222 | Pro vs Club Level Harness Construction
Summary
While we probably all love scrolling through Instagram feeds full of concentrically twisted motorsport wiring harnesses featuring ultra-expensive Autosport connectors, the reality is that this sort of harness might be expensive overkill for your application. In this webinar we’ll discuss the differences between a club level and pro level harness, what materials and costs are involved, and find out why you’d choose one over the other.
00:00 | - Hey guys, Andre from High Performance Academy here. |
00:02 | Welcome along to another one of our webinars and today we're going to be discussing the topic of wiring techniques or more specifically we're going to be comparing the sort of techniques, the sort of tools and materials that are used when we're comparing between the likes of a club level or street level wiring harness and those that we see that are more familiar or more commonly seen in proper professional racecars. |
00:27 | Normally these are referred to across the industry as Mil-Spec wiring harnesses which is a term that is so misused that we try and stay away from it wherever possible. |
00:39 | While yes a lot of the components do in fact have a military specification, so that term isn't necessarily out of place, we find it's a lot easier to refer to these as professional motorsport wiring harnesses. |
00:52 | So, in this case, I've got a couple, or one of each so here we've got our professional motorsport wiring harness. |
01:00 | Pretty commonly seen with the Autosport bulkhead connectors. |
01:03 | Don't worry we're going to be having a look at that in a little bit more detail shortly. |
01:07 | And on the other side of the bench, we've got our club level wiring harness. |
01:12 | And on face value other than the lack of Autosport connectors, it can be a little bit hard to pick one from the other at a distance but we're going to jump in and find out what's actually involved there. |
01:23 | As usual we are going to be having questions and answers so if there is anything that you'd like me to talk in a little bit more detail about or anything just generally related to this topic, please ask those in the chat and the team will transfer those through to me at the end. |
01:39 | Now I think this topic, first of all, needs to be discussed because with the advent of social media and a lot of the poeple who are building professional motorsport wiring harnesses having a really popular following on the likes of Facebook and Instagram, it can be sort of common now for home enthusiasts just getting interested in wiring, just getting interested in modifying their cars, thinking that they're going to need to be shelling out thousands on a professional motorsport wiring harness if they've got any chance at all of their car performing how they want it to. |
02:13 | We're going to find out that that may not strictly be the case. |
02:17 | And really when it comes down to choosing between these two construction techniques, there are a few different areas that they differ but I want to start by actually discussing why we would move away from a factory wiring harness in the first place. |
02:33 | Now if you are building a purpose built racecar and you're stripping the thing completely bare, well this is a no brainer. |
02:40 | Chances are that you're going to be stripping out all of the existing wiring, maybe you don't even need headlights and tail lights in the car, maybe you're changing the ECU so that would obviously be a case where there's not a lot of point working with the stock wiring harness. |
02:56 | By the time you peer down that stock wiring harness to remove everything that isn't necessary and then modify what's left to suit the components you're going to be working with, you're probably actually going to save yourself time and money by simply starting from scratch. |
03:11 | On top of that, you're going to have the potential to gain reliability and save yourself some weight. |
03:16 | The more common aspects though would be let's say we're looking at a club level enthusiast, someone even just building a street car for themselves and with this sort of application the most common option would be to start with a factory car that's already running. |
03:32 | Let's say perhaps an aftermarket ECU has been installed, perhaps an engine swap has been performed or maybe a turbocharger's been added to a factory naturally aspirated engine. |
03:42 | So in this instance what we find is that most of the factory wiring harness in the car is actually still going to be absolutely fine, particularly what I refer to as the body harness. |
03:52 | So this is for the likes of the headlights, the indicators, maybe the gauge cluster, tail lights, fuel pump et cetera. |
04:00 | Probably most of that's going to be fine but what we will probably find there is that there's no real way of utilising that factory wiring harness to wire up to our engine so in this case, we need to do something that's going to interface between the factory existing body harness and our new engine harness that we're going to make up, probably chances are we'll also be adding in an aftermarket programmable ECU there. |
04:25 | So at that level this is where we'd be perfectly suited to our club level harness construction techniques. |
04:33 | And really when it comes down to it, what we're trying to do, regardless of whether we're building our street level car, our club level racecar or a professional GT3 style racecar, is we're trying to aim to reduce the weight of the car through the wiring harness and that might seem a little bit futile, it might seem like when you look at the overall weight of the car, the harness is not that big of a deal but when every little bit counts, you can actually be quite surprised how much a complete factory wiring harness from a car does add. |
05:04 | We've also got the simplicity to consider and this is something that I think is often overlooked. |
05:11 | Particularly in the heat of battle where we may have a wiring fault, god forbid, but it does happen. |
05:17 | Being able to diagnose and fault find that wiring fault very quickly in the pits is critical to get the car back out on track. |
05:24 | And sometimes the complexity of a factory wiring harness can be a little bit tricky without all of the factory documentation to go through and find. |
05:31 | When we're looking at either a club level or professional motorsport wiring harness purpose built for the car, often it's going to be much much simpler than the harness that it replaces. |
05:42 | The layout of things such as fuses and relays or power distribution modules if you're going that way, again much easier to work out exactly where everything is and if you've got your own documentation that you've created again, just makes it that much easier to figure out exactly what's going on. |
05:59 | The other aspect when we are moving away from a factory wiring harness and making our own, again regardless of technique is it gives us flexibility in the design. |
06:09 | Maybe we've got a factory car where the ECU is fitted in the engine bay, pretty common with modern cars these days. |
06:15 | But if we're swapping to an aftermarket ECU, there's a pretty good chance we're going to want to mount that inside the cabin where it's going to be more protected from heat, more protected from moisture and dust ingress as well. |
