383 | Affordable 3D Scanning - Shining 3D Einstar
Summary
3D scanning isn't reserved for pro-level teams with big budgets. There are now many affordable 3D scanners on the market that we can use to get great results in our CAD projects. In this webinar we'll be looking at the scanning process using the Shining 3D Einstar, from setting up for the scan, taking the scan and then transferring it into our CAD software.
00:01 | Hey team, Connor here from HPA, welcome back to another one of our webinars. |
00:05 | This week we're going to be continuing on our little journey of looking at accessible 3D scanning options and today we're going to be looking at the Einstar from Shining 3D. |
00:17 | So, we're going to start by just having a bit of a look at the scanner, seeing what it's all about and then we're going to show you how to take a scan using the scanner, using the software that it comes with and then how to bring that scan into our CAD software and get set up to use that scan data. |
00:34 | So, we'll jump straight into it and we'll just have a little bit of a discussion about the scanner first. |
00:39 | So, the Einstar is something that if you've been looking at 3D scanners, especially in the enthusiast market, it's probably something that you've seen online or in reviews and so on. |
00:52 | Because this is probably the most popular enthusiast level 3D scanner and it's under $1000 now, started at about $1000 and it's decreased in price slightly so I think it's about $750 now. |
01:09 | Which is not the cheapest scanner that you can get but it is probably in the range of ones that are worth buying, it's probably one of the cheaper ones. |
01:20 | And it's been quite surprising how good it really has been. |
01:24 | So, this is a structured light scanner, more specifically it's infrared VCSEL. |
01:32 | So, which is a typical kind of scanning technology used in scanners of this price point. |
01:39 | At the enthusiast level but it's also something you can use at a professional level as well. |
01:45 | The resolution of the scanner can be adjusted anywhere from 0.1 millimetres to 0.3 millimetres. |
01:51 | They advertise this as the point distance but this is something I'm going to talk about in just a moment, resolution and accuracy and how those kind of relate. |
02:01 | Probably the biggest thing about using this scanner is the working distance. |
02:06 | So, it's got a working distance range from 160 millimetres, this is basically how far away from the part you need to be. |
02:14 | 160 millimetres all the way up to 1400 millimetres, so 1.4 metres, in that case way back there. |
02:21 | It does have an optimal range in there that you should be aiming for around 400 millimetres but that large field of view that it also has and the large depth of field makes it very easy to use. |
02:34 | It just basically means it's quite forgiving to the distance and as you move around an object and scan it, it's not going to keep stopping and starting because you're too far away or too close or whatever. |
02:47 | OK accuracy, this is something that I just wanted to discuss because Einstar actually seem to have stopped advertising or quoting their accuracy which I think is actually a really good thing because the accuracy, especially of these enthusiast grade or entry level grade 3D scanners is very misleading. |
03:10 | Basically, the accuracy that they advertise on many of the websites for these scanners is very high or it shows a really good accuracy and then when it comes to using the scanner to scan our parts in the real world, we're not getting anywhere near that because that accuracy is what they've been able to achieve in the best case in a lab environment, a super controlled situation. |
03:38 | So, you often see they use phrases when they're advertising their accuracy and it might be something like accuracy up to 0.1 millimetres. |
03:50 | So, they'll use up to there because that's the best they're able to achieve. |
03:54 | Or they will say something like 0.1 millimetres but that'll actually be at the smallest size part that they can scan because generally the larger part we scan, the worse the accuracy gets. |
04:11 | And in that case they might also express the accuracy as a percentage there as well to kind of show that. |
04:20 | If we just jump onto my computer here, Shining 3D actually have a few articles here. |
04:29 | So, the accuracy of the Ironstar and what you really need to know. |
04:32 | And I think this is actually quite a good look at it and it kind of compares accuracy and resolution here. |
04:39 | So, essentially if you're not familiar with this, resolution is the distance between the data points that the scanner gets. |
04:49 | And that could be, like we talked about before, point distance of 0.1 millimetres to 3 millimetres in that case. |
04:58 | So, each data point that it picks up might be 0.1 millimetres apart, in which case it's getting a lot of data points and a really fine resolution. |
05:05 | Or if it was 3 millimetres for example, they'd be a lot more spread out. |
05:11 | And that does have some relationship to accuracy which I'll discuss in a moment. |
05:15 | But accuracy is a completely different thing where it's basically the distance or the difference between the scanned value that we get and the actual real geometric value of the part. |
05:30 | So, for example if we scan an object, which we'll do in a moment, and the cylinder size here of the scanned data is significantly larger or smaller than the real thing, then our accuracy in that case is poor. |
