155 | Controlling Torque Delivery using Drive by Wire Throttle
Summary
DBW or E-Throttle is common on most late model production engines and we’re seeing more and more aftermarket ECUs adopt this technology. In this webinar we’ll discuss the technology, look at what is required from your ECU to control a DBW system, look at the configuration and testing, and finally discuss some techniques we can use to optimise torque delivery using DBW throttle mapping.
00:00 | - Hi guys it's Andre from High Performance Academy, welcome along to this webinar where we're going to be discussing some of the ins and outs of drive by wire throttle bodies or electronic throttle bodies. |
00:10 | And we're going to focus on what exactly that technology is, what we need in order to be able to utilise it, and then probably most importantly we're also going to see some of the advantages for us in the aftermarket. |
00:24 | How we can actually utilise aftermarket ECUs with drive by wire throttle body control in order to help control and improve the torque delivery from our engines. |
00:36 | So drive by wire throttle bodies are certainly nothing new, they've been relatively common now on most cars produced probably after about the year 2000, and these days it would be hard if not impossible to find a current generation car that is still equipped with a cable driven throttle body. |
00:56 | So first of all what exactly is a drive by wire throttle body? Well essentially it's a conventional throttle body with a normal butterfly controlling the air flow into the engine however instead of being actuated via a cable there is a DC servo motor that drives the throttle physically open and closed. |
01:16 | All of that is controlled by the ECU. |
01:20 | Now straight away that sounds a little bit scary. |
01:22 | We've now got no physical connection between the driver's throttle pedal and the throttle body itself. |
01:29 | And I know there is a large portion of people out there who are scared to death of drive by wire throttle, thinking that it's going to be a recipe for disaster. |
01:39 | Well first of all let's look at the facts. |
01:43 | These are the accepted technology now on just about every production car available and obviously the OEs are very very interested in limiting their liabilty so if the OE manufacturers are comfortable with that technology, first of all that should say something about it. |
01:59 | Now there's also some safety or redundancy measures at both the driver's foot pedal as well as in the throttle body itself that we'll talk about in a little more detail shortly and this allows the ECU to monitor, make sure that the throttle body is in fact doing exactly what the driver's requesting or in fact the ECU is requesting, and if something isn't quite right there, it can simply shut down the throttle control or bring on a rev limiter on the engine to prevent any damage. |
02:26 | The other aspect when people complain about the safety or reliability of drive by wire throttle, that I think is really often overlooked is there's numerous instances where cable throttle bodies have jammed and resulted in injury or even death, and I've had this happen to me on my own drag car which ran a cable throttle body. |
02:49 | Went through the end of the drag strip at around about 170 mile an hour, pulled the parachute, got on the brakes and realised that the car wasn't slowing down particularly well, and when I put my foot on the clutch, the engine came straight up onto the rev limiter. |
03:04 | What had happened when we actually got a chance to look at everything in the data, what had happened is that the throttle body had jammed at around about 50% or 60% throttle when I'd jumped off the throttle so obviously there's a really good chance that that could've ended badly. |
03:18 | So no technology is infallible and cable throttle bodies are certainly not a 100% reliable option as well. |
03:26 | I should've started with this webinar as well by mentioning that we will be having a question and answer session so if you do have any questions about drive by wire throttle in general or anything that I talk about during today's webinar, please ask those in the comments or In the chat and the guys will transfer those through to me at the end. |
03:46 | OK so why have OE manufacturers moved so dramatically away from cable throttle to drive by wire throttle? As I've said, it's pretty much impossible these days to find a new generation factory car still using a cable throttle. |
04:01 | So first of all it allows the manufacturers to have complete control over the engine torque delivery. |
04:08 | And what this means is that the ECU can control independently of what the driver's doing at the foot pedal what the actual throttle body's doing. |
04:17 | This allows for example the ECU to close the throttle body if the OE manufacturer decides for any reason that they don't want maximum torque then generated. |
04:28 | Even while the driver's trying his absolute hardest to push that throttle pedal through the fire wall. |
04:34 | This also allows control for aspects such as auto blipping for downshifts and this is useful for both automatic transmissions as well as the DSG or dual clutch transmissions that are becoming much more popular in late model cars. |
04:52 | These really couldn't be controlled adequately with a conventional cable throttle body. |
04:57 | In OE applications we also see the drive by wire throttle body being used for traction control. |
05:03 | Generally in a factory car these are really overbearing and quite dramatic. |
05:08 | And it's not so much of a function to allow you to slide the car, it's really something that closes the throttle really abruptly if wheel spin is detected to ensure that the car isn't going to lose control. |
05:23 | The other aspect that OE manufacturers use this for as well is to protect drive train components. |
05:30 | So if for example the engine is able to produce more torque than a component in the drive train maybe can handle then the manufacturer may choose to limit the throttle opening in turn to control that torque and make sure that the drive train components are going to be reliable. |
05:48 | Another way we've seen this used as well is often a manufacturer will produce multiple models of car, all based largely on the same engine and drive train platform. |
05:59 | And in order to sell a higher spec vehicle at a premium, often the manufacturer will release that premium model with more power. |
06:08 | Now there are obviously a variety of ways of doing this but in our locally delivered Holden or HSV product we've seen that this is often dealt with specifically through the drive by wire throttle tuning, and in particular in the lower spec or lower powered model, the electronic throttle body is simply closed through the mid range to artificially limit the torque. |