06:27 | Just basically giving us the flexibility to lay out the components wherever we want through the car is quite important there. |
06:36 | The other aspect, I've kind of touched on reliability there in terms of being able to fault find problems. |
06:42 | But the other thing that's really easy to overlook is that with factory wiring harnesses or more specifically the connectors that are used on factory wiring harnesses, they're not designed for multiple removals and insertions. |
06:55 | So realistically when the OE manufacturer produces a car, they're not expecting that you're going to be working on that car every weekend, removing the engine, refitting it, and you'll find that a lot of those connectors are only rated for something in the order of maybe 50 insertions and removals. |
07:13 | So what happens there is over time when you're constantly removing your wiring harness from the engine and refitting it, some of these connectors lose their drip or their bite so this can cause all sorts of really frustrating reliability issues with maybe a misfire for example where a connector to an ignition coil comes loose. |
07:35 | So going to a motorsport style wiring harness or club level style wiring harness with more reliable connectors, or techniques to get around those common problems does make things a lot easier. |
07:47 | We've also got speed of servicing so this really is more related to our motorsport, professional motorsport wiring harness. |
07:54 | So if we just have a quick look under our overhead camera for a minute. |
07:57 | So this is a plate that's going to mount on the firewall of our FD-RX7. |
08:03 | And on the far side of this, this is where our harness is going to go into the cabin to our ECU. |
08:10 | But the benefit of using these Autosport connectors despite their cringingly expensive price tag is that with a simple half twist, we can then remove them from that bulkhead connector. |
08:22 | Now what that means is that it makes it a lot easier for us to service the car in the pits. |
08:28 | So what I'm getting at here is particularly professional motorsport level, engine failures aren't unheard of and with teams that are at that professional level, the chances are that they're going to probably have a spare engine sitting in the transporter and that spare engine probably already has a wiring harness attached to it. |
08:47 | So to aid in terms of speed of the engine swap, the mechanics will simply disconnect the wiring harness at that bulkhead connector. |
08:53 | They don't need to worry about taking the harness off the engine and then they'll simply swap in the fresh engine, all they need to do then is reconnect those two bulkhead connectors and the engine's electrically ready to go. |
09:06 | So that speeds things up dramatically. |
09:08 | The other aspect as well and let me just get another couple of these connectors under our overhead camera here. |
09:16 | So we can see that we've got little labels here, a little bit hard to see but this one is an ignition interconnection and this one here is a fuel interconnection. |
09:26 | So we've got two Autosport connectors. |
09:28 | And you'll see that they've both got different coloured bands on them. |
09:31 | So first of all, the labels here, this means it's really easy for a mechanic or technician working on the car at a glance to see exactly where that specific connector is going to go. |
09:43 | Normally these are labelled so that most people can at a glance figure out what that connector is for. |
09:49 | Then on top of this, because we have different colour bands, this relates to the keyway on that particular Autosport connector, it's physically impossible for the technician to connect for example, the fuel sub harness to the ignition sub harness, making sure again reliability and human error more specifically is taken out of the equation there. |
10:10 | So that's probably a quick run down there of some of the key differences between at least initially our factory wiring harness that we see on our stock standard road cars and some of the reasons why we would choose to modify that harness in the first place, move to either a club level harness or a professional motorsport wiring harness. |
10:33 | At this point we're going to now start talking about some of the differences between these two harnesses and obviously get towards why you would decide to choose one over the other. |
10:42 | And what I want to do is actually start by talking about the type of wires that are used in motorsport wiring or just automotive wiring in general. |
10:50 | And this is something I actually do in one of our wiring webinars quite frequently so we'll head across to our macro camera and just show you the three different wires here. |
11:00 | So, first of all, we've got our black wire which is our PVC insulation. |
11:07 | So this is something you're likely to find from your local auto parts distrubutor. |
11:11 | Basically used for some hookup wiring, not something that we're going to want to use which we'll talk about in a second. |
11:19 | In the middle in red, we've got our TXL wire and then on the far side we've got our Tefzel wire. |
11:26 | So the differences between those, obviously there we can see the difference in the outside diameter of the wire, that's really apparent. |
11:34 | However, what may not be quite so apparent is despite the difference in the outside diameter of those three pieces of wire, the actual wire itself, the cross sectional area of the conductor area of the conductor strands is exactly the same. |
11:47 | All those three pieces of wire there are what's referred to as 20 gauge wire or 20 AWG wire. |
11:54 | So essentially for all intents and purposes, what this means is that all three of those pieces of wire are rated to handle the same amount of current flow. |
12:01 | So the difference in the diameter of the wire that we see there is really down to the thickness of the insulation. |
12:08 | So that again on face value might not seem like too big of a deal but essentially between our Tefzel which is our smallest wire there or our smallest insulation and our PVC, we've got close to double the cross sectional area. |
12:22 | And when you're looking at the main trunk of your harness which may consist of 30 to 40 wires or perhaps even more, then that starts to add up and that PVC wiring's going to end up really really bulky. |
12:34 | Now irrespective of that, PVC is not a wire product that we want to use in a club level or professional level motorsport wiring harness and the reason for this is that it doesn't hold up very well with heat. |
12:47 | The difference between those three insulating materials is that the PVC insulation is rated to a maximum temperature, working temperature of about 85 degrees C. |
12:57 | On the other hand our TXL which is a good choice for a club level wiring harness, that's rated to about 125 degrees C and finally the Tefzel which is the wire of choice for a professional motorsport wiring harness, you're going to find that that's rated to 150 degrees C. |
13:14 | Now on face value you might think that even 85 degrees C is more than ample for a wiring harness and that should be absolutely fine. |