05:46 | Because if we have a low resolution between those data points, we're essentially extrapolating or making guesses at what the object actually looks like. |
05:57 | We lose accuracy between the data points in that case. |
06:01 | So, that is somewhat of a way that resolution does affect the accuracy in some cases. |
06:07 | And you can kind of see by this image here how that works. |
06:11 | So, a high resolution, the scanned data and the real surface in these areas here is actually going to be closer to the real thing where for a lower resolution we're actually going to have more kind of discrepancy there so the accuracy actually does reduce slightly. |
06:31 | From my experience of scanning with the Einstar, I generally get an accuracy anywhere from within about 0.4 millimetres to about 1 millimetre, which is actually pretty good because some of the other entry level scanners you might be seeing a few millimetres and that's where they start becoming really not that useful for the type of work we do. |
06:54 | And it's a common kind of misconception I think that we need a crazy high accuracy of 0.05 millimetres, really metrology grade stuff to be able to do the motorsport design work that we do and that's not always the case. |
07:10 | For some applications, yes maybe, in other cases we can kind of tailor our approach and account for some of the discrepancies that we might have by slotting holes or just allowing for that tolerance basically. |
07:24 | But I'll leave it at that anyway and that's given you a little bit of an overview on the scanner. |
07:30 | So, what we're going to do now is just get it connected up and jump into the software and do a little bit of scanning. |
07:37 | So, this is probably one of the main drawbacks that I find with the Shining 3D Einstar is that it has quite a lot of cords required to connect it up so what I've got here is a power bank and then that kind of splits into two, connects to the USB on my computer and then connects to the Shining 3D. |
07:58 | Some scanners probably only need to connect to the USB port, some can be completely wireless as well. |
08:05 | It also takes quite a lot of power to run this. |
08:10 | I think I just closed that screen before. |
08:14 | For example in this case it actually, the recommended specs of the computer, it requires 32 gigs of RAM if you're working on a Mac which I am. |
08:23 | In this case I'm actually working with a Mac with only 16 gigs of RAM but it tends to get the job done pretty well unless we're working on something much larger which we might come back to if we have time in just a moment. |
08:37 | So, it's saying device is offline. |
08:40 | I think that'll reset. |
08:43 | Yep. |
08:45 | Device reconnecting. |
08:48 | So, go new project group and I'm just going to call this F820 block. |
08:55 | Test. |
08:57 | Cool. |
08:57 | And go confirm. |
08:59 | Alright, so this next one, this is typical when we're setting up a new project for 3D scanning, it kind of prompts us to fill in these boxes depending on what we're actually scanning and that kind of sets the settings of the scanner up to be suitable for whatever we're scanning. |
09:17 | So, object size in this case, saying a small object is between 100 millimetres cubed and 200 millimetres cubed and a large object is basically anything larger than that. |
09:30 | This is bigger than 200 millimetres cubed so we'll stick with medium. |
09:36 | The tracking mode or select mode of alignment, so that's aligning the frames that it gets as it moves around, we can do that with features, we can do that with markers, those little targets that you see around 3D scanners a lot and we can do that based off the texture as well. |
09:53 | If for example we're scanning something with art on it where there's not actually geometry features to it but there's a lot of texture and different colours, that can be helpful there. |
10:04 | In this case we're going to be scanning this engine block, we don't need to use markers, it's really feature rich so it has lots of geometrical features that the scanner can pick up on and use for tracking. |
10:17 | Scan resolution, so saying 2 millimetres in this case, I'm just going to drop it down to, we'll go 0.5, if we had the time we could probably go lower than that but because we're doing this all live we'll just keep it a little bit simple. |
10:32 | I might actually just, nah we'll leave it at 0.5 and just kinda see how we go. |
10:39 | Alright, down one, cool, confirm. |
10:42 | So, that's set up our new project and jump into the next window here, I have calibrated this previously so just like any measuring instrument which a scanner is, you need to calibrate them every so often. |
10:57 | That's all set up. |
10:58 | So, we have our kinda scan settings down the side here, working distance, range, because I'm scanning something pretty small we can keep this low so I don't include too much of the background. |
11:09 | It's going to pick up on plane detection and probably try to remove some of the table. |
11:15 | Data quality indicator, you'll see that as we get running and that's all looking pretty good. |
11:21 | So, in this case we can start the preview from over here or we can just hit the plus button, sorry the play button on the back of the scanner here and it's also got some lights which will kinda indicate the distance we need to be within. |
11:35 | So, I'm just going to get that started there. |
