214 | Adjusting Bearing Clearances
Summary
One of the most critical clearances inside any engine is the bearing clearances. When we’re building an engine that’s designed to make more power than stock and rev higher than factory often the stock clearances may not be suitable. In this webinar we’ll discuss our options for making adjustments to the bearing clearances.
00:00 | - Hey guys it's Andre here, welcome to another one of our webinars. |
00:04 | Now today we're going to be talking about the topic of bearing clearance, or more specifically we're going to be talking about what you can do if you find that your bearing clearances aren't quite within your specification. |
00:15 | Now this is a questions we quite often get asked about. |
00:18 | And I know that it is an area for confusion for a lot of novice engine builders. |
00:22 | And it does make it a little bit more difficult because there isn't necessarily just one particular way we need to go about achieving this clearance or adjusting our clearance. |
00:32 | So I want to talk about our options, we're going to talk about the pros and cons of the different options and as usual if you do have any questions, please ask those in the chat and the team will transfer those through to me. |
00:43 | So first of all I think we want to start by talking about what our bearing clearance is, just so we're all on the same page and we know what we're talking about. |
00:50 | And simply put it is the clearance available between the inside of our bearing shell. |
00:57 | So in this case we've got our connecting rod bearing shells here. |
01:00 | These will go in our connecting rod big end and then the difference between that clearance or diameter and the diameter of our big end journal on our crankshaft, of course we've just talked there about our connecting rod, exactly the same thing goes for our main bearings. |
01:15 | The difference between the outside diameter of our crankshaft journal there and the inside diameter of the bearing surface or journal in our engine block. |
01:22 | Now this really needs to be very very carefully controlled and maintained, if we want any chance of getting good service life and reliability out of our engine. |
01:32 | Both clearances that are too tight as well as too loose are going to give us problems. |
01:36 | So the first thing we need to really figure out is what are we aiming for? And in this instance there is a rule of thumb that we can use. |
01:45 | I'm going to talk in imperial terms here, for those who prefer to work in metric, you can convert between the two if we just remember there are 25.4 millimetres in one inch. |
01:55 | But in general terms a good rule of thumb is that our bearing clearance is generally going to end up being somewhere around about one thou per inch of journal diameter. |
02:05 | So what I mean by this is if we've got a 2.5 inch journal diameter on our main bearing, then we would probably expect that our bearing clearance is going to want to be somewhere around about 2.5 thou. |
02:17 | So that's our rule of thumb, this is a pretty good sanity check on where our clearances should be. |
02:23 | Of course the next thing we're going to do is go to our factory workshop manual and check the specific clearance range that the manufacturer dictates. |
02:33 | So there will be a range there with a high limit or an operating limit both high and low and a service limit above which we need to either replace our components or have the components machined. |
02:45 | And you do need to be a little bit careful here, and the reason I say this is I've just given you a rule of thumb and that would be fine for a fairly wide majority of cast iron blocks however particularly the crankshaft that I've got in front of me here, this is out of a Subaru FA20. |
03:02 | The Subaru FA20 uses an alloy block and what we quite often find is that the recommended clearances for an aluminium block on our main bearing journals are quite significantly tighter than what we would specify on a cast block. |
03:16 | Now the reason for this is simply because of the thermal expansion coefficient of alloy versus cast iron, simply the block is going to grow more as it comes up to operating temperature. |
03:28 | So when we're measuring our clearances at room temperature, obviously that's not what we're going to actually have when the engine is out there running at speeed and at operating temperature and that's why we see with our alloy clearances, we want to go a little bit tighter, generally. |
03:43 | So always start with our workshop manual. |
03:45 | And I also just want to talk about the range that we're going to be using. |
03:49 | So of course if you're dealing with a completely bog stock engine, you're not modifying it, and you're just doing a freshen up on it, then unless you've got an engine that is known to have some specific problem with bearing clearances, which these days for a performance engine would be incredibly unlikely, you've really go no reason to deviate from the manufacturer's recommendations and that's probably an absolutely perfect place to be. |
