157 | Understanding Direct Injector (DI) Timing
Summary
Timing the injection event in relation to the location in the engine cycle is critical to the performance of a direct injected engine and there are some important considerations for DI engines that aren’t applicable to port injected engines. In this webinar we’ll discuss what you need to understand and demonstrate the effect of DI injection timing using our Toyota 86 with a MoTeC M150 ECU.
00:00 | - It's Andre from the High Performance Academy, welcome along to this webinar where we're going to be investigating the effect of injection timing or fuel injection timing on a direct injected engine. |
00:11 | We're seeing that these days, more and more of the engines that we are dealing with in the aftermarket are now equipped with direct injection, it is definitely becoming a trend that all of the manufacturers are going towards. |
00:23 | So particularly for tuners who have maybe been more familiar with dealing with port injected engines, you're at some point probably going to need to start learning about direct injection technology, and while there is a lot to do with direct injection, it's quite a complex subject, today we're going to focus on just one small aspect of that which is the injection timing. |
00:47 | In other words what we're talking about here is where abouts in the engine cycle the fuel injection event occurs. |
00:54 | Now with a conventional port injected engine, we don't have too much limitation here, we've essentially got complete freedom because we can inject fuel throughout the entire engine cycle. |
01:07 | What's obviously going to happen is that during the intake stroke the intake valve is open. |
01:12 | This is the only time clearly with a port injected engine where the fuel and air is actually going to be drawn into the cylinder. |
01:20 | However what we can do is continue to inject fuel against the closed intake valve during the rest of the stroke. |
01:29 | So the compression stroke, the power stroke, and the exhaust stroke, and then that fuel is going to be basically in that port, against that intake valve when the next intake event occurs, and it's going to be drawn into the cylinder. |
01:42 | So it's not uncommon to see injection duty cycle in the region of 85% to 95%. |
01:50 | Certainly we could run, although it's not recommended, 100% injector duty cycle, where the injector literally is just open all of the time. |
02:00 | So that's what's happening there. |
02:02 | And it gives a lot more freedom with us in terms of getting the fuel into the cylinder, or where exactly we're going to be injecting the fuel. |
02:12 | One of the common misconceptions or myths that I hear is that with a port injected engine, we can only inject during the intake stroke when the intake valve is open and that just isn't the case at all. |
02:26 | That would ultimately limit us to only about a quarter of, or actually it's a little bit more than a quarter of our engine cycle, our intake valve opens before the start of the intake stroke and it closes a little bit after. |
02:40 | So we might be limited to somewhere around about 30% injector duty cycle, and clearly even with OE cars, we're seeing much more injector duty cycle than that. |
02:50 | So with direct injection, it's quite different. |
02:52 | The direct injector is fitted, as its name implies, straight into the cylinder, straight into the combustion chamber, so it's injecting fuel directly into the combustion chamber. |
03:03 | So what this means is there is a much bigger limitation on when we can inject the fuel into the engine. |
03:11 | This means that we're only really able to inject the fuel during the intake stroke, and part of the compression stroke. |
03:20 | So the injection event does need to be complete before the ignition event occurs. |
03:26 | We're not going to want to be injecting fuel after the combustion even has already begun. |
03:31 | So of course depending on our actual ignition timing, this probably gives us a window of somewhere in the region of 300, maybe 320 degrees of the engine cycle where we can inject fuel. |
03:45 | Remembering again, subtle but important aspect with the engine operation, a four stroke engine, there are 720 degrees of crankshaft rotation to one full engine cycle. |
03:58 | In other words the crankshaft has to rotate twice for one full engine cycle. |
04:02 | So this give us a little bit less than half of the entire engine cycle where we are able to actually inject fuel. |
04:13 | So again, particularly for someone who's come from a port injection tuning background, there are some really important aspects that we need to watch when it comes to tuning these DI engines or direct injected engines. |
04:25 | One of the things is it's really important for you to keep an eye on your injector duty cycle. |
