380 | Affordable 3D scanning - Creality Otter
Summary
3D scanning isn't reserved for pro-level teams with big budgets. There are now many affordable 3D scanners on the market that we can use to get great results in our CAD projects. In this webinar, we'll look at the scanning process using the Creality CR-Scan Otter, by setting-up the scan, taking the scan, and then trasferring it into our CAD software.
00:00 | Hey team, Conor here from HPA, welcome to this week's webinar. |
00:03 | This week we're going to be having a look at affordable 3D scanning, in particular we're going to be having a closer look at the Creality CR Scan Otter. |
00:13 | So, we're just going to have a look at the scanner itself and then we're going to get set up and scan something, then we're going to bring that into our CAD software to just show the transfer of our scan data over to CAD and how we get set up to use that. |
00:29 | So, with that covered, let's get straight into it. |
00:32 | So, what I've got here on my desk is the Creality CR Scan Otter. |
00:38 | This is an entry-level scanner from Creality. |
00:42 | Most of their scanners are in that case, and this is at about $1,000. |
00:49 | So, as far as 3D scanning goes at the moment, this is definitely considered more on the entry-level side of the spectrum. |
00:58 | What I'm going to do is just open a page here, just their webpage, and we're just going to scroll down a little bit to the technical specs here, product parameters. |
01:15 | So, I just wanted to run through these quickly just before we kind of get set up and working. |
01:21 | The first one I wanted to start on is the accuracy, which is kind of a point of contention with a lot of these scanners, and we really need to understand what this means. |
01:31 | So, you'll see it notes here up to 0.02 millimeters, and that's at 60 millimeters. |
01:38 | So, what you need to understand about accuracy and when they quote it is basically what it really means. |
01:44 | So, the accuracy is often based on the size of the scan. |
01:48 | So, sometimes they'll actually give it as a percentage measurement, and that's just something you need to be aware of. |
01:54 | So, if you see a really cheap scanner quoting a very high accuracy, sometimes that's specifically at their minimum scan size. |
02:05 | So, for example, I'm not sure if it shows here, but this basically has a scanner size range that they kind of recommend that you work to, and this one's quite a versatile one. |
02:20 | So, I think up here it says, yeah, 10 by 10, so 10 millimeter cube size up to basically two meter cube size is their kind of range. |
02:33 | So, if they give that 0.02 millimeters, oftentimes that'll be at their smaller side of the range. |
02:39 | It looks like they're saying that's at 60 millimeters in this case, but that's just something to be aware of. |
02:45 | And why I bring this up is it's also measured in their case in a laboratory setting. |
02:51 | So, it's a very controlled environment, and basically that doesn't always translate to us working in our workshops or our garages to work on our cars. |
03:01 | So, it's just something to be aware of. |
03:03 | Again, I'm just going to bring up a photo that I've got here. |
03:08 | So, this is from a test that I did on a bunch of these more accessible 3D scanners, and we're going to link to that video in the chat soon. |
03:18 | But basically what I've done here is scanned, I think this is, yeah, the K20 block by the looks of it. |
03:26 | It might be the SR20 as well. |
03:29 | No, it's the SR20 because I can see the Mazworks front cover thing on there. |
03:33 | So, this is an SR20 block, might even be an SR22, but basically did the scan and then brought it into a scan or I guess you'd call it a scan to CAD or reverse engineering software package called Geomagic Design X, which is kind of one of the most well-known ones. |
03:56 | And it's, again, a very expensive piece of software, but very, very useful. |
04:01 | But basically what that allowed me to do is I use the auto segmentation tool to break up the scan into all these different kinds of geometric forms. |
04:11 | And basically from that, I was able to fit cylinders to the bores of the cylinders in the block and then take measurements from them to be able to basically analyze to see how accurate the scan data actually was. |
04:25 | And basically what I found from that is that the accuracy in the scan for that particular dimension of the bore spacing and also the bore sizes was about 0.5 millimeters, so half a mil, which, again, is actually really good for a scanner of this level. |
