382 | Genius Lattice Structures for 3D Printing & CAD
Summary
Additive manufacturing opens the door to designs that wouldn't be possible with traditional techniques. In this webinar, we'll discuss volumetric or 3D lattice structures and how we can use them in our designs that will be 3D printed.
You’ll discover what lattice structures are, how they work, and why they’re especially powerful when combined with 3D printing technologies like FDM, SLA, and powder bed fusion (SLS/MJF).
You’ll explore common lattice types including cubic, body-centred cubic, and triply periodic minimal surfaces (TPMS) like the gyroid, along with how each performs mechanically. You’ll also learn how lattice structures can enhance thermal transfer, fluid flow, and impact absorption, making them ideal for motorsport applications such as lightweight structural parts, heat exchangers, and safety devices.
You’ll be introduced to how these structures are created in Fusion 360, including the software tools and extensions required. You’ll also gain insight into support requirements for different 3D printing methods, when structures can be self-supporting, and how to approach your designs for real-world printability. Finally, you’ll get a quick look at specialist tools like nTopology and how this area is rapidly evolving, although with a huge price tag.
00:00 | At 3D lattice structures and volumetric lattices in CAD and also 3D printing. |
00:09 | So, we're going to start by just talking about what these are, if you're not familiar with them, how they're related to 3D printing, how we can use them in motorsport or automotive design applications, and how we can go about creating some of these in our CAD software as well. |
00:25 | So, let's just start off by discussing what a lattice structure or a 3D lattice is, and I'll just bring up some photos I have here on my computer. |
00:37 | So, if we just jump to my computer screen here, these are some 3D printed lattices on my screen, just an image that I found online. |
00:47 | But basically a 3D lattice is a 3D repeating kind of structural pattern that fills a volume. |
00:54 | In some cases it can fill a surface as well, just depends on the application. |
00:59 | The main purpose around these lattice structures is in lightweight designs or efficiency. |
01:07 | So, they basically allow us to maximize or get maximum specific mechanical properties. |
01:15 | So, when I say specific mechanical properties, what that means is a mechanical property per unit mass. |
01:21 | So, something like this stiffness to weight ratio or the strength to weight ratio. |
01:27 | But they also provide some benefits around things like fluid flow and thermal transfer and also impact absorption as well. |
01:37 | But we'll have a little look at that as we progress through the webinar. |
01:43 | These structures are often inspired by nature or naturally occurring structures because nature has this kind of tendency to be extremely efficient and waste no material basically. |
01:57 | So, if that's out. |
02:07 | But there's many different types of structures. |
02:10 | The common ones that we're often seeing in mechanical design anyway would be cubic face centered cubic and body centered cubic, which I think there's no cubic here, but some of these are body centered cubic. |
02:25 | It's basically these kind of diamond or triangular structures here or cubes and some orientation. |
02:34 | And a lot of these structures, like everything shown here will have slightly different mechanical performance as well. |
02:40 | So, some of them might be maybe tougher than others, where some of them might be stiffer and they all kind of fail and function in slightly different ways. |
02:50 | And we can use those depending on what type of design we're working on, what we want the properties to be for that. |
02:59 | So, but one of the key types of lattice structure that I want to talk about is called a TPMS. |
03:06 | And that's not what we're probably all familiar with, with that acronym being tire pressure monitoring system. |
03:13 | What that stands for is, bear with me here, triply periodic minimal surfaces. |
03:19 | So, these are some examples of those here. |
03:22 | But basically what this means, triply periodic means that it's basically a pattern that repeats itself in three dimensions and minimal surfaces. |
03:32 | When that term is used, this is basically the minimizing the surface area for the, how do you put it, the structure, I guess you'd say. |
03:47 | So, this is something that we'd often see in nature or natural structures. |
03:54 | And that is basically what ends up leading to that minimal weight as well. |
04:01 | If we can reduce the surfaces, we're reducing the amount of material used and that reduces the weight. |
04:12 | So, these are some more examples of different types here. |
04:16 | These swars, ones that we'll commonly see, and there's P for primitive, D for diamond. |
04:25 | I think this might be a kind of split primitive here. |
04:29 | This is a diamond example. |