04:32 | Now we also need to understand how the injector duty cycle is calculated. |
04:38 | This does vary a little bit from ECU manufacturer to ECU manufacturer. |
04:44 | We're seeing now, a lot of aftermarket ECUs with direct injection support, of course there are also options where we may be reflashing a factory ECU. |
04:54 | So normally what we're going to find is that there is some limit point that limits the injection event, so limits the point where we have to actually stop the fuel injection event. |
05:07 | So for example we might want to limit it to somewhere around about 30 or 40 degrees prior to the most advanced ignition point that we're likely to use. |
05:18 | Another way of doing this, this came up with a Syvecs ECU that we were recently tuning. |
05:23 | Syvecs use a different technique where they're taking the full intake stroke and the full compression stroke and then for the limit you can specify a percentage of that entire 360 degrees. |
05:35 | So a little bit different there. |
05:37 | If you're doing it that way, with a Syvecs you do also need to be mindful of the actual ignition timing is going to affect that. |
05:44 | So in other words if we're talking about the ignition timing that we might look at use at light load, we might be using 35, 40 degrees, or even more. |
05:53 | When we're at wide open throttle we're likely to be much more retarded than that, so we need to account for that when we're choosing our limit point. |
06:02 | The other aspect here is that we're looking at the start of injection point to calculate our duty cycle. |
06:09 | So in other words in the ECU here that we're going to be using for our demonstration, the Motec M1, what the ECU does is it looks at the point that we've selected for our start of injection, and it looks at our limit point that we've set in the ECU, and then what it does is it decides how much of that available engine cycle we are using for our injection event. |
06:31 | So again because we are very limited in the sort of duty cycle's we're able to use in a DI engine, just as a rough guide to the sort of pulse widths, injector pulse widths that we may like to see or like to use, if we're operating an engine at 7000 RPM wide open throttle, full power, we're probably going to want to limit our injector pulse width to somewhere in the region of about seven milliseconds maximum. |
07:01 | So again much shorter than what we're likely to see in a port injected engine. |
07:08 | Alright just to give you a bit of an idea of how this all works, let's head across to my laptop screen, and what I wanna do is just give you a bit of a run through on this on the Motec ECU. |
07:21 | So we've got our engine running at the moment, and we're on our fuel timing worksheet. |
07:26 | The FA20 engine is unique in so much as it includes both port and direct injectors. |
07:34 | So that we can just concentrate on the DI aspect today, I've completely disabled the port injection. |
07:42 | So we're only running on our direct injection. |
07:44 | So this is our timing limits here. |
07:48 | So for a start what we've got is our fuel timing primary. |
07:52 | So let's just full screen that. |
07:54 | So what we've got here is a two dimensional table of our injection timing versus our engine RPM. |
08:01 | At this point for our webinar I've just set this up as a simple two dimensional table. |
08:07 | If we press A for the axis setup, what we also can choose is to add a second axis, in this case we've got the ability to add a throttle position axis so that we can get a little bit more involved with our direct injection tuning, and we can vary the direct injection point, the timing point based on both throttle position and engine RPM. |
08:28 | We've also got this two dimensional table displayed graphically over to the right. |
08:33 | So you can see that for most of this table, I've got it set really basic at the moment. |
08:37 | We've got 320 degrees and then right at very high RPM, we ramp up to 375 degrees. |
08:45 | So it's important to first of all understand what these numbers mean. |
08:49 | So what we're talking here is start of injection. |
08:52 | So that's again something that's a little bit different to how we'd normally describe port injection. |
08:58 | I'll deal with that in a bit more detail soon. |
09:00 | And we're talking about that versus the point at the top of the compression stroke. |
09:07 | So in this instance for example, at 3000 RPM we are starting our injection pulse, 320 degrees of crankshaft rotation before top dead centre on the compression stroke. |
09:21 | So what this really means is if we had 360 in there, we would be right at the very beginning of our inlet stroke as the piston is beginning to come down the bore. |
09:31 | OK so we've also got a fuel timing primary limit. |