04:47 | And of that test, we looked at the 3DMaker Pro Moose, the RevoPoint Range 2 Creality Scan Otter, and the Einstar, and the Einstar is usually the pick for most people in this kind of price range. |
05:03 | But what we found is that the Creality Scan Otter here was actually more accurate than the Einstar for something like this. |
05:11 | They do lend themselves to slightly different use cases. |
05:14 | So, again, just something I wanted to note around the accuracy. |
05:19 | If we just jump back here over to the Creality page, the resolution is kind of quoted here as 0.05 to 2 millimeters, so it's an adjustable range there. |
05:32 | And something like that is more than suitable for our mechanical design or automotive or motorsport projects. |
05:41 | And yeah, when you're working with accuracy, you just need to be aware of the range that you're working in. |
05:46 | So, you can kind of adjust your designs to suit, if that means opening up some tolerances around holes and so on, or backing up physical measurements, things like that. |
05:56 | I will note on that resolution though, that this does seem to be an area where the scanner kind of lacks from my experience with it. |
06:07 | I've noticed that unless we are working on the high resolution settings on the software, which we'll see in just a moment, the resolution of the models is actually quite poor. |
06:18 | And if we do work on those high resolution settings, processing time for it in the software is really, really slow. |
06:26 | So, again, we'll see this in just a moment. |
06:29 | Something else which is probably best shown on the screen here is the various size options here. |
06:37 | So, on the front of the scanner, there's actually a whole bunch more cameras than usual. |
06:44 | Usually we have this middle one, and then the kind of projectors, or the projectors and the cameras out to the side. |
06:53 | So, basically these scanners are structured light or near infrared structured light, and they work on the principle of triangulation. |
07:03 | So, where it projects a light pattern onto the surface, and then the other cameras kind of pick up that light, and by how it interacts with the surface that the scanner is able to build a 3D model from that. |
07:16 | So, this has these two different sets of cameras with different focal lengths. |
07:21 | And basically, in the practical sense, what that means is that it opens up a wider working range, I'd guess you'd call it, for the size of the object that we're working with. |
07:34 | The further they get apart, those cameras, the bigger the kind of working area that we get, so we can scan more efficiently. |
07:43 | But there's some downsides to that as well, with scanning very small things in high detail. |
07:50 | So, this scanner essentially covers both of the bases, and it means it's quite versatile, which is quite good for the home enthusiast just trying to scan lots of different things. |
08:02 | You might be scanning a small part, like what we're going to look at today for your project tower. |
08:07 | Or you might be scanning the bonnet, for example, down the whole side of the vehicle, which is obviously a lot larger. |
08:15 | Cool, so with that out of the way, let's just jump into the RealityScan software here, and we're going to get set up and start taking a scan here. |
08:28 | So, what we're going to scan, it's a little bit of a funny piece, but basically this is the center cap off a wheel, just some little 14-inch Volk GRC wheels that I have on a little K11 Nissan March in the garage. |
08:45 | And it's actually a two-piece center cap design with this piece here as well. |
08:51 | This piece I'm going to be retaining, this piece here I'm actually going to be remaking. |
08:57 | Basically, when you put them on the car with the low offset that they have, these parts stick out the side really far and it just looks funny. |
09:04 | The other thing is there's this kind of plastic threaded part in here which has been damaged by use or something in the past, and it just doesn't thread on very nicely anymore. |
09:17 | So, basically I'm going to remake this part in CAD and then probably 3D print it, maybe with a resin 3D printer so I can accurately print those threads. |
09:28 | But what I'm going to do is just scan this today and then we're going to bring it into our CAD software and just align it with the rest of the wheel that I scanned previously. |
09:41 | So, you kind of get an idea for how to capture a scan like this on the scanner, how it does, and then how to bring your scan software into your CAD software and scan data into your CAD software and start using it. |
09:55 | Cool. |