13:23 | Now that could be the case however if we're running the wiring harness through the engine bay which inevitably at some point it will be, and particularly if it's running anywhere near a turbocharger or a hot exhaust manifold, you could actually be quite surprised at the sort of temperatures that will exist in the engine bay. |
13:40 | And this is really really apparent when the car comes in after a few hard laps on a racetrack and it sits in the pits stationary with no airflow with the bonnet closed, you're going to get a lot of heat soak occurring there. |
13:53 | So what can end up happening is the PVC insulation starts to deteriorate, it gets really soft and it can melt. |
14:01 | And in that case in extreme circumstances, we can end up with the conductors internally shorting which is really really frustrating because externally there may be no obvious sign of damage to that wiring harness. |
14:13 | So it can make it really hard to actually fault find and figure out what's going on there. |
14:17 | So on that note, PVC, that's out so our choice really comes down to our TXL wire and our Tefzel and the differences there come down to cost, TXL significantly cheaper than Tefzel. |
14:29 | And then there is the size and the weight. |
14:32 | So basically this comes down to the budget that is available for the job and what you're trying to achieve. |
14:39 | Obviously if budget's no consideration or no problem and minimum bundle size and minimum weight is the key objective, then you're going to want to be going with Tefzel wire. |
14:49 | And particularly at the professional motorsport level, when we take into account the Autosport connectors that are used on the wiring harness, the actual cost of the wire becomes relatively insignificant. |
15:00 | So there's our wire considerations. |
15:05 | Now the next thing that we need to talk about is the sheathing that we're likely to see on our wiring harnesses. |
15:11 | Now in this case, just to make things a little bit trickier, both the harness samples that I've got here, both actually use the same sheathing technique. |
15:20 | It's a product called Raychem DR25 and we'll just have a quick look at our professional motorsport wiring harness under our overhead camera. |
15:29 | So we can see that the Raychem DR25 basically gives us an impermeable membrane there, it is resistant to just about any chemicals that we're likely to come across in the engine bay of a car, or any chemicals that we're likely to use in our car in general. |
15:47 | It also provides abrasion resistance and it provides a nice look to our finished harness as well, a nice professional look to our harness. |
15:58 | However it is a reasonably costly product, particularly if you are looking at the club level style harness development. |
16:07 | And it's not strictly necessary at club level. |
16:10 | One of the reasons that sheathing is used at a professional level is when it's combined with the heat moulded boots that we're going to look at shortly and a sealing epoxy resin, basically it provides a harness that is completely impermeable to moisture which can obviously be important to provide long term reliability. |
16:31 | The other materials that we are quite likely to see used, one of my favourites for a club level harness is this expandable braid here, if we look under our overhead camera, so this is quite a small section, this is 1/4 inch or 6.4 millimetre expandable braid. |
16:48 | And basically if we push it back on itself, we can see, exactly as its name implies, it does expand. |
16:55 | So what we can do is choose a suitable diameter of this expandable braid, we can then expand this out, get our wires through the middle of it and basically cut it to length. |
17:06 | Now that will give you a reasonably professional looking wiring harness. |
17:10 | It can still be secured at branch points using the likes of SCL dual wall heat shrink and that's going to also have the effect of kind of gluing that expandable braid into place and stopping it from moving. |
17:23 | You do need to be a little bit mindful of the expandable braid because it does have some downfalls. |
17:28 | First of all, obviously it is going to give you no protection from moisture, fluid ingress at all. |
17:34 | It is expandable, you can see straight through it so obviously that's exactly where fluids are going to go. |
17:41 | So yeah that's one consideration there, are you going to end up with the potential for moisture getting into your harness. |
17:47 | The other consideration is that depending on the particular material you're using, the expandable braid can end up melting and you do need to be mindful of this when you are using a product like the SCL dual wall heat shrink because when you are shrinking that down on the expandable braid, if you aren't a little bit careful with your use of the heat gun, you can actually end up melting a hole through your braid which is a real pain because then you have to strip everything you've just done off, cut a new section of braid and start again. |
18:16 | At the very very entry level as well, we often see, I'll just get this under our overhead camera. |
18:24 | This sort of fabric looming tape. |
18:27 | It's not something that I'm a huge fan of but I will mention it because we do see this used. |
18:33 | And despite the fact that I'm not a huge fan of it, we're actually seeing this style of sheathing used now quite a bit in the GT4 racecar builds from OE manufacturers. |
18:47 | So this is again just trying to drive down the cost of GT4 racecars for the end user customers. |
18:55 | So the advantage with that looming tape is it's very cheap. |
18:59 | It's also very easy to install because it's self adhesive, it will just adhere to itself as well as the wiring harness and we can wrap it around the wiring harness. |
19:08 | So it means that you can service a wiring harness, you don't need to have all of the connectors removed from the harness in order to sheath it so it's quick and easy to work with but again you're not getting very much protection there. |
19:22 | Certainly if you're going to run that into the engine bay and sheath your harness like that, you're going to end up again with problems with water, with oil, fuel et cetera soaking into that sort of sheathing. |
19:36 | I will mention the one product that regardless of what level I'm working at I'm never going to use which is the split PVC convoluted tubing. |
19:45 | I see this from time to time, it's a horrible product, just like the PVC insulation on our wiring. |
19:53 | It doesn't handle the sort of temperatures that we are likely to see in an automotive application and it's just generally difficult to work with and in my opinion at least, the finished product doesn't look professional either. |
20:06 | Alright so moving on, then we get into the boots that are used for particularly our professional motorsport wiring harnesses. |
20:16 | So we've already had a quick look, I'll just back to our overhead camera, at our Autosport connectors at our bulkhead here and what we've got here is a Raychem heat moulded boot on the back of this Autosport connector. |
20:28 | And this is a heat recoverable boot so basically we can put it over the connector once everything is terminated. |