04:15 | However as we start pushing our engines, making more power and also running them to higher RPM, what we find is that the components like our crankshaft, which here at room temperature sitting on our bench, seem really really strong and rigid, likewise our engine block, at higher operating RPM and high power, essentially everything starts moving around and flexing, and it's that flex that can play havoc with our bearing clearances. |
04:45 | I just want to also dispel a myth that the crankshaft journal runs directly on our bearing surface, that's not the case. |
04:54 | In fact we want to avoid that at all cost because if we end up with our crankshaft journal contacting our bearing surface, we're instantly going to end up with damage and that's going to result very quickly in the demise of our engine. |
05:10 | So it's important to understand that the bearing surface and the crankshaft journal are protected from each other by a thin film of oil. |
05:18 | Now the problem is of course when we start getting this flex that I've just mentioned, what we end up with is the potential for that flex to be enough that the journal can break though that oil film and actually contact the bearing surface. |
05:29 | So if you've been following along, what you're probably figuring out there is that for high powered engines where we're deviating a long way from the factory specification, generally we would build the engine with slightly looser tolerances. |
05:44 | Now that just gives a slightly thicker oil film, often this is also coupled with a heavier viscosity oil. |
05:51 | And it just gives a little bit more margin for making sure that we're not going to end up with metal to metal contact. |
05:58 | And at moderate power levels we might just simply aim for the looser side of the factory tolerances, in some instances we'll need to go much further than that. |
06:10 | Alright so we've also, I should mention here, got a webinar in the archive that you can check if you want to see how to actually measure bearing clearances 'cause we're not covering that today. |
06:22 | We've assumed you've already gone through and measured your clearances and you know what they are so we're going to be talking about what to do. |
06:27 | So use the search function in our archive if you want to learn how to measure your clearances. |
06:32 | So there are a number of options here that we're going to go through. |
06:35 | And the first one is that we're going to talk about using graded bearing shells. |
06:41 | And this is quite common with a lot of late model performance engines, particularly a lot of the Japanese performance engines that we deal with. |
06:50 | And what you'll find is that on the crankshaft journals as well as the connecting rods, there will often be a number stamped and essentially it's a way of factory blueprinting it. |
07:00 | What they do is once the components are built or manufactured in the factory, what they'll do is, for example with the journal, they will measure the journal diameter and of course there is a specification above or below which the crankshaft is considered to be no good, it's out of spec and thrown away. |
07:18 | However even within specification there is a range and depending where abouts in the specification range each of the journals on the crankshaft sits, that will be given a number. |
07:29 | So I'll see if I can show you that. |
07:33 | We do have, let's see, yeah let's go to our overhead camera there. |
07:38 | So we've got this information printed here, we can see that we've got ZZZZ and we've got CBBBC. |
07:46 | So this gives us the five clearances for our main journals and the four clearances for our big end journals. |
07:53 | Basically tells us what that crankshaft clearance or specification is for all of those journals. |
08:01 | Now again when we've got exactly the same information from our connecting rod, the big end journals will be measured after the rod is manufactured and honed to a finished size and again even within the specification there'll be a top size and a bottom size for that bore and that will be basically given a number based on what it is. |
08:21 | So with a lot of late model performance engines we have the option then to choose specific bearing shells based on the combination of the crankshaft journal size and for example our rod big end bore and we can choose the correct bearing shells to get the exact specification we want. |
08:40 | And this is kind of a factory blueprinting technique. |
08:43 | So what we'll do is we'll just head across to my laptop screen here. |
08:46 | So this is the exact information you'll find in the factory workshop manual for a Honda K series. |