09:55 | So, let's just start by clicking new project here and I'm just going to say bolt. grc set to CAD and go, okay, cool. |
10:10 | So, configuration here, a lot of scanning software has something like this where as we set up a new scan, it basically prompts us to fill out these boxes depending on what we're scanning so it can choose the best settings to apply to it. |
10:26 | So, let's just start at the top here. |
10:28 | We've got object. |
10:30 | We're not doing a face or a body. |
10:32 | So, normal is good there. |
10:34 | The size of the object in this case is going to be small, under 250 millimeters cubed. |
10:43 | So, that works good. |
10:44 | And these ones are for larger ranges and that will change the cameras that the scanner is using like I discussed just before. |
10:53 | Features. |
10:53 | So, this is basically the features that the scanner is going to track the movement on. |
10:59 | So, we can use geometry here, we can use texture, or we can use some markers, which don't have them out, but I'll just bring out the calibration board here for the scanner. |
11:12 | So, the markers are kind of like this little, the little black dots here, there's the markers. |
11:18 | These little stick-on markers that you usually see with around 3D scanning, which basically the scanner is calibrated to pick these up and you'll be looking for them when tracking and that will help it keep its tracking and understand its position relative to the object as it moves easier. |
11:39 | We won't be using that as today. |
11:40 | We're just going to stick to geometry for this part and I'm going to talk about some considerations around that as we go, because the geometry on this part is quite consistent, circular, and that can cause a few issues. |
11:57 | Cool. |
11:57 | For the accuracy, I'm just going to go fast, just because like I said, the processing time is quite slow for this and we're working live here, so I want to keep things moving on. |
12:08 | Disable flat base. |
12:10 | So, what that's going to do is just try to remove the little turntable that I have set up here from underneath the part. |
12:20 | Just a note on that turntable as we get started, that is just a lazy Susan, I'd guess you'd call it. |
12:26 | It's a little turntable for food in the fridge and I've just put a plate, like a dinner plate on top of it upside down to make a nice surface. |
12:38 | So, you don't need to go out and buy a, you know, expensive one specifically for 3D scanning. |
12:45 | You can make it work with other ones and the turntable just allows you to rotate the object relative to yourself so you don't have to move around it. |
12:53 | Cool. |
12:54 | So, with that covered, let's get started. |
12:55 | I've just clicked scan there and then this brings us into the next window and we can see here out of the cameras. |
13:05 | So, this is our camera which picks up the color texture and then this is our infrared camera here which is going to be doing most of the work for gathering the scan data. |
13:16 | And this little bar on the side shows us that we're too far away at the moment. |
13:21 | As we move in, we can see the data being collected and what range that's picking up from. |
13:27 | So, we want to stay at about this distance here. |
13:30 | If we go too close, it gets unhappy. |
13:32 | Too far away, we start to lose the data as well. |
13:36 | Cool. |
13:36 | So, there's not really too much to it. |
13:39 | We're just going to, we can either click start on the screen here or actually on the backside of the camera, we have some little buttons as well. |
13:46 | So, I'm just going to hit start and see it beeps there and start to work around the part or move the part around on the turntable in this case. |
14:00 | And I'm just going to kind of do that slowly and I'm just kind of capturing it from a 45 degree angle, but I will want to move the scanner and the angle of it just so we can capture all the data from every angle possible and make sure we don't miss any kind of faces that are angled away from us or something. |
14:25 | We can see this is doing a really good job of this part in this case. |
14:30 | Oh, and I'm just going to stop there. |
14:33 | That is what I thought would happen. |
14:36 | So, basically, because this part is very circular, it starts to get confused where it sees the same side of the part multiple times and thinks it's in a different orientation. |
14:48 | And it basically just got into a spiral there and keeps spinning. |
14:52 | So, I'm going to try to undo this. |
15:00 | Yeah, it looks like using the little undo tool here, which just steps back frames has basically managed to get rid of any kind of overlapping parts there. |