20:35 | Using our heat gun we can then recover it down onto the Autosport connector and at the other end we also recover it down onto our DR25. |
20:42 | And it is also sealed at both ends with a ResinTech epoxy resin. |
20:47 | So again this is providing environmental protection from moisture and dust ingress. |
20:53 | Also because it is basically a rigid boot once it is shrunk down. |
20:58 | This also provides strain relief. |
21:00 | So if the wiring harness is moved then that movement is then not going to be transferred into the terminals inside of the connector. |
21:08 | So that again aids reliability. |
21:11 | Now it's not just at the back of the connectors we see these boots though. |
21:14 | I'll just move to a transition here on our harness. |
21:17 | And we've got another head recoverable moulded boot here. |
21:23 | So again both sides of this are filled with epoxy to provide ingress protection from moisture et cetera. |
21:30 | And we can purchase those boots in a variety of different shapes. |
21:33 | So at the ultimate level, I'll just show you this boot here. |
21:37 | This is a T intersection boot. |
21:40 | So it doesn't look much like a T intersection boot now, it's obviously pretty big. |
21:44 | But it's actually quite surprising how much these change in shape and size when we recover them down. |
21:51 | So that particular heat moulded boot is designed to work with this T intersection here. |
21:57 | Basically we can run our different branches through the different legs on our heat moulded boot and then when it recovers down everything's going to spring back basically like I've got it laid out right here. |
22:09 | So in the perfect scenario we're going to be using one of these heat moulded boots at every single junction. |
22:15 | So for example when we're got our injector wiring, let's say we're running out to four injectors and we're going to have a branch point off our wiring harness at each, or at least the first three of those injectors. |
22:25 | So we're going to be using a heat moulded boot at each of those points, sealed with epoxy and again once we've done that, if we do that, we're going to end up with a completely sealed harness that's going to offer us good environmental protection. |
22:39 | The downside of course is the cost and the time that that takes. |
22:44 | Each of those heat moulded boots is pretty pricey, obviously the actual cost of the boot will depend very much on the specific boot part number and the size of that boot. |
22:54 | It's easy for these boots to be anywhere in the range of sort of USD$20-40+ and as you can understand if you're using a lot of these boots, that really really quickly adds up. |
23:03 | So connectors is the other obvious, sorry actually before I move on from that, I'll just bring in our club level harness and we can see that we still can achieve some of the same sort of results at a much cheaper level so in this case as I mentioned, this harness has already been sheathed in DR25 although that's not strictly going to be that normal. |
23:31 | But with the DR25 here, this particular branch point has been sealed with a section of SCL so that's a semi rigid heat recoverable dual wall heat shrink. |
23:42 | So this isn't going to provide the same level of environmental protection as our heat moulded boots but it is much much cheaper and it still gives a nice professional result and because it is a semi rigid product as well when it is recovered, again provides some of that stress relief that I've kind of mentioned. |
24:03 | Alright so the other aspect here is we need to talk about the construction techniques. |
24:09 | Because this is where a lot of the time goes into a professional motorsport wiring harness. |
24:14 | And again any of you who are following those who are producing these wiring harnesses on the likes of Instagram and Facebook, will inevitably have seen multiple photos of beautifully concentrically twisted harnesses. |
24:27 | And I've got a little test section of harness here that I just want to show you and we'll talk through what is involved here. |
24:33 | So this is our concentrically twisted harness, consisting here of three layers and some sheathing so we'll have a look first of all, we've got our centre layer. |
24:41 | In this case we've got two pairs of shielded cables that are twisted together so that makes up our core. |
24:49 | Shielded cables, generally the bulkiest cables are what we want to put in our centre of our concentric twist and of course the engine speed and position sensors are a good candidate for these. |
25:01 | So those are twisted together. |
25:04 | On our next layer we've got a series of 20 gauge wires. |
25:07 | This is Tefzel wire here because it is a professional motorsport harness construction. |
25:13 | And you'll notice that they are twisted in the opposite direction. |
25:16 | So this is the key with concentric twisting. |
25:18 | Each subsequent layer we step up in both our number of our conductors as well as reversing the direction of the twist. |
25:25 | So we've also got visible here some Kapton tape. |
25:30 | So this is the gold coloured tape that again you'll see quite frequently used in professional motorsport wiring harness construction. |
25:37 | The Kapton tape is a nice thin tape which lends itself really well for our application here. |
25:43 | It provides good insulation and the other important aspect with it is that it is very heat resistant. |
25:50 | So for this reason, you'll quite often see the Kapton tape is used behind a transition. |
25:54 | So let's just bring in our little t transition here. |
25:57 | I've used it there, well actually I think in this case Zac used it there but let's not split hairs. |
26:04 | And the idea behind this is that when we recover down our heat moulded boot. |
26:10 | The epoxy that we're going to place inside that boot, or if it's a epoxy lined boot is going to end up sticking to the Kapton tape. |
26:17 | And all this means is that if we do need to service this particular transition at a later point, we can cut that boot off and instead of the epoxy sticking to each of our individual conductors, it's going to stick to that Kapton tape which makes it much easier to remove the tape and then service the transition as required. |
26:35 | So the other aspect here is we do have this kevlar lacing cord that is also over our concentric twisted layer. |
26:44 | We've reversed the direction of twist there and this just helps hold everything nice and tightly together as we're building up our concentrically twisted harness. |
26:52 | Moving on we've got our third layer which is our final layer here. |
26:56 | This time 22 gauge and we've twisted that again the opposite way. |
26:59 | We've got our Kapton tape, we've got our kevlar lacing cord. |
27:02 | Now one of the important things to understand with concentric twisting is why the technique is used in the first place. |
27:11 | And we hear arguments from both sides as to why it should or shouldn't be used. |
27:15 | One of the advantages with it is it does provide a really flexible finished harness. |
27:21 | And the reason for this is that each of those layers can move in relation to the other layer. |
27:26 | So if we get our final layer here we can see that we can twist it back really tightly through 180 degrees on itself. |
