246 | Mechanical vs Electric Fuel Pumps
Summary
While electric fuel pumps have come a long way with their flow capabilities in the last few years, the mechanical pump is still the go-to option if you need huge fuel flow. The mechanical pump however is not without some downsides and in this webinar we’ll cover what you need to know when making your fuel pump decision.
00:00 | - Hey guys, Andre from High Performance Academy, welcome along to another one of our webinars and today we're going to be talking about the options available when it comes to fuel pumps. |
00:10 | In particular we're going to be talking about mechanical versus electric fuel pumps, where the advantages are in one over the other and when you may decide to choose one over the other. |
00:21 | And this is actually an area that probably over the last five or so years with the advent of the newer brushless fuel pump technology, there's less of a defined line in the sand now. |
00:33 | It used to be back when I first got involved in import drag racing, that there was a point where you literally couldn't support the power requirements of a high boost turbocharged methanol fuelled engine on an electric pump. |
00:47 | That's now not quite so clear cut as I mentioned but we'll dive into that and you'll find out a little bit more about it. |
00:53 | As usual, if you've got any questions on anything I'm talking about today, you can ask those in the chat and we'll deal with those at the end. |
01:01 | This is probably going to be a little bit shorter than our normal webinars, not quite so much detail to cover here so if you do have questions, I'd urge you to jump in there reasonably quick with them. |
01:13 | So let's start with the basics though, why do we need a fuel pump at all, and that should be pretty straightforward, we obviously need the fuel pump to provide both the flow and create pressure so that our fuel injectors can deliver the fuel as required. |
01:27 | Now in terms of pressure, there's no real fixed 100% rock solid number that we need to be running and the fuel pressure that we see will depend a lot on the particular application. |
01:38 | For a normal road going car that runs a return style fuel pressure regulator which is referenced to manifold pressure, it's quite typical to run around about three bar or 43.5 psi of differential pressure and what that means is that the pressure across the injector, the differential pressure which is the difference between fuel pressure at one side and our manifold pressure at the other side is always going to remain the same, three bar, 43.5 psi. |
02:06 | A lot of more modern or late model engines now, they come out with a returnless fuel pressure, or fuel system which runs at a fixed fuel pressure irrespective of our manifold pressure. |
02:18 | Typically that works out to be four bar or 58 psi fuel pressure so there or there abouts. |
02:26 | But there's no fixed rule that says that's what we've got to run. |
02:29 | Particularly when we look at drag racing which is where a lot of the mechanical pumps that we're going to look at today end up, it's not uncommon to run somewhere in the region of 80 psi base fuel pressure, plus we'll have boost pressure on top of that so if we've got a vehicle for example running 80 psi of boost pressure, again not unheard of in a high boost turbocharged application, the actual fuel pressure in the rail could end up being as much as 160 psi. |
02:59 | And the problem with this is that with a conventional fuel pump, as we increase the fuel pressure, it makes it harder and harder for the pump to flow fuel and this can actually limit its output. |
03:13 | This gets worse as well when we start running on specialist fuels which are so common in motorsport, particularly drag racing, the likes of methanol and even E85. |
03:23 | If we look at E85 as a fuel, compared to the volume of fuel that we'd need to supply if we're running on pump gasoline for a fixed amount of power. |
03:35 | If we go from pump gasoline to E85, we need to increase our fuel volume flow by around about 35% to 40%. |
03:42 | Now if we go to methanol though, we need to increase that flow by around about 2.5 times so you start to see on top of an engine producing huge amounts of power, because of the fuel requirements as well, we're starting to talk about really really high levels of fuel flow. |
03:59 | There's a rule of thumb that I've always worked to with pump gasoline which sort of gives us a bit of a guide for where we need to go with our fuel requirements, which is that we need around about a litre of fuel flow per minute for every 200 horsepower we want to make. |
04:15 | That's actually injector flow though and generally with a fuel pump we need to actually oversupply because if we are consuming or at least delivering I should say, exactly the same volume of fuel through the injectors that the pump is capable fo supplying, we're going to end up with the pressure dropping away which is not what we want. |
04:34 | So generally working on the principle of having around about a 20-30% oversupply from the fuel pump gives us enough headroom to make sure that we're going to maintain fuel pressure. |
