181 | Measuring Thrust Clearance
Summary
One of the clearances inside the engine that’s often overlooked is the thrust clearance for the crankshaft. While the thrust bearings are a little more forgiving when it comes to clearance than the other engine bearings, we still need to confirm that the clearance is correct. In this webinar we’ll see how we can check and measure this clearance.
00:01 | - Hey guys it's Andre from High Performance Academy, welcome along to another webinar. |
00:04 | This time we're going to be looking at our thrust bearings inside our engine, and we're going to be seeing how we can go about measuring our thrust clearance which is another one of those clearances inside the engine that we really need to pay attention to, make sure that we've checked to make sure that it is within our specification during our engine assembly process. |
00:24 | We're also going to be talking about a few of the things that you really wanna watch out for and make sure that you stay on top of to get the best possible results when you're disassembling a used engine and then cleaning it up, refreshing it and putting it back together. |
00:39 | As usual we will be having a question and an answer session at the end of this webinar. |
00:44 | So if there's anything that I talk about today during the webinar that you'd like to know more about, please ask your questions in the comments and I'll get to those at the end. |
00:51 | We will be having a demonstration of the process of measuring our bearing clearance or our thrust bearing clearance here, using our Honda B18C engine which we've got behind us. |
01:01 | So first of all we need to start by talking about what the thrust bearing is. |
01:05 | I think probably most people involved in engine building or with some knowledge of engine building would understand about the main bearings as well as our big end bearings and those clearances understandably are really critical, particularly on the connecting rod, the big end bearings, those clearances are really critical because there is a huge amount of load placed through the connecting rod and we need to maintain a very accurate control of our oil film to ensure that we don't end up with metal to metal contact between the bearing shell and the crankshaft journal. |
01:36 | The thrust bearing is still pretty important though. |
01:39 | The thrust bearing locates the crankshaft longitudinally in the block. |
01:44 | And the reason we need the thrust bearings is that it eliminates any movement fore and aft or longitudinally in the crankshaft either when the engine is running or more importantly particularly with a manual transmission when we engage and disengage the clutch. |
02:03 | Particularly with a push type clutch, when we put our foot on the clutch to disengage the clutch, the thrust bearing presses into the end of the crankshaft essentially and puts a lot of thrust loading through the crankshaft, trying to essentially force the crankshaft through the front of the block. |
02:17 | So the thrust bearing is there to support the crankshaft and prevent any excess movement. |
02:24 | So in most instances the thrust bearings are incredibly reliable and we really don't need to give a lot of though to them. |
02:31 | There are certain engines though where the thrust bearings are known to be reliability problems. |
02:37 | One of the real common ones that I dealt with a lot during my early career was in the Mitsubishi Lancer Evo 1 through to 4 engines. |
02:47 | And these particular engines were known for suffering from what is called crank walk. |
02:53 | And in this instance what happens is that when you're putting your foot on the clutch and the crankshaft is forced into the thrust bearing surface, due to a variety of reasons and primarily a lack of lubrication, basically we end up with the thrust surface on the crankshaft contacting the bearing surface and this results in excessive wear. |
03:14 | And over a relatively short period of time often, this results in excessive thrust movement, so the crankshaft can end up moving backwards and forwards in the block up to a couple of millimetres and obviously that's not going to end well. |
03:27 | So it is something that we do need to pay attention to. |
03:31 | Alright we'll start by looking at a couple of thrust bearing designs, because there are two primary designs. |
03:37 | The first one we've got here is a couple of bearings from our Subaru FA20 here. |
03:43 | So this is a main bearing that also incorporates a one piece thrust washer. |
03:49 | So let's just have a look at this under our overhead camera here. |
03:52 | So we can see that the thrust surface, and where we've got this sitting in the block the crankshaft obviously is located on the main bearing, and these two thrust washers here will locate against the thrust surface on the crankshaft. |
04:08 | So that's one design. |
04:09 | The other way we can often see thrust bearings is with separate thrust washers. |