27:33 | Now that might not seem that useful but particularly when we are twisting and maneuvering our harness through the engine bay when we're routing it how it needs to go, quite often some flexibility is essential. |
27:44 | And that ensures that as we're moving that harness through and we're twisting it or bending it that no extra strain is placed on any individual wire compared to any other. |
27:53 | So the advantage here of course is in reliability of that harness long term. |
28:01 | The other aspect is that it does give a minimal bundle size. |
28:04 | So again pretty important when we are trying to keep our wiring harness as small as possible. |
28:11 | And it's also going to give us a nice round profile for our finished harness which makes it really easy to install our DR25 sheathing over the top of. |
28:20 | So if anyone has tried to use DR25 and put this sheathing over the top of a harness where all of the wires are just haphazardly bundled together, it gets to be really tricky because that DR25 isn't going to want to slide that nicely over our haphazardly collected bundle of wires so when we've got a concentrically twisted harness, really easy to insert the harness into our DR25 and when it is recovered down it's going to give us a nice finish as well. |
28:51 | Now there's no free lunches here though, there's also some significant downsides with our concentrically twisted technique. |
28:59 | The first of which is it is time consuming. |
29:02 | It's actually not that difficult but it is really time consuming to get your head around. |
29:07 | And it's going to add a lot of additional time, particularly if you've got long branches of wiring harness to create, it's going to add a lot of time to doing this. |
29:16 | The technique is to start with a core, then we're going to build up our second layer twisting the wires around, once we get to the outer layers though where we've got a lot of conductors, we tend to need to work with a small group of wires at a time because otherwise as we're twisting the wires around the harness, we're going to end up with this massive birds nest so it is quite frustrating, particularly when you are learning the technique. |
29:39 | The other aspect with concentric twisting is that we do need a specific number of conductors for each layer, each subsequent layer of the twist. |
29:47 | And this really comes to a head when we get to our outside layer because inevitably in most instances we're going to find that we don't have quite the right number of wires to make up the required number conductor count for that outside layer. |
30:03 | So we get around this by including what's called filler wire. |
30:08 | And as its name implies, this is wire that's literally just along for the ride. |
30:11 | So this becomes a little bit counter productive, particularly when we've been talking about the advantages of keeping our weight down. |
30:17 | But this is one of the considerations with concentric twisting and this is something that you need to take into account and understand if you do want to go and use that technique. |
30:27 | Quite a lot of harness constructors will actually use that to their advantage and what they'll do is include additional wires that are in the harness essentially as a filler and they'll be broken out into a connector that can be used for additional functionality so it makes it easier to extend the harness and make changes, add additional sensors at a later point if the owner of that vehicle decides that they want to do something they hadn't originally envisaged. |
30:53 | This is also important to consider because if you are using this style of construction technique, it's all but impossible to make modifications or changes to your harness at a later point once it's built. |
31:06 | Alright so we've talked a little bit about the materials there, we've talked about the construction techniques, the other thing that's important to understand is the tools that you're going to need if you do want to build either of these sorts of harnesses. |
31:23 | So for our club level harness that we've got over here on my left, we can generally construct one of these harnesses with a reasonably small range of fairly generic tools. |
31:34 | So what I'm talking about here is generic crimp tools like this one I've got here, this particular one is a Delphi crimp tool. |
31:44 | We're still going to probably need three or so different crimp tools for all of the different style of terminals that we're likely to come across but each of these particular crimp tools is relatively cheap to purchase. |
31:56 | You should be able to purchase something of this nature for somewhere in the region of about USD$50-80. |
32:02 | The other crimp tool that I'll show you here, this is one of my favourites, which is what we use for our DTM connectors which are a relatively cost effective option compared to the more expensive Autosport connectors. |
32:19 | So this particular crimp tool here does a great job of crimping the DTM pins and sockets. |
32:25 | You can purchase these for around about USD$50. |
32:27 | So tools that aren't going to break the bank there. |
32:31 | We're also going to probably need, or we are going to need a good quality set of side cutters, sorry wire strippers. |
32:39 | Side cutters are another product that we are going to need but I'll at least talk about the tool that I've got under the overhead camera here. |
32:46 | These vary quite a lot in terms of cost and functionality. |
32:50 | This is a pretty cost effective option from Ideal, this is called their Custom Stripmaster Lite. |
32:56 | The important aspect is that the specific blades that are included on this product are designed for our wire, particularly the TXL and Tefzel wire that we're going to be using and they are marked with the different gauges as well. |
33:09 | And that makes sure that we can do a really good job of stripping away the insulation without damaging the underlying conductor strands and I know that a lot of people will strip insulation off their wires using a pair of side cutters and bit of force, you can get away with this but more often than not, you're going to end up nicking or damaging the underlying conductors and this will affect the ability of the wire in the end to support current flow. |
33:34 | Now just because I have mentioned them and we haven't really talked about them too much at this point. |
33:40 | I just want to get a DTM connector under our overhead camera and this is what we're working with when we're talking about DTM connectors. |
33:48 | These are available in a range of styles. |
33:51 | This is a DTM, they also do DT and DTP which step up in conductor size to handle more current flow. |
33:58 | So these are available in two through to 12 position. |
34:01 | We've got I think a 12 position here and we've also got a four position here. |
34:06 | So you can buy, depending on the number of positions, a pair of these connectors for probably somewhere in the region of about USD$10-20 and they are really really cost effective, they do a pretty good job of sealing from moisture and as I've mentioned the crimp tool that we're going to need is not going to set you back hundreds of dollars. |
34:28 | So that's why we use them a lot here at HPA. |
