is not matching the shape of your torque curve, that's a sign to look a little bit deeper. |
48:06 | The other aspect of course that we can see is if we look at our logging we may get to a situation where our injector duty cycle has hit or exceeded 100% injector duty cycle. |
48:17 | This will depend on the ECU but often the ECU won't give you a warning and you'll actually have to do looking for it. |
48:24 | So this is another situation where we need to really keep our eyes open and look at all of the data we're seeing and make sure that we don't ignore any important aspects such as our fuel pressure, such as our injector duty cycle. |
48:37 | We need to really carefully look at our logging and see what the tell tales are that are trying to tell us what's actually wrong there. |
48:45 | So what do we do if we're in this situation? Well first of all we want to stop tuning. |
48:48 | This is something that we are not going to be able to fix with a laptop keyboard. |
48:52 | We're going to actually have to find out specifically what the problem is. |
48:57 | We want to check our logging, we look at our injector duty cycle. |
49:00 | If our injector duty cycle is still moderate, perhaps we're only at 60% or 70% injector duty cycle, and we're still seeing this problem, then it's a pretty safe bet that our fuel flow is not up to task and we'll find our fuel pressure is dropping away. |
49:17 | Obviously if we've got logging of our fuel pressure, that'll be apparent. |
49:21 | If we haven't it's time to actually fit a fuel pressure gauge, a mechanical fuel pressure gauge to the engine and monitor what's happening there. |
49:29 | Now if we do find that our fuel flow is nosing over and that's causing our lean areas at high RPM and high load, that's not necessarily to say that it is the fuel pump's problem. |
49:43 | Often on paper the fuel pump should be more than up to task and in this situation we want to dig a little bit deeper. |
49:51 | I would be checking the voltage being delivered to the fuel pump under a wide open throttle ramp run, often we can log this straight into our dyno, or we can get a little bit more ruthless with it and simply connect a volt meter to the fuel pump and watch what that volt meter's showing under high load, high RPM conditions. |
50:10 | Now if the voltage is dropping away then that shows us that there's a problem with our wiring, we need to address that. |
50:16 | The last area that we may need to address is this can also be the result of a partially blocked fuel filter. |
50:25 | Alright let's move into some questions and answers here. |
50:29 | So our first question comes from Barry G, who's asked does the type of fuel affect the brake specific fuel consumption of the motor? Eg for example the ethanol. |
50:39 | Yeah absolutely it does. |
50:41 | All of those calculations there in the brake specific fuel consumption values that I quoted were based on gasoline fuel. |
50:50 | So as we've talked about a little earlier in the webinar, we know that as we go from gasoline to E85, we need to add around about 40% additional fuel. |
51:01 | And that is represented in the brake specific fuel consumption. |
51:06 | Next question comes from Northern Forest Motorsports who's asked should I compensate for premix in injector selection for running a rotary without a metering pump? Oh look generally the amount of premix that you're going to be using in a rotary fuel system is really almost insignificant in the big scheme of things. |
51:27 | I know every engine builder, every rotary engine builder, has their own sort of ideas on what level of premix to run but generally if my memory serves correct, the last premix we ran was in the region of something like 50 to 100 mils of two stroke premix for every 20 litres of fuel. |
51:48 | So that sort of level of premix is simply not going to impact on your calculations. |
51:56 | Drew has asked does vacuum play a role in changing fuel pressure needed like boost does? Yeah absolutely so the idea behind the boost pressure referenced pressure regulator is that it maintains that differential pressure across the injector, and that differential pressure always remains the same. |
52:15 | So just like the fuel pressure regulator needs to increase fuel pressure as we move into positive boost, as we close the throttle and we move into vacuum, we also need to reduce the fuel pressure. |
52:27 | And actually I'll touch here on another aspect which I didn't talk about in the body of the webinar. |
52:33 | Often if we're using a fuel pressure regulator that is a little bit marginal in terms of its flow capability, maybe it's a little bit too small for the fuel flow that we're asking from is, asking from the fuel system, this will show up because we won't be able to reduce the fuel pressure far enough. |
52:52 | So if we've got an adjustable fuel pressure regulator, we may find that our minimum fuel pressure is artificially limited because the regulator essentially limits the flow through the return side. |
53:05 | So that's not gonna be an ideal scenario and it can affect the shape of our fuel table if we get down to low vacuum areas and our fuel pressure is artificially held higher than it should be. |
53:23 | Chris Goutchy has asked if you're running 1000cc injectors at 80% and you want to run E85, what size is next? OK so actually I think I missed this out. |
53:36 | There is a sizing calculation that we can go through, if we've got a system that's already set up and running on gasoline. |
53:43 | Generally on E85 we need, as I've discussed, we need to add about 40% more fuel volume flow, compared to what we were running on E85, so in that example there we need to multiply our injector size by a factor of 1.4 So in other words if you're running 1000cc injectors at 80% injector duty cycle, if we multiply that by 1.4, 1400cc injectors would also be running at that same 80% injector duty cycle, give or take, when we go to E85. |