04:44 | It's really really common to see one of the quickest and easiest places to come unstuck when modifying a factory turbocharged car is once we start increasing the boost pressure, maybe freer flowing exhaust and freer flowing intake we find that the air/fuel ratio at high RPM starts to move lean. |
05:06 | And while this can be a case of the fuel injectors not being big enough, quite often we'll see that lean move even when we still have injector head room and quite often this will be because the fuel pump simply can't keep up so that's one of the indicators that you've got a fuel pump problem. |
05:25 | So conventionally most cars have come equipped with a conventional style fuel pump like this, an electric fuel pump that is a brush style pump so it uses two little brushes to transfer 12 volts through to the actual pump windings, the pump body itself and then it's just essentially like a little electric motor, nothing particularly flash, we're not going to get too deep into the workings of that. |
05:50 | And these have worked well but of course over the years we've seen the engine's power levels climb and the fuel requirements as I've mentioned have also increased. |
06:01 | And what we tend to see, if we look at the likes of a conventional fuel pump, the output from it, we'll head across to my laptop screen for a moment and this is just one of the Aeromotive pumps which I've found which is convenient for the data that they provide, you'll be able to get this from most suppliers though. |
06:19 | If we look at this little flow diagram here, that is going to come up, I'll just zoom in on this a little bit. |
06:27 | So we've got our flow rate out of the pump here on the vertical axis and this is in pounds per hour. |
06:32 | Conveniently different pump manufacturers will rate their pumps in different ways, litres per hour, gallons per hour, in this case pounds per hour. |
06:42 | Probably actually more useful because the problem is that when we're talking about air/fuel ratio, we're actually interested in the mass of fuel not the volume. |
06:53 | So that's a little intricacy there where you've got most pump manufacturers will be talking in a volume flow, either litres or gallons per hour. |
07:01 | Anyways, that's how this is rated and we've got psi, the pressure that the pump is working at on the horizontal axis. |
07:09 | So for example here if we were only requiring 20 psi of pressure, we're somewhere around about here, we've got two lines on that graph, one at 12 volts, one at 13.5 volts, we'd like to think we're probably going to be at 13.5 volts with the alternator charging. |
07:24 | So we can see at that point there we're somewhere around about maybe 570, 580 pounds of fuel per hour. |
07:33 | That's all well and good but particularly on a turbocharged or supercharged engine, we're going to find that as the boost pressure increases, if we are using a manifold pressure referenced regulator we're going to be moving out to the right here and while that number might have seemed quite impressive at 20 psi, if we're all the way out here at 70 psi, very easy to get to, then we're going to find that our flow all of a sudden drops down to something like 350 pounds per hour so essentially at 70 psi we've got about half the flow out of the pump and this is something that I see so many people overlook, the number of people who brought cars to be tuned in my old workshop and basically they'd looked up the specs of a fuel pump and the fuel pump might have been advertised as a 1000 horsepower fuel pump and they're thinking to themselves well happy days, I'm only going to be targeting 800 horsepower so clearly that's going to be enough and I don't know if this is deceitful perhaps on the part of the fuel pump manufacturer, might be a little bit of marketing ploy in this but when we actually dig in deeper, the reality is that that pump will support 1000 horsepower on a naturally aspirated engine where we're only going to be running something like 43 psi rail pressure. |
08:48 | When we add a turbocharger and now we're adding 30 psi of boost and we're now up at 70 or 80 psi rail pressure, the flow of the pump drops down and instead of being able to support 1000 horsepower, now it can actually only support somewhere in the region of maybe 600 horsepower. |
09:04 | So those are little things that are very important to watch and make sure that you don't end up getting caught out on. |
09:11 | Now I'll also just give you some insight into my own car so we'll head over to one of the photos from our Instagram. |
09:19 | So this is my old Mitsubishi Evo drag car. |
09:21 | And this was developed probably I'm guessing about 15 or 16 years ago now, it's actually starting to get a little bit hard to remember the exact timeframe of this but I think it was retired somewhere around about the early 2000s so that would probably work out about right. |
09:39 | And this was built up initially as a relatively streetable modified drag car and then obviously things went crazy, the front fell off and we tube framed it as you can see here. |
09:51 | Now the part that is interesting was the fuel pump choice and it's a little hard to see. |