09:36 | So again I've set this up very simple at the moment, this is just a single value. |
09:41 | So this will basically cut off the injection event, if it calculates that the injection event is going to continue past 60 degrees before top dead centre. |
09:53 | Now while it might seem like a good idea to be able to inject right up to the point where our ignition event occurs, in reality we find that if we get too close to the actual ignition event, this actually results in the engine running very poorly. |
10:09 | We get poor combustion. |
10:11 | So we do want to be quite conservative here. |
10:14 | Obviously every engine is going to be different. |
10:17 | The remaining parameters that we've got here are not going to be of interest to us at the moment. |
10:23 | These are to do with the secondary injection, which is the port injection system on the FA20 so we're going to ignore that for the purposes of today's demonstration. |
10:34 | OK so that's just really what it looks like there in our Motec M1 software. |
10:40 | Of course it's going to look a little bit different in every software. |
10:44 | But what we're talking about here, the actual principals to those fundamentals behind the tuning or the calibration of our injection timing are going to remain the same regardless whether we're tuning Motec, Syvecs, or we're reflashing a factory ECU. |
10:59 | OK so it is also important, because a lot of ECUs won't easily display aspects like injector duty cycle for our direct injectors. |
11:09 | And we may not necessarily have a really clear idea of what's going on. |
11:15 | So it's really good if we can understand how to calculate this for ourselves. |
11:20 | So I'm just going to go through that process now. |
11:23 | And really what we're going to be talking about here is just some really basic math that comes from our EFI tuning fundamentals course. |
11:35 | So what I'll do is I'll follow this through if I can on our calculator here. |
11:40 | So let's just head back across to my laptop screen. |
11:44 | One of the key things here, and this is a really really good equation, just to always have in the back of your mind to understand that if you want to calculate how long the engine cycle time takes at a particular RPM, we can really easily do that in just one single step. |
12:02 | What we want to do is divide 120 by the engine RPM. |
12:07 | So if for example we wanted to find out what the cycle time was at 6000 RPM, what we could do there is we could enter 120 divided by 6000, and we'd see that that takes 0.02 of a second, or in other words we're generally going to be talking in milliseconds, we're talking there that it takes 20 milliseconds. |
12:28 | OK so another subtle aspect, I've already mentioned this but I'll reiterate, we need to remember that there are 720 degrees in one engine cycle. |
12:37 | OK so what we could do is go one step further, if we divide our 720 by 20, just going to talk here in milliseconds and represent it like this, what this means is that for every millisecond, the crankshaft is going to rotate 36 degrees. |
12:56 | So now that we understand this, and this is just how we would work if we're looking at one of our logs and we maybe didn't have injector duty cycle, maybe our ECU isn't able to display for us end of injection, what we would do is be able to calculate this. |
13:11 | So let's take an example where we know that our start of injection point is 360 degrees. |
13:16 | And we're using an injector pulse width of 8.5 milliseconds. |
13:20 | So what we can do is we can calculate how long the injection event lasts. |
13:25 | So we know that each millisecond the crankshaft's going to rotate 36 degrees. |
13:30 | So if we now multiply this by the length of our injection event, 8.5 milliseconds, what we're going to find is that that now takes 306 degrees of crankshaft rotation. |
13:43 | So to find out where our injection event is finishing, if we take our start point, 360, and we subtract the length of our injection event, 306, we're going to find that our injection event's going to finish around 54 degrees before top dead centre. |
13:59 | That's probably going to be pretty marginal, so this is why I suggested, we did talk about 7000 RPM, but 8.5 milliseconds probably a little bit long in terms of our injection time. |
14:13 | OK so now that we've got that, again even if you're not talking about DI, that's a really nice sanity check if you're just trying to figure out what's going on in your engine and you want to understand how long you have available to inject fuel, or for that matter for anything to occur, 120 divided by our engine RPM is going to give you your cycle time in milliseconds. |
14:37 | Or actually in seconds, you can convert to milliseconds of course. |