06:29 | That's also obviously good news for anyone buying one of those models the ability to retune them or reflash them, we can simply allow maximum throttle opening and gain back all of that power and torque that the car was missing. |
06:43 | OK so we've talked a little bit about the OE use here. |
06:47 | And we're going to now talk about what we would need in the aftermarket from an ECU in order to be able to adequately use drive by wire throttle control. |
06:59 | So for a start you are going to need to be using a programmable aftermarket ECU that is designed to encompass or encorporate drive by wire throttle control. |
07:11 | There's some really specific software and hardware that's required inside the ECU in order to control the throttle bodies so you're not going to be able to necessarily control a drive by wire throttle body with any ECU on the market, you're going to need one that is specifically designed to drive a drive by wire throttle. |
07:29 | Often we're also finding in the case of V6 or V8 engines, they'll often use dual drive by wire throttle, in some cases even up to four drive by wire throttle bodies so the ECU needs to be able to cope with the number of drive by wire throttle bodies we are going to be running. |
07:47 | Now in particular here, there's a small increase in the number of sensors that we are going to be using as well. |
07:54 | In order to be able to really accurately track what the driver's doing at the foot pedal, as well as what the throttle body's doing, these systems incorporate four individual sensors. |
08:06 | So there are two sensors at the accelerator pedal, and there are two sensors on the throttle body. |
08:12 | And these are normally known as accelerator pedal sensor one and two or main and sub, and throttle position sensor one and two or main and sub. |
08:21 | Now the reason for this is that safety is obviously paramount here. |
08:27 | And the ECU is constantly checking that both of the signals at the throttle pedal, and both of the signals at the throttle body match. |
08:36 | Now if one of those signals doesn't match what the ECU is expecting, this allows the ECU to go into a safety shutdown mode. |
08:44 | So we can't adequately run drive by wire throttle body control with just a single sensor at the throttle pedal and a single sensor at the throttle body. |
08:54 | So straight away what this should tell you, is you're going to need, for one drive by wire throttle body you're going to need four spare analog voltage inputs at your ECU header. |
09:04 | So if you overlook this you can find that you can really quickly chew through the available analog voltage inputs on your ECU and this may mean that you can run out. |
09:13 | So if you are using drive by wire or looking to use drive by wire throttle bodies, particularly on engines with multiple throttle bodies, it's really important to make sure that you've got enough spare inputs to cope with the throttle bodies plus anything else that you want to do with your ECU. |
09:31 | So we've covered how the ECU will detect what the driver's foot pedal's doing, and it can also detect what the actual throttle body's doing. |
09:39 | It also needs to physically be able to drive the DC servo motor that opens and closes the throttle body, and this is done via a dual half bridge output. |
09:49 | So this allows the ECU to drive the throttle body in two separate directions. |
09:54 | It can physically drive it open and it can also drive it closed. |
09:58 | Now often there will also be some specific wiring information based on the ECU that you're using as to how the outputs to the throttle body need to be wired. |
10:11 | So that's all important just to make sure that we've got that safety or redundancy to make sure that the ECU can shut down the throttle or bring on a rev limiter if something does go outside of bounds. |
10:26 | The other thing that the ECU will do is it will monitor that actual throttle position versus the target throttle position. |
10:34 | And if there is a significant error there, the ECU will also detect that something's not right and again can shut down the throttle and go into a safety or limp home mode. |
10:46 | OK so obviously again with safety being paramount, we've got something here that has got the potential to cause us a lot of damage if it isn't set up. |
10:55 | It is essential to make sure that your drive by wire throttle system is correctly installed, correctly wired, and then correctly calibrated or set up inside your ECU. |
11:06 | Now in order to do this, what I'm going to do, is just take you for a tour of the setup or functionality here in the Link G4 Plus ECU, fitted to our Nissan 350z. |
11:19 | Now obviously the drive by wire throttle setups for various ECUs are all going to look a little different, but don't let that bother you too much, what we're looking at really here is the fundamental or core principals behind the drive by wire setup, and these are going to be broadly similar regardless what ECU you are tuning. |
11:39 | So let's head across to my laptop screen at the moment, we're on our drive by wire throttle target. |
11:44 | What I'm going to do is just go through to our setup so you can see exactly what's involved here. |
11:50 | We'll go to our E-throttle 1 setup. |
11:52 | And this is all of the parameters available here. |
11:55 | Now for a start we can see that our E throttle mode at the moment is on setup mode. |
12:02 | This is a mode that the G4 Plus uses only while we are going through the setup process, and it actually disables the safety functionality in the system. |
12:11 | So it's really important with the G4 Plus, once we have gone through and we've configured and set up our drive by wire throttle, we can double click here, and we would want to actually select on, and that will bring on the safety parameters. |
12:26 | We've got here the ability to choose a number of tables we're going to be using. |
12:30 | I'm not gonna focus too much on these parameters right now because we're gonna come back and talk about them in detail shortly. |
12:35 | So let's just gloss over that. |
12:37 | Now the important part that I wanted to really focus on here is our PID setting. |
12:42 | So that's our proportional, our integral, and our derivative gains. |
12:46 | And these are really the key aspect to getting good control over that drive by wire throttle body. |
12:54 | So for those who aren't familiar, a PID control algorithm is an algorithm that's common in just about any aspect of our ECU where we're looking at controlling an aspect and making sure it meets a target. |
13:07 | So for example a really common one would be closed loop boost control where we have a boost pressure target. |