09:55 | We can see it down there mounted on the, one of the lower rails for the tube frame front end, we'll just drop back and have a quick look at it. |
10:03 | You can see it again down here. |
10:05 | The reason it is mounted down here is because we ran a little 20 litre fuel cell up here in the front right hand corner of the chassis and that gives a direct feed basically straight in through a filter and Into the pump. |
10:17 | Now back at this point in time, there wasn't a huge supply of large aftermarket electric fuel pumps available, there were definitely some mechanical pumps but back at this time I was sort of in a position where I was still finding my way with these fuel systems, I hadn't had any personal experience with a mechanical pump and I wanted to stick to something that I knew and could understand which is why we stuck with an electric pump. |
10:44 | So the one that I chose there was the Weldon 2345A pump, bit of a mouthful but that's what it was. |
10:53 | I'm pretty sure this was the largest flowing pump that Weldon produced. |
10:57 | And it's a pretty hefty piece of kit there, obviously designed to run on a 12 to 14 volt electrical system. |
11:07 | This particular pump though was also designed to be compatible with 16 volt charging systems so again in drag racing it's quite common to ditch the 12 volt battery and actually go to a 16 volt battery, run that without an alternator in a total loss style, basically the teams will then plug the car into a charger between rounds so that the system is running at 16 volts. |
11:28 | So the advantage with this is by increasing the voltage to the pump, it actually does do a dramatic, it gives a dramatic increase in the pump output. |
11:38 | Again going to a full 16 volt system wasn't something I really wanted to do, there's a few downsides with that as well when you don't have an alternator charging it but I could get the same effect by using a fuel pump voltage controller. |
11:53 | I don't think it was actually this MSD part number that I ended up using but basically it gives you an idea of what I'm talking about and it was adjustable and I could bring the voltage up to I think we ran it at about 16.5 volts. |
12:07 | I'm pretty confident that the actual unit that I used was called a booster pump but again, you get the idea. |
12:14 | So this basically gave me a situation where I could still run an electric, conventional electric pump which I understood and we did still have those problems of the flow dropping away as the boost pressure increased, we were driving that pump harder and harder but with the 16 volt system and the Weldon pump we were still just within the head room of what we needed to flow on methanol fuel and got us through. |
12:41 | I think it's probably fair to say that if I had my time again now, knowing what I know now, the experience I've gained on other drag cars I've been involved with, I would without hesitation have gone straight for a mechanical pump which we're going to get into in a second. |
12:55 | But at the time it served the purpose and it was something that I understood. |
13:00 | Alright so the problem is that while conventionally it's fair to say that electric fuel pumps did have their limitations, as I've mentioned already, these days those limitations are kind of getting a little bit less cut and dry and the reason for this is we now have a range of manufacturers providing what's referred to as a brushless pump. |
13:24 | Now again I'm not going to get into the nitty gritty of how these work, there's some pretty clear videos out there on YouTube if you want to learn how the brushless pump works but as its name implies it doesn't use brushes like a conventional pump like this little guy here and instead it basically uses electromagnets inside the pump and by powering up different electromagnets they can make the pump turn and there's quite an advanced control of it that goes along with this which can then control the pump speed very accurately. |
13:56 | So the thing with the newer range of brushless pumps is that their power potential has really climbed to some insane levels now. |
14:05 | I think, if we just jump across to my laptop screen again, this is an Aeromotive pump, let's just drop that, nope making it bigger not smaller which is not what I wanted to do. |
14:19 | Yeah so this is one of the Eeromotive pumps here which is 10 gallons per minute. |
14:24 | So this particular pump will be able to support, I think they've valued, their numbers here, so on E85 forced induction we're almost 3500 horsepower at the wheels. |
14:36 | This would have been completely unheard of just a few years ago and it's this sort of technology as I say, is making it a little bit less clear on whether or not we do need to go to a mechanical pump. |
14:48 | There are some other advantages with the brushless style pump in that they can be speed controlled as well so one of the problems is if you've got a pump that can move 10 gallons of fuel per minute, then you only really want it to be moving 10 gallons of fuel per minute when it actually needs to which will be high in the load, high in the rev range. |