54:18 | Of course you need to play around that that a little bit because to my knowledge I haven't seen a set of 1400cc injectors on the market, maybe you'd get away with a set of 1300s, or you may need to step up a little bit more. |
54:32 | Northern Forest Motorsports has asked do you trust a mechanical fuel pressure gauge any more or less than an electric? Yeah I do have problems with some of the mechanical fuel pressure gauges. |
54:46 | Particularly we're seeing a lot of fuel pressure regulators coming out of China which come with a fuel pressure gauge which is probably valued at something like $3 or $5 and I mean the old story goes you do tend to get what you pay for. |
55:02 | So you can't write these off, I've seen a lot of really cheap products come out of China that I've been sceptical of and they have actually worked surprisingly well but that's not always the case. |
55:13 | So generally in a mechanical workshop I'll have a mechanical fuel pressure gauge that I know and trust. |
55:20 | In my last workshop we had a Snap-on fuel pressure gauge so I can add that into the fuel system and I know that that particular fuel pressure gauge is accurate. |
55:31 | In terms of electric sensors as long as we're using a quality sensor, generally I use either Texas Instruments or Honeywell sensors. |
55:39 | Provided that they are installed correctly and wired correctly, we should be able to get reliable readings out of those particular sensors. |
55:48 | But it is a difficult one where we've had a car that's maybe been built elsewhere and brought to us to have the tuning performed, you can never take for granted that anything is correct. |
56:00 | Next question is I see articles about unreliable injector companies, how do you know you're buying injectors from a trustworthy company? What are some good brands? OK yeah it's a really good point. |
56:12 | There's been a lot of talk in the industry over the last few years about injectors, and I think it's become probably one of those hot topics out there. |
56:23 | There's a lot of companies have popped up, seeing that there is money to be made in supplying aftermarket performance injectors. |
56:31 | A lot of these injectors it is important to note, are based around the same core Bosch injector. |
56:38 | And they've gone through the process of what's referred to as decapping the injector. |
56:42 | So this is one aspect that's important, and in a lot of ways there are big similarities amongst a lot of the injector suppliers, 'cause the core unit that they're using, it was all coming from the same place. |
56:53 | So one of the big things is that the injectors themselves is one aspect but as our ECUs have become more complex, and more advanced, we really need good data about the injector characterisation to input into our ECUs in order to get the best possible results and the most accurate control over those injectors. |
57:13 | And that's where a few companies have stepped up and Injector Dynamics is one that I've mentioned. |
57:18 | Not a paid advert for Injector Dynamics I must point out here. |
57:23 | We've got no ties specifically to the company, but it is a product that I know and trust. |
57:28 | Injector Dynamics were one of the first companies to come out with proper characterisation data for the injectors and then we saw a lot of other injector companies jump on the bandwagon, sometimes creating their own, sometimes copying others. |
57:42 | In terms of finding out which companies that you should be dealing with, if you spend any time on enthusiast forums, you're going to find the particular brands that people are using and having good success with. |
57:56 | Long answer to a short question, sorry about that, but I needed to put in a little bit of detail there. |
58:02 | OK so Daniel Schultz has asked, how does the boost pressure affect the intake charge temp? I've heard approximately an added 13 degrees in the charge temperature for each pound of boost. |
58:13 | Haven't had an opportunity to play around with anything more than 25 to 30 psi. |
58:17 | Look probably a little outside of the scope of our particular webinar but just briefly, there's a huge number of factors here that will affect the charge temperature. |
58:27 | So yes as we compress air, whether it's a super charger or a turbo charger, thermodynamics says that we will be adding heat to that air. |
58:37 | The amount of heat that we add though will also be affected by the efficiency of the compressor. |
58:46 | So depending on the compressor we're using, where in the compressor map we're operating, will affect the ultimate compressor outlet temperature. |
58:55 | So we can't use an across the board value such as 13 degrees per pound of boost unfortunately. |
59:04 | Now next question comes from Andrew who's asked when do you need larger fuel supply lines? Haven't touched on this in this particular webinar, there is another webinar in our archive where we go into a lot more detail about the other fuel system component sizing. |
59:20 | So just like all of our components in our fuel system, the size of the fuel lines does also need to be taken into account. |
59:28 | For example we're not going to be able to flow 1000 horsepower of fuel through a quarter inch inside diameter fuel line so it does need to be taken into account. |
59:39 | There is as I've said some information there in the webinar archive that you may want to look at. |
59:44 | Alright that's taken us to the end of our questions there. |
59:47 | Again hopefully everyone's enjoyed today's webinar. |
59:50 | Hopefully it's given you some more insight into how to choose the correct components for your fuel system. |
59:57 | It's always going to save you money if you can do this once, do it right the first time, you're not going to waste any time on the dyno, and you're going to end up with better results. |
01:00:06 | As usual if you do have any other questions that crop up, please ask those in the forum and I'll answer them there. |
01:00:12 | Thanks for joining us everyone and I'll see you all next week. |
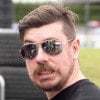