13:13 | The ECU is monitoring the actual boost pressure that we've got, comparing it to that target, and if we're not quite at the target, it's going to adjust the output to our wastegate solenoid in order to drive the boost pressure towards our target. |
13:26 | So that's exactly the same concept that we're using here for our drive by wire throttle body. |
13:31 | The ECU has a target throttle position, that's based on the driver's foot pedal, and then it's also monitoring the actual position of the throttle butterfly. |
13:41 | Now if the position of the throttle butterfly doesn't match the target then the ECU is going to drive the throttle body in order to reduce that error, and the way it makes adjustments to the DC servo motor position is based on these proportional, integral and derivative gain elements. |
13:59 | So again these three items here are really key to getting good, accurate, and fast control out of our drive by wire throttle body. |
14:10 | Now I know a lot of you will be sitting there going OK well that's great but how do I come up with these numbers, and this is another really important part here. |
14:17 | Again because getting these wrong can potentially result in a dangerous situation with poor control over the throttle body. |
14:25 | These aren't numbers that we should be coming up with ourselves. |
14:29 | What I would recommend, is when you're looking at an installation that you talk to the ECU manufacturer. |
14:35 | The ECU manufacturer obviously also wants to keep you safe, and they will have the correct parameters for most of the common or popular throttle bodies that are on the market so you don't actually need to do that hard work yourself. |
14:49 | Now for this case if we just go to our help file here, and what I'll do is I'll click on E throttle, and we'll come down to our Ford BA Falcon electronic throttle just for an example. |
15:02 | So straight away in the setup notes here inside the Link G4 Plus software, inside their help file it gives us all the information we need for a range of popular throttle bodies. |
15:11 | In particular when it comes to our wiring, we've got the wiring for the throttle position sensor and also the throttle motor. |
15:18 | And then we've got the setup notes which gives us our proportional integral and derivative gain. |
15:24 | Also our dead band which is basically the amount of error that the ECU will accept between our target throttle position and our measured throttle position before it tries to drive the throttle towards that target harder. |
15:40 | We've also got our maximum and minimum duty cycle for the servo motor and the frequency that it's going to be operating at. |
15:48 | So again this makes it really really easy, we don't have to come up with these numbers, and if you don't have these numbers in a help file, please make sure you get hold of your ECU manufacturer and get their advice. |
16:02 | Lastly if you are dealing with a throttle body that we don't have or the ECU manufacturer doesn't currently have parameters for or setup information for, most of the ECU manufacturers that I deal with would ask you to send that throttle body to them and they'll actually characterise it themselves on the bench making sure that they have got proper control over the throttle body and then they'll send it back to you along with the correct configuration information. |
16:30 | So again just to reiterate, you don't and shouldn't be coming up with these numbers yourself. |
16:37 | Alright so we've got all of those parameters set up there already. |
16:41 | One other aspect here, you can see at the bottom it's got this particular parameter that says when stalled in this case quiet throttle. |
16:49 | So what we find is that due to the frequency that the DC servo motor runs at, if the DC servo motor is being operated to meet a target, it will emit a light humming sound. |
17:01 | Not a problem obviously once the engine is up and running, you'll never hear that over the engine. |
17:06 | But particularly when the engine is keyed on, like I'm sitting here now and not running, you can hear that humming coming from the engine. |
17:15 | So in this case Link just gives you the ability that when the engine isn't running, quiet throttle will just disable the throttle control, and the throttle body will just sit in its natural or relaxed position. |
17:29 | OK so that's the basic setup or parameters that we need to go through there to get our throttle body up and running, and once we've got our throttle body up and running, obviously if we move our throttle pedal, we're going to end up with that throttle body also moving. |
17:44 | Which brings me to the next common myth or misconception that I hear so often out there in the industry. |
17:52 | And this time I'm actually going to borrow a little bit of information from a really great video that Mark McCoy from Motec Australia presented on basically myth busting the lag or latency involved with drive by wire throttle bodies. |
18:08 | Now I've heard this so many times over the years, people have driven a factory drive by wire throttle body car and complained about the dead or dull feeling that the throttle body gives, and it basically doesn't respond as crisply or as quickly as they would expect with a cable throttle body. |
18:27 | Now what you need to understand is that this technology has advanced a long way since the first drive by wire throttle body cars. |
18:33 | Some of those definitely were a little bit ugly and did result in this lag or mushiness to the throttle pedal. |
18:41 | That's really a thing of the past though. |
18:42 | Most of the modern factory drive by wire throttle cars, you'd never even know that there wasn't a cable connected between the throttle body and the driver's foot pedal. |
18:53 | And really what it comes down to if there is any lag or latency there, it's really more often than not a factor of the OE or factory tuning strategy. |
19:03 | They're purposefully adding in a little bit of latency or lag to soften the throttle response. |
19:09 | So when we're talking about an aftermarket performance application, particularly in the motorsport application, then we really don't need to worry about this. |
19:16 | It is a non issue and we shouldn't end up with almost any lag. |
19:21 | So again just borrowing from some of the terminology that Mark McCoy offered. |
19:25 | So if we have a perspective that we sort of can relate things to, generally most people would understand what a blink of an eye is. |
19:34 | And in general terms it's accepted that it's about 300 milliseconds to blink your eye. |
19:39 | Obviously that's not a lot of time. |