15:11 | If we're sitting there idling, moving 10 gallons of fuel per minute around the fuel system, all we're doing is needlessly adding heat into that fuel so this is where fuel pump speed control with these brushless pumps comes in and they can only give the fuel flow that is required. |
15:29 | Now one of the downsides with basically any big electric pump, and my Weldon wasn't too far off the mark, it was still a consideration here, is that it does take a lot of electrical energy to keep these pumps working. |
15:43 | And particularly when you are limited to maybe 14 or even 16 volts, what this means is that the current draw from these pumps is massive. |
15:54 | It's not unheard of to see somewhere in the region of 90 to 100 amps from one of these brushless pumps when you are pushing it really really hard. |
16:01 | So this needs to be considered as well, even if the brushless pump does fit the bill in terms of your requirements, that's a massive current draw on your electrical system and this is why again in drag racing, it's a very specific type of motorsport, we tend to see that brushless pumps still aren't that common, the mechanical pump is still the go to pump of choice because a lot of the high end drag cars that are purpose built for drag racing, again will have a 16 volt charging system with no alternator. |
16:31 | If you're trying to draw 100 amps for the length of a pass down the drag strip, that's very quickly going to drain the 16 volt battery so not exactly ideal there. |
16:43 | So also one of the pumps that we've actually been following for a number of years, and if you want to get a little bit more in depth, if you head to our YouTube channel and you search Injector Dynamics fuel pump or something of that nature, you'll find some technical details on their Injector Dynamics brushless pump and controller, something that's been in development basically every time we've been at PRI. |
17:06 | I do believe they've got beta units up now, and we'll just head over to my laptop screen. |
17:12 | This is some test results from one of those beta units that Radium Engineering did. |
17:16 | So just to kind of back up, here's the unit itself so this is the fuel pump controller so it's not actually the fuel pump itself. |
17:26 | If we scroll back up, there's the actual pump which is the generic veyron pump and this is all of the componentry that comes with it. |
17:34 | So the pump is not really necessarily the special part, it's actually the controller that is the tricky part. |
17:40 | The controller from Injector Dynamics controls the pump speed, it's also got a lot of CAN interfacing between ECUs so you can actually control the pump flow based on the engine demand. |
17:52 | Anyway, getting a little bit too advanced there, let's scroll down and we'll have a quick look here, so this is just an idea of the current draw, so we've got current on the vertical axis here, versus the pressure that the pump is being operated at. |
18:04 | So you can see if you're down around let's say 75 psi, we're somewhere around about 38 amps so not too terrible but as I've mentioned, at the pointy end, if you're up around 150 psi, then you're drawing in this case, I think it's around about 70 amps there. |
18:23 | So quite high current draw, you obviously need to keep this in mind with the design of your electrical system. |
18:29 | This little graph here which is probably a little bit hard to see in detail shows you for various flow rates, and also various voltages and various differential pressures, what the current draw will be. |
18:41 | The impressive thing here, if we scroll down, this is flow in litres per hour out of the pump, this is pressure in, differential pressure in PSI and you can see this is the nice thing with these brushless pumps is as we drive the pump harder, we increase the fuel pressure. |
18:59 | Because it is controlling the pump speed, the actual speed of the impeller in the pump, we essentially, right up to the point where the pump can no longer move any more fuel, we see that the output from the pump is almost rock solid and again Injector Dynamics, if any of you have been to the PRI show, for the last five years have had a really nice visual display on their stand of exactly this. |
19:21 | It's got a Bosch DDU dash display showing all of the parameters, including fuel flow, fuel pressure, voltage and current and also estimate power capability and you can actually wind the regulator down and crank up the fuel pressure and you can watch that the flow doesn't vary, all it does is it draws a crapload more current from that pump so just an idea there of what the brushless pumps were. |
19:45 | And really this webinar is more about electric versus mechanical pumps but I think given how far the brushless pumps have come and again I've said, kind of starts to blur the requirements a little bit, it was worth diving into those a little bit there. |
20:03 | Anyway, moving on now to mechanical pumps, what they are and why we may want them. |
20:10 | So the advantage with a mechanical pump is that they, see if I can find my pictures, mechanical pump is that they basically can be sized to flow just about any amount of fuel. |
20:24 | So it's just a case of sizing the gears inside the pump to suit your actual flow requirements and you're away. |