14:41 | OK so let's talk about our injection strategy. |
14:43 | So if we inject our fuel too late in the engine cycle, we know that we're going to start interfering potentially with our combustion event, and we're going to end up with unstable combustion, the engine's not gonna run very well, and it's going to make it really apparent when you've gone too far, you're going to find that the torque will drop and you're going to find that the engine just runs very very roughly. |
15:09 | On the other hand if we inject our fuel too early, what we're going to be doing, once we go past 360 degrees, essentially we start injecting the fuel while the exhaust stroke is still completing. |
15:21 | So obviously that's not particularly smart. |
15:24 | We get into a situation which we can't achieve in a port injected engine, we get into a situation where we're literally just pumping the fuel straight out the exhaust. |
15:33 | Now that might sound really stupid and it might sound really obvious but I'll just actually explain a situation that I found myself in right at the very start of our FA20 development. |
15:44 | At that point we were still running on a very early version of the Motec M1 package for the Toyota 86. |
15:51 | And at that point we had our fuel injection, our direct injection timing event configured on the basis of end of injection. |
16:01 | Now the reason this was done is because this is how we normally talk about injection timing with port injection. |
16:09 | So we just basically copied that same philosophy across to our direct injection. |
16:15 | So we really knew clearly exactly where the injection event was ending. |
16:19 | But of course without the ability to automatically see what the start of injection point was, as you increase the injection time, the injection pulse width, the start of injection event starts coming earlier and earlier, and we got to a point on the dyno where we were injecting more and more fuel and of course we weren't seeing any improvement. |
16:39 | And we got to a point where once I actually did the calculations we were injecting a reasonably considerable way into the exhaust stroke. |
16:45 | So again should be pretty clear, but sometimes maybe not as clear as you'd think. |
16:50 | Definitely not the best way to get good fuel ecomony or good emissions I can guarantee you that much. |
16:56 | So yeah it is important to understand, again if you're coming from a port injection background, that when we are talking about the injection timing events for DI we're going to be talking in terms of start of injection. |
17:11 | We don't always need to use end of injection for port injection. |
17:14 | Certainly systems do allow that to be changed to start of injection or even centre of injection, but in my own experience, end of injection is easily the most common for port injection systems. |
17:28 | So with the DI system, obviously because we have such a small window to inject the fuel, this is one of the reasons why we also use very high fuel pressure. |
17:40 | The other of course is because we are injecting against the higher cylinder pressures we're gonna see as we move through the compression cycle. |
17:48 | But of course as we take a factory direct injection engine and we start improving the power, maybe we increase the boost pressure, maybe we add a freer flowing exhaust system, and improve the efficiency of the engine, we're going to need more fuel to match the extra air flow, and of course as we do this our injector pulse width naturally is going to expand. |
18:10 | So we can combat that, if we're dealing with a factory direct injected engine to a degree, by increasing the fuel pressure target as well when we're under high load. |
18:20 | Of course there are also limits on how far you can go with that. |
18:25 | OK we're going to go through a bit of a demonstration here now. |
18:29 | And we're going to use the torque optimisation function on our Mainline dyno to see how we can tune or optimise the direct injection fuel timing. |
18:39 | After this we're going to move into some questions and answers so if you do have anything that you would like me to explain in more detail, or anything related to the webinar in general, direct injection timing in general, please ask those in the comments and the chat and I'll deal with those shortly. |
18:55 | Now one of the first points when it comes to selecting our direct injection timing, obviously it's nice if we have something to base our timing on. |
19:05 | In a lot of instances we can reverse engineer the factory injection timing map. |
19:13 | So if we can head across to my laptop screen for a moment we've got the factory ROM file here from the Subaru FA20 engine, the Toyota 86, same thing. |
19:26 | And this is our direct injection, our base factory direct injection timing map. |