34:34 | However if you do have your sight set on professional motorsport wiring harnesses, you are going to need to spring out for a set of proper crimp tooling. |
34:45 | This is the generic crimp tool that is what you'll see most often used in professional motorsport harness construction from Daniels Manufacturing Corp, or DMC. |
34:56 | So this on its own is not that much use. |
34:59 | What we actually need to do is also use it in conjunction with a specific positioner. |
35:04 | And the positioner will go into the turret at the end of the tool and we're going to need a specific positioner for each of the different terminals that we're going to work with. |
35:15 | So that can in itself get quite expensive when each of these positioners can be in the range of maybe USD$50-80 depending where you're getting them from. |
35:23 | I forget off the top of my head the cost of the crimp tool itself but I think you're probably going to be looking somewhere in the region of USD$300-400 or thereabouts. |
35:34 | So obviously things are going to step up quite considerably in terms of cost if you are going to want to work at that level. |
35:42 | And that's only one of the crimp tools that we have looked at there. |
35:47 | Now that being said, even if you are working at a club level harness construction level then there are options available for crimp tools. |
35:56 | So the likes of the AMP Superseal connectors that are so common for aftermarket ECUs, we've got a couple of those here on our club level harness, we'll just have a look at those quickly under our overhead camera. |
36:09 | So these connectors, I'm doing a really shoddy job of getting them in shot but these connectors here, used by the likes of Link, MoTeC, Haltech, Adaptronic and numerous other ECU manufacturers, pretty easy to work with, pretty cost effective, easy to get terminals. |
36:29 | And we can do a really good job of crimping the terminals for the AMP Superseal connectors using generic crimp tooling. |
36:37 | However if you are going to be doing a lot of these, there are specific crimp tools available with dies that are designed only for that AMP Superseal connector and they'll also be able to do both operations of the crimp in one shot so that's going to save you time. |
36:52 | Aright we're going to jump into our questions and answers really shortly so if you do have any questions, this is the ideal opportunity to ask those. |
37:00 | Before we do though, couple more topics to cover off here. |
37:04 | So the next one is time, how long is it going to take to create one of these wiring harneses? Now it's a difficult question to answer because there are so many aspects that this will depend on. |
37:16 | Obviously it is job dependent, how complex is the harness, how long is the harness, what sort of engine are we wiring up, is it a basic naturally aspirated four cylinder engine or is it a V8 with twin turbos and a lot of additional sensors added to it. |
37:30 | So those things will factor in exactly how long the job is going to take. |
37:33 | Also of course you need to consider your level of proficiency. |
37:37 | So of course when you're just getting started, you're going to take a lot longer to do these jobs. |
37:43 | But in general if I had to give you an average, if you're building a club level harness like the one we've got here, for a relatively run of the mill four cylinder engine, and you're pretty competent on the tools, you're probably going to be looking at somewhere between 20 and 30 hours of work. |
37:59 | Now if we're looking at the professional wiring harness construction on the other hand, that's going to jump up significantly. |
38:06 | Again obviously factoring in there's a huge range in here depending on the complexity of the job and exactly what's entailed but it wouldn't be uncommon for these jobs to start out at 40 hours and that would be fairly light to be honest. |
38:18 | Easily could go up to and over 200 hours in total. |
38:22 | Now depending on how you're doing this, if you are looking at getting a professional to do it, obviously if you're going to be paying a professional maybe $100 or $150 an hour, then multiply that by 200, it's going to start giving you some idea of where you're looking at price wise and that really comes into the next topic which is the cost of the harnesses. |
38:44 | Again very very difficult for me to put an exact figure on this, a lot of it's going to come down to the complexity and design as we've already talked about. |
38:51 | A lot of it's also going to come down to whether or not you're going to be doing this yourself. |
38:57 | So at the entry level with a club level harness, you're probably going to need at an absolute minimum to be investing somewhere in the region of about maybe USD$300-500 on some basic tools. |
39:08 | Of course you can add a lot more to that. |
39:12 | I'm looking at bare bones basics. |
39:14 | And of course if you're going to be getting into this and doing a few wiring harnesses, you're going to be building up your tool kit over time. |
39:20 | So you don't necessarily need to go and shell out thousands straight away. |
39:24 | A few hundred dollars is going to be adequate to get you up and running and you're going to be able to perform quite a lot of different tasks with the generic crimp tools that we recommend. |
39:36 | On top of that you've got your consumables and materials. |
39:38 | I would say that on average you're going to need to allow at least USD$500-600 for materials. |
39:47 | So at that point you're probably going to be looking somewhere in the area of maybe at the very light side, USD$800-900, probably more likely between about USD$1000-1500. |
39:58 | On top of that you've got your time to consider. |
40:01 | On the other hand with the professional motorsport wiring harness, you're going to probably be looking at a minimum of about USD$1000 in tooling to get you up and running so it's going to be expensive, particularly if you are only looking at doing one harness. |
40:18 | Beyond that though it's the materials that really do become pretty pricey and it's not uncommon to end up putting maybe USD$2000-3000 or much much more into your harness. |
40:29 | When you consider that one of these Autosport connectors like the bulkhead connector that I've got here can end up running anywhere between about USD$300-$500, if you've got a few of these going into your job, obviously that's quickly going to blow out. |
40:47 | That's why I said before as well, when we're looking at the difference between the cost of the likes of the TXL wire and the Tefzel wire, at professional motorsport wiring harness level, the cost of the wire is really almost an insignificant aspect. |
41:00 | So if you're looking at professionals doing this work, we recently visited Renvale in the U.K. while we were over there for Goodwood Festival of Speed, and Renvale if you aren't aware of them, they produce the wiring harnesses for every F1 team with the exception of Williams, as well as WRC, Superbikes, basically if it's fast and it's at the upper echelon of professional motorsport, chances are that Renvale had a hand in the wiring harnesses. |
41:26 | So for their F1 harnesses, just one section of harness that we saw them producing for Mercedes, that particular piece of harness was valued to the team at something like £20,000 and that's probably about a third of their entire harness, also keep in mind that these F1 teams, most of the top teams, will replace the harness after every round of F1. |