20:31 | That's why we'll see these pumps are used up to and including the most powerful engines in the world which are, internal combustion engines I suppose I should say there, which is our Top Fuel drag engines. |
20:44 | So that's what you'll find on those. |
20:46 | The other nice thing with a mechanical pump is because it is driven via the crankshaft or indirectly from the crankshaft in some way, basically the speed of the mechanical pump is in relation to our engine speed. |
20:59 | The flow of the pump increases in relation to engine speed and of course that's exactly where we do want maximum flow, high up in the rev range, that's where we're going to be using a huge amount of fuel so it kind of nicely ties in the fuel flow with the engine's fuel requirements. |
21:18 | One of the aspects we do need to keep in mind here though is the way the pumps need to be driven, they do need to be driven at half engine speed, 50% of the crankshaft speed so this comes into probably one of the downsides of the pump which is the fact that mounting one of these pumps can be a bit of a pain and can be quite cumbersome. |
21:42 | So what we'll do for a start is have a quick look at a few of these pump designs. |
21:47 | So these are available from a range of different manufacturers. |
21:52 | This one here, I'm pretty sure was a Waterman pump, I'm pretty sure. |
21:59 | But basically what we can see here is you've got the pump, this will be either the inlet or the outlet and the design of this pump, we've got this three bolt flange here which can be mounted in this case to the likes of the back of a dry sump pump and then we've got this little hexagonal drive which is how the pump is actually driven. |
22:17 | This one here from Aeromotive, and same sort of deal, so we've got the mechanical pump body here, this one comes with a little adjustable mounting bracket and this is also gear driven straight off the crankshaft so another option there. |
22:33 | This is probably one of the neater ways of going to a mechanical pump and driving it and particularly if you are already running a dry sump system on your engine, which is pretty common with a lot of high end race engines, there will usually be the facility to drive an ancillary device like a mechanical fuel pump straight off the back of the dry sump pump. |
22:55 | I actually struggled to find too many photos of this but that's exactly what we've got there and again there's sort of a pretty standardised three bolt flange pattern here that allows the adaption. |
23:05 | Now the nice thing about this is the hard work of getting drive from the crankshaft, to the dry sump pump, physically mounting the dry sump pump to the engine block, that's all been done, the belt's already there, it is just literally a case of bolting the mechanical pump into place and you're good to go. |
23:23 | If we look, on the other hand, the likes of this style, there's a bit of work to do in order to actually get a mounting location sorted out for your pump, align it properly for the crankshaft pulley or your ancillary pulley that you're going to be driving it on and then also get the belt into location and get that properly tensioned so this is probably one of the things that puts people off going down the path of the mechanical fuel pump so again if you've got the dry sump pump already there, it makes your life just that much easier. |
23:54 | Now the other aspect we've got, the other option is that you can drive these pumps off the camshaft and of course the camshaft also drives at 50% engine speed. |
24:04 | So it's a natural option to go for. |
24:07 | This particular kit here, this was a 4G63 drag engine I built for a customer over in Germany and he used what you can see here is a Magnus Motorsport kit, it's all CNC machined and it bolts to the backing plate behind the cam and it aligns, as you can see there, in this case it was an Aeromotive pump and it's aligned with the exhaust cam so it drives it straight off the exhaust cam, nice and easy to do and if we can we'll also head across, I've got a few other examples here. |
24:38 | This one is on a Nissan RB, I can't remember the brand of kit here but again this one mounts the Kinsler mechanical fuel pump straight off the back of the exhaust cam. |
24:51 | And I think I've got one more as well, yeah so this is a Waterman pump mounted on the front of a Toyota 2JZ. |
24:59 | So pretty simple, particularly if there is a off the shelf kit rather than having to develop it all yourself. |
25:06 | Now the other nice feature with the mechanical pump is that because it's obviously been driven by the engine, if you are involved in an accident and the engine is stalled, the pump is obviously instantly going to stop and this means that you're not going to end up in a situation with an electric pump which could potentially be constantly pumping fuel out and if you've got a ruptured fuel line, this could be dangerous. |
25:34 | Yes I know, most aftermarket ECUs and factory ECUs will control the fuel pump so that if the engine stalls, the fuel pump will only run for a couple of seconds and then shut down but I do also know that some people tend to bypass that. |