19:31 | So what we can see here is we've got on our x axis, we've got our engine load. |
19:36 | Now because this is a MAF based tune, we are looking at load in grams per revolution. |
19:44 | Essentially still the same thing regardless, where as we move to the right of this table, we're increasing our load, we're increasing our airflow. |
19:52 | Then on our vertical axis on the left hand side, we've got our engine RPM. |
19:57 | So the interesting thing is if we look in the sort of general idle cruise areas, we are injecting around 320 degrees before top dead centre. |
20:06 | You can see however that right at very high RPM and high load, the injection timing event is actually being brought forward and it's injecting prior to reaching top dead centre. |
20:19 | Now again this gets us into that weird spot where we're technically beginning the injection event prior to the piston reaching top dead centre. |
20:29 | So a little bit into the exhaust stroke. |
20:31 | Now I've actually tested this backwards and forwards on a couple of cars on both Motec and Syvecs as well as also the factory calibration via EcuTek and we find that we do actually get advantage from advancing the timing there around 370, 375 even I think I'm using in the Motec, and that doesn't make a lot of sense. |
20:54 | Obviously we don't wanna be injecting fuel out the exhaust. |
20:56 | So my understanding of this is that the timing event here doesn't actually account for the injector dead time. |
21:05 | So this timing event is the pulse width being supplied from the computer to the injector. |
21:11 | And obviously even with a direct injector we still have some latency in the injector actually opening, and what we'd actually find is that up at very high RPM, around 7000 RPM, the latency has the injection event delayed to the point where we've gone past top dead centre. |
21:30 | The other point here if we can just have a look at this piston, the piston design for a direct injected engine also has a big influence on the way the fuel and air mixture is distributed through the combustion chamber and we can see that we have a pocket or a fan pocket cut into the top of the piston to help direct the fuel flow. |
21:53 | What we find is that in the FA20 combustion chamber, the direct injector is located over on the left hand side, right hand side of your screen I guess, and it just sprays the fuel essentially into that pocket when the piston is near to top dead centre. |
22:07 | So of course we need to take this into account because this is going to have little to no effect once the piston has moved past top dead centre. |
22:17 | So always a great idea if you can get hold of a base calibration for your stock engine and see what those OE manufacturers were doing with the injection timing. |
22:29 | This is obviously going to be a really good guide to start you with your tuning. |
22:33 | You know you're going to have safe numbers. |
22:34 | But of course we also need to understand that the OE's techniques or requirements might be very different from ours. |
22:42 | The OE's always are going to be much more interested in the emissions than they are on power and torque. |
22:49 | So as long as we aren't required to meet emissions then we can choose to optimise our injection timing to give us peak torque. |
23:00 | Alright so what we're going to do here is we're going to set up a torque optimisation test on our Mainline dyno. |
23:06 | And I'll just explain what's going on on that test. |
23:11 | Just bring that up on our screen. |
23:14 | OK so what we've got on the vertical axis here, we've got our torque being registered from our Mainline dyno. |
23:21 | On the horizontal axis at this point I'm now looking at fuel timing from our ECU. |
23:26 | So we have a CAN communications network going between our Motec M1 and our Mainline dyno so that the Mainline dyno can see exactly what our injection timing is. |
23:38 | We can see right now that's sitting at 320 degrees. |
23:42 | Let's just show you how that changes. |
23:44 | I'll just jump into our software, let's set that to 280, and we'll see that that changes in our Mainline dyno. |
23:51 | So what I'm going to do is I'm going to get our car up and running, and we're going to go to 3000 RPM in fourth gear. |
24:00 | And what I'm going to do is try and hold my throttle position relatively fixed. |
24:06 | And we're going to, let's try and bring our set point back down to 3000 RPM. |
24:17 | What we're going to do is initially I'm going to advance the injection timing event up to 360 degrees. |
24:26 | And then I'm going to start our test and I'm going to bring our injection timing all the way back down until probably around about 200 degrees. |
24:38 | We might actually not need to go that far. |