15:10 | And that looks pretty good. |
15:12 | Looks like we've captured this from every angle. |
15:15 | We could try to flip it upside down and take another scan and merge them together. |
15:19 | But for the purposes of this, I'm actually just not going to do that. |
15:23 | It'll work completely fine just having a scan like this. |
15:27 | So, from this point, it's just a matter of hitting this red button again. |
15:32 | And we're just going to remove some of this excess data that we don't need from around that. |
15:37 | So, I've got lasso select tool selected. |
15:40 | I'm going to hold shift on my keyboard and just start to work around here and just press delete. |
15:47 | Otherwise, I can use this delete selection here and just try to remove some of this data that we don't need. |
15:58 | It's a little bit time consuming in this case. |
16:00 | Usually it does do a slightly better job at removing the table from underneath. |
16:10 | We get most of the data there as we process it, it'll probably do the rest of it for us. |
16:18 | I'm just going to work around a little bit more here and remove this. |
16:24 | So, if you're not familiar with 3D scanning, this is quite a common kind of process of taking the scan data and then cleaning it up before processing it, converting it to a mesh, which we're going to do in just a moment. |
16:39 | And then moving through to kind of, we can tidy it up even more after that. |
16:45 | And then you do all sorts of stuff of it as we bring it into our CAD software. |
16:53 | So, bear with me and just get a little bit more of this. |
16:58 | Won't spend too long here tidying it up, but you get the idea. |
17:03 | So, in the Creality Scan software, we do have this option to do a wide select process here, which basically will just fuse all the raw scan data we've got into the point cloud and then it'll actually mesh that point cloud. |
17:23 | So, create the mesh file from the point cloud. |
17:26 | So, the point cloud is essentially the scan data and all its relative 3D space. |
17:34 | And then the mesh basically converts that all into a mesh file, which is like the surface of the part broken up into all these small elements and those elements, faces, facets, whatever we want to call them, are connected by edges and nodes. |
17:49 | And depending on what type of mesh file it is, they might be triangular faces or they could be polygons or whatever. |
17:57 | But for now, we can come in here and do these different fusion settings here and control the resolution ourself. |
18:07 | We could also do some hole filling, which I think is in the next step. |
18:12 | We're just going to do this one click process. |
18:14 | So, that says execute all processing operations with default parameters. |
18:19 | I'm just going to click yes here and we're going to run this through. |
18:23 | And hopefully this doesn't take too long. |
18:27 | I am kind of expecting it to take a few minutes. |
18:31 | So, while that's going, I'll try to think of some other stuff to talk about. |
18:36 | If we compare the software to other software in that kind of accessible scanner space, I would say it sits where you'd expect it to in terms of it was better from memory than the 3D Maker software. |
18:52 | That is a very basic software package compared to the RevoPoint. |
18:56 | I think it's quite similar, but it is limited compared to the Einstar offering. |
19:03 | So, basically, if we compare that to professional software as well that we pay quite a bit of money for, like what we have for our Peel 3D scanner, it's very limited. |
19:14 | There's a lot of processing options. |
19:17 | And yeah, mesh cleaning things and stuff that we can use in those software packages to basically edit our scan data and the mesh to be able to take the best mesh file into our CAD software. |
19:34 | And it basically sets us up with a nicer scan when it comes to filling holes or just removing data from the scan data that we have that we don't need. |
19:47 | So, we can see here, it's fused the mesh and is now... |
19:55 | So, it's fused the point cloud together and now it's meshing and now it is just doing the color mapping, which we're actually not going to need for most of our mechanical design. |
20:06 | You can already see it has filled in this kind of central part just because I didn't remove enough of the table. |
20:15 | But that's not going to be a problem. |
20:17 | So, we can see it's applied the color texture there. |
20:20 | Not going to need that again. |
20:22 | We're just going to go back to the mesh file here and have a look at it. |