25:48 | Alright we're going to move into our questions and answers pretty soon so this is a good time to remind you if you've got any, please ask them. |
25:54 | There are a couple of other considerations when it comes to mechanical pumps though. |
25:58 | I've said already that the flow from the pump is very much linked to our engine speed, which is both good and bad. |
26:06 | Obviously if we're at high RPM and wide open throttle and the engine is consuming a huge amount of fuel, that's going to be a great thing, that's exactly what the engine wants. |
26:16 | However what happens is that when we back off the throttle, particularly in the case of a drag car at the end of the run, we get off the throttle, if we don't immediately clutch in, the engine RPM is still incredibly high, we've now closed the throttle so the fuel demands have dropped to almost zero but the pump is still pumping massive amounts of fuel and we do need to keep this in mind with the section of the regulator that we choose, we do need a regulator that is designed to work with a mechanical fuel pump and has a large enough bypass to do that. |
26:48 | Something of the nature of this Aeromotive regulator that I've got here that's designed to work with their range of mechanical pumps. |
26:56 | Basically it includes a much larger bypass port, I think from memory this one uses two -10 feeds and a -10 return whereas a lot of the conventional electric fuel pump regulators might only have -6 return line or something of that nature so just important to keep that in mind, otherwise you can end up with uncontrolled spikes in your fuel pressure. |
27:21 | The other aspect there as well which is easy to overlook is that mechanical fuel pumps generally do a horrible job of self priming at cranking speed. |
27:32 | So this can be a problem where essentially at cranking RPM, maybe 200 to 300 RPM, the pump is physically not able to build enough fuel pressure to start the engine. |
27:42 | So there's a couple of ways that this is dealt with, in a drag application where it is a very specialised type of motorsport, it's quite common to see competitors will actually use a can of engine start to get the engine to start up initially, of course as soon as the RPM climbs up and the engine's at maybe 800 to 1400 RPM and normal idle speed, then the pump's fine, it's on its own and it's happy to keep building pressure, it's just getting it to initially fire the engine that's the problem. |
28:13 | The other aspect which is the way I went on the mechanical pump cars that we built, I wanted to be a little bit more neater and tidier than that, a can of start you bastard's not really a good look on the start line in my opinion so what we ended up doing was incorporating an auxiliary little electric fuel pump like this, didn't need to be anything big, and what we did was we incorporated that into the bottom of the fuel tank and we ran a small -6 feed line and we ran that into the outlet of the mechanical fuel pump through a one way valve. |
28:46 | So what we could do then is program the ECU so that when the RPM was let's say above 50 RPM and below 500 RPM it would run the little electric fuel pump, that would create pressure which would allow the engine to start, as soon as the engine RPM was above 500 RPM, the electric fuel pump would disengage, the mechanical fuel pump was then happy to keep going and that was that so a nice neat solution but it does add a little bit more complexity to your system. |
29:15 | Alright so there we go, a quick run down on the pros and cons of electric versus mechanical fuel pumps, we'll jump in and see what we've got in the way of questions now. |
29:25 | First question from our most regular watcher, Manitou Black, since no fuel pressure regulator is linear, how important is it to run a fuel pressure sensor and have a volumetric efficiency ECU do mapping in conjunction with accurate injector characterisation to deliver accurate injector timing. |
29:41 | Look it's nice, it's not essential. |
29:45 | I think this is something that's important to say with a lot of the technology that now we see applied to modern ECUs and don't get me wrong, I'll take all of the technology I can get but I think what's important to understand though, a lot of newer tuners think that if we don't have all of this stuff, if we don't have a fuel pressure regulator, there's absolutely no chance we can do a half decent job of tuning the engine and that's simply not true. |
30:10 | There will be variations of course, because you're absolutely right, fuel pressure regulators aren't always entirely linear, but we can often bake in the non linearities into our calibration and I mean a much more important aspect of this for many years I was stuck tuning ECUs that made no attempt to compensate for the likes of batter compensation or injector dead time, injector offset, whatever you want to call it and yeah I could still get a reasonably good job of tuning those ECUs, yes the air/fuel ratio would fluctuate a little bit more at idle than I'd like but particularly once you're up and running we're good to go. |
30:47 | So yeah while it's nice to have, definitely not essential to have. |