41:50 | So there you go, some idea of the cost involved. |
41:54 | The last topic, before we jump into our questions, is serviceability and this is really a big one as well. |
42:01 | I've kind of already touched on it, with the professional motorsport wiring harness because everything is booted and covered in DR25 heat sheath, there's really almost no possibility for us to add additional wires, if they haven't already been considered during the original design. |
42:19 | So very very difficult to modify this. |
42:21 | And this is something that I see as a real problem with a lot of enthusiast level cars is that we tend to tinker, develop and modify our cars over time and in particular if you want to add an additional sensor or maybe use a different function or output that wasn't originally thought up, then it's really difficult to do that if you are dealing with a professional motorsport harness. |
42:44 | On the other hand if you are dealing with something a little bit lower down the rung on the club level side of things, then it's not that difficult to add in an additional branch straight from the ECU, run it out through your grommet, through the firewall out into the engine bay and it's pretty easy to adapt and modify your harness as your requirements grow. |
43:05 | So a few considerations there, hopefully that's given you some more insight into what goes into those two harnesses. |
43:10 | For me, unless you are basically dealing with a professional build for purpose built motorsport where budget is not a consideration, or alternatively you're building a car where you're really after that look and feel of a professional motorsport wiring harness and the budget isn't a consideration or a problem for you, then the club level harness construction techniques are going to be more than adequate for 99% of enthusiasts out there. |
43:39 | Alright we'll jump into our questions, if you've got any more please feel free to keep them coming. |
43:48 | Matthew Holt has asked, why do you guys use Kapton tape versus 3M 33+ electrical tape when building the harness? I have not used the 3M product, I think Matthew it's probably just a case of once you've got a product that you know, you're familiar with, you've got a source of it and it's doing the job, I kind of tend to stick with it. |
44:07 | Now I know, I don't know if this is the angle you were going with here, I know we posted some information about Kapton tape on our Instagram, it was probably about a year ago now and we got put on blast by a lot of people telling us that Kapton tape is a horrible insulator and it was actually forced to be removed out of the aerospace industry because of a number of crashes. |
44:28 | I think off the top of my head maybe with Airbus. |
44:31 | Yep absolutely all fine and dandy but we don't work in the aerospace industry. |
44:36 | The voltages that we're dealing with here are in an automotive application very very low so it's perfectly suitable for our application. |
44:44 | Again just going a little bit off course there Matthew but I just wanted to get that in there because I know a few people may have that question in their mind. |
44:54 | Cash has asked, what type of or where do you get your wiring quick disconnects, are they Mil-Spec, Amphenol or something different? So the particular products we most often use are the Autosport connectors. |
45:06 | Yes there are cheaper ones that are used, these sort of become a bit of a crossover, between the club level and the motorsport harness world. |
45:20 | Autosport connectors are our most usual go tos, there are a range of suppliers of these depending on whereabouts in the world you are. |
45:29 | Some of our favourites include racespeconline.com, milspecwiring.com and Prowire USA. |
45:36 | Obviously all of those are based in the U.S. but they also ship internationally depending again on where you are in the world. |
45:44 | There's like to also be a supplier local to you. |
45:50 | Kfennell has asked what is a suitable bulkhead connector for a club level harness, flanged, DTM or Mil-Spec? OK so in a club level harness construction I would probably actually more often use a wiring grommet through the firewall. |
46:08 | So basically at that level to cut down on costs and keep things simple, we would basically repurpose the factory grommet through the firewall that your stock wiring harness comes through. |
46:18 | Now there are people who do want to step up and then include an Autosport connector or the like. |
46:23 | As I just mentioned I can't give you a name off the top of my head because we simply don't use them. |
46:28 | There are some cheaper alternatives these days to the Autosport connectors. |
46:30 | Obviously with price comes quality so you need to work on those two trade offs. |
46:38 | There are flanged DTM connectors but generally at the bulkhead where you're going to be feeding a lot of wires through, the DTM connectors only go up to a 12 position and you're going to end up with a fair few of them which is going to end up being a little bit messy. |
46:53 | So just some considerations there as well. |
47:02 | Doing Stuff Daily has asked, should shielded wires all have the same direction twist? OK so with the shielding I'm assuming you're talking here about our concentric twisting, with the shielded wires what we're using is a section of specific manufactured wire which is a shielded pair or maybe it'll be three conductors depending on what exactly you're trying to do. |
47:26 | So that's actually a twisted, let's say we're talking about a two core shielded cable, that'll be two cores of conductors which are twisted together, then there'll be the shield around that. |
47:37 | So beyond that it's actually not that critical, the twist in terms of the concentric twisting has no effect on the ability of that shielded cable to reject electromagnetic interference. |
47:47 | Obviously regardless how we're constructing the harness, the key is that the shield needs to be grounded generally at the ECU ground so it can drain away any EMI that makes it into that harness, protecting the conductors underneath and ensuring the integrity of that signal. |
48:05 | Wrathboy has asked, what are the best sleeves to protect the wiring from heat? Actually great question there. |
48:10 | So we do need to be a little careful with the harness where we've routed it and try and keep it away from heat as much as possible. |
48:19 | But sometimes that's not entirely possible, sometimes it's still going to be exposed to heat and we do need to protect the harness where we can. |
48:27 | What I'm actually going to do is just awkwardly pop out for a second and I'll grab a section of what I actually recommend, so bear with me for a second, I'll just go a little bit off script. |
48:57 | Alright well going off script didn't help because someone's moved it. |
49:00 | I was hoping I was going to be able to show you the product that we use. |
49:03 | But it's actually a product that is a heat sheath used generally around fuel lines and the like. |
49:10 | So it's a material that goes over the top of the fuel line and in this case of course we can just put it over the top of our DR25 or our existing sheathing. |