20:27 | So, in this case, when it was doing the meshing, it has filled the holes. |
20:33 | So, that was my mistake there. |
20:35 | It's kind of filled this whole backside and the center here. |
20:39 | But we'll continue with this as it is. |
20:42 | And that should be fine for our use for now. |
20:45 | But yeah, generally you'd want to not have the holes filled in this part because we got the surface texture pretty good and we had no holes in the actual part that we wanted to capture. |
20:58 | Anyway, I digress. |
21:00 | From this point here, we now have our mesh. |
21:05 | Probably the biggest downside I've found with this program and that might be something that they change in an update, but there is no alignment functionality. |
21:16 | So, basically, in the software, it does do a pretty good job of aligning it to our coordinate system as we start scanning with the scanner. |
21:24 | But I can't then set the alignment to my coordinate system. |
21:29 | And you might be thinking, surely that doesn't matter. |
21:31 | But it's actually really important when we bring that into our CAD software that we align it with the coordinate system. |
21:39 | It just makes it a lot easier to work with. |
21:42 | We can do it in our CAD software, which is what I'm going to show you how to do for this part. |
21:47 | But it just slows us down. |
21:48 | And that's always nice to be able to do as much as we can in our scanning software that's designed to work with the scan data. |
21:56 | So, yeah, the other thing that I just wanted to mention before we move out of this software is if we come up here and we added a new scan, for example, and we scanned the backside of the part, we would be able to merge those two together. |
22:11 | So, we had both sides. |
22:13 | Or if we're scanning something large, like the side of a vehicle, and we did it in kind of different stages, we could merge those scans together. |
22:23 | So, there is that functionality in it. |
22:25 | But again, we're just missing the alignment, which I think is probably something that it would benefit from a lot. |
22:32 | So, anyway, we're just going to export here. |
22:36 | And we're going to export this as an STL file, which is just the most basic Mesh file that we can use. |
22:44 | We're going to go, Vault Center Kit STL, and just drop it into that folder and go save. |
22:53 | So, that's just exported that Mesh file for us into somewhere that I know where it is. |
23:00 | I'll just delete that one, was one that I practiced with before. |
23:04 | Cool. |
23:05 | And now we're going to jump over into Fusion, which is our CAD software of choice for this project. |
23:15 | Here we go. |
23:17 | Cool. |
23:18 | So, I'm just going to show you something that I've got set up already here. |
23:25 | So, this is a scan I did of the actual wheel on the vehicle, just out in the garage there. |
23:33 | I'll just hide those. |
23:35 | It's just a scan of the face. |
23:37 | So, quite a stunning old design from the 80s, but quite cool for a old little hatchback as well. |
23:45 | And we can see we're just going to fill the space with our new center cap design in the part that we just scanned. |
23:52 | So, again, this was done with the Creality unit. |
23:56 | Just a quick one to get the kind of bulk of it. |
24:01 | And then what I've done here is I've put a plane on the mounting face where the center cap mounts. |
24:10 | And then I've also just put a little sketch line in there that you can see vertical, just to align it with that kind of valve stem area in this little section of the part, which on the back of this part here, it has a little nub which locates into that. |
24:28 | So, basically just some features here on the sketch that with a sketch that I can use to align the parts together. |
24:35 | I won't show you exactly how I did these ones because I'm going to show you how to do the exact same thing now with our center cap scan, and then we'll bring it into an assembly and align it up this part. |
24:49 | Cool. |
24:50 | So, I'll just save that. |
24:54 | And we're just going to start for now with a new design. |
25:00 | So, just a little note, if you have any questions about the scanner or the scanning process or anything we're doing here that come up, feel free to ask them in the chat and I'll do my best to answer them at the end. |
25:13 | So, back in Fusion, if we jump into the mesh toolbar here, I'm going to under the create tab here, just go insert mesh. |
25:23 | Then I'm going to select from my computer, find that bulk center cap STL file and open that up. |
25:32 | So, here we have our mesh file, our scan of our center cap that we've brought in. |