08:54 | So here we've got our main bearing journal codes. |
08:57 | So this is in the crankshaft and then we've got, sorry this is on the crankshaft. |
09:03 | And then we've got the bore of the engine block, so that's the bore in the engine block that the bearings are going to sit in. |
09:12 | And basically depending on where you are, so if you've got a two or a B or a two depending on how it's marked, in the bore in the block and you've got let's say a number five on your main journal code for your crankshaft, you come across and you see alright well we want to order the brown bearing shells for that particular journal. |
09:33 | So basically you can go through and use that grading chart to choose the correct bearings for each location both in the engine block and the connecting rods. |
09:41 | And that's going to theoretically get you right onto the factory specification for your oil clearance. |
09:49 | There are a couple of caveats that you do need to be aware of with this. |
09:52 | Clearly if these parts are brand new, straight out of the factory box, then we should be able to take notice of these numbers and use that grading grid as expected. |
10:05 | However particularly if we've got a high mileage engine or one with a bit of an unknown origin, maybe it's been rebuilt before and you're really not too sure what's been done, it's not a good idea to make assumptions that the crankshaft and the engine block or the connecting rods are as per manufacturer's specifications. |
10:22 | What you'll find is that in another place in the workshop manual, there will be the diameters or dimensions for all of these components and how those align to those grading numbers so it's always a good idea to actually check and make sure that your crankshaft journal for example does line up as to the stamped number on the crankshaft, so you're actually working in the right direction. |
10:44 | Now that's also going to get you onto the factory recommended clearance. |
10:48 | But of course as I've already mentioned, particularly if we are building an engine which is going to make substantially more power or rev to a higher RPM, we may want to go a little bit looser. |
10:59 | However it's relatively easy to make small adjustments just by adjusting where you're located in that grid. |
11:08 | If you, for example went with a bearing shell that was designed for a tighter bearing bore in the block, that's going to end up giving you a slightly looser clearance so pretty easy to mix and match your bearing shells using that technique to get where you want to go. |
11:29 | However in a lot of instances you're not going to have the benefit of using graded bearing shells like we've just talked about there. |
11:37 | Particularly if you are using an off the shelf aftermarket bearing shell. |
11:42 | So for example here we've got some of our King Racing bearings for our Subaru FA20. |
11:48 | And in this instance they have a standard bearing shell size. |
11:52 | So if you're limited on what's available there, this makes things a little bit difficult. |
11:59 | If you start with your off the shelf bearing sizes for a standard journal, you can then do a dummy assembly, measure and find out where your clearances are. |
12:11 | That's going to give you a pretty good idea of where you are versus the specification you're trying to achieve. |
12:16 | This is where it gets a little bit tricky, what if you aren't on that clearance size? So what you're going to find is now there are a few more options and it really depends what sort of engine you are dealing with. |
12:29 | In some instances, and this seems to be very common with a lot of the US domestic market engines that are popular for modification, small block and big block Chev, Ford, LS et cetera, a lot of the aftermarket bearing shell manufacturers produce a range of bearing shells. |
12:49 | So they may have for example a standard bearing shell, they may have a 10 thou undersize bearing shell and then they'll also bracket that with a nine thou undersize and an 11 thou undersize. |
12:59 | So it gives you the ability to make small adjustments based on what you've actually measured your clearance to be. |
13:07 | So for example if you ended up having your crankshaft ground and don't worry I'm going to talk about this in a second, to 10 thou under, you would expect that you can use an off the shelf set of 10 thou undersize bearings. |
13:21 | However if you then went through and measured and found your clearance was a little bit tight, you could go to a 11 thou undersize bearing shell and that will give you an extra thou of clearance. |
13:32 | So it's kind of a coarse way of making adjustments but it is quite effective. |