19:41 | So if we relate everything back to the blink of an eye, if we look at some data on how long it takes for us to go all the way from completely closed throttle to completely open throttle, if we essentially just jam our foot onto the throttle as quickly as we can, that takes somewhere in the region of about 30 milliseconds. |
20:02 | Now there is going to be a small amount of lag in the drive by wire throttle physically moving. |
20:08 | It's got some mass to that throttle plate, it takes some time to overcome that and physically start opening. |
20:14 | And dependant obviously on the throttle body we're talking about, we might see an initial delay between the driver's foot pedal moving and that throttle body first starting to crack open, somewhere in the region of 15 milliseconds, which is about 5% of the time it takes to blink. |
20:31 | Now if you can put that into perspective, it's essentially nothing. |
20:34 | Now there's also a delay once we do get to wide open throttle at the driver's foot pedal, until the throttle body has also reached wide open throttle and that's a little bit longer. |
20:45 | That's somewhere in the region again depending on the throttle body, something in the region of about 60 milliseconds. |
20:50 | So again if we put that into perspective, that's 20% of the blink of an eye. |
20:54 | Again almost no time at all. |
20:57 | Now the reality though is that these tests aren't actually that relatable to the way we really drive our cars out in the real world. |
21:05 | This isn't something we're tending to need to do, go all the way from closed throttle, to wide open throttle in 30 milliseconds. |
21:12 | It's just not a realistic way of using a car. |
21:16 | So in real world terms the tiny amount of latency that is inherent in a drive by wire throttle system, you'll never notice, and all of the horror stories and myths that have come about from mushy, slow response in the throttle system, really that's an aspect of the OE factory control strategy and not what we can do in the aftermarket. |
21:39 | And if we wanna relate this back to a cable throttle system, if you've got any slack in your cable throttle, which is really really common when they throttle's completely closed, that slack is also going to result in some lag or latency in the opening of a cable throttle so they're not immune to it either. |
21:57 | OK we're going to move into some questions and answers shortly. |
22:01 | Before we do that we're going to go through a bit of a practical demonstration and talk about some of the ways that we can utilise drive by wire throttle control for us in the aftermarket. |
22:10 | So if you do have any questions, please ask them in the comments and the chat and we'll get into those shortly. |
22:16 | So we'll just get our engine up and running while I'm talking here. |
22:19 | So for us in the aftermarket, what are the advantages if we're dealing with a car that has drive by wire throttle and why would we want to potentially add drive by wire throttle to our car? Well there are a number of advantages, and often the potential or what we can actually do with that drive by wire throttle control, really comes down to how smart you wanna be and how far outside of the box you want to look. |
22:49 | So first of all we're going to talk about torque management or power management for the engine. |
22:56 | So this is something that I think is often overlooked, even by tuners who really have a pretty good handle on how the engine operates. |
23:04 | And the key point here is that the air flow into the engine understandably is being controlled by our throttle body. |
23:12 | The problem with that though is that the air flow through the throttle body is very non linear. |
23:18 | So what I mean by this is we see a really large increase in the air flow through the throttle body, when we first move it open from it being completely closed. |
23:28 | So as we move say from zero to 50% throttle opening, we're going to see a really large increase in our air flow through the throttle body. |
23:37 | Once we get to 50% throttle, the increase from 50% to 100% sees a much much smaller increase in the air flow through the throttle body. |
23:46 | So what this results in is a really non linear relationship between throttle position and air flow, and it's that air flow that directly relates to the amount of torque our engine produces. |
23:58 | So let's have a look at exactly how that works. |
24:02 | Let's jump back into our Link software for a moment, and we'll just have a quick tour of what we're looking at here. |
24:09 | So you remember I showed you earlier that I've set this up with three active tables. |
24:15 | So we're going to talk about the first of those for the moment, so we'll just go and have a look at that table. |
24:22 | We're going to be working on E throttle target table one at the moment. |
24:26 | OK so this E throttle target table one, it's a three dimensional table. |
24:30 | On our vertical axis here we have our AP main, which stands for accelerator pedal main. |
24:36 | So this is what the driver's foot pedal is doing. |
24:39 | Obviously it's spanned between zero and 100%. |
24:42 | We've also got an RPM axis. |
24:45 | At the moment really this isn't particularly relevant, you can see we've got the same target throttle position regardless of our engine speed. |
24:54 | So this is set up essentially with a 1:1 relationship between the driver's foot pedal and the throttle body opening. |
25:02 | Now as I've just talked about though, this is going to result in a really unequal airflow through the throttle body as we open that throttle. |
25:10 | And this can become a problem if we're dealing with a car that produces a lot of torque, it can make it really difficult for the driver to get good throttle control over the engine and really control the car, particularly when we're cornering. |
25:24 | So in order to demonstrate this, let's have a look at running this car on our dyno, and we'll just get it into fourth gear. |
25:33 | And what I'm going to do is I'm going to go to 2000RPM, or 2200 RPM, it doesn't really matter. |
25:40 | Just got us up and running on our Mainline dyno at the moment. |
25:43 | So what I want to do, on our Mainline dyno, you can see we've got our torque gauge, which is showing the torque being registered in newton-metres. |
25:51 | So you can see at the moment that's saying 132, 131 newton metres. |
25:55 | What I'm going to do is I'm going to go all the way through to full throttle and we're going to see what sort of torque the engine produces when we're at 2200 RPM and full throttle, let's do that now. |
26:10 | OK so we can see at wide open throttle here, we're sitting at about 420, 425 newton-metres of torque. |
26:18 | Now in order to get really good control over this engine, what we would like is some relatively linear relationship between our foot pedal position and the engine torque. |