49:19 | And it uses a fibreglass insulating material. |
49:23 | Comes in either a silver colour or an orange colour. |
49:27 | Some of it's called fire sleeve I think off the top of my head. |
49:30 | We get it from Speedflow in Australia, they're one of the manufacturers, but there are other manufacturers such as Aeroquip as well. |
49:39 | Not strictly made for wiring harnesses but it does actually do a really really good job. |
49:44 | So if you've got anything that's going to be running reasonably close to an exhaust manifold or something hot, it does make sense to take the opportunity to protect that where possible. |
49:56 | Nick has asked, what was the brand and model of the wire strippers you use? So the ones that I had here, these actually aren't the ones I normally use. |
50:04 | These are an Ideal Custom Stripmaster Lite. |
50:07 | So this is the entry level product from Ideal. |
50:11 | The other one that's slightly up further in their range is the Ergo-Elite which is just a little bit nicer to use, particularly if you are building a lot of harnesses and you're spending a lot of time stripping insulation off wires, they're just a little bit more comfortable in your hand. |
50:26 | Might sound like it's irrelevant but yeah it does make a lot of difference if you're doing a lot of wire stripping. |
50:36 | Shed has asked, how does the pin numbering system work for the round motorsport connectors? So this will depend on the particular connector, some of them use letters, some of them use numbers, some of them use a combination of letters and numbers. |
50:50 | But essentially if you, I'm not going to be able to probably show you here but if you look at the back of the connector, you'll actually see the numbering or lettering scheme. |
51:01 | There is a round terminal marked which is essentially the first one and then you work your way around towards the centre. |
51:08 | Takes a little bit of time to get yourself used to doing that and of course it's essential to make sure that you are very careful when you are inserting any pins or sockets into those Autosport connectors, making sure that you are absolutely certain you've got the correct location in that connector. |
51:27 | Girtain has asked, does a PDM seem like overkill for a club level racer or is it a nice feature to have over a typical fuse and relay block? Look I'd say probably if you asked me that question five years ago, I would have said yeah it's probably overkill. |
51:41 | And let me be really clear, it's certainly not essential to have a power distribution module. |
51:47 | But there are a lot of upsides and sometimes when we factor in the overall cost, the difference in price may actually not be as much as it initially sounds. |
51:56 | So particularly if you are paying a auto electrician or someone to produce a wiring harness for you, if you are using fuses and relays, this is actually one of the most tedious and time consuming aspects of producing the wiring harness. |
52:10 | You've got to mount all of those relays, you've got to mount up all of those switches and then do a nice neat job of running the wiring between them. |
52:17 | Now when you're dealing with a power distribution module, particularly if you are incorporating a CAN based keypad which most of these will interface with, it really speeds up the power distribution wiring dramatically. |
52:30 | So yes you're going to be paying more initially for the power distribution module but the overall cost when you save the labour actually doesn't end up being too dramatically high, or too much higher. |
52:42 | Then you need to factor in the advantages that the power distribution module can give. |
52:46 | So we've just had exactly this situation with our Toyota 86 endurance car where due to a crash we ended up with a wire to one of our fuel pumps intermittently shorting against a piece of chassis when enough load was placed on it due to cornering or braking. |
53:02 | So because we were using a power distribution module, this monitors the current flow, when it shorts the current obviously spikes, so the power distribution module then will cut that particular circuit to protect it. |
53:13 | So then what it will do though, in a conventional fuse I should say, that would be us, we'd be out of the race because the only way of resetting that circuit would be to stop and physically replace the fuse or reset a circuit breaker. |
53:25 | However with a power distribution module, the power distribution module will then monitor things, it will wait a preset amount of time and then it will retry that particular circuit and it will retry it as many times as you want it to. |
53:38 | So it can actually limp you through to the end of a race or at least get you back to the pits where more permanent repairs can be made. |
53:46 | And there's also a lot of cool functionality that we can incorporate with a power distribution module in terms of how we operate all of our outputs, when we operate them and some safety features there as well. |
54:00 | Masoud has asked, what's the correct way to ensure good grounding when relocating your battery? OK this is actually a question that popped up on our forums just recently as well and I think this comes down to our discussions around our star earthing points. |
54:14 | And that doesn't mean that for example if you are moving your battery to the trunk area of the car, the boot area of the car that you need to run a ground strap all the way forward to the engine block, that's not necessary. |
54:27 | We're quite OK to just run a short earth strap straight from the battery negative to the chassis of the car. |
54:34 | Now we want to be a little sensible with this, we want to make sure that we are choosing a good location that's nice and solid. |
54:40 | We don't want to be attaching this to something that's flimsy. |
54:44 | Maybe a thin piece of sheet metal. |
54:46 | It's also a good idea to make sure that you've removed some of the pain from that particular area so that your ground strap can get a good connection to earth. |
54:55 | Then we can do exactly the same at the front where the engine is, we can run a ground strap between the chassis, keeping in mind those same considerations straight to the engine block. |
55:05 | Alright that looks like it's brought us to the end of our questions so thank you to all of those who have joined in there, hopefully everyone's learned a little bit more about the different techniques when it comes to motorsport wiring. |
55:16 | Hopefully that's maybe broken down some of those misconceptions that are out there and you've got a better idea of what to choose for your next project. |
55:24 | As usual, for our HPA members if you've got any questions after this webinar has aired, please ask those in the forum and I'll be happy to answer them there. |
55:32 | Thanks for joining us and I look forward to seeing everyone next week. |
Timestamps
0:00 - Introduction
0:25 - Why we don't use the term milspec
1:40 - You don't need to spend thousands of dollars
2:25 - Factory vs motorsport harness
10:40 - Wire
15:00 - Sheathing
20:05 - Boots
24:00 - Concentric twisting
31:05 - Tools
37:00 - Time
38:40 - Cost
41:50 - Serviceability
43:45 - Questions
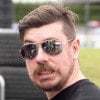