11:39 | And we can see the preview. |
11:41 | And essentially what we want to see in this little camera window onto the side here is this just faint red kind of glow I guess. |
11:51 | And that red just indicates that we have about the appropriate exposure time. |
11:57 | So, if I turn that down you're going to see that disappear. |
12:00 | And if I turn that right up it probably gets a lot of red. |
12:03 | So, we kinda wanna be somewhere in the middle. |
12:05 | We can also adjust that with the plus or minus button on the back of the scanner too. |
12:12 | So, yeah, pretty happy with that. |
12:13 | And then in our main kinda workspace here we can see if I move too far back so outside that 400mm range I lose it. |
12:21 | And then if it's saying too far in that case. |
12:24 | And then if I move back in we can see I can see it all again. |
12:29 | I'm picking up scan data and then if I move in too close it starts to disappear again. |
12:35 | So, yeah, we'll just get right about in the range and then I'll just hit the play button again. |
12:39 | And now we are capturing scan data. |
12:43 | And that data quality indicator that we looked at just before on the settings down the side is what we see there with the green and kinda orange colour. |
12:53 | So, green is where we've picked up a good amount of scan data from. |
12:59 | And the orange is kinda where we've got a little bit of data but not quite enough yet. |
13:06 | So, we're basically wanting to make the whole block go green essentially. |
13:13 | So, we're just losing a little bit of tracking there. |
13:17 | It is going to pick up my hand to some extent but that shouldn't matter too much. |
13:23 | So, we just wanna capture the block, all sides of the block from as many angles as possible. |
13:33 | And I'll just try to avoid getting my hand in it as I turn it around. |
13:39 | Might have to move out of frame a little bit to get that side. |
13:44 | Trying to avoid getting my hand touching the block. |
13:52 | And you can see, if you're not familiar with scanning, this is fairly, I would say, we're losing a bit of tracking in this case and that might be a little bit to do with the computer that I'm using not being quite powerful enough. |
14:13 | But otherwise this is reasonably smooth and we're picking up quite a lot of data quite quickly. |
14:20 | Some scanners, especially cheaper ones like this, takes a long time to work around and get the data. |
14:27 | So, you can see, I mean it picked up that side of the block in just a few seconds. |
14:32 | What I really wanna try to do is get up on top here and get a good scan down into the bores of those cylinders as much as possible. |
14:50 | Because what I'm going to do is take, bear with me one sec, is take a measurement of those cylinders soon and use that to determine the accuracy of our scan. |
15:06 | So, I just pause that, just start in the preview again and then I can just start it. |
15:12 | Are we picking up data tracking loss? No. |
15:18 | Ah, paused it again, sorry. |
15:20 | Start the preview, hit play and then we can start scanning again. |
15:30 | There we go. |
15:32 | Probably is just a little bit too far away I think. |
15:36 | But if we can get down into those bores, pretty good. |
15:45 | Yeah, cool. |
15:47 | Right, I'm pretty happy with that for now. |
15:49 | We could obviously spend a bit more time but I'll keep things moving along. |
15:55 | So, in here we just basically have our raw scan data and we can go around here and put a cutting plane. |
16:06 | So, the cutting plane method will just help us remove this table. |
16:11 | So, fitting point cloud, I think I should just be able to hold shift and click a few points on the table there and create a plane and then just drag that up a bit to remove, chop out a bit of that stuff. |
16:26 | I won't worry too much about potentially just getting rid of a bit of the bottom of the block. |
16:40 | So, we can kind of play around with that quite a lot, go apply and that'll cut off the bottom of the table there. |
16:45 | And there's all sorts of other tools in here that we can use to just remove data that we don't need because basically it's going to make things look messy and it's just going to slow us down when it comes to processing the data as well. |
17:01 | So, hopefully what we can do here, yeah. |
17:05 | If we just select a bunch of the block there, we should be able to expand that to the connected domain. |
17:15 | So, we've got everything on the block there, looking pretty good. |
17:20 | And then we should be able to invert that and then that basically gets everything else and then I can just go delete selected data. |
17:27 | That removes it and then I just have to apply that edit. |
17:31 | So, that's just going to go through and process that change and get rid of all that scan data and then we're going to move on to process that scan data into a mesh file which we'll then be able to bring into our CAD software. |
17:44 | Cool, so that's just a block there. |
17:47 | We could of course spend a bit more time tidying all this up but I'm not going to. |
17:52 | What we're going to do now is just generate a point cloud if it lets me. |
18:02 | Continue, there we go. |
18:04 | So, it's going to optimise and generate that point cloud. |
18:07 | So, basically now it's taking that raw scan data and it's going to kind of take all of that and create a point cloud out of it which is basically doing its best to get rid of any noise and stuff in there and just get the data points in their geometric position that it actually wants to use. |