26:29 | So what we'll do now is I'm going to back off the foot pedal position and we're gonna come back down to 50% here, 50% throttle opening, just do that, and we're at 50%. |
26:42 | You can see that we've actually only dropped around about 10 to 15 newton-metres of torque. |
26:48 | We're still producing over 400 newton-metres of torque despite that fact that I've got the throttle body, well in fact the throttle body and the throttle pedal half closed. |
26:59 | So this isn't going to give us a lot of control over this engine using the driver's foot pedal. |
27:05 | Essentially it's going to almost feel like the throttle pedal's a switch. |
27:10 | It's going to do nothing initially, then as soon as we crack the throttle open a little bit, we're going to have this big rush of air flow, that's gonna give us a big increase in torque, and then once we've got the throttle pedal open past about 20%, the last 80% of travel is going to have almost no effect on the engine's torque. |
27:30 | So again with our 350z it's not that relavent because the engine doesn't produce much power or torque. |
27:35 | But if we're talking about an engine that does produce a lot of power and torque, this can make it really hard to control. |
27:42 | So let's have a look at how we could address that. |
27:45 | What I'm going to do now is go back to that same point, now 50% driver foot pedal or accelerator pedal. |
27:54 | And you can see that our target for our throttle pedal is sitting at 50%. |
27:59 | Instead of 50% what I'm going to do, is I'm just gonna highlight those two cells, and I'm going to set them to 25%. |
28:08 | Now if we look at our torque, we can see that we're not quite halfway, we're not at quite 50% of our maximum torque, but we're now at 300 newton-metres instead of 400. |
28:18 | So we're doing much better, we now have seen a sizeable reduction in our engine torque as we've closed down that throttle body. |
28:26 | So that's going to be a big help. |
28:28 | So the original table that I've shown you there, where we've got a 1:1 relationship between our foot pedal position and our throttle body position, let's just have a look at that graphically. |
28:41 | That's not particularly realistic. |
28:44 | This is something that we would probably be pretty unlikely to want unless we're dealing with an engine that really doesn't produce very much power at all and we can essentially use all of the power all of the time. |
28:56 | So let's have a look at what we more likely would want to use, so we'll have a look at one of our second E throttle, or drive by wire throttle target tables. |
29:07 | Let's just go through to E throttle target table two. |
29:10 | OK so this is much more likely to be what we would end up using. |
29:15 | So you can see in this case I've got a much slower onset of the throttle position. |
29:21 | So we're opening the throttle much slower relative to our foot pedal. |
29:25 | So for example, at this position here, when the driver's foot pedal position is at 30%, you can see we're only requesting 11.5% throttle opening. |
29:34 | And if we look at this we see we've got kind of an exponential shape to our throttle target table. |
29:41 | And this is going to make the engine much easier to control for the driver. |
29:47 | Again particularly with those engines that produce a lot of torque, it's gonna make it much easier for us to gain control of the engine. |
29:55 | And that's just one of the tricks we can play there. |
29:59 | Again as I said, a lot of what we want to do here, or what we can do, is gonna depend on exactly what we want to achieve, and there's no sort of limit what you can do with your imagination here. |
30:13 | So we'll talk about some of the other options. |
30:15 | So we've talked about torque management there. |
30:18 | We can also sort of adopt the same principal there for torque management in a car that's maybe two wheel drive and is traction limited, we can have a wet weather and a dry weather throttle target table and we can switch between those either via a switch on the dash, or alternatively we can even use some of the parameters in the ECU to automatically switch between these two throttle maps. |
30:44 | Maybe based on road speed or even what gear we're in. |
30:48 | So in that situation what we can do is use our throttle target tables to artificially limit the throttle opening, and this can be helpful to reduce the torque and help maintain traction. |
31:01 | So again let's look at our laptop screen here. |
31:03 | And this is where having a three dimensional table where we've got engine RPM as an x axis is useful. |
31:10 | So let's say for example we've got a particularly peaky engine that produces a lot of torque down around 3000, 3500 RPM. |
31:19 | What we could choose to do there, in order to help control the car, make sure that the car doesn't end up going into wheel spin, we might want to limit our ultimate throttle opening at 3500 RPM to something like 60%, and then we might interpolate that outwards and downwards. |
31:39 | So this is just going to artificially limit our throttle opening and make the power delivery a little bit more manageable, essentially reducing that peak torque value. |
31:48 | Of course once we're in the higher gears and the car is a little bit more settled, we could revert to a full throttle map as well. |
31:55 | Another way that I've actually used this myself, for a number of years I was the parity manager in the New Zealand V8 Touring Car class. |
32:04 | This is a class where a variety of different engines were used including a five litre Toyota V8, a five litre Ford V8, and a 6.2 litre GM LS V8. |
32:16 | And the idea was that all three of those engines needed to produce exactly the same power and torque curves. |
32:22 | And what we did with that was use the drive by wire throttle body along with one of these three dimensional tables to essentially detune the more powerful or more torquey engines to match the torque and power curve of the lowest power engine. |
32:37 | And that worked remarkably well, we managed to get really good parity across those three very different engines. |
32:45 | OK we've also got another application that I was involved with which was a circuit car that ran in a class where there was a breakout time or breakout lap time. |
32:58 | So essentially what this meant is that the car couldn't go faster than a certain lap time, if it did it ended up getting penalised. |
33:06 | And the particular car I was involved with the tuning on was an E36 BMW M3, and it was fairly highly developed, and at the end of the development process the car was able to break out fairly regularly at most of the racetracks that it visited. |