04:31 | And there's H as well, which I can't quite remember what that one stands for. |
04:35 | Or we'll also see this gyroid one here as well, which if you're familiar with 3D printing already or done a bit of work around modern CAD software, you might have seen this gyroid come up specifically in the infill for 3D printing. |
04:54 | But I'll show that in just a moment. |
04:57 | I just want to jump into 3D printing and have a little chat about how this all relates to 3D printing. |
05:06 | So, I'll just leave that on the screen while I talk through this. |
05:11 | So, basically, if we're talking about these structures, I'm actually just going to jump back and to show those structures here. |
05:19 | If we talk about these structures and actually manufacturing them, that's where a lot of the kind of difficulty comes in. |
05:26 | So, if we think about the traditional or more conventional style of manufacturing, especially with automotive parts, subtractive manufacturing, so that would be things like machining on a CNC mill or a lathe or more traditional methods like casting, injection molding and so on like that, you can probably see how it's very difficult to manufacture these, if not impossible or extremely impractical anyway to manufacture these types of structures. |
06:00 | The flexibility of additive manufacturing, basically the design flexibility that allows us to be able to create these structures. |
06:11 | And not only is it very easy and takes little time or no extra time for the 3D printer to do, it's also lighter weight, which is a lot of the reason for doing this. |
06:25 | So, it uses less material. |
06:27 | And one of the kind of core functions that leads to the price of our 3D printed parts is the material used. |
06:37 | So, this by nature is actually a way of reducing the cost, as opposed to something like subtractive manufacturing, where we start off with a raw stock or a billet, for example, generally making that part lighter is going to be more machining operations, more machine time, and it's actually more expensive to make the part lighter. |
06:59 | 3D printing or additive manufacturing is actually kind of the opposite way there. |
07:04 | Making a lighter part ends up being a cheaper part. |
07:09 | The other thing here is the main challenge around 3D print, sorry, the main challenge around these lattice structures comes down to the support in 3D printing. |
07:21 | So, we need these support structures to basically support the material so it doesn't break or fall and we can build it up as we are 3D printing. |
07:33 | In some cases, if these need support structures within these lattice structures, it basically becomes very difficult again and practical or impossible to remove the support structures from out of a 3D lattice like this. |
07:52 | So, we're just going to jump back over here to the 3D printers. |
07:57 | I'll start with this here. |
07:59 | So, the typical, if you're not familiar with 3D printing, the typical ones that we'd use in automotive design or the main ones that we see being used at the moment are FDM or FFF printers. |
08:13 | And these are the ones that you'd be most familiar with, resin and basically use light to cure a resin. |
08:42 | And it kind of generally builds it up upside down like this, but again, building up layers to create the 3D part. |
08:51 | Another alternative, that's not a very good photo I see now. |
08:55 | I'll just make that a bit bigger. |
08:58 | SLS 3D printing and SLM 3D printing or also MJF or DMLS, these are all powder bed fusion methods. |
09:09 | So, basically, I think the other photo might be a little bit better that I've got here. |
09:13 | Yeah, we have a very fine powder of the material and then generally by way of lasers and things like that, it'll sinter or melt the powder together in the cross section of the part and then again, build up layers as it goes. |
09:30 | So, SLS uses thermoplastics, thermoplastic powders. |
09:35 | MJF is the same, but generally it's just a nylon thermoplastics. |
09:40 | So, similar materials to our FDM, but a different type of 3D printing. |
09:48 | And then SLM and DMLS, they use metallic powders. |
09:55 | So, aluminum, stainless steel, different types of steels, Inconel, titanium and so on. |
10:01 | So, don't get the SLM confused with SLS in that case. |
10:08 | I just wanted to jump into BambooLab here. |
10:12 | We have BambooLab in 3D printing. |
10:39 | We don't have to print a solid part. |
10:42 | The part can have an infill density, so a structure on the inside of it to basically reduce the weight of the part and the material usage and so on. |
10:51 | So, I'm going to slice this in a second and show you what that looks like. |
10:55 | But down here, so we can set the sparse infill density to 10%, for example. |
11:01 | And then we can use all these different structures here. |
11:05 | And you'll see down here, there's gyroid and honeycomb and so on. |
11:09 | And some of these are essentially the latter structures that we're talking about. |