18:27 | So, it does some filtering and so on in that to do that job and hopefully this doesn't take too long. |
18:34 | While this is going I'll just have a little bit of a chat about the scanner. |
18:37 | We bought this scanner, we actually also have kind of a more professional grade Peel 3D scanner. |
18:44 | And we bought this scanner and some other ones to have a look at scanners that would be able to efficiently scan larger objects. |
18:52 | So, scanning something like this isn't actually what the scanner's really good at, it's actually much better at scanning for example an engine bay or a body panel or something like that. |
19:03 | It does quite a good job of it because it's got such a big depth of field and field of view as well, it makes it quite easy. |
19:11 | So, it's not really tailored towards getting a highly detailed design like this and being really accurate. |
19:18 | But of course if we're looking at scanners in this kind of price range, we generally are going to want something that can do everything. |
19:25 | Being car enthusiasts, that might involve scanning an engine or engine parts or mechanical parts like this anyway. |
19:33 | So, yeah it's good to be able to use it for whatever we might be working on. |
19:40 | Just going to unplug it with kind of a hope that that's going to help to keep things moving along a little bit. |
19:48 | Just plonk it over here. |
19:56 | Here we go. |
20:02 | Don't reconnect, OK cool. |
20:05 | So, this is our point cloud now and then we can come into here and we can either just save the scan as it is or we can mesh the model. |
20:16 | So, I'm just going to go mesh model and then it gives us some parameters to set up for the mesh. |
20:21 | So, I don't need a watertight model in this case so watertight is basically where it seals all the holes so you imagine if there was water inside the mesh body then it would be watertight. |
20:33 | But in this case we're not going to be too worried about the holes. |
20:38 | We'll just do the standard filtering, standard smoothing. |
20:42 | Remove any small floating parts, there shouldn't really be any because of the work we did before. |
20:49 | There's a little one down there though. |
20:51 | Simplification, I'm just going to go yeah max triangles on this to a million because I know my computer can kind of handle that. |
20:58 | If this doesn't make sense to you, this talk about meshes and triangles, I'll explain that in just a moment. |
21:04 | But this is all looking pretty good so we're just going to kind of go with the standard settings, it wants me to preview it first. |
21:12 | So, yeah I'll talk about those mesh files while we're at it. |
21:15 | So, what a mesh is, if you're not familiar with it, it's the type of file that our 3D scanning software ends up giving us that we can, I'll just confirm this now, work with in our CAD software, although we'll come back to that in just a moment because it's not that straightforward. |
21:34 | But it's a common file that's used in 3D scanning and also in 3D printing as well as some other things. |
21:40 | But basically what it's doing is a mesh is breaking the model or the surface of the model down into lots of tiny little elements. |
21:48 | So, in this case, depending on the mesh file we use, if I zoom right in here, you can kind of see it's tessellated so there's all these little triangles here to make up the surface of the part and that's kind of defined, their size is defined by the resolution of the mesh. |
22:08 | So, the finer the mesh is, the smaller the triangles, the higher the resolution and in some cases, as we now know, that has an impact on the accuracy as well. |
22:18 | But basically this part is made up of lots of little triangles to form this mesh. |
22:26 | And when we bring that into our CAD software, there are some considerations around dealing with that type of file as well but we'll get to that in just a moment. |
22:36 | So, after we have this mesh, we have these different mesh editing options here so we can work with this and tidy it up a lot. |
22:45 | As you can see, I've just kind of taken a quick scan here and it's not the best, I would say. |
22:51 | There's definitely some issues with it. |
22:54 | So, I'd probably retake this or you could spend a while going around and auto -filling holes or manual-filling holes, for example. |
23:02 | If you jump in here, we could patch a hole like this up and it'll do its best to kind of match the surface and in that case, it looks like it's done a pretty good job and confirm and then, yeah, that's patched that hole. |
23:16 | So, you can, ideally, you want to be picking up all the scan data you can but in cases where you can't get it all, you can go back and patch holes and tidy up the mesh like that. |
23:28 | To move on, so what I'm going to do is not use any of these. |
23:38 | Texture remapping, show high texture, model display. |
23:42 | So, we're just going to jump onto this. |
23:44 | Oh, that's not the tab I wanted. |
23:46 | Exit model display. |
23:52 | Ah, measurement. |
23:53 | So, I'm going to just jump onto this next measurement tab here and we're going to do a couple of things here. |
23:59 | So, when we're working with our scans, if we can align them with our coordinate system within our scanning software, that's always the best way to go because basically, as we bring it into our CAD software, it's always already going to be aligned. |