25:40 | And we can see that's just trying to kind of align it with our coordinate system now, but we're going to do this manually and kind of get it all aligned properly. |
25:50 | So, if I just hit okay there, the next step is I'm going to hide that. |
26:02 | Basically, I'm going to create some planes and some sketch features that I know I'll be able to align the part with the wheel using. |
26:11 | So, one of the kind of key tools I like to use for this, actually I'll create the plane first. |
26:18 | So, if you notice, if we try to create a plane straight off this mesh body here, which if I show you shaded with visible edges then you can see all those tiny little elements there that make up the mesh file. |
26:35 | If I tried to create a plane, for example, through three points, I can't select anywhere on this mesh file. |
26:41 | So, the little workaround for this is jumping into the create forms toolbar here. |
26:47 | And then part of the scan that I know is flat and I'll use a part that we actually scanned from. |
26:56 | So, I'm going to go play with three points and I'm going to select three well-divided points on the surface here. |
27:05 | I know that's nice and flat. |
27:07 | And then I'm just going to hit okay. |
27:09 | And that's a quick way to create a form, a plane on a 3D scan infusion. |
27:15 | So, the next step is a tool that I use infusion really often when I'm working with 3D scans. |
27:22 | And it's really helpful for maybe creating a sketch to use the features for making alignments like we're going to do here or picking up on geometry and recreating it for reverse engineering or picking up on it to just use it for a reference for scan -based design if we're designing a new part. |
27:41 | So, that is this create mesh section sketch. |
27:45 | So, I'm going to select that. |
27:47 | This just prompts me to select the body for the section sketch and the section plane which is going to be this one that we just created. |
27:57 | And if I just drag that down slightly, we can kind of see this dark orange line here. |
28:04 | That is the profile as the plane intersects the mesh body. |
28:12 | So, we're getting that section sketch. |
28:15 | I'm just going to hit okay there. |
28:18 | And that'll create this new feature in our timeline, actually two new features. |
28:22 | So, we've got the mesh section feature and we've got the sketch here. |
28:26 | So, I'm going to right click on the sketch and I'm going to edit the sketch. |
28:30 | And then the other kind of key point to using this tool is going to create and then set curves to mesh section. |
28:36 | Then we're going to fit a circle to that there, just like that. |
28:42 | It's kind of tricky to see. |
28:47 | But that has actually fitted a circle kind of as best fit as possible to that curve. |
28:56 | And I'm also going to fit one to that there. |
29:01 | Just to kind of do the cheating easy way to do this, I'm just going to fix those two. |
29:08 | Then just out of curiosity, what I'll do is I'll measure that profile there. |
29:14 | And that's giving me 75.1 millimeters. |
29:18 | And just as a quick sanity check, I've got some veneers here, which are just plastic, you know, analog ones. |
29:28 | Cut that out very good. |
29:32 | But it's sitting at about, yeah, 74.5 on these and that's 75. |
29:42 | It's probably is 75. |
29:43 | So, to be honest, the scan's probably more accurate than my veneers I've got here. |
29:49 | So, you can see that the accuracy and the scale of everything is looking pretty good. |
29:53 | But we don't need that measurement for now. |
29:55 | So, I'm just going to go finish sketch. |
29:57 | Actually, I'm going to jump back into that sketch at the moment. |
30:01 | It's moving quite slow. |
30:04 | So, I just want to add one more little feature to it, which is just going to be a line between these two. |
30:12 | And just go, okay. |
30:13 | So, that's going to help me kind of orientate the part in the assembly that I'm going to jump into in just a moment. |
30:20 | So, I'm going to finish sketch there. |
30:23 | And this is moving pretty slow. |
30:26 | Just going to close the scanning program in the back to hopefully speed things up. |
30:34 | So, now we have our sketch and our plane with our mesh file. |
30:37 | And we're going to use that to align it with the assembly in just a moment. |
30:43 | So, again, I'm going to save this as bulk center cap. |
30:50 | Yeah. |
30:53 | And I'm just going to go and call it test. |
31:00 | Let's save. |
31:02 | Cool. |
31:04 | So, that saved that there. |