04:14 | So again we'll have a look at these under our overhead camera. |
04:18 | So these will locate either side of the crankshaft, and these will locate into a specific locating point in the engine block. |
04:26 | So they obviously have to go in the right spot there and we also need to be careful with this style of thrust washer to make sure that we've got the correct face facing outwards. |
04:35 | So in this case we can see that on this face here we've got a couple of little slots here for oil flow. |
04:42 | So this is the surface that actually will run against the crankshaft. |
04:46 | The other surface is the surface that will run against the block, so getting that around the wrong way is going to be a really quick way of destroying your engine. |
04:54 | OK so the first thing I wanna talk about here in terms of fitting and checking our thrust bearing clearance is actually to go back one step and look at a couple of aspects that are really important to deal with when we are disassembling the engine. |
05:09 | And this is something that's really easy to overlook. |
05:11 | Often when we're disassembling the engine we know that we're going to be fitting some aftermarket components, typically that's going to be perhaps conrods and pistons and because a lot of the components such as bearings aren't going to be resused, it's really often that we're going to overlook actually having a careful inspection of these components to check their condition. |
05:31 | And this can end up wasting a lot of time when we come to reassembling and find out that we may have overlooked a potential problem that's lurking inside our engine. |
05:39 | If we continue to overlook that, it can result in a quick failure of our freshly built engine. |
05:44 | Obviously no one wants that to happen. |
05:46 | So the very first thing we want to be looking at is the condition of these thrust bearings when we pull them out. |
05:52 | Obviously we're also going to be inspecting the condition of all of our bearings but the thrust bearing is the one that often is overlooked. |
05:59 | So let's just have a look under our iPhone camera here and we'll locate our used Subaru FA20 thrust bearing and this is the sort of condition that we'll see from a thrust bearing that basically is brand new. |
06:12 | And this is used but despite that, this is on the non loaded side of the thrust bearing. |
06:18 | So we've seen basically no sign of any wear on that bearing, that's in great condition. |
06:23 | Let's flick it over though to the side that is loaded during use. |
06:26 | Actually I'll grab the other one that I haven't drawn all over, probably be a little bit easier. |
06:31 | And we can see there is some slight wear on this side. |
06:34 | Now there's nothing too drastic going on there. |
06:37 | We can't see any major scoring, but this is what we'd be looking for. |
06:41 | If we've got any sign of major scoring on our thrust bearing, that's going to be an indication that we may have a problem with our thrust surface on our crankshaft so we'd want to inspect further. |
06:52 | And we'll also have a quick look at the bearings that we've just pulled out of our Nissan SR20 block that we've disassembled and sent to the engine machinist. |
07:01 | And I'll just try and get a little bit of a better look at these. |
07:04 | And this is a sign of a bearing that is probably pretty close to actually giving us some trouble. |
07:12 | What we're seeing is this copper colour where there is a reasonable amount of wear on the surface of that bearing shell and a good test there as well is if we are seeing something like that we can also run our fingernail across the bearing surface and what we're looking for there is anything that we can really feel, any scoring that we can feel there that would again indicate that we may have some matching damage on the thrust surface of the crankshaft. |
07:38 | So that brings us to our crankshaft, we've got the crank here out of our LS1. |
07:44 | And I'm just gonna set up our camera here so we can get a look at our thrust surface, this probably isn't going to be too pretty unfortunately with the lighting here, I'll just see if I can get a little bit better. |
07:58 | That will probably have to do but I imagine you're going to be able to get the idea here. |
08:03 | So if we swap across to that iPhone camera. |
08:05 | So what we're looking at here is the thrust surface on the crankshaft. |
08:08 | So this surface here is what that thrust bearing is going to run against. |
08:13 | And again this is something that really is easy to overlook. |
08:17 | So particularly in a manual transmission, particularly if it's a push type clutch, it'll be this surface here that is located towards the fly wheel that is going to be loaded when the clutch is disengaged. |
08:29 | Of course if we're talking about a manual transmission with a pull type clutch it would be the opposite side. |