24:40 | It's probably going to be pretty apparent what's going on at that point. |
24:44 | The other thing, while I'm doing this test we'll have a look at the data once the test is completed. |
24:48 | We are also logging the closed loop fuel trim. |
24:53 | So the closed loop fuel trims are going to constantly keep us at our target of lambda one. |
24:58 | But they're also going to give us some really good insight into what's going on with our injection timing once the test is completed. |
25:06 | Alright so everything's pretty stable, I'm just going to hold our load at around about 60 kPa here. |
25:12 | Just clear everything there and start our test. |
25:16 | OK so what I'm going to do now is just try and hold our load, our manifold pressure really constant and you'll be able to see a red line being drawn there on our dyno. |
25:28 | And we're going to just do this as smoothly as we can. |
25:34 | Obviously we're seeing some bumps in our torque as well which is pretty typical with this sort of test. |
25:41 | This hopefully is gonna be a pretty quick test that's going to at least show you a generalised idea of what we can expect to see as we vary our injection timing. |
25:52 | So coming down past 290, 280 degrees now. |
25:57 | And we can see that we've gone past a torque peak, and our torque is actually dropping away now, so obviously not ideal if we are aiming in fact for peak torque. |
26:09 | What you'd need to do with this particular graph here is sort of mentally smooth it a little bit. |
26:14 | Obviously it is a little bit erratic and I'm just trying to do a pretty quick and dirty job of showing you what's going on. |
26:21 | Of course if you wanna get a little bit more involved with it you can take your time and go over everything in a little bit more detail. |
26:29 | Right, down to 200 degrees, I'm just gonna back off and we'll have a look at our results. |
26:36 | What we can see is that the dyno is showing us that at that particular load point, we ended up with peak torque at 126 newton metres which was achieved with 312 degrees of injection timing. |
26:54 | So the injection event starting 312 degrees before top dead centre. |
26:58 | Now we do need to sort of be a little mindful here that this is quite an erratic graph and we're seeing relatively consistent torque value through this region of probably about 305 through to maybe about 320, 325. |
27:13 | So we can't try and read into that to an individual 10th of a degree for example, we're probably within five degrees. |
27:20 | But what we do see is a very clear indication that as we bring the timing back towards top dead centre on the compression stroke, we see our torque drop away quite sharply as we got towards 200. |
27:32 | And we also see a really big negative impact on that when we've got the injection event all the way out at 360 degrees before top dead centre. |
27:42 | So of course again as well for those of you who are more familiar with tuning port injected engines, we would not expect to see such a dramatic effect on our torque as we change the injection timing. |
27:54 | In a port injected engine sometimes it can be quite hard to really register a significant enough change to even guide us in the direction we should be going. |
28:04 | With a direct injection engine, it is very very clear, it's very very obvious. |
28:08 | So what we've done there, let's just look at our laptop screen again, we've only concentrated here on our 3000 RPM cell. |
28:17 | We've obviously got a full table here, two dimensional table and of course we could make this a three dimensional table to replicate that factory table that we've already looked at. |
28:29 | Interestingly enough as well, 3000 RPM, we're probably operating somewhere around about this point here, you can see that what we've just registered here on our Mainline dyno basically mirrors exactly what the OE map is. |
28:46 | Probably again not necessarily that surprising. |
28:50 | OK what I wanna do is just bring up our time graph here though and we'll just zoom out of this a little bit. |
28:58 | And I'll just explain what we've got going on on our screen here. |
29:02 | So we've got our RPM up the top, we can see that we're at 3000 RPM. |
29:07 | We've got our manifold pressure. |
29:08 | So for the purposes of this test, I tried to keep it at about 60 kPa. |
29:12 | I've done a pretty good job of that but you can see it does vary up and down a little bit. |
29:16 | This is one of the keys to getting good results from those torque optimisation tests. |
29:20 | If we don't hold our manifold pressure in the same cell very accurately then obviously our engine torque is going to be affected by that. |
29:29 | We've got my throttle position, we've got our exhaust lambda versus our target. |
29:34 | Obviously in closed loop control those are matching exactly as we'd expect. |