24:12 | So,metimes with these more basic systems, the alignments in the software aren't that good so I'd rather do it in the CAD software just to be sure that I've got everything how I want it but as a more professional kind of level scanning software, it's always best to align it in the scanning software. |
24:30 | The software is designed to work with this type of file and it does a really good job at it. |
24:37 | It's best to always align your scans with the coordinate system because as you come to design around it and just use that file, it makes it a lot easier if you're working with a scan that's kind of on a weird angle or something like that. |
24:50 | When we're working with those modeling tools in our CAD software and we're trying to align something up with vertical and so on, and we can't, it just slows down the whole process basically and makes aligning multiple parts difficult as well. |
25:03 | So, if I click this align feature here, there's some kind of alignment tools where we can drag it. |
25:11 | We can do a quick alignment and kind of drag it into the position we want or a precise alignment, same kind of idea there. |
25:19 | Or we can use this 3-2-1 system alignment which is the technique that I usually like to use and basically what that means is 3 -2-1 is three points which define a plane and then two points which define a line and then one point being the final point. |
25:36 | And if we use that then we can define the location or alignment of our scan in three dimensions. |
25:42 | So, basically what this wants is a constraint plane, a constraint line and a constraint point. |
25:49 | And to create those we first need to exit out of that and create these features. |
25:54 | So, if I create a plane feature from here, I can use different options for doing that. |
26:01 | I'm going to use this three point fit option here. |
26:06 | Basically, then if I select three well -divided points on the top kind of head gasket surface here, so one there, one there and we'll get one over here. |
26:19 | Then that's going to fit a plane through those three points on that surface and it's good having them well-divided like that because we get quite an even and accurate level of that surface. |
26:29 | So, I'll go create and that's made that plane. |
26:34 | And then I'm going to use this line feature and I'm going to do point-to -point. |
26:39 | So, basically this is now just two points to make a line. |
26:44 | And let's see if we've got something that we can kind of pick up on here. |
26:49 | Sometimes we can use an edge. |
26:58 | Yeah, I might use... So we really want a line that runs perpendicular to this plane. |
27:08 | Yeah, I might just pick up on like the edge of the block here to here. |
27:15 | So, we know that's kind of a straight line. |
27:18 | Go create and then finally as a point, just something in the middle of the block works pretty well here. |
27:27 | So, yeah, I might even just have a point in the middle here. |
27:30 | Select method, select points, bang a point there, go create. |
27:36 | Cool, and then we'll close that, jump back to the alignment tool, 3-2-1 system, plane one that we created, line one that we created, and point one, go align, and we can see now that that has aligned the center of the block with that coordinate system on the head surface there. |
27:56 | And we can flip those around and everything as well. |
27:59 | So, yeah, negative Z, that should be all right, but we can change the kind of alignment of that as well. |
28:07 | Align, cool, close. |
28:09 | So, now we've aligned that. |
28:12 | We can do some measurement work in here as well. |
28:16 | So, for example, just basically measuring between two points in this case. |
28:24 | If I collect a point on the cylinder wall there, that's not a very good one, I'm just going to start that again. |
28:31 | If I collect a point on the cylinder wall there and then a point kind of opposite it on the other side, we could essentially measure across the bore. |
28:44 | That's obviously not a very good one, but it's not too far off to be fair. |
28:49 | But it's not a very good example, but basically we can measure, take measurements off the scan and kind of ensure that it's around the correct scale at least to the part. |
29:01 | But we'll take another measurement inside our CAD software which will be more accurate in just a moment and then we'll compare that to the actual measurement from the block to get an idea of the accuracy that we've got. |
29:12 | So, let's wrap up there and we're just going to go save our scan. |
29:17 | I'm just going to save it to my desktop in this case and I'll just save it as an STL mesh file rather than an OBJ or any of these other ones here. |
29:26 | STL is just a very basic one and that'll be perfectly fine for a part like this with no kind of color texture or anything like that. |
29:33 | So, I'll hit save, that's done that, and from here I'm just going to close this EXSTAR software and get into my Fusion software. |
29:49 | Cool, so now we're in Fusion. |
29:53 | We use Fusion at HPA but you can also do all of the same work and the likes of SOLIDWORKS and so on. |
30:00 | Fusion is actually just really good and well tailored to working with 3D scans. |
30:05 | So, I'm just going to start on this mesh tab here because that's what we're working with and I'm going to insert a mesh file. |
30:12 | Select from my computer, I know it's on my desktop. |
30:15 | I think I just saved that as scan STL. |