13:37 | The other thing with this is if you do have the ability to purchase bearing shells in that sort of range with one thou plus or minus of your target, what you can do, and this is sort of an area that's a little bit unknown, is you can mix and match, so what I mean here is that you could use, if you want to make a half thou change, that gets a little bit tricky, you could use a 10 thou undersize bearing shell on one side and an 11 thou undersize bearing shell on the other side so that would achieve a half thou change. |
14:10 | The recommendation if you are going to be mixing and matching bearing shells like this is that you don't make a change of more than one thou so we wouldn't want to go nine thou on one side and 11 thou, it's only suitable for making very very small changes. |
14:26 | OK the other aspect is if we don't have the flexibility of multiple bearing shells like that, the other option we can do is, particularly if we find that our clearance is too loose. |
14:42 | So let's say we start with a standard crankshaft and we start with our standard bearing shells, we assemble everything up, we're looking for 2.5 thou and we find that our clearance is at 3.5 thou or four thou. |
14:52 | Well it's very difficult to make that smaller. |
14:55 | So the option that we've got there is that we can have the crankshaft journals precision ground to an undersize. |
15:03 | Now that would require us to start by purchasing our undersize bearing shells and generally what we would do is then assemble those into the engine block or the connecting rods and we would measure the bore diameter and basically our engine machinist is going to be performing this because we need some very specialist equipment. |
15:20 | They can then grind the crankshaft journals and they'll grind it to achieve a finished size to get us right onto the clearance that we want. |
15:28 | So this is where you do need to be using a quality machinist, you want to be using someone that is used to working on performance engines because it does require some very very high precision to get that where we need it to be. |
15:41 | So there's the upside there that we can get our clearance just about wherever we want it. |
15:46 | Another upside, particularly if you've got a high mileage crankshaft that's showing a little bit of surface wear, you're going to be grinding through the crankshaft journal, we're going to be getting rid of any surface wear and you're going to have a nice fresh surface to start running on again. |
16:01 | There is a downside with this though in that most production crankshafts are induction hardened, so this is a process that provides a very very hard surface finish and that's right on the crankshaft journal. |
16:14 | And this is good for wear over the lifetime of the crankshaft. |
16:18 | Unfortunately with that induction hardening process the actual hard layer is very very thin so if we're going to be grinding 10 thou off the crankshaft which is five thou per side, generally that's going to grind through the hardening process. |
16:34 | And a lot of people are put off by this thinking that it's going to ruin the crankshaft and there are some pros and cons there. |
16:40 | Obviously it is a way of getting very precise clearances and recovering a crankshaft that would otherwise be unusable. |
16:48 | We also do need to keep in mind that the crankshaft should be seeing no metal to metal contact so just because we've gone through that hardened surface, it's not necessarily the end of the world. |
16:58 | Particularly if you're looking at the use of a crankshaft where it could be considered a consumable in a race engine. |
17:06 | You're not too worried about trying to get 100000 miles of life out of that crankshaft, it's probably not a big deal. |
17:12 | I will point out that even though we shouldn't be getting metal to metal contact on the crankshaft, there's inevitably going to be debris running through the oil from time to time and this will still end up marking the unhardened surface on our crankshaft journals. |
17:27 | The other way that you can recover a crankshaft where you've ground it like this is that after the crankshaft has been ground and processed, you can have it heat treated using a process called nitriding. |
17:38 | And that rehardens that surface finish. |
17:42 | Nitriding in my experience so far is a bit of a mixed bag. |
17:46 | While yes it does provide that surface hardening that we've just removed by grinding the crankshaft, the downside with it is because of the heat treating process that it goes through that the crankshaft is heated up very high, to a very high temperature for the nitriding process to actually operate, and what I've inevitably found is that the crankshaft often ends up bending very slightly so you're fixing one problem and creating another. |
18:11 | There are companies that specialise in nitriding crankshafts though and may have special cradles to support the crankshaft during the nitriding process, eliminating or at least reducing the chance of that bend. |