11:13 | So, not only are they used for the main structure of the part, but they can be used for infill, which is essentially the same thing in these 3D printing software. |
11:26 | So, if I just hit gyroid there, I'll just slice the plate and see what happens. |
11:34 | Hide these. |
11:36 | Slicing, basically, if you're not familiar with 3D printing, just slices the part up into the layers that it'll be manufactured in. |
11:43 | And then if I pull this down and I zoom in here, you can see this gyroid infill here being built up in the red. |
11:52 | So, that's an example of using these 3D lattices already. |
11:58 | And it might be something that you're already doing. |
12:00 | But we can actually use these in our designs as well. |
12:06 | So, the other thing before we move on from this that I wanted to talk about, basically, just be blown or dusted out with a paintbrush or blown out with compressed air. |
12:42 | So, it's quite easy in these methods to be able to create these lattice structures and not worry about the supports. |
12:50 | Generally, though, when we are 3D printing, for example, if we jump back into BambooLab here and we have enable support, we have this threshold angle. |
13:02 | And that's essentially the overhanging angle of the part at which point it's going to need to be supportive. |
13:09 | So, if we look at the side of these here, we can see perhaps that this angle must be less than 30 degrees because this face is not being supported. |
13:22 | Or more than 30 degrees, I should say. |
13:24 | So, somewhere usually between 45 to 30 degrees is the threshold angle. |
13:29 | And past that, we need the support, which is the green material here holding up the part. |
13:36 | In saying that, we can create designs that are self-supporting. |
13:40 | So, if you think about, if we just jump back and have a look at that lattice structure again, we can see that if this part here, for example, these diamond shapes are built up on 45 degree angles, then we're never going to have an overhang in the structure that's over 45 degrees, for example. |
14:05 | So, in that case, it's going to be self -supporting and it can be printed without using support material. |
14:12 | So, that's generally what we're aiming for when we're printing these parts. |
14:17 | We don't want to use these in motorsports use. |
14:41 | So, one example, one area that they use would be anything that needs to be stiff and strong, but very lightweight. |
14:50 | So, anything structural, basically. |
14:52 | And I have a few examples here. |
14:55 | So, some of these, I think, concepts for brake pedals. |
15:00 | Whether they're in use or not, I'm not exactly sure. |
15:03 | Again, I've just found these online. |
15:05 | So, we can see that's a brake pedal there, or maybe a clutch or accelerator pedal. |
15:10 | And it's got this very intricate lattice structure being used there. |
15:15 | And then I have another one as well. |
15:18 | I think some of these were concepts for use in F1. |
15:22 | Again, I'm not really sure if they're being used or not. |
15:25 | But the idea here is that we've got surfaces that we need to be used. |
15:31 | We've got holes for the hardware and so on to go through. |
15:35 | But we've got this very lightweight structure here. |
15:38 | And these are likely being designed with some type of simulation software as well to ensure that they're stiff and strong enough. |
15:45 | And that, of course, be physically tested as well. |
15:49 | I've actually got another design here just open in my Fusion, which is a little design I've been playing around with for an RX-7 strut tower brace. |
15:59 | So, in our FD RX-7. |
16:02 | It's got this kind of carbon fiber aero cross tube. |
16:06 | And then this will be a 3D printed aluminum mount here. |
16:10 | And then I've used some lattice structures in here. |
16:14 | I actually have a little example part that I'll show you a bit later on. |
16:20 | But we'll come back to have a look at this in Fusion soon. |
16:23 | So, again, it's just an example of making the stiffness that will be important for an application like this. |
16:44 | Let's just jump back to some more examples. |
16:50 | So, I actually didn't grab a photo of this. |
16:53 | But another example would be around fluid flow and heat exchange. |
16:57 | So, if you think about those TPMS or minimal surfaces, the surface design can actually be something that is manipulated of fluid flow. |
17:11 | I might have something here on this page, actually. |
17:16 | Well, maybe not. |
17:17 | Maybe in here. |
17:20 | So, we often see things, yeah, heat exchangers. |
17:23 | So, here you go. |
17:24 | This is an example of a heat exchanger. |
17:28 | I'm not exactly sure what for. |
17:30 | But we have fluid flow through this, through the different channels. |
17:35 | And it has this kind of gyroid structure in here. |
17:38 | And basically, this software is used to develop these lattice structures specifically for heat exchange. |
17:47 | And the idea is that you can get a much more efficient heat exchanger. |