30:18 | Yep, that's the one, go open. |
30:22 | And that's plonked that in there and we can see that that's already aligned with the coordinate system as we set up in our scanning software just before. |
30:32 | So, that's looking pretty good. |
30:34 | I'm just going to go OK and now we have our scan in our CAD software and it just kind of applies this color because of the settings that I've got so it's a little bit easier to see. |
30:46 | So, I'll just basically show you a simple approach to getting this scan kind of set up so we could use it perhaps in designing some parts to go on this or assembling it with other engine parts. |
30:59 | For example, if we scanned the cylinder head and we wanted to align those two scans together. |
31:06 | So, what I'm going to do is create a few features here and what I first want to do is I could rely on this being the kind of correct plane for the head gasket surface because that's aligned with our origin planes there or I could create a new plane on that surface but you'll notice that if you try to do this infusion using the plane through three points tool here, we can't actually click the surface of the scan to do this. |
31:40 | We actually have to jump into this create forms toolbar as a little kind of trick and then we can do it from there because it kind of just changes the type of data that it's looking for. |
31:50 | So, same thing as before. |
31:53 | I just trust Fusion a little bit more than the scanning software so I'm going to click three well-divided points on that plane and you can see that's applied a plane to the surface and it looks pretty good like it's matching the scan data. |
32:07 | Go OK. |
32:09 | I'll finish that form. |
32:10 | Now, we have this plane. |
32:12 | So, the next tool is one that I find probably to be the most important infusion and something I use all the time when working with scan data and that's this create mesh section sketch tool. |
32:25 | So, basically what this does is if I select a body and then a section plane being the one we just created it will basically create a profile of the intersection between that plane and the mesh body. |
32:40 | So, if I drag this down 10 millimeters like that it's a little bit hard to see but you see these kind of orange lines here are the profiles that it's cutting through and it's actually cutting those through the cylinders right there and because we know the cylinders are obviously perpendicular to the head surface we can be fairly confident that they're going to be cut directly through and give us nice circular sections. |
33:13 | So, what I'm going to do in this case is just hit OK. |
33:17 | We'll chuck that body back on. |
33:19 | We'll hide the construction plane for now and then this gives us two features on our timeline. |
33:24 | So, we have this mesh section feature but it also gives us a sketch. |
33:28 | I'm going to right click and I'm going to edit that sketch. |
33:32 | I'll hide the body so we can just kind of see that profile a bit better and then this is the second kind of trick to using this tool is coming to this create tab here and going fit curves to mesh section and then this will automatically fit in this case circular curve to the mesh section so based on that profile it'll do a best fit circle there and also do one to that one there as well and in that case that second one's got a bit of deviation I know but the first one looked pretty good and then what I'm going to do is measure that bore essentially. |
34:10 | So, that's giving us 87.32 millimetres and this is going to give us an idea of the actual accuracy of the part so bear with me now anyone out there who's worked on engines and is an engine builder is probably going to cringe. |
34:24 | I know this isn't the right way to measure the bore of a cylinder but I didn't bring the right tools over so it is what it is. |
34:32 | That looks like it's this cylinder here. |
34:36 | Turn this around so I can see it and I'm going to measure across there and that's giving me 86.3 millimetres bang on the dot and I'm just going to measure the other one as well. |
34:51 | That's giving me the same measurement, 86.3 millimetres. |
34:54 | So, we can see in that case that we have a one millimetre difference so our accuracy in that case is one millimetre. |
35:03 | So, that gives you a kind of idea for how if a scanner like this might have advertised 0.1 millimetres, that doesn't mean we're always going to get that, if we've just done a quick simple scan like that this is what we're kind of working with. |
35:17 | So, we've got one millimetre error in that case but we'll move on anyway and basically now that I've got these two features I'm going to use those to create a bit of a better alignment if I wanted to bring this into another assembly. |
35:34 | So, what I'm going to do is just make that other one equal to it and then I'm going to lock the position of these two circles so they're fully constrained and then I'm going to start by just drawing a few lines to make, essentially map out a coordinate system. |