18:23 | So don't think that just because you need to grind a crankshaft that you have to throw it away and start again. |
18:31 | Now, so we've talked about our graded bearing shells, we've talked about aftermarket bearing shells that are available in plus or minus one thou increments. |
18:39 | The other situation we may get ourselves into is where we measure our bearing clearances and we find that they are a little bit tight. |
18:48 | Now if they are a little bit tight this gives us another option depending on exactly how much material we need to remove. |
18:56 | So one option there, and this works quite nicely again with a high mileage crankshaft that may have some light scoring on the surface, is if we're only trying to adjust our clearance by maybe a half a thou or somewhere in that region, we can have our engine machinist actually polish the crankshaft journal to achieve the clearance that we're looking for. |
19:16 | This needs to be done carefully because if you're trying to remove too much material, you're almost inevitably going to end up affecting the taper on the bearing journal or ending up with some ovality in the journal so it's really only suitable for very small adjustments and your machinist is going to be able to explain whether what you're trying to do is going to be achievable by just polishing that surface. |
19:43 | The last one I'll just talk about and then we're going to get into some questions so if you do have any questions, this is a great time to ask them. |
19:51 | The last one, and this is one that we just recently struck wtih one of our Subaru FA20 builds and this is where we were using a set of Brian Crower H beam connecting rods, much like the ones I've got here. |
20:05 | And what we found is that, with the crankshaft in this particular build, we hadn't removed from the engine block, we were doing what we called our ghetto build, just a very quick and cheap rebuild where we were only replacing a bent connecting rod and we'd chosen to upgrade the rods to the Brian Crower rods. |
20:23 | And obviously as a matter of course, one of the things we wanted to do was check our big end bearing clearances. |
20:30 | And when we did this we found that the clearances were a little bit tighter than what we were aiming for. |
20:36 | We were around about 1.1 to 1.2 thousandths of an inch and I was trying to be somewhere closer to about 1.7, 1.8 thou. |
20:45 | Now in this instance one of the options we've talked about, polishing the clearance into the journal, possibly achievable but would have been a right pain in the bum because we would have had to then remove the crankshaft out of the block, break the engine block completely in half and then send our crankshaft off to our engine machinist. |
21:03 | Because the engine machinist isn't local to us, that was going to waste quite a lot more time as well as of course money. |
21:09 | Another option we looked at there though was we checked the spec of the big end of the connecting rod and what we found is that the rod was machined to the bottom size of the big end bore tolerance. |
21:22 | Nothing wrong with that, it was within tolerance and that's generally a pretty good aim for aftermarket rod manufacturers because it gives a little bit of freedom for a machinist to adjust that bore diameter. |
21:34 | Now of course when the bore diameter is smaller, it tends to provide more crush to the bearing shells and that provides a smaller finished inside diameter to our bearing shells. |
21:45 | So what we did in this instance and of course it did actually still require the work of our machinist but we had the machinist hone the rods to the top size. |
21:54 | So this is removing just a small amount of material and this gave us actually almost exactly the clearance we were looking for at about 1.7 thou. |
22:02 | Now the point I do need to make is this can be done but we do need to be very careful. |
22:08 | The reason I say that is because achieving the correct amount of crush on the bearing shells is critical if we want to make sure that those bearing shells aren't going to have any risk of spinning in the journal. |
22:19 | So don't think that you can just use that technique to make all of your bearing clearance adjustments, you do still need to make sure that you are within specification there so you've got the correct amount of crush on the shells. |
22:34 | Alright we'll jump over and have a look at our questions. |
22:37 | Remember if you've got any more, please keep asking them. |
22:44 | Michael has asked, feelings on chamfering oil outlets? Look I think anything you can do to improve the oil supply to the crankshaft is definitely a good idea. |
22:56 | We can actually see, maybe I'll have a quick look actually under our overhead shot here, that, and this is pretty common with a lot of factory crankshafts, is we can see that there is chamfering on the oil supply holes there. |