33:22 | Now one way of doing this would of course be to set up a throttle map to artificially reduce the power from the engine to make sure that it didn't break out. |
33:32 | That's great and that's going to prevent the car from breaking out but of course that additional power can be a benefit when you're stuck in a fight with a number of cars and you need a little bit of additional power to get through the field and make up places. |
33:46 | So what we did with that car was develop two throttle maps, one was a maximum attack map, which the driver could use if he was stuck in a battle, and then once he was in clear air, he could revert to the lower throttle map in order to make sure that he wasn't going to end up breaking out and getting penalised. |
34:03 | The other option as well is if you are looking at a race car that requires a pit lane speed limiter, here in New Zealand the pit lane speed limit is 40 kilometres an hour for the classes I'm involved in. |
34:14 | Normally this is achieved using a fairly harsh and crude ignition cut. |
34:20 | And this can be a little bit harsh on the engine, doesn't sound that pleasant, and the other thing I've noticed is more often than not, the driver will end up going right through to full throttle while on the pit limiter which means that the ECU is doing a lot of ignition cutting, and you end up with a lot of backfiring and popping out the exhaust which isn't exactly pleasant. |
34:43 | So another option is to set up the pit switch to switch to a separate drive by wire throttle table. |
34:49 | Now if we just come back into my laptop screen for a moment, we'll see the sort of setup we could use to achieve that. |
34:56 | Now in this case what we've done is we've set up driven wheel speed on the x axis. |
35:01 | We've got our throttle position or driver's throttle position on the vertical axis, and here what we're doing is basically limiting the throttle opening. |
35:11 | So even when the driver's at maximum throttle, the throttle opening will only end up ever reaching 50%, we simply don't need that much throttle when we're heading down pit lane. |
35:20 | And as soon as we get up close to the 40 kilometre an hour limit the throttle is rolled off quite dramatically. |
35:27 | So this gives a nice smooth and quiet way of controlling the pit lane speed. |
35:34 | Of course there are other options as well for using drive by wire throttle body as part of a launch control strategy. |
35:41 | So quite often in a powerful car, we won't need maximum throttle opening for getting a good consistent launch, but it's very difficult for the driver to consistently open the foot pedal to a specific value. |
35:55 | So much easier to use the ECU to do all of that for us. |
35:58 | So the driver can go to full throttle, knows he's always gonna be at exactly the same point on the throttle pedal every launch, and we can artificially limit the throttle opening during the launch strategy via the ECU. |
36:10 | Of course there are also motorsport functions for aspects such as throttle blipping for downshifting with sequential gearboxes et cetera. |
36:20 | Now the other thing that I should've mentioned there as well or that I can mention there as well, is you see quite often in a factory application, the throttle target table will tend to roll off as we come up towards the rev limiter. |
36:36 | So this can be incorporated to help soften the rev limiter and basically bring the engine torque down as we get up towards that rev limiter. |
36:45 | This means that if we do need to still induce a fuel cut or an ignition cut for rev limiting, it's not going to be needing to reduce as much engine torque or engine power in order to achieve that. |
36:57 | So hopefully that's given you some insight into some of the aspects of drive by wire throttle control and also some of the reasons why I'm personally a really big fan of drive by wire throttle bodies, even in our aftermarket ECU applications where we can use them for some pretty big advantages. |
37:17 | I'll jump into some questions now, I see we've got a few, if you do have any more, please ask them now and I'll do my best to answer them. |
37:26 | Our first question comes from Algier who's asked, can auto blip be used with sequential boxes, also as you only go through the gears by forward and backward motion? Yes auto blip can be used with sequential gear boxes. |
37:39 | In order to do so what you're going to need is a strain gauge gear lever which can indicate to the ECU whether you are trying to upshift or downshift. |
37:50 | Now this is a pretty common modification or common addition I should say, when adding a sequential dog box to a car. |
37:57 | On the upshift this allows the ECU to detect the driver's trying to upshift and incorporate an ignition cut to allow the next gear to be selected. |
38:06 | On the downshift the throttle body can then be blipped to match revs on the downshift. |
38:12 | Now that's actually a really important aspect. |
38:16 | We quite often post about this and also paddle shift and we quite often get people complaining about the fact that a good driver should be able to do all of this and of course that's right, we see some really good drivers who will be blipping the throttle manually to match revs as they downshift. |
38:35 | And we've also looked at data, even from a professional race driver, which shows that as the driver rolls his heel across to blip the throttle to match revs on the downshift, even the best drivers in the world will still end up reducing their brake pressure. |
38:53 | So essentially what I'm saying there is it's impossible for even the best drivers in the world to maintain perfect brake modulation while blipping the throttle to match revs on the downshift. |
39:03 | So if we can have the ECU do all of that for us, it's going to mean that the driver can concentrate solely on braking and this can allow braking distances to be reduced so really important there. |
39:16 | Orlando has asked is it worth using drive by wire throttle control on a drag car with a clutchless box? Look on a drag application it probably isn't. |
39:27 | And what we find, at least the rules that I've dealt with under both New Zealand and Australian drag racing, drive by wire throttle bodies are not legal unless they came out as a factory fitted option for your particular engine. |
39:43 | So when we start getting to the upper eschelons of drag racing where you're looking at purpose built drag engines, two frame drag cars, drive by wire throttle body's generally illegal. |
39:53 | Personally I think that's probably just an indication that maybe they haven't kept up with the times, but the other reality is the advantages for pure drag racing are probably a little bit negligible compared to what we've talked about so far today. |