31:06 | So, in this bulk center cap design file here that I created earlier, basically what it does is an assembly. |
31:17 | I'm just going to change my view a little bit here. |
31:21 | So, this is an assembly that just has an external component brought in. |
31:25 | That is that wheel scan that we had before. |
31:29 | And I used the sketch that I'd created in that, if we just remember what that looks like, to align that with our coordinate system. |
31:39 | And then basically what I've done is I've just grounded that component. |
31:42 | You can see this tiny little anchor up here. |
31:45 | So, it won't move in our workspace by accident. |
31:48 | You move out of that alignment. |
31:50 | And then basically what I'm going to do now is just bring in our center cap that we've just scanned and align it with this mesh body as well. |
32:02 | So, let's jump into here. |
32:06 | Well, center cap test is the one that we just saved before. |
32:10 | Insert that into the current design. |
32:16 | Finish that up. |
32:17 | Just want to drag it up here for now. |
32:23 | So, yeah. |
32:24 | What we're going to do is align that with our wheels. |
32:30 | So, it's a couple of different ways to do this. |
32:33 | But what we're going to do is just, first of all, use the align tool for that component. |
32:41 | And if we jump back into this one, I'm going to show the... |
32:46 | Oh, sorry, this one here, this wheel component, show the plane there. |
32:51 | I'm going to start off by aligning those two planes to each other. |
32:56 | And then I'm going to align those two sketches to each other and actually just flip those. |
33:06 | And then I'm going to jump into the move tool and I'm going to move this component and use the point-to-point there. |
33:16 | Now, I don't select the center point of the part, base of that line. |
33:23 | And I'm going to move that to match the center point from the wheel. |
33:29 | So, we can see it's centered there now. |
33:31 | It's just kind of sitting at the wrong height. |
33:33 | I just clicked enter by mistake on my keyboard, but that's fine. |
33:37 | So, we'll use that move tool again. |
33:39 | And what we're going to do now is we're just going to drag this part up into the correct alignment. |
33:45 | So, if I just use the free move tool here, I'm going to set the pivot on the end of the line there. |
33:56 | So, I get a nice vertical kind of orientation or arrow that I can drag it with. |
34:02 | Click done when I've set that pivot. |
34:04 | And then I can just drag this part up and kind of match the face there. |
34:14 | Bring this back down to 11.5. |
34:17 | See how that looks. |
34:18 | That looks pretty good. |
34:20 | Choose to capture the position. |
34:22 | OK. |
34:23 | So, we can see that using those line sketches there aligns the orientation or the clocking, I guess, of that center cap in the right place. |
34:33 | And we're on the correct plane from that plane that we created with the frame tool. |
34:38 | And then, yeah, we've just dragged it up into the correct alignment. |
34:44 | And because this just uses a threaded feature on the little snub here, which I will use a physical measurement to determine exactly what it is. |
34:54 | Not take that from our scan data. |
34:57 | I can now use the setup to design that little center cap. |
35:01 | Just hide those, kind of tidy things up. |
35:06 | So, yeah, I've got these scans all in place, aligned to each other, and it's set up so I can design a center cap on that. |
35:13 | And I'll know exactly what it's going to look like because it gives us a nice visual reference and also know that it's going to fit correctly and so on. |
35:23 | So, I'm going to leave it there for now, but hopefully that's given you a little bit of insight into scanning not only of the Creality scanner and kind of how it works and using the software, but also bringing that scan data into Fusion and just kind of getting it set up to design our projects with some finer good practices and ways to do it. |
35:47 | The last thing that you should do though is create a rigid group between those components so we don't have our center cap moving slightly out of alignment without us noticing or something while we're designing. |
36:00 | And that's how little errors will creep in. |
36:02 | So, now everything's locked down and we're ready to go. |
36:06 | So, with that, I'll just jump back to my notes and see if there's any questions from the chat that I can do my best to answer. |
36:22 | Bear with me a sec. |
36:27 | So, Jay Sally, "I've never used an actual scanner. |
36:30 | So, does it truly make the difference when it comes to final model result?". |