23:10 | Often that won't be the case, in which case you can do that manually. |
23:15 | You do need to be very very careful though because this is something where if you don't get it right, it's very easy to end up damaging the journal surface of the crankshaft, we don't want to do that. |
23:26 | And also, as I've kind of mentioned, with a factory crankshaft you're going to be trying to remove material from an induction hardened surface which is incredibly difficult. |
23:35 | So sometimes this is better left to an engine machinist, they can do that job reliably and safely without any chance of damaging the crank. |
23:49 | Manitau Black has asked, why are no manufacturers investing in the engine design popularised by Offenhauser where where the combustion chamber and cylinders are cast and machined as a single piece? OK so I think this comes down to a pretty unique but incredibly effective take on how to get around head gasket integrity problems. |
24:10 | If there is no head gasket, no problem. |
24:12 | And I think this was used as well in F1 back in the turbo era, there was a few manufacturers messing around with this technique. |
24:20 | I think probably the answer is that in production engines, head gasket integrity simply isn't an issue. |
24:27 | And the advantages with doing this technique where everything's machined as one piece is maybe overshadowed by the complexity of the machining processes when you need to actually do any work on it. |
24:40 | So for example cutting a new valve seat or replacing a valve guide all of a sudden becomes a very very serious and intensive operation. |
24:47 | So yeah it's a very narrow focus product, how's that sound? James Fox has asked, what break in oil do we recommend? OK this really is probably a pretty tricky question because I know there are a lot of specific running in oils out there on the market. |
25:10 | I've used a few of the running in oils and I've actually ended up more recently switching back to just using a good quality mineral based oil. |
25:20 | Now what we're trying to do when we are choosing a running in oil is we want to choose an oil that is not a full synthetic, that's probably the biggest key. |
25:30 | This might sound a little bit counter intuitive but a full synthetic oil during the break in process can actually be in an essence, too slippery and what this does is it can inhibit the ability for the rings to bed properly on the fresh hone pattern on the bores. |
25:45 | Now that is probably a stretch these days, with modern ring technology and modern honing processes you'd probably have to try pretty hard to mess up the running in process but I've kind of had a process that I've been using for about the last 18 or 20 years, it's always worked and I think most engine builders kind of tend to be just a touch superstitious, if you've got something working, don't mess with it. |
26:06 | So anyway, getting back to the actual question, the running in oils from a lot of the manufacturers tend to be incredibly thin and they are designed to allow the rings to bed in, often there will be some additives, some zinc additives to protect some of the components, particularly with a solid tappet style lifter, you do need to be careful with running in those components properly to prevent excessive wear. |
26:34 | However I just am a little bit uncomfortable with some of those running in oils because they are such a thin oil. |
26:40 | And our engines, even though we're running them in, they are still a performance engine, even at modest power levels they can still be putting a lot of load into the engine components that need to be supported by that oil film. |
26:52 | So that's why I've sort of switched to just a good quality mineral based oil. |
26:55 | I'll generally swap that out after about maybe an hour to two hours running on the dyno, or if you're out on the road I'd probably do that somewhere between 100 and 200 miles. |
27:04 | After that point, your engine is as run in as it's going to get. |
27:11 | Darius has asked, when mixing bearing shell size, does it matter where they go, top or bottom? We are only talking about the merest tiniest amount of change there so it doesn't specifically matter. |
27:27 | As a rule of thumb I generally try and make sure that if I am mixing the bearing shells, I will put all of the smaller shells on the bottom, all of the bigger shells on the top. |
27:38 | Now that's just a good rule of thumb just to keep them all in the same location. |
27:43 | With the connecting rod bearings as well, what we do need to be mindful of, and this is very very rarely going to be an issue unless you're building a very high specification, high compression engine, we do need to take into consideration that there may be some very very minor effect on our bearing clearance choice like that in terms of the deck clearance between the piston and the cylinder head. |