40:10 | Algier has asked which popular aftermarket ECUs do you know that can use drive by wire and auto blip? I know the Haltech Elite 2500 has drive by wire but no auto blip. |
40:21 | Look I probably couldn't give you an exhaustive list sorry off my head. |
40:26 | I know obviously our G4 Plus that we've looked at here does, the other ECUs that we use here include the Motec M1, that'll also definitely do it. |
40:36 | I would suggest getting in touch with the ECU manufacturer that you're looking at purchasing from and discussing your requirements with them. |
40:45 | It's certainly a relatively common software option on a lot of the higher end aftermarket ECUs. |
40:54 | Cipher Mick has asked, would you say that realistically using the throttle to control torque is really more of a last ditch effort. |
41:01 | Seems like reducing ignition timing and or fuel would be faster. |
41:05 | OK so we're talking about two different things there. |
41:09 | If we looked at that little demonstration that I did there where I went from wide open throttle, 425 newton-metres to 50% foot pedal position, 50% throttle pedal position and we'd only dropped 25 newton-metres. |
41:24 | Now that's not a big reduction in our torque and we certainly wouldn't want to be trying to make that sort of reduction in torque via ignition retard for example, we're gonna be needing to reduce the ignition timing massively and that's gonna be really detrimental to the engine performance. |
41:42 | We're gonna end up with a huge amount of heat being produced and it's also not gonna be a very efficient way of operating the engine. |
41:48 | So this isn't a last ditch effort. |
41:52 | And what we'll even find though is with the way a cable throttle body is designed, the way the bell crank mechanism operates the throttle body is some of this non linearity that we've been talking about today, is already built in to a cable throttle body system, so these do not operate at a 1:1 relationship between foot position and throttle body position anyway, but of course it's a mechanically actuated system and we have no way of controlling it with drive by wire throttle, we've got infinite control at our fingertips. |
42:25 | Cipher Mick's also said it seems like a great use of a drive by wire throttle would be an anti lag strategy since it would effectively replace the kicker. |
42:31 | Yeah actually that's a perfect solution there and that's probably one of the ones I should have been talking about there in the application. |
42:38 | So yeah that's something that's really revolutionised the ability to have a very very high level of control over your anti lag strategy. |
42:47 | Conventionally in a group end system the throttle body was continually open which makes the car horrible to drive on a touring stage and then there's also throttle kicker systems which don't allow a lot of control over how far open the throttle body is. |
43:02 | In turn how far open the throttle body is will have a large effect over how aggressive the anti lag strategy is. |
43:09 | So if you're using a drive by wire throttle for your anti lag strategy, again you can have multiple throttle maps, in other words multiple throttle openings, so you can have a relatively aggressive or a relatively mundane anti lag strategy that's adjustable at the flick of a switch to suit driver preferences. |
43:33 | Barbernet has asked, any suggestions on tuning out the rev hang in the Subaru Legacy GT? I've tuned plenty of Subarus in my time and off the top of my head I can't think of anything I've struck with a rev hang. |
43:47 | So not too sure that I can offer too much help off the cuff there, it's probably something I need to think about a little bit more. |
43:55 | One thing you do definitely notice with a lot of the Subaru drive by wire throttle body cars is that they do exactly what I was talking about earlier, they close down the throttle table, the throttle target, as you approach the rev limiter, but sorry I can't help you with your specific question. |
44:12 | Cipher Mick's asked, last question, can you see any scenario where you'd use drive by wire throttle for traction control in lieu of timing and fuel cuts? Look it's definitely possible, it's a strategy that I've actually incorporated in our custom firmware in our Motec M1. |
44:29 | I've tested it with limited success so far. |
44:33 | Probably in the main part, it's difficult to get the sort of accurate and fast control over the throttle body position using a traction control strategy, you'd really need to get the best possible traction control. |
44:50 | So I think, all things considered, what I've personally seen and done myself, I think you're going to still find that with traction control, a combination of ignition retard, along with fuel or ignition cutting, does give you much faster and much finer control over the engine torque production like that. |
45:11 | It's not to say it can't be done, just at this point I sort of haven't seen an advantage from trying to do it and probably opens yourself up for more problems than it potentially solves. |
45:24 | Craig has asked, does Link control other manufacturer pedal sets? Yeah look I mean essentially the throttle bodies and the pedal mechanisms are all very very common, very very similar I should say, so it's really just a case of finding the pin out for your particular pedal assembly or throttle body assembly, again Link are helpful with most of the common stuff there anyway, providing these pin outs. |
45:50 | And yeah it's usable with just about any system, I haven't come across anything we couldn't use it with. |
45:58 | Willock has asked, how would this strategy apply when in a turbo charged car, where the torque does not come on linearly like NA motors would? OK so that still really works in a pretty similar way. |
46:09 | So we've still got that same scenario where the air flow through the throttle body is not linear in regards to air flow versus throttle position. |
46:17 | As you've mention though with a boosted car, turbo charged car, we also have a scenario where, particularly when you first go to full throttle, we can instantaneously have almost not boost, and then as the engine comes up on boost we have that in rush of torque. |
46:32 | So exactly the same strategy that I've already talked about here in our naturally aspirated application, I'd still be applying exactly that same strategy in a turbo charged application. |
46:42 | In a turbo charged application though, the other aspect that I also like to incorporate is a three dimensional boost control table where our boost target is relative to throttle position. |
46:54 | So what we can find in a turbo charged engine is that often we can get exactly the same boost pressure at 100% throttle and maybe then we would back off the throttle, we can still see that same boost pressure all the way down to maybe 50% or 60% throttle. |