17:53 | So, you can reduce the size of it significantly, make it smaller and lighter. |
17:59 | And if we think about heat exchangers for our cars like oil coolers, transmission coolers, radiators, and so on, intercoolers, that means if they can be smaller, they're also going to be less drag in terms of aerodynamics as well. |
18:16 | So, there's all sorts of different advantages to these lattice structures. |
18:23 | And the final one that I wanted to talk about, and it looks like they've got, yeah, a little bit of an image here. |
18:29 | This is on the nTopology website, which we'll talk about in just a moment. |
18:34 | But impact absorption here. |
18:37 | So, in this case, it's showing a football helmet. |
18:41 | But the idea here is that the structure can be designed to be able to absorb as much kinetic energy or impact energy as possible. |
18:50 | So, it can also be used in automotive designs for the likes of helmets and so on. |
18:56 | Obviously, that's probably not, it might be a motorsport helmet, probably not, some type of other helmet there. |
19:05 | But yeah, you get the idea there that it's also used for impact resistance as well. |
19:12 | So, if we just talk about software for a moment, I'll just jump back to this page here. |
19:17 | This is nTopology. |
19:19 | This is an area that's developing really, really quickly. |
19:24 | Some of this lattice structure generation is being built into our typical CAD software that we'd use. |
19:32 | For example, Siemens NX, SolidWorks, or DeSalt Systems also has some lattice structure generation in it. |
19:42 | Fusion does, that we'll have a little look at in a moment. |
19:45 | And it's all kind of in different capacities and different capabilities, I guess you'd say, around that. |
19:52 | Some of these software are a lot better than others. |
19:55 | There's some online cloud-based, browser and cloud-based ones as well. |
20:00 | Yeah, there's all sorts out there. |
20:02 | Some of them are free, some of them are paid. |
20:05 | This one here that I have on the screen, nTop or nTopology, is kind of like the gold standard for a lot of this stuff at the moment. |
20:14 | But in saying that, it is extremely expensive. |
20:17 | I think it's about 20,000 US dollars or 40,000, I can't quite remember, for a one -year license. |
20:24 | So, yeah, it's not something a lot of us are going to be using, but with all of this software, it's kind of a trickle-down effect. |
20:32 | And hopefully, eventually, we'll see this in a little bit more of a usable space that's a bit more accessible to all of us. |
20:42 | But yeah, nTopology is a good example here. |
20:46 | And I think if we just look under their software tab here, you can see that they have lattice structures, generative design, topology optimization, simulation, and so on. |
20:56 | And a lot of that can kind of be used together. |
20:59 | So, you can use this generative design to develop your lattice structure, for example. |
21:05 | And that's how you get the kind of most optimal system. |
21:08 | They're using this a lot in our jet engines and so on, heat exchangers and really complicated things. |
21:14 | But naturally, using it with additive manufacturing as well. |
21:19 | Cool. |
21:19 | So, I think that's covered that enough. |
21:23 | You get a pretty good picture of what's going on with these 3D lattices. |
21:26 | So, let's just look at a simple example here of actually using Fusion in this case, since it's just such an accessible software that a lot of us are probably using already. |
21:40 | And we'll just have a look at an example of using Fusion to do some 3D lattice work. |
21:47 | I'm just going to jump back in here. |
22:01 | Cool. |
22:02 | So, where is it? Gearbox map. |
22:04 | Here we go. |
22:04 | OK. |
22:05 | So, this is something that we actually posted about a while back. |
22:08 | So, I just wanted to show this image first, give a little bit of context to the model that we're going to be working on. |
22:14 | So, this is in our GT86, which we call the SR86 because it's SR20 powered. |
22:22 | And this is the back of our Hollinger six -speed sequential. |
22:25 | And we have this kind of fabricated transmission mount here on a bushing for the transmission. |
22:33 | A while back, we actually just threw this in our generative design software in Fusion. |
22:40 | And this is kind of mapping out the constraints, I guess, in this case with the obstacle and preserve bodies. |
22:47 | And then that spat out this kind of generative design version of the gearbox mount. |
22:55 | So, it was kind of interesting to compare the actual fabricated one, which was produced beforehand to what the computer. |
23:07 | What I've done in Fusion here is I've just made a really simple version of that, that would perhaps be machined out of billet aluminium. |
23:20 | So, we see in black here, we just have that kind of spigot or the end mount of the gearbox. |
23:26 | And then I've got the bushing on here as well. |
23:29 | And then the mounts to the transmission tunnel here and just a structure in between. |