36:35 | Yeah, I think so, but it really depends. |
36:38 | It's a case by case basis. |
36:39 | Some projects don't need a 3D scanner. |
36:42 | Even using a 3D scanner will probably just slow you down. |
36:47 | But in saying that, since we've had 3D scanners at HPA, we use them for almost everything. |
36:54 | They are, as some of the kind of professionals in the industry like to call them, the best tape measure you'll ever use or something like that, where basically it takes millions or hundreds of thousands of measurements all at once. |
37:12 | They're really accurate. |
37:13 | It does a lot for providing a visual reference, but being able to also design accurately to things saves you a lot of time. |
37:22 | And then I think from having that visual reference and seeing how it all works in the virtual world before you go and then spend the money to bring it to life, you can do a lot of iterations and design and changes to it to get the best result before you go and spend the money on it. |
37:40 | So, definitely reduces the chances of any kind of oversights or errors as well. |
37:47 | So, yeah, I'm a big advocate for 3D scanning. |
37:50 | I use it for almost everything that I do now. |
37:53 | When it comes to CAD, if I have the chance to do it, I really think they're worth it. |
37:59 | And some of these more accessible scanners, like you can see from that, are showing some pretty usable results as well. |
38:08 | When the accuracy of the scanner is a little bit kind of compromised compared to maybe a more professional scanner, we just need to keep that in mind. |
38:17 | And maybe, like I said, back it up with some physical measurements to ensure that we're getting the right hole spacing or the right size for components and so on. |
38:29 | Chris, "I was curious on your thoughts between the Creality Audit and the Einstar from Shining3D, assuming the proper PC specs and doing car design for larger projects.". |
38:41 | So, I would say for larger projects is really where the Einstar shines. |
38:46 | Pun not intended there. |
38:50 | It is really good for capturing a large amount of data really efficiently and without any errors from what we've kind of found from our experience. |
39:02 | Yeah, that's really the area where the Einstar shines. |
39:05 | It just, you can scan down the side of a car with almost no print, like for glossy or transparent surfaces. |
39:14 | And yeah, it does a really, really good job there. |
39:18 | I do have a little video here. |
39:21 | I'm just going to open and hopefully, Joel can drop that into the show notes as well. |
39:29 | And that just gives you a little bit more of a insight into using these 3D scanners or hearing a different 3D scan that's here. |
39:40 | Einstar, the Otter, and some of the other ones we've got raised in the notes. |
39:47 | And we had a little bit of a post-look at the accuracy and so on and just the usability. |
39:53 | Joel drops that into the chat. |
39:58 | Again, the Creality otter is a little bit cheaper than the Einstar and it does a really good job. |
40:05 | It's arguably more accurate than applications. |
40:08 | It's quite versatile with the different scanners. |
40:12 | As I said, the Einstar was our choice from a couple of people as well. |
40:16 | So, I wouldn't take it long. |
40:18 | The Einstar works really great for those larger projects. |
40:23 | Chris, "Does the Creality Otter do well with scanning car panels?". |
40:28 | So, I kind of just talked about that then. |
40:30 | I would say, yes, it does. |
40:33 | Do pretty well, but I don't think it does as well as the Einstar in regards to that. |
40:41 | So, if that was specifically what you're working on, maybe you're scanning car panels because you do aero design or CFD or maybe you make composite panels or body kits or something like that, then I think the Einstar is probably the pick for this bunch of scanners. |
41:02 | So, yeah, with that covered, I'm just going to lead to wrapping up. |
41:06 | Hopefully that's given you some insight into more accessible scanning option and then the kind of process of scanning something and bringing it into our CAD software as well. |
41:17 | So, thanks for watching. |
41:19 | We'll be back next week with another topic and we'll see you then. |
00:00 - Introduction and Overview
03:00 - Scanner Specifications and Accuracy Discussion
08:15 - Scanner Features and Capabilities
10:10 - Software Setup and Configuration
13:35 - Scanning Process Demonstration
16:18 - Scan Data Cleanup and Processing
22:30 - Exporting and CAD Software Integration
27:45 - Measurement Verification and Accuracy Check
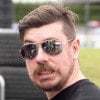