28:07 | So really it's probably not going to be a, even a consideration for 99.9% of people. |
28:15 | But if you are running things incredibly tight, just understand that depending on where you locate the thicker and thinner shell there, you could be getting half a thou difference in your deck height. |
28:30 | Andrew has asked, I'm currently building an EJ257 sleeved short block. |
28:33 | I'm told that plus 0.025 rod bearings in conjunction with a proper weight oil, would lend itself to a high boost application. |
28:45 | If you're going to go to a undersize bearing like that, a rod bearing like that, you're still going to need to actually make changes to your journal diameter so you wouldn't just go and put a 0.025 undersize shell in without actually checking everything. |
29:07 | So really it's just going to come down to where your clearances end up with that shell in there. |
29:12 | You'd want to check that, it may work out there, sorry I'm just working in imperial/metric units there and just doing a conversion in my head so as I'm doing that. |
29:23 | Yeah it may work out, I haven't specifically done that but it's just as with every aspect of engine building, you don't ever want to make assumptions on that, you just want to check and make sure that your clearances are where you expect them to be. |
29:39 | And with that particular engine, because they are known for rod bearing problems, definitely I tend to build them with a slightly loser clearance, that's definitely a good direction to be going in. |
29:51 | Derek's asked, when using two different bearing shells, OK got the same question there, should the thinner one be on the top or the bottom. |
29:57 | So I generally would like to have the thinner one on the bottom so we're not going to introduce any more problems with our deck clearance as I mentioned. |
30:04 | Barry's asked, do you recommend mixing bearing shells to get the clearance? Think I've already talked about that. |
30:10 | Lucifer the Sixth has asked, so I measure my clearances on my D16 to be 0.0019 to 0.002, so two thou essentially, where the surface limit is two thou and the spec is 1.1 to 1.15. |
30:25 | Should I run it as it is or use another half shell to tighten it up? Planning to run at about 1000 to 1500 above stock. |
30:40 | It's probably in all honesty at that point going to be just fine. |
30:45 | So as long as you're within the service limit, obviously you are within the point that Honda deem to be suitable for that, albeit yes you are a little bit looser than that, than their target specification. |
30:59 | The reason I say that you're probably going to be just fine there is the fact that you are expecting to increase the RPM range. |
31:07 | And what I would probably do is combine that with a thicker oil than stock, and I certainly would not be concerned about that. |
31:15 | Freaks89 has asked, I had undersize bearings fitted to my engine which is a mild, build because the crankshaft had some scarring or scoring and had to be machined, does this limit the engine's ability to rev higher than the stock RPM limit? I fitted aftermarket cams to benefit from a higher RPM operation, I don't know if I can raise the RPM limit. |
31:33 | Does using undersize bearings affect that? OK so the answer to that is a resounding no. |
31:41 | We have used ground crankshaft with undersize bearings in some of our 4G63 race engines which we've revved to 9000, 9500, even 10500 RPM, with no problems. |
31:53 | So as long as the rest of the crankshaft is in good condition, one of the things we want to know there is was there any cracking in the journal radius, that's something we'd want to check before we really go to the trouble of spending money on having the crankshaft ground in the first place. |
32:09 | But just because the crankshaft has been ground, doesn't mean that it's necessarily any weaker or won't withstand a higher RPM. |
32:16 | We do have those issues that I've talked about with grinding through the hardening on the surface there but that's more a longevity issue as opposed to outright strength. |
32:33 | Alright so yeah we've got another question exactly the same there from Rodrigo about the ability of a ground crankshaft to rev higher so again obviously exactly the same answer. |
32:43 | Alright guys that brings us to the end of our webinar and as usual, for our HPA members if you've got any other questions, please ask those in the forum and I'll be happy to answer them there. |
32:53 | Thanks for joining us and look forward to seeing you all next week. |
Timestamps
0:00 - Introduction
0:40 - What is a bearing clearance?
1:35 - What should the clearance be?
6:30 - Graded bearing shells
11:25 - What if you don't have graded bearing shells?
13:35 - Mix and match bearing shells
14:25 - Crankshaft grinding
18:30 - Crankshaft journal polishing
19:40 - Rod/block honing
22:40 - Questions
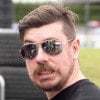