23:33 | It's very simple. |
23:34 | I just whipped this up just before in a couple of minutes to illustrate some points here. |
23:40 | So, if we were going to go down the machining route for something like this, probably what we'd end up doing to remove a little bit of material out of this part and keep it lightweight is, for example, I'm going to have a profile in here. |
24:03 | We'd probably just do something like this. |
24:12 | And cut into the surface. |
24:16 | No, I'm doing the wrong buttons. |
24:18 | Bear with me. |
24:20 | Five. |
24:21 | So, pocket out the surface, something like that. |
24:26 | Sorry, that's a bit easy to see. |
24:28 | And do something like that, probably on both sides here, to remove some of the material and hopefully from areas that aren't going to reduce the stiffness or the strength of the part as well. |
24:41 | So, that would be a typical approach if we were going to be machining this part. |
24:45 | So, let's just have a look at the alternative being, if we're going to do some additive manufacturing. |
24:51 | And with all honesty, if I was doing additive manufacturing, I wouldn't really follow this general shape for the part. |
24:59 | I'd use a bit more of a flexible, not flexible, a bit more of a... |
25:07 | into the flexibility of additive manufacturing. |
25:11 | But this is just an example. |
25:14 | So, I'm just going to delete that feature that we just did here and step a few features forward here. |
25:20 | And just before I get into it in Fusion, actually, I forgot to mention, while Fusion is free for private use and relatively cheap for the professional version as well, doing volumetric lattices, which we have down here in Fusion, actually requires the design extension. |
25:42 | And the design extension is, I think, about $100 or $115 per month. |
25:50 | So, it's not exactly cheap. |
25:53 | There's a whole lot of different plans they have and ways that you can pay for that with cloud credits and so on to suit your needs. |
26:01 | But this is just an example. |
26:03 | And there's a lot of other software out there as well that can do the same thing. |
26:08 | This is just an example of how to create a lattice. |
26:11 | So, basically, what I've done here already is I've created these two bodies here, which are just cutouts of that same kind of shape we looked at just before. |
26:23 | And they're just, yeah, I've just made those separate from the actual body there. |
26:28 | And what we're going to do is we're going to jump into our volumetric lattice tool here and then set up some lattices structures for these bodies. |
26:39 | So, the first thing I do is I just select the body. |
26:44 | I can only do one in this case, I think, at the moment. |
26:48 | Yeah, we'll just start with one. |
26:50 | And then there's all these different settings that I have here. |
26:53 | So, let's run through them and talk about what they essentially mean. |
26:57 | And I'll just hide the outside ones. |
26:58 | It's a little bit easier to see. |
27:10 | Solidity, sorry, to 0.2 and keep that uniform for now, just so we can kind of see the structure a little bit better. |
27:18 | Let me jump back to the setup. |
27:20 | Maybe if I make that 10, it might be a little bit more clear. |
27:23 | Yeah, there we go. |
27:24 | So, let me go to 7. |
27:28 | So, here we have our cell shape set to gyroid at the moment. |
27:33 | So, it's this kind of lattice structure in that gyroid TPMS cell type. |
27:41 | But we also have some other options down here. |
27:44 | We have these basic cross setup, which I think is just a cubic. |
27:52 | Different types of cubics, they're calling XL in this case. |
27:57 | Swarz primitive here and diamond as well. |
28:03 | So, yeah, a few different types of cell shapes there that we can choose between. |
28:10 | So, we're just going to leave that as gyroid. |
28:14 | Oh, the other option down the bottom here is we can actually create a little 3D sketch as reference and use that to make our own cell structure as well. |
28:23 | So, that's a cool little tool if you want to get creative with it. |
28:27 | Proportions, we're just going to keep it all uniform for now. |
28:30 | So, it just keeps the kind of symmetric or same size in all directions. |
28:37 | Again, solidity there. |
28:40 | We can just change this depending on how solid we want the structure to be. |
28:45 | So, I'm just going to keep it at 0.2. |
28:47 | So, we can kind of see what's going on. |
28:49 | And we can also use this offset tool here. |
28:52 | So, what this does, if I select a surface. |
29:08 | So, for example, if I made the thickness of that 5, that just changes how thick that kind of offset is. |
29:20 | So, if I just go 0, for example, and then do the blend distance as 5, that'll blend it into from full solidity to that 0.2 solidity in 5 millimeters. |
29:35 | I could increase that or I could have the offset thickness as 1 millimeter. |
29:40 | So, I get 1 millimeter of full solid material just from that face. |
29:47 | And then over 10 millimeters, it blends it away as well. |