35:54 | So, if I draw a line between the centre of these two then what I can do is turn on this 3D sketch preference here and I'm going to draw some more just construction lines, one from the centre here so this little triangle indicates the centre point, I'm going to select the active plane as one of these vertical planes and I'm just going to drag that up to be in vertical alignment shown by this constraint here and then select that point again and then just draw a line out horizontally and then use the perpendicular constraint just to make sure that's perpendicular in both of those cases and we can just set all of these as equal as well, equal length so everything's fully constrained there and we have this kind of coordinate system that I'm just realising I'm going to delete and just change a little bit so bear with me because I just realised that's actually 10mm further down on the head surface so what I'm going to do is further down than the head surface but I want to create the alignment on that head surface plane so I'm going to jump back in here, I can show the body again and I'm going to sketch on the head surface, I'm going to project those two points that I know are in the middle of the cylinders and then I'll just hide that other sketch that we created before and then I'm going to do the exact same thing and now I just know that it's aligned with the surface of the head there so midpoint along that line, get a vertical plane, pop that up and then same thing here in this case, just pull that out, little bit hard to see, okay and perpendicular constraint to that line and that one, that goes all white so it's fully constrained and I want those endpoints to be constrained as well, cool, happy with that. |
38:13 | Now, we have that coordinate system in the centre of the block, I can save this and I'll just call it FA20 block, just want to change the location of this, bear with me for a moment, FA20 block, save that and then if I was to create another design, when we're working with multiple parts, it's always best to basically have those represented as individual parts. |
38:51 | If they're going to be an individual part in the real world, then in our CAD software we should bring them in as individual parts as well so we can control the relationships with movement or location at least relative to other parts and it just helps keep everything kind of nice and tidy. |
39:10 | So, what I'm going to do is just find that other part we just had, I'm going to right click and I'm going to insert it into the current design. |
39:22 | Cool, I'll just go OK in this case, I'm just going to edit it because I forgot to do one thing on that and that is use the plane through three points tool here. |
39:33 | So, we know we have this construction plane but we also want a plane through this one and then another plane here through these three points and then finish it in place and then I know this is grounded to this so I can't actually move this but I actually want to unground it for a moment and then I'm going to go modify, align, component because this is a new component in this assembly and I'm going to turn on the origin for this actual assembly. |
40:14 | I'm just going to actually first just pull this out of the way, turn on the origin, pull it out of the way a bit more and then go modify again, align, I'm going to align these planes with our coordinate system here. |
40:29 | So, just like that and like that and we have now those three planes which I'll just hide, aligned with our coordinate system for our actual assembly here and we can capture that position and we can come back into here and we could create a rigid group between this and the actual component we're working in or we could just ground this to parent and update the initial position so it's in the correct position there. |
40:58 | And then basically now we have our engine block aligned in a new assembly and if we were working with a cylinder head for example, we could basically pick up on the same features on the cylinder head and then bring it in, align it with this and know that they're in perfect alignment or as close as our 3D scans will allow us to do anyway. |
41:17 | So, that's just also a little bit of an alternative way of aligning a 3D scan with your workplace coordinate system in your CAD software if you don't have the ability to do that in your 3D scanning software. |
41:31 | So, yeah, I'll just basically leave it at that and I forgot to mention if you had any questions or still have any questions, please jump in the chat and ask them now and I'll do my best to kind of answer them. |
41:43 | So, I'm just going to jump over to those and see if there's anything there. |
41:48 | Bear with me. |
41:51 | Alright, looks like we've got quite a few. |
41:54 | Mr Corn, "How does the scanner compare to the Creality one?". |
41:58 | So, we actually had a Creality CR-Scan Otter that I got because it's kind of similar to this in a lot of ways and the Creality one was actually really good and I found this one a lot easier to use and easier to catch data and the software it has is better as well. |
42:18 | The Creality scanner I found actually when measuring engine blocks like this I actually found it to be a little bit more accurate than using the Shining 3D Einstar and that wasn't using this method of checking accuracy it was actually using a software package called I'm blanking on the name now Geomagic Design X which is kind of like a gold standard of 3D scanning or mesh reverse engineering software. |
42:47 | So, I'd say the Creality ones are actually pretty good as well it just depends on what you're working with. |
42:52 | The Creality Scan Otter also has I think two separate two separate lots of cameras on it so it basically is really flexible in that it can scan small parts quite well maybe better than this and it can scan large parts as well but this one's really good if you're trying to scan the side of a car or an engine bay or something like this I'd probably pick this. |