08:34 | So what we're looking for here is any sign that there is scoring or marking on this thrust surface. |
08:41 | Again what we can do is we can run our fingernail across that. |
08:44 | We shouldn't be able to feel any scoring there. |
08:46 | And in really dire situations we'll actually find that there would be a lip towards the outside edge here where the thrust bearing has actually worn into the crankshaft as well. |
08:58 | Now the reason why this is a problem is because if we overlook it, if we don't check that out and notice that we've got a problem there, when we refit the crankshaft with our new bearings, the damage on the thrust surface on the crankshaft is going to quickly destroy our brand new thrust bearings. |
09:16 | So this is why I say it's a good thing to check out early on in the piece. |
09:20 | There are a few problems involved with actually fixing any damage to the crankshaft though and this is going to depend on the particular engine that you're building. |
09:32 | Particularly if you have a one piece main bearing with the thrust washers incorporated. |
09:38 | In order to correct any damage to the crankshaft what you're going to have to do is have your machinist grind and lap that surface on the crankshaft that will run against the thrust bearing and in some instances you will be able to get oversize thrust washers that will go in or an oversize thrust bearing that will go in and allow you to recover that crankshaft. |
10:01 | It is also important to understand though that if you are going to need to grind material off the crankshaft, you're probably going to end up grinding through the surface hardened finish on the crankshaft so this can end up accelerating future wear so that's something to consider. |
10:17 | Often it is a situation where if there is excessive damage on that thrust surface of the crankshaft, often you may be better off actually scrapping that crankshaft and moving to another unit either second hand or another new unit. |
10:34 | Alright so once we've inspected our components we know that we've got components that are reusable, we'll get to the point where we're going through and reassembling the engine, checking our clearance. |
10:45 | So what we need to do here understandably is start by finding out what the clearance for our engine should be. |
10:53 | And this is something we're going to need to know anyway. |
10:55 | I always start by sourcing an engine workshop manual for whatever particular engine I'm working on. |
11:02 | This is going to give us all of the factory specifications and even if we are changing components inside the engine, it's really handy to have all of those factory specifications. |
11:11 | Often we will be still sticking to some of the specifications or clearances or at least basing our new clearances off what the factory recommended anyway. |
11:21 | So in this case we're going to be doing our demonstration on our Honda B18C. |
11:25 | I've got my Honda B18C workshop manual and the specification for our thrust clearance is 0.10 millimetres through to If you work in imperial measurements that's four through to 14 thousandths of an inch. |
11:42 | So straight away you'll notice that the range or tolerance for the thrust bearing oil clearance is much much greater than what we can get away with for our main bearings and our big end bearings. |
11:55 | It's just nowhere near as critical. |
11:58 | So this gives us quite a wide range to be inside. |
12:01 | And generally as a rough rule of thumb, we're likely to find that the thrust oil clearance is going to be somewhere, the factory spec is going to be somewhere in the region of about 10 thou plus or minus maybe five thou. |
12:15 | So once we've got that clearance we need to go and check and see what we've got. |
12:20 | So the process of doing this is to dummy assemble the engine block. |
12:25 | We're going to assemble all of our main bearings, we're going to fit the crankshaft into the block, we're going to make sure obviously we've got our thrust bearings fitted, and then what we're going to do is locate a dial indicator on the front cover of the engine block and we're going to locate that dial indicator onto the snout of the crankshaft. |
12:41 | Now what I might do here is I'll just take our iPhone camera and I'll give you a quick tour of exactly what we've done here. |
12:48 | So I'll just get this into location. |
12:50 | Right let's swap over to that camera because one of the important aspects is locating our magnetic base on the front of the engine. |
12:57 | What we can see here is we've got an aluminium block and I've actually put a steel plate on that aluminium block so I've got something for that magnetic base to actually stick to. |
13:07 | Obviously if you've got a case iron block then that's not gonna be an issue but a lot of our late model blocks now are aluminium. |