30:52 | Suhas has asked, what pressure would you recommend for naturally aspirated engines and what would you recommend for turbocharged engines? Can you brief more about the return and returnless systems? OK look there are no rules here. |
31:05 | I kind of mentioned a couple of brief targets there that are pretty commonly used so if you're running a return style fuel system it's pretty common but definitely not essential to run three bar, 43.5 psi. |
31:21 | Quite often though if you're getting to a point where you're just getting a little bit marginal for injector duty cycle, so you really just about need a larger set of injectors but you're on that borderline, you might be able to get yourself enough headroom by lifting that fuel pressure up to four bar for example. |
31:37 | Problem with this is if your fuel pump is also marginal, as you lift the fuel pressure, as we've already talked about during the body of the lesson, the pump has to work harder, so you actually find the flow drops off so that'll only work if you've got enough fuel pump head room available. |
31:52 | Now there are also some potential arguments around improved atomisation through the injectors as we lift the fuel pressure. |
32:00 | I haven't done a lot of back to back testing on this so it's a bit of a hard one to really give any solid information about. |
32:06 | The other thing is that as we raise the fuel pressure, it's not just going to be the atomisation of the injector that will change, the flow pattern as well, how it's targeted, that can all change as well. |
32:18 | For turbocharged engines, there's not necessarily going to be that we want to change the base fuel pressure. |
32:25 | But the important part here is that with a turbocharged engine, we would almost always run a manifold pressure referenced fuel pressure regulator which means it maintains that same differential pressure across the injector and raises the fuel pressure with respect to boost. |
32:42 | If we don't do that, and you can do it with a returnless fuel system, what happens is let's say we've got for example, 60 psi of base fuel pressure, that's where our fuel pressure's going to sit. |
32:54 | Let's say we now run 20 psi of boost pressure, what that means is that the differential pressure across the injector has now dropped to only 40 psi, 60 minus our boost of 20 is 40. |
33:07 | If we got to extremes and we ended up increasing our boost pressure up to 60 psi, probably a little unlikely in this scenario but let's say we did that. |
33:15 | We'd actually have zero flow through the injectors because there is no differential pressure across the injector. |
33:20 | So that's...as you increase the boost pressure on a returnless system, your differential pressure is eroded which means your effective flow through the injector for a given pulse width will also reduce. |
33:34 | Next questions, Potato has asked, when camshaft driven mechanical fuel pumps suffer catastrophic failure, is there much risk in causing damage to the camshaft? Look I can't say it wouldn't happen but it's not a direct drive to the camshaft. |
33:50 | Generally there'll be a little CNC machined adaptor that bolts on and there's actually a little, I forget the name of it, there is a term for it but it's basically a little isolating rubber mount that goes between the two, this takes any harshness out of that system. |
34:06 | So I haven't seen any catastrophic failures that have taken out the cam, can't say it's impossible but probably pretty unlikely. |
34:15 | Herney GTI's asked, how to you prime in a mechanical pump? Oh I've covered that. |
34:20 | Jaffromobile has asked, can you expand on the topic of swirl tanks with a mechanical pump and a feeder pump? A swirl tank, I'm not 100% sure exactly that you're referencing there so with a mechanical pump, normally in a drag application we would use these with the fuel cell mounted up in the engine bay, much like I showed with the shot of my own drag car, that's not to say that it's essential though, you can still run a rear mounted fuel cell which would then, you may have struggled with the, you may struggle I should say with the pump actually drawing from the fuel cell. |
34:58 | Quite often the solution there, which I think might be what you're talking about is to use an in tank electric pump and then use a swirl pot or a surge tank which the in tank electric pump feeds and then the mechanical pump can draw from that. |
35:17 | Island Boy's asked, any thoughts on the new Magnus K20 on the mechanical pump? Not a product that I've seen. |
35:25 | Pretty much everything that I've seen that does come out of Magnus Motorsports' workshop though is pretty high quality, their CNC work is pretty great so yeah without having used one or seen one myself, can't really say too much more about that. |
35:38 | Alright that brings us to the end then, no more questions for today. |
35:42 | Remember if you are watching this in our archive and you've got other questions, please ask those in our forum and I'll be happy to answer them there. |
35:49 | Thanks for watching and hopefully we'll see you in our next webinar. |
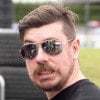