29:38 | Here's our more interesting points here, we've got our fuel injection timing. |
29:43 | So we can see at the start of our test, we're at 360 degrees and we've gone all the way down here to 200 degrees. |
29:52 | Ignition timing there fixed at 34 degrees as you can see. |
29:55 | Now the point that I wanted to show you here is our next group down we have our closed loop fuel trim. |
30:03 | So this tells us a lot about what's going on here or where we're getting an advantage from our fuel timing. |
30:10 | So at the start of our test at 360 degrees, hopefully you'll be able to see these numbers. |
30:14 | We've got the closed loop control system pulling out about 5% fuel to get us to our target of lambda one. |
30:21 | What we can see though is as we start bringing our timing back from 360 degrees, so we start retarding our injection timing, we can see that our closed loop trim actually drops. |
30:34 | And we can see that probably around about this point here, probably somewhere around about here, our closed loop trim has now gone from minus 5.2% to minus 3.3% and that also coincides reasonably closely, well we're at 326 degrees but we're pretty close to the point where our MBT test, our torque optimisation test found that our injection timing was optimal. |
31:01 | We can see that our closed loop trim stays reasonably flat around that point and then as we continue to retard our injection timing we see our closed loop trim drops away again. |
31:13 | So this really shows us very clearly, even if we don't have access to a torque value from a dyno, this does give us some direction to head. |
31:25 | It's not gonna be as clear and obvious as the dyno of course but it does give you some indication of where the correct injection timing value was. |
31:35 | OK so moving on from this, we've only looked at tuning one cell, and obviously we've got that two dimensional or potentially three dimensional table. |
31:43 | The ways that we can deal with that, we can continue this exact same process. |
31:48 | So we can essentially steady state tune our injection timing table. |
31:52 | Again as we've just seen our closed loop trim is varying so this becomes an iterative process. |
31:57 | As we adjust our injection timing we're also going to have to go back and adjust our fuel delivery so that we're staying on target. |
32:05 | The closed loop trim that I've just displayed there, it's a bit of a bandaid fix and we don't really want that to be doing very much work, we'd always like our closed loop trims to be very close to zero. |
32:17 | Now at the higher RPM ranges and particularly higher loads you're probably not going to want to tune these cells in steady state. |
32:25 | And really in this instance we can treat this table a little bit like the same process we'd go through if we were tuning ignition timing or maybe cam timing. |
32:34 | We can perform some ramp runs on the dyno with our injection timing fixed and then we can go ahead and add maybe 20 degrees. |
32:43 | We always wanna make a reasonably step initially. |
32:46 | If we're going to only try a five or a two degree change, we're probably unlikely to see the effect of that change, so we can make a change of 20 degrees. |
32:54 | We can do this to our whole table and do another ramp run. |
32:58 | Chances are what you're going to do is quickly see that in some areas that we've gone backwards. |
33:02 | Particularly if you've got this optimised in steady state. |
33:05 | If you make a change from what you've found to be optimal in steady state, chances are you're gonna go backwards in terms of torque and power. |
33:12 | But at higher RPM where we can't tune in steady state you may start to see a direction to continue heading that's going to give you an improvement in torque. |
33:20 | If we see that sort of improvement, what we'd do is simply continue and go in that direction. |
33:24 | Now once we start getting a little bit closer to the point, what we can start doing is fine tuning our injection timing, make smaller changes, in other words I've just suggested you start with 20 degrees and we can start dropping that back down to 10 or even five degrees. |
33:39 | Now the other reason that you'll definitely want your injection timing advanced there at higher RPM under higher load is again just because this is important to give you the biggest window possible in order to get the fuel into the engine. |
33:55 | OK so we'll close everything down there and we'll move into some questions and answers and again if you do have any questions, please ask them in the comments or in the chat. |
34:08 | Tommy Bueno has asked, can an OEM direct injection system support over 40 psi or 2.8 bar of boost? Chances are that no it would not be able to. |