13:13 | So it's always handy just to have a bit of a steel plate there that you can just find and empty bolt hole and locate so you've got somewhere to actually put your magnetic base. |
13:21 | The other aspect here is with our dial indicator, we want to make sure that we've got our dial indicator aligned straight parallel to the centreline of our crankshaft. |
13:33 | That's gonna make sure that our measurements are nice and accurate. |
13:35 | Alright we'll get that back into location there now so you'll be able to see a bit more of an overview of what I'm doing. |
13:44 | So once we've got our crankshaft in location and we've got our dial indicator set up and zeroed, what we're going to do is simply take a couple of pri bars, got these here, you can also use a couple of flat blade screwdrivers. |
13:56 | And what we're going to do is just gently pri between the counter weights of the crankshaft and the main bearing caps and we're going to use one at the front and we're going to use one at the back and we're just going to work the crankshaft backwards and forwards in the engine block. |
14:11 | So we'll get those in there now so I'm going to start with one pri bar on the rear main and I'm going to place the other one on our front main. |
14:21 | And we're just going to move the crankshaft backwards and forwards. |
14:24 | So it's pretty easy, you'll feel it clunk backwards and forwards. |
14:28 | So if we swap to our overhead camera, our close up shot, you'll be able to see our dial indicator. |
14:33 | So we need to be reasonably aggressive with this. |
14:37 | So we can see that when I've got a little bit of pressure on this we're right on our zero mark on our dial indicator, this is a metric dial indicator I'll just add as well. |
14:45 | And now if I force the crankshaft back towards the back of the block, we can see that our movement there is about .15 maybe .16 millimetres, so we'll just check that again. |
14:59 | Let's just get that pri bar in there a little bit more accurately. |
15:03 | Alright so we're on our zero mark there, and we'll move the crankshaft back, yeah we're about .16 almost .17 millimetres. |
15:10 | So remembering again that our clearance, our specification here for our B18C was 0.10 to 0.35 millimetres, we know that we're within that specification. |
15:22 | So at this point we're happy to continue with our build. |
15:27 | It really is a fairly straightforward and easy process to go through but again it is something that a lot of engine builders overlook or simply don't bother with. |
15:36 | Now we will be moving into some questions and answers really shortly. |
15:40 | So if you do have any questions, please add those now to the comments. |
15:44 | There is one more aspect that I wanted to add here. |
15:47 | And this goes back to what I was saying at the start of the webinar, one of my early experiences with engines that had known thrust bearing problems was the Mitsubishi 4G63 that came out in the Evo 1 through to 4 shape. |
16:01 | And that used a one piece main bearing incorporating the thrust washers, and it had a full 360 degree thrust washer system. |
16:10 | So essentially when that's all installed in the engine block, looks a little bit like this. |
16:15 | So we've got support from the thrust washers, both above and below. |
16:20 | So in the engine block as well as in the cradle or bearing caps. |
16:24 | Now this actually in itself can create one of the problems that we saw with the 4G63 thrust bearing failures. |
16:33 | The reason for this failure was because there is some flexibility in where we locate the main bearing cap. |
16:41 | Actually I'll just grab the main bearing caps from our B18C here. |
16:44 | It's not quite the same but basically I should be able to replicate the problem that we saw. |
16:50 | So in the 4G63 we have a full main bearing girdle incorporating all five main bearings. |
16:57 | And because of the tolerance with the holes in the cradle versus the studs, what we could do is locate that cradle slightly towards the front of the block or slightly towards the end of the block. |
17:08 | Now what that would do in turn is if I exaggerate it, obviously we want our thrust bearings to be located in the same plane. |
17:16 | But if we don't have the cradle aligned correctly, if I exaggerate it, we end up with a situation where the thrust bearings essentially either sit like this or sit like this. |
17:26 | Now that has two downsides, first of all it's reducing the contact surface between the thrust bearings and the thrust surface on the crankshaft because essentially the crankshaft's only going to be contacting on one half of that thrust bearing. |
17:42 | So that's one problem, it's reducing the load bearing surface, the other issue is when we've got that misalignment, it causes a problem where we're dramatically reducing our thrust clearance so this is one of the reasons that we found the 4G63s ended up with thrust bearing failures. |