47:09 | So again just like the throttle position, the air flow through that, this provides sort of a non linearity between our throttle pedal and the engine torque. |
47:18 | So by incorporating a 3D table for our boost targets, our boost control, and reducing that boost as we close the throttle, this can help. |
47:32 | We've got a question here from Michael who's asked, would it be a good application in circuit racing to limit power on a wet track with throttle body limiting? I think Andy's also asked a similar question there, or rain versus dry racing. |
47:46 | So yeah absolutely I think I've probably touched on that with one of my applications but yeah absolutely, it's a really useful advantage there, is being able to reduce the ultimate throttle opening if you have got a wet track setting. |
47:59 | And I think this sort of comes down to, obviously there's still an element of driver control, but if for example with, the car can only put maybe 350 or 400 newton-metres of torque to the track at a particular point, then it's useful if we can limit the ultimate amount of torque to somewhere pretty close to that point. |
48:22 | If we are starting out with 600 newton-metres, we've got so much more torque than the car can put to the track, that it's gonna be really a big struggle, the driver's gonna have to do a lot of work in order to control traction, and when the driver's really struggling to control traction, then that takes their mind off the other aspects of controlling the car. |
48:42 | So if we can match the engine torque to what we can actually put to the track as closely as we can, essentially reduce the amount of traction problems we've got then the car's gonna be easier to drive and generally that's going to result in it being faster. |
48:59 | Motoraya's asked can you set boost control duty cycle to times by pedal position and what advantage would that be over traditional boost control strategies of gear versus speed? Yeah I think that really comes back to my answer there to Warlock's question and absolutely it's a very important aspect that a lot of tuners overlook. |
49:16 | And it really, particularly in a light two wheel drive car with a reasonable amount of power, just incorporating a boost control versus throttle position strategy can really transform the ability of that car to make its way around the track fast and in control. |
49:35 | Python has asked, you mentioned a launch control, I know IHRA banned non OEM fitted fly by wire for drag racing, are you aware of other limitations for motorsport use? OK so I've touched on the drag racing thing and yes fly by wire or drive by wire throttle is generally banned as I've mentioned unless it's an OE application. |
49:55 | Traction control or launch control in most forms of motorsport outside of drag racing seems to be a free for all. |
50:03 | I can't say that with authority in absolutely every aspect so definitely check with your governing body and make sure that they don't have any rules that you're about to go and break. |
50:13 | But drag racing is probably one of the very specific niches where traction control and launch control strategies are a little bit more limited often, though we still see plenty of ways that manufacturers and tuners are getting around that anyway. |
50:29 | Steve has asked, you touched on lag from the earlier model drive by wire cars, is this something that can generally be tuned out, or a physical limitation of the throttle. |
50:38 | As an example of this is late 2000s Subaru. |
50:41 | Look the only one that I can think of that really did seem to be maybe a mechanical limitation of the system as much as anything was some of the earlier Ford, these are a Australian domestic market model product, the Ford BA Falcon. |
50:58 | Those tended to be really horribly laggy. |
51:01 | I've also actually used a late model Ford Racing throttle body which we really struggle to get good control over as well. |
51:10 | It just seemed to really struggle to get accurate repeatable throttle position. |
51:16 | But most of the scenario that I was talking about there seems to be more to do with the OE tuning strategy as opposed to mechanical limitations in the system itself. |
51:27 | So particularly a late 2000s Subaru you should have no issue getting good control over. |
51:34 | Oloaf has asked, is it possible to use drive by wire to control cruise control? Yeah absolutely, you'll see that's exactly how OEs do it on late model cars. |
51:43 | Our Toyota 86 running the Motec M150 ECU runs cruise control using the drive by wire throttle, so yeah absolutely it can. |
51:52 | Andy's asked have you done drive by wire mapping utilising GPS location on the track? No I mean GPS fencing on a racetrack is a strategy that I still don't think there's lot of people using, certainly we have the ability if we wanna program it using a development license in our Motec M150, I know having spoken to Scott Kuna, who's the developer of MTron, that's something he was using in a few of the cars that he tunes at World Time Attack. |
52:23 | Certainly I wouldn't say that it's a common strategy, but certainly it is a possibility. |
52:30 | Adds another huge element of complexity in there though and gives you another big element to end up getting wrong and maybe making the car worse rather than better. |
52:41 | Alright guys that's taken us to the end of our questions there so some great questions, hopefully everyone's learned a little bit more, got a little bit more insight into drive by wire throttle. |
52:52 | Hopefully I've also maybe blown away a few of those myths and misconceptions that maybe a few of you have had. |
52:58 | As always for HPA members, if you do have any further questions on this webinar, please ask those in the forum and I'll be happy to answer them there. |
53:08 | Thanks guys for joining us and I'll see you all next time. |
53:11 | Now for those of you who are watching on Facebook, this is just a little bit of insight into what we run every week for our High Performance Academy gold members. |
53:21 | For our High Performance Academy gold members, they can rewatch these webinars in our archive where we've got over 150 hours in existing webinar content. |
53:29 | Also get access to our private member's only forum. |
53:33 | If you are interested in becoming a High Performance Academy gold member, this is available for USD$19 a month. |
53:40 | Or you also get three months of free gold membership with the purchase of any of our courses. |
53:46 | So I'll get the guys to put a link into the comments there that you can follow if you want to learn a little bit more. |
53:52 | Thanks again and I'll see you next week. |
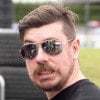