34:23 | This is really one of the limitations we're currently seeing with direct injection engines. |
34:27 | We don't have the support in the aftermarket for larger injectors. |
34:31 | Also larger pumps are really a limited supply. |
34:34 | We are starting to see some manufacturers get on board with this, but certainly it's not as easy as going to any of the dozens of injector suppliers that are out there on the market right now for port injectors and buying a set of 1000 or 1600 or even 2000cc injectors, fitting them to your engine and you're good to go. |
34:54 | So 40 psi in itself is not really an indication of air flow, but if you're talking about a turbo that's gonna support 40 psi I'm going to guess that you're really looking at pushing the boundaries. |
35:07 | So what we're seeing with the limited number of engines out there at the moment that are direct injected that are really being pushed hard, what we're most often seeing is that the direct injection system will be sort of accompanied with an add on aftermarket port injection system. |
35:26 | So it actually brings it into operating very much like our Toyota 86 here. |
35:31 | The FA20 has from factory, both port injectors and direct injectors, best of both worlds, and it gives us incredible flexibility and be able to make a lot of power not being limited by those direct injectors. |
35:42 | A really good example of this is Radium Engineering in the United States, they make a kit for the eco boost engine which basically bolts to the cylinder head, it's essentially like an inlet manifold spacer. |
35:57 | And the inlet manifold bolts back to that spacer, and it has a location for a set of injectors along with a fuel rail et cetera. |
36:06 | Of course you're then going to need an ECU that can control that. |
36:11 | These are becoming more common. |
36:12 | I know that the Syvecs ECU is capable of doing that, as well as the Motec M1 that we're using here can run both port and direct injectors. |
36:22 | There's quite likely to be other models on the market that I'm not aware of as well. |
36:28 | Cypher Mark has asked, can you explain how injector timing affects the amount of ignition timing advance that you're able to run or if it has any effect at all. |
36:37 | OK so yes it does have an effect, and you're probably going to find there's two areas of operation, if I wanna really just break this down into bare bones. |
36:47 | When we're looking at high RPM, high load operation, what you're really going to be needing to do is advance that injection timing so that you physically have a big enough window in order to get the fuel injected. |
37:00 | What can happen, and I cannot really explain in detail the physics behind it but depending on when we are injecting in the engine cycle, this can have an effect on the cooling of the charge, the intake charge. |
37:19 | So heat in the combustion chamber, heat of our inlet charge, is one of the drivers for detonation, so this can affect the amount of ignition timing the engine can make, can take, before the onset of knock. |
37:32 | So it's another parameter that you just really need to test. |
37:35 | But the other aspect of that, I'm not 100% sure which angle you're going with with that question. |
37:40 | The other angle with that though is we obviously need to make sure that our injection event is complete well before we start our ignition event. |
37:52 | Wittlebeast has asked, how do you size the injectors on these motors, online calculators? We like right now Andy, it's really not a big concern because there isn't the availability of aftermarket injectors as I've sort of mentioned earlier. |
38:06 | We just can't go and buy a set of 1500cc injectors for a Subaru FA20. |
38:13 | There are some engines that are being supported, Extreme DI I think might be the company that's on my mind, are producing some injectors that are compatible I think with the VW, Audi group range of vehicles. |
38:26 | It's not something I've personally gone into myself. |
38:30 | One of the difficulties is that in the aftermarket we have very little access to information around the DI injectors. |
38:37 | So for example, getting accurate flow figures, getting latency values, dead time values for DI injectors is just about an impossibility. |
38:48 | Again we're probably in the infancy of the aftermarket support for DI engines so of course over the next five or 10 years as DI engines become the primary engine that we'll be working on, this is all likely to change so I guess the answer there is watch this space. |
39:05 | Alright guys that brings us to the end of the webinar so if anyone does have further questions, please feel free to ask those in our forum and I'll be happy to answer them there. |
39:16 | Thanks for joining us and I'll see you all next week. |
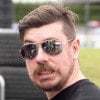