29:51 | And that can be a good way to kind of come around here and select all these faces. |
30:02 | And kind of blend that in, change that back to 5. |
30:07 | Okay, and then if I turn the body back on there, they need to be merged together, which I'll show you how to do in a moment. |
30:16 | But you get the idea there that that's created that lattice structure just in that zone. |
30:24 | Another alternative, and I'm just going to delete that and jump back a little bit here that you might be thinking about is to basically use a volumetric lattice on the entire part. |
30:40 | And we could reduce this again to 7, change this to 7. 0.2. |
30:47 | And then we can use the offset here to kind of offset it away from the features as well. |
30:54 | So, I'll just select a few. |
31:07 | You can select that inside surface. |
31:12 | And we can basically make the entire part like it. |
31:16 | And I'll make the thickness there as, say, 3 millimeters. |
31:21 | And then the blend distance, for example, is 10. |
31:25 | And we could also select some other surfaces of the part depending on how we wanted it all to look. |
31:33 | But that's another approach to basically using a lattice structure in the part as well. |
31:39 | If we wanted to then 3D print this, for example, we can't just export this volumetric model straight from here to a mesh because essentially it's not a solid model yet. |
31:56 | It's just this kind of intermediate model that Fusion uses. |
31:59 | So, we actually come to here, and we convert this volumetric model to a mesh. |
32:04 | Typically, we're going to use a high refinement if we've got quite a fine lattice structure. |
32:11 | And we can just hit OK there. |
32:12 | I'm not going to do it because it'll probably take 10 minutes or so in this case. |
32:17 | It just depends on your model and the computer. |
32:20 | But we'll skip over that. |
32:21 | But you get the idea there. |
32:24 | So, that's a quick and easy way to be able to use a lattice structure in a mechanical carpet. |
32:33 | But the thing I will say about this in the case of Fusion, while these can be good for certain projects, it is limited compared to some other software as well. |
32:47 | So, yeah, it just really depends on what you're working with people. |
33:08 | So, yeah, I'd be really interested to hear if any of you guys have looked into some software for this or have some other ways of doing it. |
33:19 | Because yeah, it's really something that's going to be used a lot more in the future and something to kind of stay on top of all of this. |
33:26 | So, yeah, it's really interesting and definitely worth getting familiar with. |
33:30 | So, just a little note before we wrap up. |
33:33 | I held this up at the start of the module. |
33:36 | I'm not sure if you'll be able to see it. |
33:38 | Just bear with me for a second. |
33:41 | You might be able to see it there. |
33:43 | So, basically what this is, is a little cutout section of the strut tower brace for the RX-7 strut tower mounts that I showed you earlier with that volumetric lattice there. |
33:57 | This has been 3D printed out of aluminium by a Chinese manufacturer in this case through the use of CraftCloud, which is basically a hub that links you up with manufacturers all over the world. |
34:14 | So, you can jump on CraftCloud, upload your model, select the materials that you want to use, the type of 3D printing and so on, surface finishes and all of that. |
34:24 | And then that will basically link you up with a manufacturer to be able to produce your part or give you an option in this case of about 10 manufacturers who might be able to produce it, their quotes for it, lead times and so on. |
34:38 | So, I didn't want to print the whole thing first because I was a little bit worried to be honest, that the manufacturer wouldn't be able to do it and the results wouldn't be that good. |
34:48 | So, I just did this kind of trial first to see what it would look like and it came out really good. |
34:54 | Obviously, if you're a manufacturer as well, just expect to pay for what you get I guess in some cases and there is a difference between those manufacturers that are quoting you $3,000 to do a part this size to those that are quoting you maybe $300 to do a part about that size. |
35:29 | But it is interesting to see that for those of us looking for more accessible options, this is looking pretty good. |
35:40 | So, yeah, and that's only going to get more accessible in the future as well. |
00:00 - Introduction to Lattice Structures
01:43 - Nature-Inspired Design and Structure Types
03:06 - Triply Periodic Minimal Surfaces (TPMS)
05:19 - Manufacturing Challenges and 3D Printing Advantages
07:33 - Support Structure Considerations
08:51 - 3D Printing Technologies for Lattice Structures
10:42 - Infill Patterns in 3D Printing
14:41 - Automotive and Motorsport Applications
16:50 - Heat Exchange and Fluid Flow Applications
18:23 - Impact Absorption Applications
19:17 - Software Tools for Lattice Design
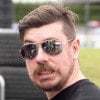