17:58 | Now of course if you are checking your thrust clearance as I've just demonstrated you're going to pick that up, you're going to know that you haven't got sufficient thrust clearance. |
18:08 | And a good way that we ended up just aligning the main bearing girdle, is that we would gently pull the main bearing girdle down into the register in the block, using the studs, and we would loosen them all so they're all finger tight and then using a copper mallet we could then tap the crankshaft forward and back and that would just align the thrust bearings so that they were all contacting evenly. |
18:32 | Then you'd tighten the crankshaft girdle down again and finally check our thrust clearance and make sure that that was on spec. |
18:38 | So that's just something to keep in mind if you are building an engine that uses a two piece thrust bearing which is full 360 degree contact, you do need to make sure that you haven't got an alignment problem between the thrust bearing in engine block and the thrust bearing on the cap. |
18:55 | Alright let's head into some questions now and we'll see what we've got. |
18:59 | Craig has asked, if you change to the clutch actuation method would it be a good idea to replace the thrust bearing on the crankshaft? I'm guessing there if you're talking about changing from a push type to a pull type, or probably more likely a pull type to a push type, if that's what you're talking about there Craig actually no that's not too critical. |
19:19 | And the reason for this is if you've got an engine that was running a pull type clutch, the wear will all be on one side of that thrust bearing. |
19:29 | So what you change to a push type clutch, essentially you're starting off with a fresh bearing surface and a fresh thrust bearing surface on the crankshaft. |
19:39 | Of course there will have been some contact but there's never a lot of loading in that particular direction so unlikely to have a big issue there. |
19:48 | Freaks89 has asked, a reputable engine machinist should be able to tell you if the crankshaft thrust surface is too far gone, correct? Yeah absolutely. |
19:56 | I know this might be linked to the quality of workmanship of the engine machinist but is checking thrust play a standard procedure when the machinist goes over your engine. |
20:04 | OK look it should be, you'd like to think that your machinist is going to be thorough and check every specification. |
20:09 | This is where one of the biggest problems I see with engine failures for novice engine builders and home enthusiasts who are piecing together their own engines is that assumptions are made. |
20:21 | What I personally believe is that the buck stops with the person who is assembling the engine. |
20:27 | So if that's you, you've sent all of your parts out to the machine shop, then it's your responsibility to check and make sure that every single component that you are then fitting into that engine is on specification and that you're comfortable and happy with the components that you're fitting. |
20:42 | The reason for this is it's easy for something to get lost in translation, it's easy for your machinist to overlook an instruction and you wanna catch that if that's the case. |
20:52 | Likewise even the best machinists in the world still have a bad day and something might be overlooked or missed out, so we really wanna catch that before it becomes a really expensive problem, and then there's gonna be a whole bunch of finger pointing and blame assigned as to who should be fixing it. |
21:08 | So much easier to catch that before it becomes a problem. |
21:10 | And ultimately when it comes to the thrust bearing surface, it's really easy to pick that up when you're having a casual inspection as you disassemble the engine. |
21:19 | Alright guys that brings us to the end of our questions there. |
21:22 | So if you do have any further questions, please ask those in the forum and I'll be happy to answer them there. |
21:27 | Thanks for joining us and I'll see you all next time. |
21:31 | Now for those who are watching out on YouTube today, this is just a little insight into what we put on every week for our HPA members. |
21:40 | So if you've liked what you've seen today, you can become an HPA gold member, which will give you access to our live weekly webinars. |
21:48 | You'll also be able to rewatch those webinars in our archive where we've currently got over 180 hours of existing webinar content. |
21:55 | And you'll also get access to our private members only forum which is the best place to get fast accurate and reliable answers to your specific engine building questions. |
22:06 | If you wanna become an HPA gold member, it is just USD$19 a month, or you'll get three months of free gold membership with the purchase of any of our courses. |
22:16 | Alright thanks again for joining us guys, I'll see you all next week. |
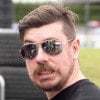