43:14 | Overall the Einstar would probably be my choice, but that Creality one is pretty good as well I'd say. |
43:20 | I haven't got to try any of the other Creality scanners or the new Einstar ones either so I can't comment on those. |
43:30 | Hicks Design "I notice you've got a Mac have you had any success on Windows with the Einstar it seems to be badly coded and often crashes development seems to have stopped too.". |
43:41 | Yeah, so I'm working on a Mac now and that was kind of a recent addition that well not recent but initially when we got the Einstar you couldn't use it on the Mac it didn't have a Mac software option so initially I was using it on our Windows laptop I actually didn't have any problems with it on our Windows laptop and the Windows laptop we had was more powerful than this Mac so it probably worked a little bit better as well. |
44:07 | Yeah, I'm not sure I can't comment on that development as well I wonder if the new Einstar Vega is using the same EX-Star software that this is and if so I'd be surprised as well that the development has stopped but I will say that the EX-Star software compared to the other kind of budget 3D scanners I've used tends to be a bit better it allows you to do a little bit more of the stuff that you can do in more professional level software. |
44:37 | Same Hicks Design "I've been trying to use it on a Dell 7670 can load an entire car into NX or Catia but fails miserably with EX-Star.". |
44:53 | Yeah, honestly I can't comment too much I'm not really clued up with computer specs and stuff as well so I'll probably just embarrass myself if I get too far into that. |
45:05 | I will just say the power kind of and processing requirements of the Einstar stuff is greater than for example the Creality stuff so maybe that's just something to consider as well I'm not sure exactly why they're so kind of hungry for power but they are. |
45:23 | Tiger Brown "How much does this go for?". |
45:27 | I closed the page before but I think they're at 750 or about 800 US dollars now when we bought it earlier on it was 1000 US dollars. |
45:39 | Tim F "How does it go for a full car scan or can I do some aero work?". |
45:45 | Yeah, so it works really good for scanning a full vehicle it does it quite quickly in fact we have a kind of more professional level PL3 scanner and if I was going to scan an entire car I would probably choose to do it in this just because it would be so much faster it definitely won't be as accurate not even close so that's just something to consider the only thing is if you're going to scan a whole car then you just need a computer that's capable of processing that in my case I could probably scan maybe a quarter of a car or maybe half it depends on the vehicle and then it starts getting quite a lot of work for my computer to process those scans but it's definitely doable and this scanner will actually scan it really quickly and efficiently so in terms of being a budget scanner really good for that stuff. |
46:38 | Philly Phil "So, what's the spec on that 14 inch MacBook Pro besides having 16GB of memory is it a M1 or M3?". |
46:46 | I'll just bring up just jump back here about this Mac here so Apple M2 Pro 16GB there you go hopefully that shows you a little bit more but yeah 16GB of memory M2 Pro so yeah I'm not sure too much on the other details I won't jump into it too much but to be honest in terms of most of the CAD stuff I do and dealing with these scans even though it's not up to the recommended one from Shining3D it actually does a really good job so yeah it's been fine for me and I use CAD every single day cool let me just jump back to my notes. Ian Campbell Just got to Ironstar 2 weeks ago; I have so much to learn do you guys have any great tips for scanning the underside of my BRZ my 32GB RAM and my PC doesn't appreciate doing it in one scan." So yeah, you can definitely do it in multiple scans and then use some of the kind of alignment techniques that I just did before to bring those all together that might be an option you can also bring them all in into one file and then kind of merge those mesh files together after you reduce the size of the mesh it's just really when it comes to dealing with the large raw scan data that it struggles but once you can mesh that and then reduce that mesh and remesh it and so on it gets a lot easier to deal with the scan data. |
48:18 | If you're looking for any other tips and that kind of brings me to the end here anyway if you're interested in learning any more of these skills then I'd just say to check out our 3D scanning course there's a whole lot of information in that course about doing all of this work and much much more from reverse engineering and scan based design and just working with scans in general and kind of the best practices you can follow to get the best results and you deal with those mesh files which can be quite tricky; so yeah hopefully that's given you some insight into an accessible 3D scanning option and thanks for joining us today and we'll be back next week with another webinar so we'll see you then. |
01:12 - Scanner Specifications and Technology
02:54 - Accuracy Discussion and Considerations
05:52 - Scanner Setup and Connection
08:15 - Scanning Configuration and Settings
10:10 - Live Scanning Demonstration
16:18 - Post-Scan Data Processing
21:12 - Understanding Mesh Files
24:30 - CAD Software Integration
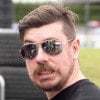